Causes of Pressing Defects (Burrs, Dents) and Observation of Defects and Cut Sections (Fracture Surfaces)
Pressing is widely used in the mass production of various products. Especially with the progression of electronic control of automobiles in recent years, there are demands for even higher accuracy, durability, and reliability of not only vehicle frames and sliding parts but also of electrical parts, which are being miniaturised and are being installed with higher density, and of metal parts for electronic equipment.
This section explains typical pressing defects and their causes and countermeasures. It introduces application examples of our 4K digital microscope, which improves the sophistication and efficiency of the observation of defects and of cut sections such as fracture surfaces. These examples are important in the testing, design, and prototyping of research and development and in the inspections carried out in quality assurance.
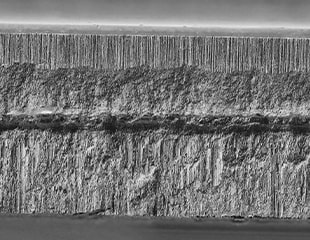
- Causes of and Countermeasures for Pressing Defects
- Observation Examples of Cut Sections and Defects on Pressed Products
- A 4K Microscope That Greatly Optimises the Research and Development, Design, and Quality Assurance of Pressed Products
Causes of and Countermeasures for Pressing Defects
Pressing types
In pressing, the material is shaped as desired through the application of pressure through various methods, generally with a mould called a die and punch. Typical pressing types are as follows.
- Shearing: The material is processed (cut) through the application of force exceeding its fracture limit.
- Bending: The material is bent through the application of tensile force on one side and of compression force on its other side.
- Deep drawing: The material is processed through the application of tensile stress.
- Compression: The material is processed through the application of compression force.
Causes of and countermeasures for typical pressing defects
This section explains typical pressing defects and their causes and countermeasures. It is difficult to completely and continuously eliminate all defects due to factors such as the properties of the material, the design, and processing principles. However, it is important to improve the yield rate as much as possible by reducing the frequency of defects through various countermeasures.
- Burrs
- Cause: This defect occurs because, for example, the gap (clearance) between the punch and die is too large during shearing.
Countermeasure: Ensure that 1/2 to 1/3 of the plate thickness is the sheared surface and that this status is uniform.
Structural images of the cross-sections of the material after shearing with various clearance conditions are shown below with explanations of the names and characteristics of the parts.
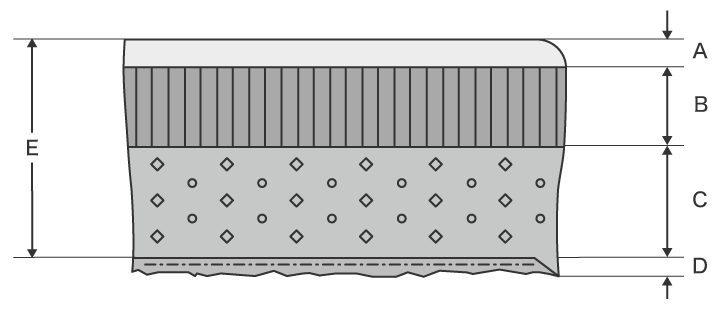
- Shear droop: Smooth surface caused by the surface of the material being pulled.
- Sheared surface: Glossy surface with vertical stripes. There are subtle scratches caused by the punch cutting during shearing and due to the friction between the deposited metal and the material.
- Fracture surface: Compared to the sheared surface, this is a rougher surface that has been torn away, making the surface extremely uneven.
- Burr: A jagged protrusion from the material. Large burrs can lead to defective products due to insufficient fit accuracy between parts and safety problems such as injuries caused by sharp burr tips.
- Plate thickness
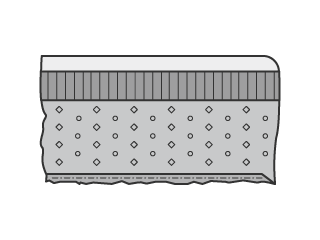
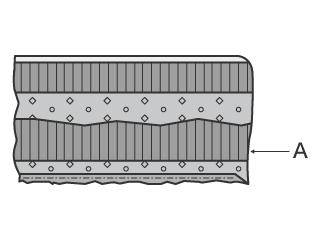
When the clearance passes the appropriate amount, the larger the clearance, the larger the burr. Also, the shape and dimension accuracies decrease due to problems such as warping caused by the extraction pressure. On the other hand, too little clearance causes a secondary sheared surface (A in the figure on the right) on the other side of the fracture surface to occur, resulting in whisker-shaped burrs.
The size of a burr is expressed as the thickness of its base (A in this figure) or as its height (B in this figure).
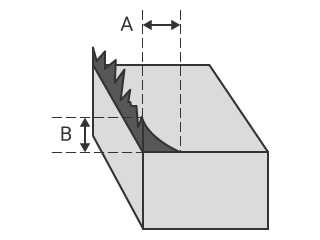
- Springback
- Cause: After bending, the residual compressive stress and tensile stress in the material act in opposition to each other, causing the processed part to bend back toward its original shape.
Countermeasures: Bend to a deeper angle than intended or add a striker plate or a notched groove to the punch.
- Wrinkles
- Cause: This happens when compression force is applied to the flange during deep drawing.
Countermeasure: Use wrinkle suppression via the deep drawing conditions to apply a uniform load to the material. In addition to fixed wrinkle suppression, there is also moveable wrinkle suppression that uses the force of a spring or a die cushion.
- Cracks
- Cause: Cracks form in the material when the tensile force exceeds the fracture limit during deep drawing.
During bending, cracks, splits, and tears may occur in the bent part due to the rolling direction of the material or the bend width dimension.
Countermeasures: In deep drawing, reduce the wrinkle suppression pressure or make the curve of the die smooth to lower the deformation resistance. In bending, ensure that the bending line and the rolling direction of the material are perpendicular or set the bend width to at least eight times the plate thickness.
- Scrap buildup (the cause of dents and scratches)
- Cause: This is a phenomenon where scrap (which should be removed from the mould) affixes to the punch due to factors such as vacuum pressure, oil films, and magnetism after extraction processing. Scrap buildup is the cause of defects such as dents and scratches on the material surface and may also damage the mould.
Countermeasures: Install a kicker pin on the punch to establish a physical gap between the scrap and the punch. Other methods include discharging air from the tip of the punch, cutting a groove in the punch and inserting air there, and suctioning the scrap from below. It may also be possible to reduce the degree to which scrap affixes to the punch by lowering the viscosity of the oil used or by cutting a groove in the punch to reduce the contact area of the oil.
Observation Examples of Cut Sections and Defects on Pressed Products
Sometimes, pressing defects cannot be avoided just by working hard at a production site. In the initial stages of research and development, material selection, and product and mould design, it is necessary to strive for improvements through as much repeated testing and prototyping as possible. In quality assurance, it is also important to research the causes of malfunctions of metal parts produced through pressing and to improve these parts.
Therefore, detailed observation of defects with an optical microscope is vital in all these steps.
For example, an optical microscope can be used to check in detail whether the processing conditions were appropriate from the cut section during shearing and whether burrs can be attributed to these conditions. On the other hand, processed metal components are three dimensional, which makes them difficult to observe because it is hard to focus the image throughout the field of view and because the surface roughness and reflectance vary within the same field of view.
This section explains the advantages of the VHX Series 4K digital microscope while introducing examples of using it to perform high-accuracy observations of microscopic surface differences such as shear droop, sheared surfaces, and fracture surfaces from the cross section of a pressed product and of the appearance of defects such as burrs and dents.
High-accuracy observation of pressed product cross sections (shear droop, sheared surfaces, fracture surfaces)
The cross section of a sheared pressed product can be used to evaluate items such as whether the clearance between the punch and die is appropriate from the ratio of the sheared surface to the plate thickness, the processing quality, and the causes of burrs. The surface conditions—such as the depressions and projections, the roughness, and the pattern—vary for the shear droop, sheared surfaces, and fracture surfaces that appear in the cross section. Furthermore, although each part has the same colour and low contrast, the light reflectance varies, so it is difficult to observe the overall surface conditions because, for example, glare occurs in some parts.
The VHX Series 4K digital microscope is equipped with features that provide both high resolution and large depth of field such as a telecentric HR lens and a 4K CMOS image sensor, ensuring that this microscope has exceptional resolution. Hence, clear images where the entire cross section is in focus can be captured even when the same cross section has various surface conditions.
The specially designed optical system, 4K CMOS image sensor, and Optical Shadow Effect Mode—a new observation method that combines lighting—analyse displacement (contrast) captured with lighting from multiple directions, allowing for clear observation of microscopic surface irregularities and other surface conditions with high contrast. Optical Shadow Effect Mode images can be combined with colour information to visualise depth and height information with different colours.
The VHX Series enables this advanced observation method with simple operations, greatly increasing the speed of cross section observation and evaluation, which require a lot of time for condition determination.
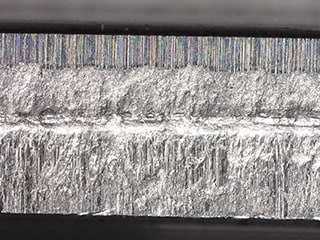
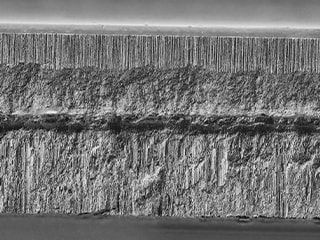
Fully focused observation of microscopic burrs
Even though burrs on pressed products are small, they are hard and sharp, so they may make the product less safe. Burrs may get caught during part assembly, negatively affecting the production yield rate.
In investigating the cause of a burr, the most important information is its base and tip, but it is difficult to observe both of these aspects clearly and at the same time in an overall image with optical microscopes because burrs are three-dimensional and microscopic, meaning that it is only possible to bring a part of them into focus at a time during observation.
The VHX Series 4K digital microscope’s cutting-edge optical technology and observation system allows three-dimensional targets to be observed with easily captured images of the target that are focused throughout the field of view.
The lens, 4K CMOS image sensor, and ring illumination—which provide high resolution and a large depth of field—allow even whisker-shaped burrs to be observed with 4K, high-accuracy images in which the entire burr is in focus from its base to its tip.
The overall image of a defect can be viewed at a glance with a high-accuracy image, greatly optimising the workflow of cause investigation via observation.
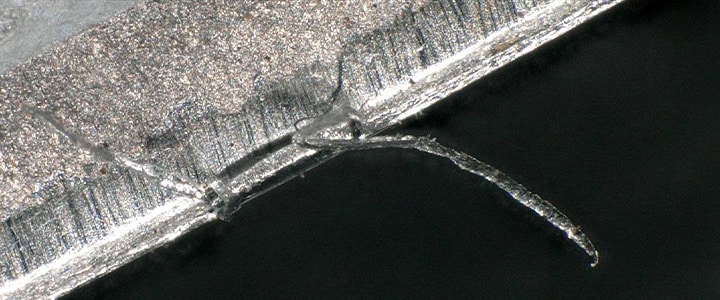
High-contrast observation of dents and other microscopic defects
Minor dents and microscopic scratches caused by scrap buildup and similar defects have minimal contrast with the background when the material is metal. Therefore, it was sometimes difficult to determine conditions and there were cases where these dents and scratches could not be detected well even if time was spent on adjustments.
With the VHX Series 4K digital microscope, there is no need to manually determine conditions. With just one click of a button, the operator can select the image that is most suitable for the observation purpose from the Multi-lighting function, which automatically acquires omnidirectional lighting data. Even after selecting an image, the images with the other lighting conditions are saved automatically, allowing for observation under different conditions without having to place the sample on the stage again.
Optical Shadow Effect Mode, a new observation method that easily captures high-contrast images while eliminating the hassle of requiring a vacuum, can be used to observe even microscopic dents with high contrast and clear images.
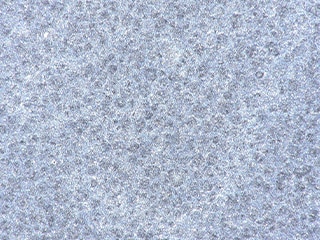
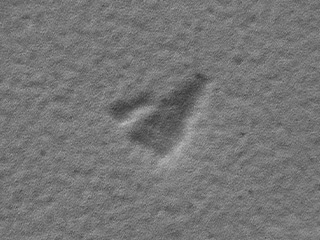
A 4K Microscope That Greatly Optimises the Research and Development, Design, and Quality Assurance of Pressed Products
Although observations of cross sections and microscopic defects of pressed products are difficult and require a long time for condition determination even for experienced operators due to factors such as the characteristic glossiness of the metal materials used to make these products, the VHX Series 4K digital microscope allows these observations to be performed quickly and with simple operations.
High-accuracy 4K images acquired using diverse functions improve the sophistication and efficiency of the observation vital to research and development, design and improvement of products and moulds, and quality assurance in the event of product malfunctions.
For additional info or inquiries about the VHX Series, click the buttons below.