Messung von Werkzeugverschleiß
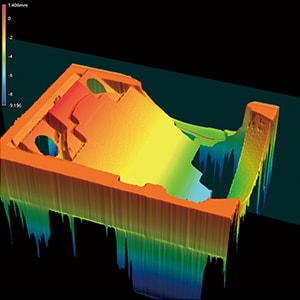
Matrizen sind unverzichtbar für die Formung von Produkten wie Autoteilen, Baumaterialien, Verbrauchsgütern und elektronischen Komponenten. Da die Senkung der Kosten für die Herstellung von Werkzeugen und die Verlängerung der Lebensdauer direkt mit den Produktkosten und der Produktqualität zusammenhängen, sind Verbesserungen im Werkzeugbau äußerst wichtig für die Verbesserung unseres täglichen Lebens.
Da Matrizen für die Formung einer Vielzahl von Materialien unerlässlich sind, wird auf dieser Seite der Verschleiß betrachtet, der bei der Verwendung von Matrizen auftritt, und es werden Gegenmaßnahmen zur Verlängerung der Lebensdauer von Matrizen auf der Grundlage des derzeit verfügbaren Wissens erläutert. Außerdem werden Methoden zur Messung des Werkzeugverschleißes, Herausforderungen bei bisher verwendeten Messungen und Lösungen für diese Herausforderungen vorgestellt.
- Werkzeugverschleiß
- Gegenmaßnahmen bei abnormalem Verschleiß
- Herausforderungen bei gängigen Messungen von Werkzeugverschleiß
- Eine Lösung für Herausforderungen bei der Messung von Werkzeugverschleiß
- Zusammenfassung: Erhebliche Verbesserung und höhere Effizienz bei komplexen Messungen von Werkzeugverschleiß
Werkzeugverschleiß
Werkzeugverschleiß ist ein Phänomen, bei dem die Oberfläche einer Matrize (oder von anderen Werkzeugen) durch die Reibung zwischen den Messobjekten abgenutzt wird. Werkzeugverschleiß wird in abnormalen und normalen Verschleiß unterteilt. Abnormaler Verschleiß wird durch ungeeignetes Material oder ungeeignete Form, Metallermüdung und Korrosion verursacht. Normaler Verschleiß wird durch den Kontakt der Messobjekte oder durch Reibung verursacht, die die Oberfläche der Matrize allmählich verkleinert.
Abnormaler Verschleiß
Abnormaler Verschleiß kann zu fatalen Schäden führen, wie z. B. Betriebsausfall oder Beschädigung des Formhohlraums oder des Kerns. Fünf der typischen Arten von abnormalem Verschleiß werden nachfolgend erklärt. Unter diesen Arten von abnormalem Verschleiß treten abrasiver Verschleiß und adhäsiver Verschleiß bei Matrizen am häufigsten auf. Der Verschleißprozess dieser beiden Arten wird als Fressen bezeichnet.
- Abrasiver Verschleiß:
- Abrasiver Verschleiß wird in Zweikörperverschleiß und Dreikörperverschleiß unterteilt. Zweikörperverschleiß tritt auf, wenn sich ein härteres Material in ein weicheres Material eingräbt. Dreikörperverschleiß tritt auf, wenn die Oberfläche des Werkzeugs durch hartes Verschleißpulver (harte Partikel) mechanisch abgeschliffen wird.
-
Zweikörperverschleiß - A
- Härteres Material
- B
- Weicheres Material
Dreikörperverschleiß - A
- Härteres Material
- B
- Weicheres Material
- C
- Harte Partikel
- Adhäsiver Verschleiß:
- Adhäsiver Verschleiß ist ein Verschleißphänomen, bei dem sich berührende, hervorstehende Stellen aneinander haften und die anhaftenden Stellen dann von der Oberfläche getrennt werden. Dieser Vorgang wird auch als Festfressen bezeichnet.
-
- A
- Berührende Teile
- B
- Adhäsion und Ablösung
- Ermüdungsverschleiß:
- Diese Art von Verschleiß entsteht durch Metallermüdung aufgrund wiederholter Starts und Stopps des Betriebs. Wiederholte Belastung führt zu einer Kaltumformung der Oberfläche, wodurch mit der Zeit feine Risse entstehen. Diese kleinen Risse entwickeln sich schließlich zu größeren Rissen, die zu einer Ablösung der Oberfläche führen. Die Scherspannung, die die feinen Risse verursacht, ist an einem Punkt leicht unterhalb der Oberfläche am höchsten. Von diesem Punkt aus bilden sich die größeren Risse. Es kann zur Abtrennung von Fischschuppenformen (Abblätterung) oder großen Blättern (Abschälung) kommen.
- Fressverschleiß:
- Diese Art von Verschleiß bildet winzige Grübchen auf der Oberfläche als Ergebnis wiederholter kleiner Bewegungen (Fressen), die Reibungskräfte an den Oberflächen der Messobjekte erzeugen, die zusammengefügt werden. Feine Risse entstehen an der Oberfläche, an der Fressverschleiß auftritt. Da an diesen Stellen eine Kombination aus äußerer Belastung und Reibungskraft auftritt, wird die Dauerfestigkeit auf die Hälfte oder weniger des ursprünglichen Wertes reduziert, was zu einem Ermüdungsbruch führen kann.
- Korrosionsbedingter Verschleiß:
- Diese Art von Verschleiß tritt auf, wenn Oberflächenmaterial aufgrund einer elektrischen Potentialdifferenz zwischen den Metallen abgetragen wird, die in einer korrosiven Atmosphäre erzeugt wird. Die zusätzliche Reibung beschleunigt den Verschleiß weiter. Dies wird auch als chemischer Verschleiß bezeichnet. Er entsteht durch die mechanische Wirkung von Reibung und die chemische Reaktion mit einer gasförmigen oder flüssigen Atmosphäre. Wenn diese Art von Verschleiß in einer flüssigen Atmosphäre auftritt, wird sie auch als Erosionskorrosion bezeichnet.
Normaler Verschleiß
Dieser Verschleiß tritt bei normalem Gebrauch auf, wenn es weder abrasiven noch adhäsiven Verschleiß gibt. Normaler Verschleiß wird in Anfangsverschleiß und Dauerverschleiß unterteilt. Der Anfangsverschleiß wird auch als Anpassungsverschleiß bezeichnet. Er tritt auf, wenn feine Oberflächenunregelmäßigkeiten nach der Inbetriebnahme von den Materialien entfernt werden. Dauerverscheiß ist die normale Abnutzung, die bei fortgesetztem Gebrauch auftritt. Indem ein Messobjekt durch ein neues ersetzt wird, wenn es ein für normalen Verschleiß festgelegtes Maß erreicht, können Werkzeugausfälle und Defekte verhindert werden.
Gegenmaßnahmen bei abnormalem Verschleiß
In diesem Abschnitt werden die Gegenmaßnahmen bei abrasivem und adhäsivem Verschleiß erläutert, die typische Formen von abnormalem Werkzeugverschleiß sind.
Gegenmaßnahmen bei abrasivem Verschleiß
Die Gegenmaßnahmen für den abrasiven Verschleiß unterscheiden sich bei Zweikörper- und Dreikörperverschleiß.
- Zweikörperverschleiß:
- Mögliche Gegenmaßnahmen gegen den Zweikörperverschleiß sind die Erhöhung der Materialhärte und die Verwendung einer Stahlart, die große Mengen an Karbiden enthält. Da die Abriebfestigkeit in der Regel bei härterer Oberfläche höher ist, ist auch das Abschrecken, Nitrieren oder eine ähnliche Behandlung der Matrize effektiv.
- Dreikörperverschleiß:
- Um einen Dreikörperverschleiß zu verhindern, sollten Sie die Gleitflächen der Maschine vollständig abdichten, um das Eindringen von Sand oder anderen Schleifpartikeln zu verhindern. Eine wirksame Gegenmaßnahme ist der Einbau eines Filters in das Schmiersystem, damit solche Partikel schnell entfernt werden können, wenn sie in das System gelangen.
Gegenmaßnahmen bei adhäsivem Verschleiß
Mögliche Gegenmaßnahmen gegen den adhäsiven Verschleiß sind die Verwendung eines Werkzeugmaterials, das die erforderliche Härte und Robustheit aufweist. Tatsächlich sind den Gegenmaßnahmen jedoch Grenzen gesetzt, die nur durch eine Verbesserung des Werkzeugmaterials bewältigt werden können. Aus diesem Grund ist es notwendig, Gegenmaßnahmen zu ergreifen, die eine Adhäsion verhindern, indem der Reibungskoeffizient zwischen der Oberfläche des Werkzeugs und dem Werkstück verringern. Die Optimierung der Schmierung ist besonders wichtig. Es ist notwendig, das Schmiermittel gleichmäßig aufzutragen, die Werkzeuge so zu konstruieren, dass das Schmiermittel nicht ausläuft, und die Verarbeitungsbedingungen zu optimieren. Eine harte Oberflächenbehandlung zur Verringerung des Reibungskoeffizienten ist ebenfalls wirksam.
Herausforderungen bei gängigen Messungen von Werkzeugverschleiß
Es ist sehr wichtig zu überprüfen, ob der Werkzeugverschleiß innerhalb der Toleranzen liegt. Insbesondere bei Werkzeugen, die für die Umformung unter hohem Druck verwendet werden, ist eine genaue und quantitative Messung der 3D-Form erforderlich.
Bei gängigen Messungen von Werkzeugverschleiß werden Profilmesssysteme oder 3D-Koordinatenmessgeräte verwendet. Bei der Messung mit bisher verwendeten 3D-Koordinatenmessgeräten oder Profilmesssystemen gibt es jedoch verschiedene Herausforderungen. Dazu gehören die Expertise, die erforderlich ist, um genaue Messungen zu erhalten und die Schwankungen der Messwerte. Die Quantifizierung der gemessenen Daten ist ebenfalls schwierig. Auch die Trendanalyse und andere Analysen im Zusammenhang mit der Alterung von Werkzeugen sind problematisch.
Herausforderungen bei der Messung von Werkzeugverschleiß mit einem Profilmesssystem
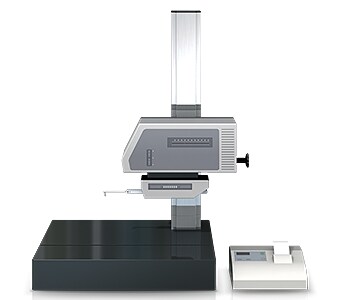
Ein Profilmesssystem oder Konturograph misst und erfasst das Profil eines Messobjekts, indem es dessen Oberfläche mit einem Taststift nachfährt. In den letzten Jahren wurden Profilmesssysteme entwickelt, die mit einem Laser anstelle eines Taststifts komplexe Formen messen, indem sie das Profil berührungslos verfolgen. Einige Modelle sind sogar in der Lage, Messungen sowohl der Ober- als auch der Unterseite durchzuführen.
Ein Profilmesssystem muss eine präzise Messlinie für die Messpunkte zeichnen.
Dies beinhaltet die folgenden Herausforderungen:

- Die Messung erfordert viel Zeit, einschließlich der Zeit für die Befestigung des Werkzeugs auf einer Vorrichtung und dessen Nivellierung. Es sind zudem Kenntnisse und Fähigkeiten im Umgang mit Profilmesssystemen erforderlich, um ein Messobjekt präzise zu nivellieren.
- Der Taststift eines Profilmesssystems bewegt sich in einem Bogen auf und ab, der auf dem Drehpunkt des Tastarmes zentriert ist, und die Tastspitze bewegt sich auch in Richtung der X-Achse. Dies führt zu Fehlern in den Daten auf der X-Achse.
- Das Nachzeichnen der gewünschten Linie mit dem Taststift ist eine äußerst schwierige Arbeit, und selbst eine leichte Verschiebung des Taststifts führt zu Fehlern in den Messungen.
- Es kann nur eine Stelle eines Messobjekts gemessen werden, und die Auswertung der gesamten Oberfläche ist nicht möglich.
Herausforderungen bei der Messung von Werkzeugverschleiß mit einem 3D-Koordinatenmessgerät
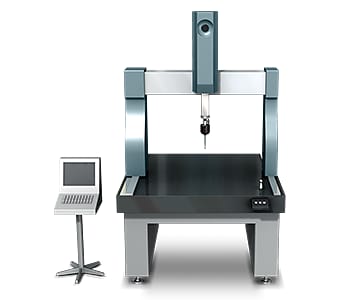
Gängige 3D-Koordinatenmessgeräte messen Formen, indem sie taktil mit einem Messtaster über die Oberfläche „scannen“, um die Form zu erfassen und zu messen. Bei dieser Art des Scannens wird eine große Anzahl von Punkten in einem bestimmten Abstand gemessen.
Diese Messung bringt jedoch folgende Herausforderungen mit sich:
- Die Sicherstellung, dass sich der Messtaster wie vorgesehen bewegt, ist eine äußerst schwierige Aufgabe. Insbesondere bei Geraden entlang der Mitte eines Zylinders oder einer gekrümmten Oberfläche oder bei Linien, die durch den Mittelpunkt eines Kreises verlaufen. Im Falle einer abgerundeten Ecke mit kleinem Mittelpunktswinkel hat selbst ein kleiner Fehler in der Messung starke Auswirkungen, da der gesamte Kreis aus einem kurzen Kreissegment berechnet wird. Derartige Ungenauigkeiten bei den Messpunkten können zu unterschiedlichen Messwerten führen.
- Wenn eine kleine 3D-Form gemessen wird, kann es sein, dass der Messtaster die Messpunkte nicht berühren kann. Da sich die Genauigkeit der Messung proportional zur Anzahl der gemessenen Punkte oder Linien verhält, ist es notwendig, eine große Anzahl von Punkten oder Linien zu messen.
So ist die Messung mit einem 3D-Koordinatenmessgerät mit erheblichen Herausforderungen verbunden. Dazu gehören fehlende Fachkenntnisse der Anwender, das Vorhandensein von Messobjekten, die überhaupt nicht gemessen werden können, und begrenzte Standorte, an denen das System installiert werden kann.
Eine Lösung für Herausforderungen bei der Messung von Werkzeugverschleiß
Die bisher verwendeten Messsysteme bringen Herausforderungen mit sich, wie z. B. den hohen Zeitaufwand für die Positionierung des Messobjekts und die Tatsache, dass die Messung von dreidimensionalen Messobjekten und Flächen mittels Punkt- oder Linienkontakt erfolgt. Um diese Messprobleme zu lösen, hat KEYENCE das 3D-Profilometer der Modellreihe VR entwickelt.
Die Modellreihe VR erfasst präzise die 3D-Form der gesamten Oberfläche, ohne das Messobjekt zu berühren. Die 3D-Form kann zudem durch einen 3D-Scan des Messobjekts auf dem Objekttisch in wenigen Sekunden mit hoher Präzision gemessen werden. Das System ist in der Lage, sofortige und quantitative Messungen durchzuführen, ohne fehlerhafte Messergebnisse zu erhalten. In diesem Abschnitt werden einige Vorteile der Modellreihe VR vorgestellt.
Vorteil 1: Messung einer großen Anzahl von Punkten in nur einer Sekunde
Die Modellreihe VR erfasst Oberflächendaten für die 3D-Form des Messobjekts in nur einer Sekunde, was die für die Messung einer großen Anzahl von Punkten erforderliche Zeit erheblich reduziert. Sie misst die maximalen und minimalen Unregelmäßigkeiten auf der gesamten Messobjektoberfläche und ermöglicht so eine schnelle Beurteilung aller Positionen auf der Grundlage der voreingestellten Toleranz. Dies ermöglicht die Bearbeitung von schwer zu definierenden Zuständen, wie z. B. dem Verschleißgrad oder Absplitterungen.

Sobald ein Werkstück gescannt wurde, kann sein Profil (Querschnitt) auch an anderen als den in der Vergangenheit überprüften Stellen gemessen werden. Dadurch muss dasselbe Messobjekt nicht mehr erneut eingestellt und gemessen werden.
Vorteil 2: Vergleich von Messungen zwischen Messobjekten oder mit CAD-Daten
Die Modellreihe VR kann mehr als nur effizient Daten sammeln. Messdaten können in einer Liste angezeigt werden und derselbe Analyseinhalt kann auf alle Daten gleichzeitig angewendet werden.
So ist es zum Beispiel möglich, die Formen von Produkten zu messen, die sowohl mit einem neuen als auch mit einem alten Werkzeug hergestellt wurden, und die Unterschiede in der Form, die sich aus den beiden Werkzeugen ergeben, zu erkennen. CAD-Daten können darüber gelegt werden, um schnell zu erkennen, wie sehr sich ein fehlerhaftes Produkt von einem guten Produkt unterscheidet. Dies ermöglicht eine einfache quantitative Analyse und Beurteilung des Werkzeugverschleißes.
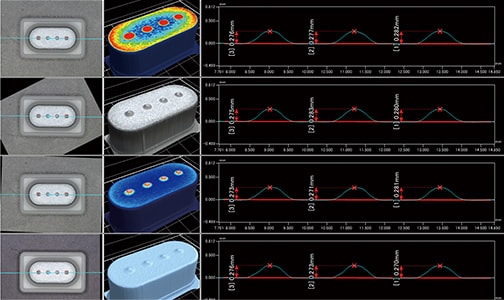
Die Modellreihe VR kann Messobjekte mit komplexen Formen schnell messen, was früher viel Zeit und Arbeit erforderte. Alle Messergebnisse sind digital, was den Arbeitsaufwand für den anschließenden Datenvergleich und die Analyse erheblich reduziert.
Zusammenfassung: Erhebliche Verbesserung und höhere Effizienz bei komplexen Messungen von Werkzeugverschleiß
Die Modellreihe VR ist in der Lage, den Werkzeugverschleiß schnell zu messen und zu quantifizieren. Diese Messung erforderte bisher viel Erfahrung, war zeitaufwändig oder bei komplexen Werkzeugen schwer durchzuführen. Dadurch kann die Modellreihe VR die Produktqualität mit einem höheren Maß an Genauigkeit und Effizienz beurteilen.
- Da die gesamte Oberfläche gemessen wird, werden Daten für eine große Anzahl von Punkten gleichzeitig erfasst. Dies kann den Zeitaufwand für die Messung komplexer Formen erheblich reduzieren.
- Mit der Modellreihe VR können mehrere Messdatensätze zum Vergleich in einer Liste angezeigt werden, sodass verschiedene Unterschiede in der durch Verschleiß verursachten Verformung erkannt und analysiert werden können.
- Durch das Scannen eines durch Pressen geformten Produkts und den Vergleich der gemessenen Daten mit den CAD-Daten ist es möglich, die Bedingungen des Werkzeugverschleißes genau zu bestimmen.
- Dies verhindert durch menschliche Faktoren bedingte Abweichungen und ermöglicht so eine zuverlässige quantitative Messung.
- Es sind weder Positionierung noch andere Vorbereitungen erforderlich: Das Messobjekt kann einfach auf den Objekttisch platziert werden und die Messung kann mit einem Klick gestartet werden. Damit muss für die Messung kein Fachpersonal mehr herangezogen werden.
- 3D-Formen können mit hoher Geschwindigkeit und Genauigkeit gemessen werden. Dadurch ist es möglich, eine große Anzahl von Messobjekten in kurzer Zeit zu messen, was zur Qualitätsverbesserung beiträgt.
Dieses System ermöglicht auch Vergleiche mit früheren 3D-Formdaten sowie eine einfache Datenanalyse, wie z. B. die Rauheitsverteilung. Es kann effektiv für eine Vielzahl von Zwecken eingesetzt werden, einschließlich der Trendanalyse des Werkzeugverschleißes im Laufe der Zeit und der Überprüfung der Bedingungen für den Materialverlust.