Messung von Graten
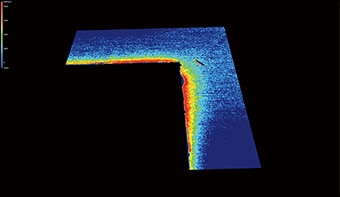
Der Begriff „Grat“ wird üblicherweise beim Pressen, Schneiden und an anderen metallverarbeitenden Arbeitsplätzen verwendet. Personen, die nicht in diesem Bereich tätig sind, ist der Begriff jedoch möglicherweise nicht geläufig. Auf dieser Seite wird erklärt, was Grate sind und warum sie gebildet werden. Zudem werden Herausforderungen bei der Messung von Graten zur Qualitätskontrolle sowie geeignete Lösungsvorschläge vorgestellt.
- Grate
- Arten und Kategorien von Graten
- Herausforderung bei gängigen Messungen von Graten
- Lösung von Herausforderungen bei der Gratmessung
- Zusammenfassung: Erhebliche Verbesserung und höhere Effizienz bei komplexen Formmessungen von Graten
Grate
Ein Grat ist eine erhabene Metallkante, die sich beim Scheren und Lochen mit einer Presse auf der Schnittfläche bildet. Grate werden oft auch als Splitter oder Auffaserungen bezeichnet.
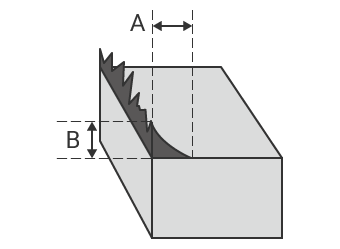
- A
- Dicke der Gratbasis
- B
- Grathöhe
Der Kontakt mit Graten an einer Kante kann zu Verletzungen an der Hand führen. Grate können auch eine korrekte Montage oder Verbindung behindern. Um diese Herausforderungen zu vermeiden, müssen die Grate durch Polieren der Kanten entfernt werden. Wenn Grate jedoch nicht vollständig entfernt werden können, ist es notwendig, Zeichnungsanweisungen bezüglich der Oberflächen zu geben, auf denen Grate erlaubt sind.
Die Größe des Grates wird durch die Höhe oder die Dicke der Basis angezeigt.
Arten und Kategorien von Graten
Neben Pressen, Schneiden und anderen Bearbeitungsmethoden werden Grate auch durch verschiedene andere Umformverfahren wie Gießen, Schmieden und Kunststoffformen erzeugt. Grate lassen sich je nach Umformverfahren in die folgend angeführten Arten einteilen, wobei jede Art ihre eigenen spezifischen Ursachen hat.
Durch Schneiden oder Schleifen erzeugte Grate
- Umformverfahren:
- Maschinelle Bearbeitung (Drehen, Fräsen, Bohren, Schleifen)
- Ursache:
- Bei der Erzeugung von Spänen kam es in einem Teil des Materials zu plastischem Fließen.
Durch Scheren erzeugte Grate
- Umformverfahren:
- Kunststoffbearbeitung (Scheren, Pressen)
- Ursache:
- In einem Teil des Materials im Zwischenraum zwischen der Matrize und dem Stempel kam es zu plastischem Fließen.
Durch Gießen oder Kunststoffguss erzeugte Grate
- Umformverfahren:
- Gießen, Kunststoffguss
- Ursache:
- In einem Teil der Materialoberfläche an der Kontaktfläche der Gussform oder des Werkzeugs kam es zu plastischem Fließen.
Durch plastische Verformung erzeugte Grate
- Umformverfahren:
- Schmieden, Walzen
- Ursache:
- In einem Teil des Materials im Bereich der Gratbahn oder der Rücklaufrinne kam es zu plastischem Fließen.
Herausforderung bei gängigen Messungen von Graten
Grate, die den zulässigen Bereich (die Toleranz) an Pressteilen überschreiten, können zu Montagefehlern, Schweißfehlern und Verbindungsfehlern führen.
Das Messen und Prüfen der Schnittflächen von Pressteilen kann die Qualität, die Montage und die Zuverlässigkeit des Teils nach dem Versand sicherstellen.
Bisher erfolgte die Messung von durch Pressen entstandenen Graten vorwiegend mit Profilmesssystemen. Diese Methode beinhaltet jedoch die folgenden Herausforderungen:
Herausforderung bei der Messung von Graten mit einem Profilmesssystem
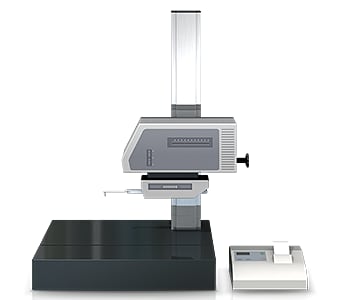
Ein Profilmesssystem oder Konturograph misst und erfasst das Profil eines Messobjekts, indem es dessen Oberfläche mit einem Taststift nachfährt. In den letzten Jahren wurden Profilmesssysteme entwickelt, die mit einem Laser anstelle eines Taststifts komplexe Formen messen, indem sie das Profil berührungslos verfolgen. Einige Modelle sind sogar in der Lage, Messungen sowohl der Ober- als auch der Unterseite durchzuführen.
Ein Profilmesssystem muss eine genaue Messlinie für die Form der zu messenden Grate zeichnen.
Dies beinhaltet die folgenden Herausforderungen:
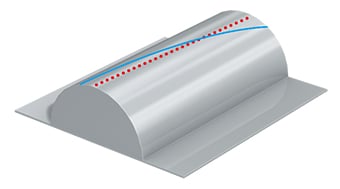
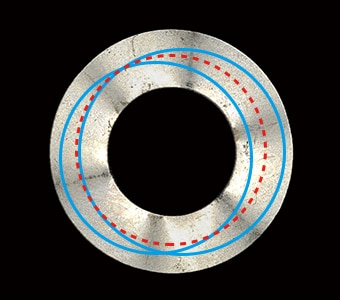
- Die Messung erfordert viel Zeit, einschließlich der Zeit für die Befestigung der Probe auf der Vorrichtung und deren Ausrichtung. Es sind zudem Kenntnisse und Fähigkeiten im Umgang mit Profilmesssystemen erforderlich, um ein Messobjekt genau zu nivellieren.
- Der Taststift eines Profilmesssystems bewegt sich in einem Bogen auf und ab, der auf dem Drehpunkt des Tastarmes zentriert ist, und die Tastspitze bewegt sich auch in Richtung der X-Achse, was zu Fehlern in den Daten der X-Achse führt.
- Das Nachzeichnen der gewünschten Linie mit dem Taststift ist eine äußerst schwierige Arbeit, und selbst eine leichte Verschiebung des Taststifts führt zu Fehlern in den Messungen.
- Es ist auch schwierig, die Anzahl der Messobjekte zu erhöhen, weil man bestimmte Positionen für die Messung festlegen muss.
- Es kann nur ein Teil eines Messobjekts gemessen werden, und die Auswertung der gesamten Oberfläche ist nicht möglich.
Lösung von Herausforderungen bei der Gratmessung
Die typischerweise zur Messung von Graten verwendeten Messgeräte beschränken sich auf die Messung von dreidimensionalen Messobjekten und Flächen mittels Punkt- oder Linienkontakt, was zu einer geringen Zuverlässigkeit der Messwerte führt. Um diese Messprobleme zu lösen, hat KEYENCE das 3D-Profilometer der Modellreihe VR entwickelt.
Die Modellreihe VR erfasst präzise die 3D-Form der gesamten Oberfläche, ohne das Messobjekt zu berühren. Ein 3D-Scan des Messobjekts auf dem Objekttisch kann in nur einer Sekunde abgeschlossen werden, wodurch eine hochpräzise Messung der 3D-Form möglich ist. Das System ist in der Lage, sofortige und quantitative Messungen durchzuführen, ohne fehlerhafte Messergebnisse zu erhalten. In diesem Abschnitt werden einige Vorteile der Modellreihe VR vorgestellt.
Vorteil 1: Messung der gesamten Oberfläche für die Analyse der gesamten Form.
Mit der Modellreihe VR lassen sich alle Oberflächendaten in einer einzigen Messung in 3D erfassen. Die Gesamtform des Messobjekts kann erfasst werden, einschließlich der höchsten und der tiefsten Punkte. Da die Messobjekte einfach und schnell identifiziert werden können, erübrigen sich wiederholte Messungen, wenn die genaue Position des Messobjekts nicht bekannt ist. Anwender können einfach das Messobjekt auf den Objekttisch platzieren und die Aufnahme per Klick starten. Es sind keine Anpassungen bei den einzelnen Messungen erforderlich. Deshalb können auch mit verschiedenen Anwendern benutzerunabhängige Messergebnisse erzielt werden.
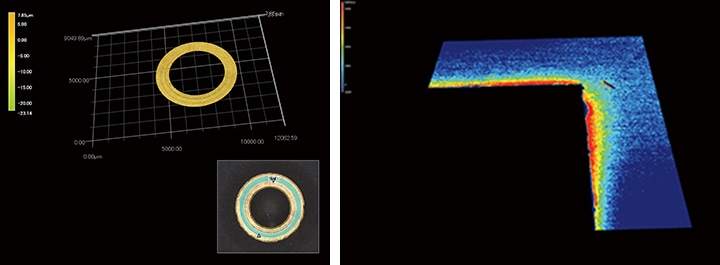
Im Gegensatz zu bisher verwendeten Messgeräten ist die Modellreihe VR in der Lage, Grate, die sich über eine große Fläche bilden, problemlos zu messen, was bisher nur mit großem Aufwand möglich war. Messwerkzeuge, mit denen sich eine Vielzahl von Messungen leicht durchführen lassen, sind ebenfalls enthalten. So können auch Anwender, die mit Messungen nicht vertraut sind, einfach und sofort Messungen durchführen, und es muss kein Fachpersonal dafür beauftragt werden.
Vorteil 2: Führen Sie schnelle, hochpräzise Messungen durch.
Eine einzige Messung, die die gesamte Oberfläche abdeckt, kann in wenigen Sekunden durchgeführt werden. Da die Messung mit bisher verwendeten Messgeräten viel Zeit erforderte, war es nicht einfach, die Anzahl der Proben zu erhöhen.
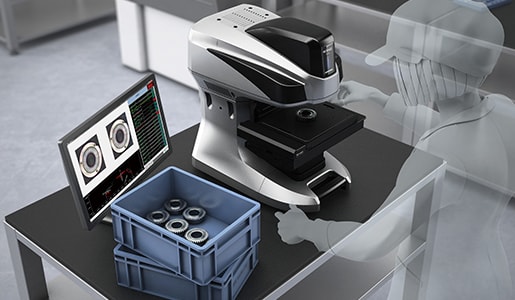
Die Modellreihe VR ist in der Lage, Messobjekte schnell und einfach zu messen. Sie kann für hochpräzise 3D-Messungen für eine Vielzahl von Zwecken eingesetzt werden. Neben der Entwicklung und Erprobung kann sie auch für Stichprobenprüfungen oder 100%-Inspektionen von Kleinserien oder hochwertigen Produkten eingesetzt werden. Sie kann den Vertrieb von fehlerhaften Produkten reduzieren und ermöglicht die einfache Erstellung von Berichten. Dies trägt dazu bei, Vertrauen zu gewinnen, ohne übermäßig viel Zeitaufwand investieren zu müssen.
Zusammenfassung: Erhebliche Verbesserung und höhere Effizienz bei komplexen Formmessungen von Graten
Die Modellreihe VR kann 3D-Messobjekte präzise und sofort mit hoher Geschwindigkeit messen, ohne das Messobjekt zu berühren. Selbst schwierige Messungen wie die Höhe und Position von Graten können in nur einer Sekunde durchgeführt werden. Die Modellreihe VR löst viele Herausforderungen, die bei gängigen Messgeräten auftreten können.
- Da die gesamte Oberfläche erfasst wird, kann die Modellreihe VR problemlos große Bereiche messen. Es können präzise Beurteilungen durchgeführt werden, die sicherstellen, dass auch feine Grate nicht übersehen werden. Dank der kurzen Messzeit lässt sich die Anzahl der gemessenen Proben leicht erhöhen.
- Dies verhindert durch menschliche Faktoren bedingte Abweichungen und ermöglicht so eine zuverlässige quantitative Messung.
- Es sind weder Positionierung noch andere Vorbereitungen erforderlich. Anwender können einfach das Messobjekt auf den Objekttisch platzieren und die Aufnahme per Klick starten. Damit muss für die Messung kein Fachpersonal mehr herangezogen werden.
- 3D-Formen können mit hoher Geschwindigkeit und Genauigkeit gemessen werden. Dadurch ist es möglich, eine große Anzahl von Messobjekten in kurzer Zeit zu messen, was zur Qualitätsverbesserung beiträgt.
Die Modellreihe VR ermöglicht auch Vergleiche mit früheren 3D-Messdaten und CAD-Daten sowie eine einfache Datenanalyse, wie z. B. die Verteilung innerhalb der Toleranzen. Das System kann effektiv für eine Vielzahl von Zwecken eingesetzt werden, einschließlich Produktentwicklung, Trendanalysen in der Produktion und Stichprobenprüfungen.