Messung der Ebenheit
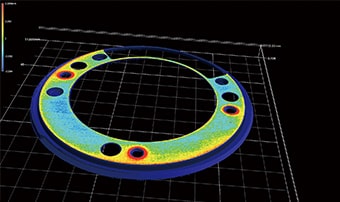
Der Grad der Ebenheit einer Objektoberfläche ist bei der Herstellung von industriellen Produkten und der Gewährleistung von Qualität von hoher Bedeutung. Der zulässige Bereich der Oberflächenunregelmäßigkeiten wird durch die Ebenheit bestimmt, die mit Toleranzen kontrolliert werden muss. Aus diesem Grund ist eine präzise und quantitative Messung unerlässlich. Ohne sie können Formfehler übersehen werden, was nicht nur die Einhaltung der Qualität erschwert, sondern auch die nachfolgenden Prozesse beeinträchtigen und die Produktionsquote senken kann.
Auf dieser Seite werden die Grundlagen der Ebenheit und die Herausforderungen bei gängigen Ebenheitsmessungen erläutert. Zudem werden Lösungen für die verschiedenen Herausforderungen beschrieben, mit denen Anwender derzeit konfrontiert sind.
- Ebenheit
- Warum die Parallelität auch wichtig für Welligkeit und Verdrehung ist
- Herausforderung bei gängigen Ebenheitsmessungen
- Lösung von Herausforderungen bei der Ebenheitsmessung
- Zusammenfassung: Erhebliche Verbesserung der Benutzerfreundlichkeit und Effizienz bei der Ebenheitsmessung
Ebenheit
Ebenheit wird als der Unterschied zwischen einer Oberflächenform und einer geometrisch korrekten Ebene definiert. Die folgende Abbildung zeigt ein Bild einer Objektoberfläche.
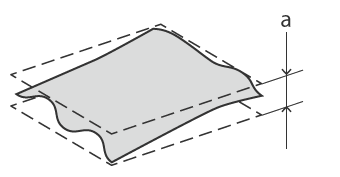
- a
- 0,1 mm oder weniger
Angenommen, das Messobjekt liegt zwischen zwei vollkommen flachen und parallelen Ebenen. Der Abstand zwischen diesen Ebenen ist die Ebenheit. Mit anderen Worten: Wenn die Toleranz angibt, wie flach das Objekt sein soll, müssen der konvexeste Teil und der konkavste Teil innerhalb zweier paralleler Ebenen oberhalb und unterhalb der Oberfläche liegen, die durch den angegebenen Abstand voneinander getrennt sind.
In dieser Abbildung ist der Abstand von 0,1 mm oder weniger als Toleranz definiert. In Zeichnungen wird die Ebenheit mit einem Symbol und einer Zahl angegeben, wie in der folgenden Abbildung gezeigt.
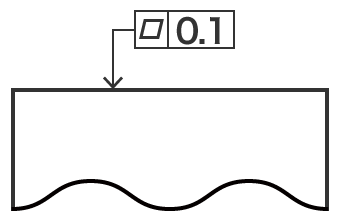
Warum die Parallelität auch wichtig für Welligkeit und Verdrehung ist
Die Ebenheit kann aufgrund verschiedener Faktoren die Toleranzen überschreiten. Wenn zum Beispiel Komponenten auf einer Leiterplatte montiert werden, kann sich die Leiterplatte durch die Erwärmung während des Reflow-Prozesses verziehen. Bleche können aufgrund von Eigenspannungen, die durch das Pressen (z. B. Stanzen oder Ziehen) verursacht werden, unbeabsichtigte Wölbungen, Dehnungen oder Oberflächenunregelmäßigkeiten aufweisen.
Außerdem kann es zu einem komplexen Zusammenspiel von Wölbung, Welligkeit, Dehnung, Verdrehung und anderen Verformungen aufgrund verschiedener Faktoren wie Wärmeausdehnung und -kontraktion, Eigenspannung und ungleichmäßiger Materialstärke kommen. Kurz gesagt, Objekte verformen sich nicht immer so, wie man es von ihnen erwartet. In den meisten Fällen verformen sich Objekte in drei Dimensionen, was zu einer Verformung von Seiten führt, die eigentlich parallel sein sollten. Um diese Verformung zu kontrollieren, ist die Prüfung der Parallelität wichtig.
Parallelität ist eine Form- und Lagetoleranz, die besagt, dass zwei Linien oder Ebenen parallel zueinander sind. Der Hauptunterschied zwischen Ebenheit und Parallelität besteht in der Verwendung eines Bezugspunkts (einer Bezugsebene oder -linie).
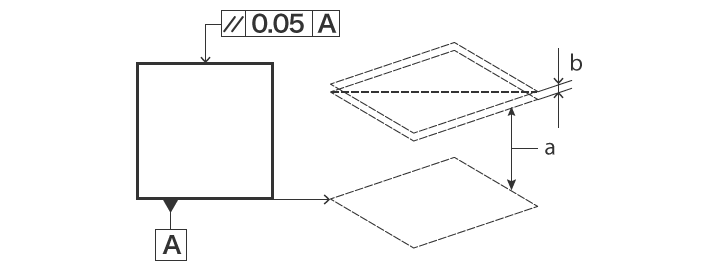
- a
- Parallel
- b
- 0,05 mm oder weniger
Die durch den Richtungspfeil in der Abbildung angezeigte Ebene muss parallel zur Bezugsebene A verlaufen (eine Ebene, die auch dann als eben gilt, wenn das Messobjekt selbst Wellen aufweist) und zwischen zwei projizierten Ebenen liegen, die in Richtung des besagten Richtungspfeils nicht mehr als 0,05 mm voneinander entfernt sind.
Bei dünnen Messobjekten wie Metallplatten, Kunststoffplatten und -folien, Leiterplatten und Smartphone-Schutzglas können Schwankungen in der Dicke zu Wölbung, Welligkeit, Verdrehung und Dehnung führen, was wiederum die Ebenheit und Parallelität beeinträchtigen kann.
Herausforderung bei gängigen Ebenheitsmessungen
In vielen Fällen wird die Verformung durch Spannungen wie Hitze oder Eigenspannung während der Bearbeitung des Materials verursacht. Bei Blechmaterial mit ungleichmäßiger Dicke kann die Ebenheit je nach Lagertemperatur oder Unterschieden in der Wärmeausdehnungsrate die Toleranzen überschreiten, was zu fehlerhaften Formen führt, die die darauffolgenden Prozesse und die Produktionsquote beeinträchtigen.
Wenn sich zum Beispiel eine Leiterplatte verzieht oder wölbt, kann dies zu einem Abheben der Anschlussdrähte montierter elektronischer Komponenten oder anderen Kontaktfehlern führen. Wenn die Oberfläche eines Wafers gewölbt oder gekrümmt ist, kann dies die Qualität der auf diesem Wafer hergestellten Chips beeinträchtigen. Um eine stabile Produktqualität zu erhalten, ist es wichtig, die Oberflächenform der Materialien vor der Verformung sowie die Form der Produkte nach der Verformung korrekt zu messen, um festzustellen, ob die erforderliche Ebenheit eingehalten wird.
Herausforderungen bei der Ebenheitsmessung mit einem 3D-Koordinatenmessgerät
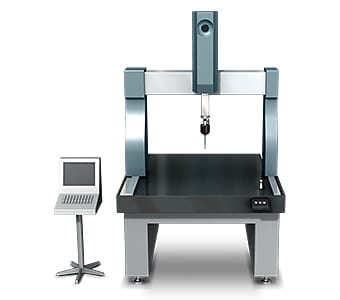
Bei einer normalen Messung der Ebenheit mit einem 3D-Koordinatenmessgerät ist es erforderlich, mit der Spitze des Messtasters mehrere Punkte auf der Oberfläche des Messobjekts zu berühren.
Wenn die Messfläche groß ist, kann die Präzision der Messung verbessert werden, indem die Anzahl der Messpunkte erhöht wird, um mehr Messdaten zu sammeln.
Dies beinhaltet jedoch die folgenden Herausforderungen:
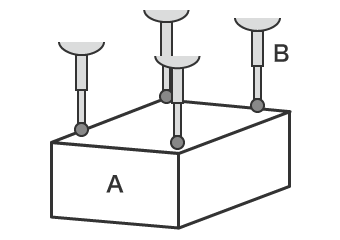
- a
- Messobjekt
- b
- Messtaster
- Da die Messung durch den Kontakt einzelner Punkte erfolgen muss, ist es schwierig, die Form des gesamten Messobjekts zu erkennen.
- Um mehr Messwerte zu erhalten, müssen mehr Punkte gemessen werden, was mehr Zeit in Anspruch nimmt. Dennoch ist es weiterhin nicht möglich, die detaillierte Form der gesamten Oberfläche zu erkennen.
Lösung von Herausforderungen bei der Ebenheitsmessung
Die Verwendung gängiger 3D-Koordinatenmessgeräte ist zeitaufwändig, weil diese mehrere taktile Messungen an dreidimensionalen Messobjekten und Flächen erfordern. Dieser Messmethode mangelt es auch an Zuverlässigkeit, da sie von verschiedenen Anwendern beeinflusst wird und es schwierig ist, aus Punktmessungen verwertbare Daten zu gewinnen.
Um diese Messprobleme zu lösen, hat KEYENCE das 3D-Profilometer der Modellreihe VR entwickelt.
Die Modellreihe VR erfasst präzise die 3D-Form der gesamten Oberfläche, ohne das Messobjekt zu berühren. Ein 3D-Scan des Messobjekts kann in nur einer Sekunde abgeschlossen werden, wodurch eine hochpräzise Messung der Oberflächenform möglich ist. In diesem Abschnitt werden einige Vorteile der Modellreihe VR vorgestellt.
Vorteil 1: Die 3D-Form der gesamten Messobjektoberfläche kann mit einer einzigen Messung präzise und vollständig in nur einer Sekunde erfasst werden
Die Modellreihe VR erfasst Oberflächendaten (800.000 Punkte) für die 3D-Form des Messobjekts in nur einer Sekunde, was die für die Messung einer großen Anzahl von Punkten erforderliche Zeit erheblich reduziert. Sie misst sofort und präzise die maximalen und minimalen Unregelmäßigkeiten auf der gesamten Messobjektoberfläche und ermöglicht so eine schnelle Beurteilung der Ebenheit auf der Grundlage der voreingestellten Toleranz.
Die Modellreihe VR kann auch Profilmessungen an bestimmten Orten durchführen. Auch nach der Messung können Profile an verschiedenen Stellen aus den 3D-Scandaten erfasst werden, ohne das Messobjekt erneut zu scannen.
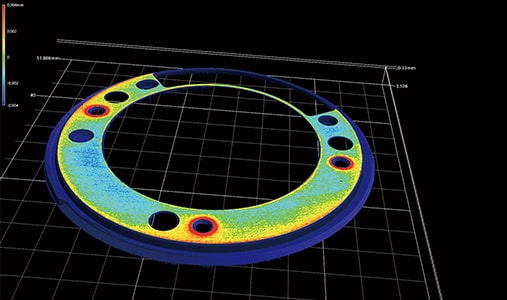
Vorteil 2: Quantitative Ebenheitsmessung bei Einrichtung und Anwendung
Die Messung von 3D-Formen kann mit einem einfachen Mausklick durchgeführt werden. Da eine automatische Positionskorrektur anhand von Messobjektdaten möglich ist, ist eine Nivellierung oder Positionierung nicht erforderlich. Diese Modellreihe umfasst auch die neue „Smart Measurement“-Funktion, die den Messbereich automatisch konfiguriert und den Objekttisch entsprechend der Größe des Messobjekts bewegt. Damit entfällt die Arbeit, die bislang für die Einstellung der Messlänge und des Z-Bereichs erforderlich war.
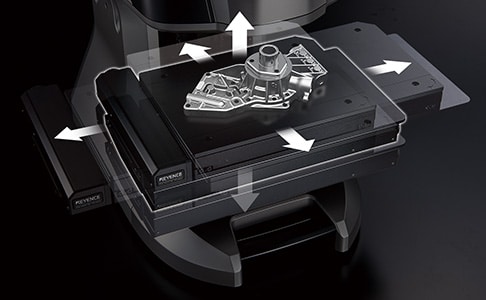
Die große Auswahl an Hilfswerkzeugen ermöglicht es, die für Ebenheits- und Parallelitätsmessungen erforderlichen Einstellungen einfach durchzuführen.
Zusätzlich zur einfachen Konfiguration ermöglichen die Hilfswerkzeuge eine einfache Bedienung des Systems auch ohne spezielle Fachkenntnisse. So können auch ungeübte Anwender, die mit Messungen nicht vertraut sind, Ebenheitsmessungen in kürzester Zeit durchführen. Dadurch kann die Anzahl der Proben nicht nur für Prototypen und Versuche, sondern auch für die Messung und Prüfung von Produkten bei der Serienfertigung problemlos erhöht werden.
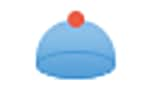
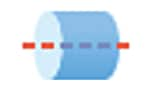

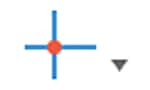
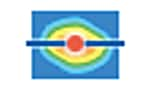
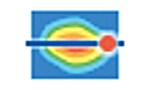
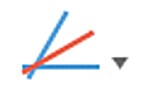
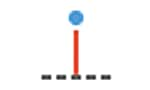
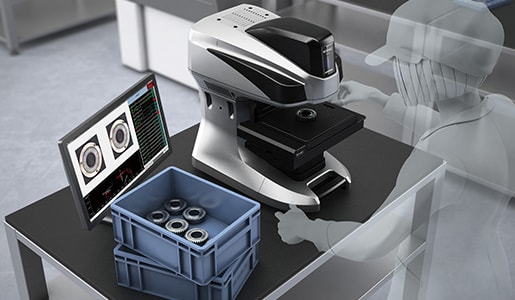
Zusammenfassung: Erhebliche Verbesserung der Benutzerfreundlichkeit und Effizienz bei der Ebenheitsmessung
Die Modellreihe VR kann die 3D-Form der gesamten Messobjektoberfläche, einschließlich Wölbung, Welligkeit, Verdrehung und Dehnung, durch 3D-Scans mit hoher Geschwindigkeit sofort und präzise messen, ohne das Messobjekt zu berühren. Dies ermöglicht eine schnelle Messung der Ebenheit.
- Da die gesamte Oberfläche gemessen wird, ist es möglich, alle Stellen auf dem Messobjekt zu identifizieren, an denen die Ebenheit die Toleranz überschreitet, und die Profilmessung an jeder gewünschten Position durchzuführen.
- Berührungslose, hochpräzise Messungen sind selbst bei weichen Messobjekten wie Gummi und flexiblem Kunststoff möglich.
- Es ist keine Positionierung erforderlich. Anwender können einfach das Messobjekt auf den Objekttisch platzieren und die Aufnahme per Klick starten.
- Da 3D-Formen bei hohen Geschwindigkeiten mit hoher Genauigkeit gemessen werden können, kann eine große Anzahl an Messobjekten in kurzer Zeit gemessen werden.
- Mehrere Messdatensätze können einfach und quantitativ verglichen und analysiert werden.
So können Parameter wie die Ebenheitstoleranz für mehrere Messungen gleichzeitig konfiguriert werden. Die Identifizierung von OK/n.i.O.-Produkten und die gemeinsame Nutzung von Daten ist möglich und ermöglicht eine schnelle Analyse von n.i.O.-Produkten. Die Modellreihe VR kann die Arbeitseffizienz bei Messungen, Fehleranalysen und vorbeugender Wartung erheblich verbessern.