Messung von Verschleiß und Defekten bei Lagern
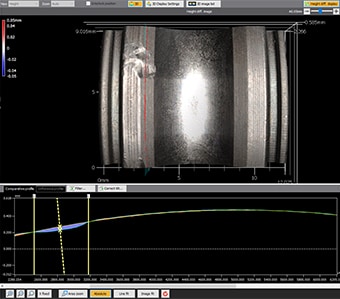
Die Qualität der Lager wird anhand ihrer Leichtgängigkeit und Beständigkeit bewertet. Die reibungslose Bewegung wirkt sich direkt auf die energiesparende Leistung und die Bewegungsgenauigkeit aus, während die Beständigkeit direkt die Betriebsdauer beeinflusst. Da die Materialien, Strukturen, Schmiermethoden und Abdichtungseigenschaften von Lagern immer fortschrittlicher werden, haben sich auch die wartungsfreien Lager weiterentwickelt. Solange die Lager jedoch gleitende Bauteile enthalten, können Herausforderungen durch Verschleiß oder Beschädigung nicht vermieden werden.
In diesem Abschnitt werden Lagerdefekte, Methoden zur Messung der Lagergenauigkeit, Herausforderungen dieser Methoden sowie Lösungsvorschläge vorgestellt.
- Lager
- Lagerarten und Belastungen
- Lagerdefekte
- Herausforderung bei gängigen Messungen von Lagern
- Lösung von Herausforderungen bei der Messung von Lagern
- Zusammenfassung: Erhebliche Verbesserung und höhere Effizienz bei der Messung der Lagerform
Lager
Ein Lager stützt eine rotierende Welle so ab, dass sie sich nicht durchbiegen kann. Lager werden in einer Vielzahl von Bereichen eingesetzt, darunter in Automobilen, Fahrrädern, Haushaltsgeräten und Flugzeugen. Daher müssen sie witterungsbeständig sein, um dem Einsatz bei hohen und niedrigen Temperaturen standhalten zu können. Zudem müssen sie eine hohe Lebensdauer aufweisen, um hohen Belastungen und hohen Drehzahlen standhalten zu können.
Lagerarten und Belastungen
Bei den meisten Lagerdefekten handelt es sich um Verschleiß und Kratzer, die an den reibungsintensiven Oberflächen zwischen den Kugeln, Rollen, Wellen und den Bauteilen, die sie tragen, auftreten. Zu den Ursachen gehören externe Stöße und Montagefehler sowie eine Abnutzung durch den Gebrauch. Die Gegenmaßnahmen zu diesen Herausforderungen variieren je nach Lagerstruktur und der Belastung, die auf das Lager einwirkt.
Arten von Lagern
Es gibt zwei Hauptarten von Lagern: Lager mit Wälzkörpern, wie Rollen- und Kugellager, und Gleitlager, die anstelle der Wälzkörper ein Schmiermittel verwenden.
- Kugellager, Rollenlager und Nadellager:
- Diese Lager stützen eine Welle mit Kugeln oder zylindrischen Rollen. Lager, die Kugeln verwenden, werden Kugellager genannt. Lager, die Rollen verwenden, werden Rollenlager oder Nadellager genannt. Rollenlager und Nadellager haben eine hohe Tragfähigkeit und können dünner sein als Kugellager.
- Gleitlager:
- Gleitlager werden manchmal auch als Metall-Lager bezeichnet, da die Welle direkt mit der Lageroberfläche in Berührung kommt. Gleitlager enthalten ein Schmiermittel, um die Reibung zu verringern. Der Schmierfilm hemmt die Drehung der Welle zu Beginn der Rotation. Sobald sich die Rotation jedoch stabilisiert hat, verringert sich der Widerstand, da kein mechanischer Kontakt mehr besteht. Da es keine Kontaktfläche gibt, während sich die Welle dreht, rotiert diese Lagerart leise und kann hohen Drehzahlen und Stoßbelastungen standhalten.
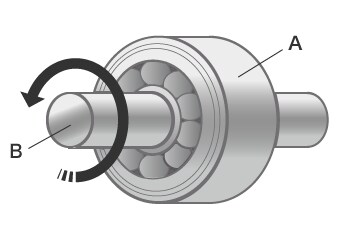
- A
- Kugellager
- B
- Welle
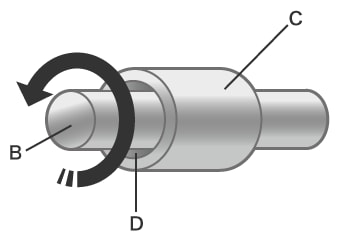
- B
- Welle
- C
- Gleitlager
- D
- Schmiermittel
Lagerbelastungen
Die auf die Lager einwirkenden Kräfte werden in Radial-, Axial- und Momentbelastungen eingeteilt.
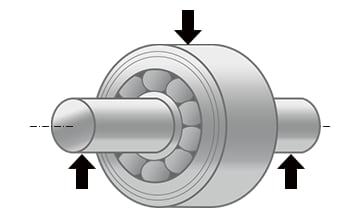
- Radialbelastung:
- Eine Radialbelastung wird in der Richtung senkrecht zur Mittellinie des Lagers (der Laufbahnrichtung des rotierenden Körpers) aufgebracht.
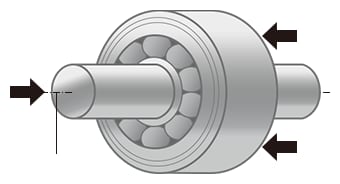
- Axialbelastung:
- Die Axialbelastung wird auch als Schublast bezeichnet. Diese Belastung wird in der Richtung parallel zur Mittellinie des Lagers (der axialen Richtung des rotierenden Körpers) aufgebracht.
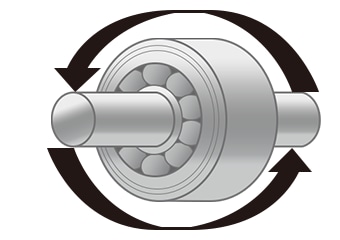
- Momentbelastung:
- Diese Belastung wird durch den Rundlauf des Lagers oder der Welle erzeugt. Wenn ein Lager einer Momentbelastung ausgesetzt ist, wird seine Lebensdauer drastisch verkürzt.
Lagerdefekte
Zu den typischen Lagerdefekten gehören Verschleiß, Abblätterungen, Fresser und Abschälungen. Andere Herausforderungen sind Vertiefungen, die durch Stöße beim Einbau eines Lagers, durch Fallenlassen oder Überlastung verursacht werden, Verschmierungen, die durch unzureichendes Spiel oder Überlastung verursacht werden sowie elektrolytische Korrosion, die durch schlechte Schmierung oder Installationsfehler verursacht wird. Die Ursachen dieser Herausforderungen können durch Messung und Betrachtung der Oberflächen ermittelt werden.
In diesem Abschnitt werden die Beschädigungsbedingungen, Ursachen und Gegenmaßnahmen für die typischen Herausforderungen wie Verschleiß, Abblätterungen, Fresser und Abschälungen vorgestellt.
Verschleiß
Verschleiß kann durch viele verschiedene Faktoren verursacht werden und sich in einem breiten Spektrum von Lagerphänomenen manifestieren.
- Beschädigungsbedingungen:
- Die Oberfläche wird abgenutzt, wodurch sich die Abmessungen ändern. Die Oberfläche ist rau oder zerkratzt.
- Ursachen:
-
- Ein fester Fremdstoff ist in das Schmiermittel gelangt.
- Die Schmierung ist unzureichend.
- Der Abstand zwischen den Eingriffsflächen ist nicht ausreichend.
- Gegenmaßnahmen:
-
- Filtern des Schmiermittels bzw. verbessern der Qualität des Schmiermittels oder der Schmiermethode.
- Verbessern Sie die Dichtungsleistung.
- Abstand zwischen den Eingriffsflächen.
Abblätterungen
Abblätterungen sind eine Art des Schälens. Dieses Problem tritt auf den Laufbahn- oder Rollflächen auf, wenn das Lager das Ende seiner Betriebsdauer erreicht hat. Wenn dieses Problem jedoch in einer früheren Phase auftritt, ist es notwendig, die Ursache sofort zu erkennen und Gegenmaßnahmen zu ergreifen.
- Beschädigungsbedingungen:
- Vom gesamten Umfang der Laufbahn lösen sich schuppige Stücke ab. Dies hinterlässt Unregelmäßigkeiten auf der Oberfläche der Laufbahn.
- Ursachen:
-
- Übermäßige Axialbelastung durch Montagefehler oder Aufquellen der Welle.
- Ein Fremdkörper ist in das Lager eingedrungen oder es ist Korrosion aufgetreten.
- Gegenmaßnahmen:
-
- Überprüfen Sie die Montagegenauigkeit.
- Optimieren Sie die Belastung. Erhöhen Sie die Viskosität des Schmiermittels und verbessern Sie die Schmiermethode.
- Ergreifen Sie Maßnahmen zur Vermeidung von Korrosion, wenn die Lager über einen längeren Zeitraum nicht benutzt werden.
Fresser
Fresser sind ein Phänomen, das durch Erhitzung eine örtliche Verklebung von Oberflächen verursacht. Dieses Problem tritt in axialer Richtung auf.
- Beschädigungsbedingungen:
- Beschädigungen führen zum Festfressen der Laufbahn und der Rollflächen.
- Ursachen:
-
- Falsche Handhabung beim Ein- oder Ausbau der Lager.
- Unzureichendes Schmiermittel oder unzureichende Schmierung der Kontaktflächen durch übermäßige Axialbelastungen.
- Übermäßige Vorbelastung. Verrutschen der Wälzkörper.
- Gegenmaßnahmen:
-
- Verbessern Sie die Montage- und Ausbaumethoden.
- Verringern Sie die Belastung und verbessern Sie das Schmiermittel und die Schmiermethode.
- Verbessern Sie die Dichtungsleistung.
Abschälungen
Die Oberflächen der Laufbahnen werden durch die Reibung stumpf. Dieses Problem tritt am häufigsten bei Nadellagern auf. Abschälungen können auch zu Schuppenbildung und somit Abblätterungen führen.
- Beschädigungsbedingungen:
- Die Oberfläche schält sich großflächig bis zu einer Tiefe von 10 μm ab.
- Ursachen:
-
- Ungeeignetes Schmiermittel.
- Fremdkörper im Schmiermittel.
- Unzureichende Schmierung.
- Rauheit auf den Kontaktflächen der Teile.
- Gegenmaßnahmen:
-
- Wählen Sie ein geeignetes Schmiermittel.
- Filtern Sie das Schmiermittel. Verbessern der Rauheit.
Herausforderung bei gängigen Messungen von Lagern
In den meisten Fällen treten Herausforderungen mit den Außen- und Innenlaufbahnen, den Kugeln und den Rollen der Lager auf. Daher können Verschleiß, Abblätterungen, Fresser, Abschälungen und andere Defekte durch die Messung dieser Bauteile festgestellt werden.
Bei der gängigen Messung von Lagern werden Profilmesssysteme verwendet. Da die Lager jedoch komplexe Formen haben, ergeben sich bei der Messung einige Herausforderungen, die nachfolgend beschrieben werden.
Herausforderung bei der Messung von Lagern mit einem Profilmesssystem
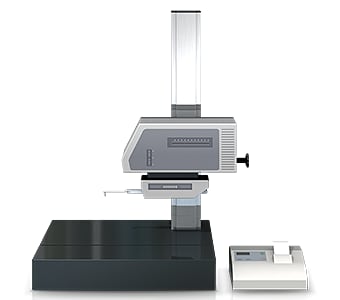
Ein Profilmesssystem oder Konturograph misst und erfasst das Profil eines Messobjekts, indem es dessen Oberfläche mit einem Taststift nachfährt. In den letzten Jahren wurden Profilmesssysteme entwickelt, die mit einem Laser anstelle eines Taststifts komplexe Formen messen, indem sie das Profil berührungslos verfolgen. Einige Modelle sind sogar in der Lage, Messungen sowohl der Ober- als auch der Unterseite durchzuführen.
Bei einem Profilmesssystem ist es jedoch erforderlich, präzise Messlinien für das zu messende Lagerproblem zu erfassen.
Dies beinhaltet die folgenden Herausforderungen:
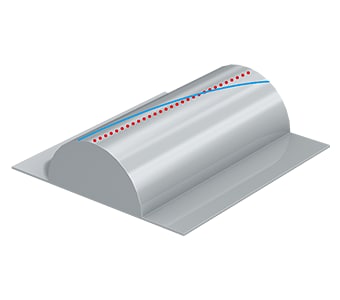
- Die Messung erfordert viel Zeit, einschließlich der Zeit für die Befestigung der Probe auf einer Vorrichtung und deren Nivellierung. Außerdem sind Kenntnisse und Fähigkeiten im Umgang mit einem Profilmesssystem erforderlich, um ein Messobjekt genau auszurichten.
- Der Taststift eines Profilmesssystems bewegt sich in einem Bogen auf und ab, der auf dem Drehpunkt des Tastarmes zentriert ist, und die Tastspitze bewegt sich auch in Richtung der X-Achse. Dies führt zu Fehlern in den Daten auf der X-Achse.
- Das Nachzeichnen der gewünschten Linie mit dem Taststift ist eine äußerst schwierige Arbeit, und selbst eine leichte Verschiebung des Taststifts führt zu Fehlern in den Messungen.
- Es ist auch schwierig, die Anzahl der Messobjekte zu erhöhen, weil man bestimmte Positionen für die Messung festlegen muss.
- Es kann nur ein Teil eines Messobjekts gemessen werden, und die Auswertung der gesamten Oberfläche ist nicht möglich.
Herausforderungen bei der Messung mit einem 3D-Koordinatenmessgerät
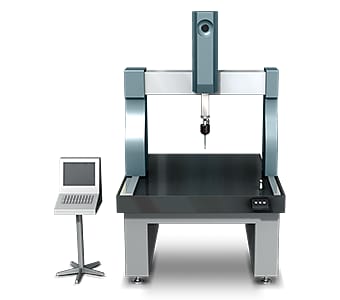
Wenn die zu messende Fläche klein ist, zum Beispiel 1 mm2, ist es äußerst schwierig, die Form genau zu messen oder eine virtuelle Oberfläche mit dem Messtaster zu erstellen. Auch bei der Messung einer kleinen Fläche ist es aufgrund der geringen Anzahl von Messpunkten schwierig, die genaue 3D-Form zu ermitteln. Viel Arbeit machen auch die damit verbundenen Aufgaben, wie z. B. die tabellarische Erfassung der Messdaten und der Vergleich der Ergebnisse mit den Zeichnungen.
Lösung von Herausforderungen bei der Messung von Lagern
Profilmesssysteme bringen Herausforderungen mit sich, wie z. B. die Tatsache, dass es unmöglich ist, die gesamte Form zu erkennen, da die Messung dreidimensionaler Messobjekte und Flächen mittels Punkt- oder Linienkontakt erfolgt, sowie die geringe Zuverlässigkeit der Messwerte. Um diese Messprobleme zu lösen, hat KEYENCE das 3D-Profilometer der Modellreihe VR entwickelt.
Die Modellreihe VR erfasst präzise die 3D-Form der gesamten Oberfläche, ohne das Messobjekt zu berühren. So kann die gesamte Oberfläche in nur wenigen Sekunden präzise gemessen werden. Das System legt den Messbereich und die Bedingungen automatisch fest. Dadurch werden präzise quantitative Messungen gewährleistet, die keine anwenderspezifischen Unterschiede aufweisen. In diesem Abschnitt werden einige Vorteile der Modellreihe VR vorgestellt.
Vorteil 1: Die gesamte Oberfläche der 3D-Form wird gemessen
Legen Sie für die Messung das Messobjekt einfach auf den Objekttisch und starten Sie die Aufnahme. Eine genaue Positionierung oder sonstige Vorbereitung ist nicht erforderlich. So können auch hochpräzise Messungen durch Anwender, die über keine Kenntnisse oder Erfahrungen im Umgang mit Messgeräten verfügen, durchgeführt werden.
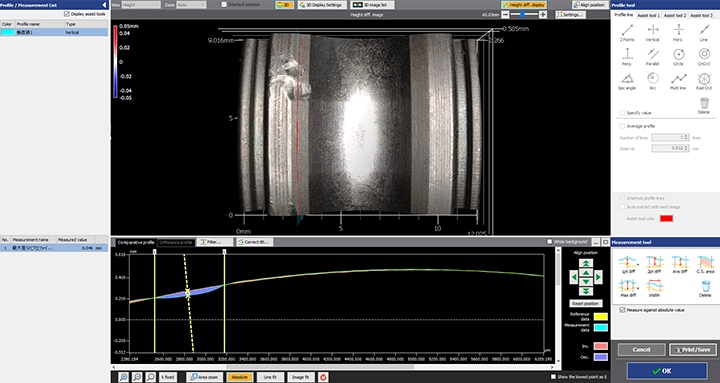
Im Gegensatz zu gängigen Profilmesssystemen extrahiert die Modellreihe VR die Merkmale des Messobjekts auf dem Objekttisch und führt eine automatische Positionierung durch. So können auch Anwender, die mit Messungen nicht vertraut sind, einfach und sofort Messungen durchführen. Es muss kein Fachpersonal beauftragt werden. Die Modellreihe VR kann einen großen Bereich von bis zu 300 mm × 150 mm abdecken, wodurch es möglich ist, mehrere Messobjekte gleichzeitig auf dem Objekttisch zu messen.
Mit der Modellreihe VR kann sogar ein Messobjekt mit einer komplexen Form, wie z. B. ein Lager, genau gemessen werden.
Vorteil 2: Eine große Auswahl an Hilfswerkzeugen verhindert Abweichungen bei der Messung
Profillinien können an definierten Stellen in den Messdaten platziert werden, wodurch Abweichungen in den Messergebnissen vermieden werden.
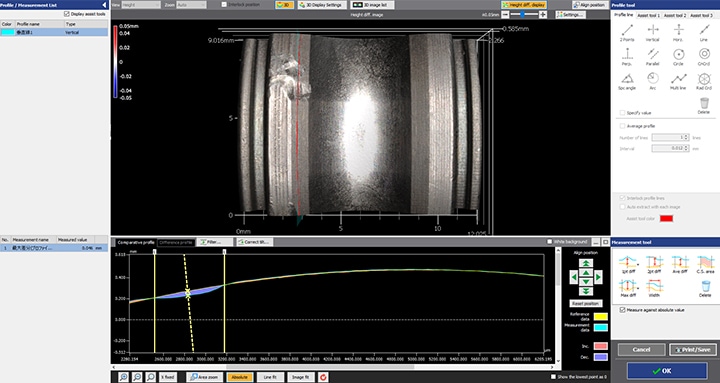
Die große Auswahl an Hilfswerkzeugen ermöglicht eine einfache Einrichtung der gewünschten Messungen. Mit dem Messwerkzeug für die vertikale Grundlinie können Sie zum Beispiel die Messlinie für den Außendurchmesser des Lagers einfach und präzise festlegen.
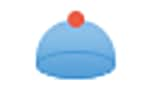
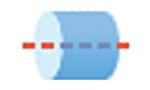
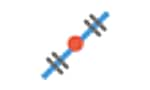
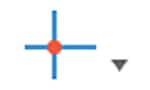
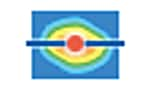
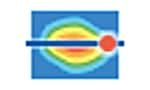
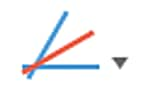
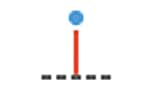
Zusätzlich zur einfachen Konfiguration ermöglichen die Hilfswerkzeuge eine einfache Bedienung des Systems, sodass selbst ungeübte Anwender, die mit Messungen nicht vertraut sind, Formen in nur einer Sekunde präzise messen können. Dadurch kann die Anzahl der Proben nicht nur für Prototypen und Versuche, sondern auch für die Messung und Prüfung von Produkten problemlos erhöht werden.
Zusammenfassung: Erhebliche Verbesserung und höhere Effizienz bei der Messung der Lagerform
Die Modellreihe VR kann 3D-Messobjekte präzise und sofort mit hoher Geschwindigkeit messen, ohne das Messobjekt zu berühren. Selbst schwierige Messungen, wie z. B. die Messung des Verschleißes von Kugeln, Rollen und Laufflächen, können in nur einer Sekunde durchgeführt werden. Die Modellreihe VR löst viele Herausforderungen, die bei gängigen Messgeräten auftreten können.
- Da die gesamte Oberfläche berührungslos erfasst werden kann, ist es möglich, Querschnitte zu messen, die ein Taststift nicht erreichen kann. Selbst kleine Lager können einfach und präzise gemessen werden.
- Die große Auswahl an Hilfswerkzeugen verhindert durch menschliche Faktoren bedingte Abweichungen und ermöglicht so eine zuverlässige quantitative Messung.
- Es sind weder Positionierung noch andere Vorbereitungen erforderlich. Anwender können einfach das Messobjekt auf den Objekttisch platzieren und die Aufnahme per Klick starten. Damit muss für die Messung kein Fachpersonal mehr herangezogen werden.
- 3D-Formen können mit hoher Geschwindigkeit und Genauigkeit gemessen werden. Dadurch ist es möglich, eine große Anzahl von Messobjekten in kurzer Zeit zu messen, was zur Qualitätsverbesserung beiträgt.
Dieses System ermöglicht auch Vergleiche mit früheren 3D-Daten und CAD-Daten sowie eine einfache Datenanalyse, wie z. B. die Verteilung innerhalb der Toleranzen. Es kann effektiv für eine Vielzahl von Zwecken eingesetzt werden, einschließlich Produktentwicklung, Trendanalysen in der Produktion und Stichprobenprüfungen.