Messung komplexer 3D-Formen von Schweißraupen
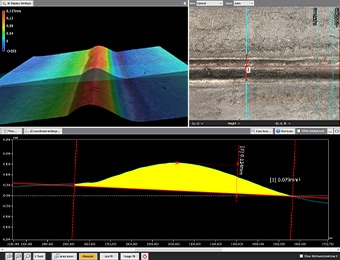
Schweißen ist eine Methode zum Verbinden von zwei Materialien an Verbindungsstellen durch den Einsatz von Energie wie Hitze oder Druck, mit oder ohne Verwendung eines Zusatzwerkstoffs. Schweißraupen, die an den Schweißnähten entstehen, sind äußerst wichtige Komponenten, die einen großen Einfluss auf die Festigkeit der Verbindung und die Produktqualität haben. Anhand der Form der Schweißraupe lässt sich beurteilen, ob der Schweißvorgang ordnungsgemäß ausgeführt wurde und ob Fehler oder Mängel vorhanden sind. Um eine Schweißraupe korrekt zu bewerten, muss ihre komplexe 3D-Form quantitativ gemessen werden, was eine Reihe von Herausforderungen mit sich bringt.
Auf dieser Seite finden Sie grundlegende Informationen über Schweißraupen und die neueste Methode, mit der Sie einfach und schnell präzise Messungen der 3D-Formen von Schweißraupen durchführen können.
- Schweißraupen
- Optimale Abmessungen und Form der Schweißraupen
- Mängel bei Schweißraupenformen
- Lösungen für die Messung von Schweißraupenformen
- Zusammenfassung: Die Modellreihe VR bietet erhebliche Verbesserungen bei der Messung von Schweißraupenformen, die zuvor nur schwer zu messen waren
Schweißraupen
Wenn unedle Metalle durch Lichtbogenschweißen, Laserschweißen oder ähnliche Verfahren verbunden werden, entstehen konvexe, abgerundete Formen an der Oberfläche der Schweißstellen, die als Schweißraupen bezeichnet werden. Der Name bezieht sich auf das Aussehen dieser Schweißnähte, die an Raupen erinnern.
Bei der Herstellung von Metallrohren für verschiedene Zwecke wird die Schweißraupe durch Hochfrequenzschweißen an der Verbindungsstelle des Grundwerkstoffs nach dem Walzprofilieren gebildet. Bei verschiedenen anderen Schweißmethoden wird die Stelle, an der das Metall und das unedle Metall geschmolzen werden, ebenso als Schweißraupe bezeichnet, auch wenn die Form anders aussieht.

Optimale Abmessungen und Form der Schweißraupen
Dieser Abschnitt erklärt die Schweißraupenform für das typische Schweißverfahren des Lichtbogenschweißens.
Die Schweißraupenform ist korrekt, wenn sie die vorgeschriebenen Abmessungen einhält.
Vorgeschriebene Abmessungen und Form der Schweißraupen
Die optimalen Abmessungen für Schweißraupen sind genormt, und es ist wichtig, dass die Anforderungen an die Schweißraupenform während der Entwicklung, der Konstruktion und des gesamten Produktionsprozesses erfüllt werden.
Im Folgenden finden Sie einige gängige vorgeschriebene Abmessungen:
- Nahttiefe – Die Mindesttiefe der Schweißraupe.
- Einbrandtiefe – Der Abstand vom tiefsten Punkt des geschmolzenen Grundwerkstoffs und seiner Oberfläche.
- Nahtlänge – Die Mindestlänge von der Schweißnaht am Wurzelpunkt der Verbindung bis zum Schweißnahtgrund.
Bei der in der Abbildung unten gezeigten Schweißnaht ist der Beurteilungsmaßstab für die optimale Breite der Schweißraupe zum Beispiel, ob die Nahtlänge 80% oder mehr der Tiefe des dünneren Grundwerkstoffs beträgt oder nicht. Wenn die Tiefe des dünneren Grundwerkstoffs 20 mm beträgt, ist eine Nahtlänge von etwa 16 mm erforderlich, die die Breite der Schweißraupe bestimmt.
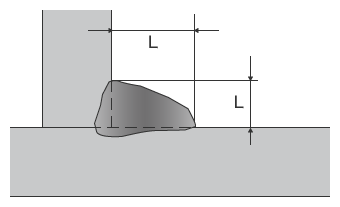
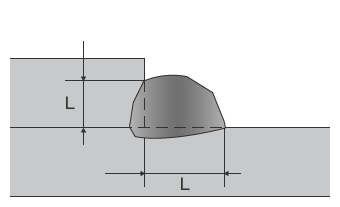
Abmessungen der Schweißraupen und Schweißstrom
Beim Lichtbogenschweißen ist der Schweißstrom ein Faktor, der die Abmessungen der Schweißraupen beeinflusst. Ein größerer Strom erzeugt größere Schweißraupen, während ein kleinerer Strom kleinere Schweißraupen erzeugt. Wenn die Schweißraupe nicht den geforderten Abmessungen oder der Form entspricht, müssen die Schweißbedingungen korrigiert werden, z. B. der Schweißstrom oder die Bewegungsgeschwindigkeit des Schweißbrenners.
Mängel bei Schweißraupenformen
Neben den Abmessungen gibt es eine Reihe von Mängeln, die bei der Oberflächenform der Schweißraupe beachtet werden müssen. Hier werden anhand von Abbildungen einige typische Mängel bei Schweißraupen und ihre Ursachen erklärt.
Überlappung
- Erscheinungsbild:
- Von Überlappung spricht man, wenn das geschmolzene Metall, das auf die Oberfläche des Grundwerkstoffs überläuft, abkühlt und als Schweißraupe erstarrt, ohne mit dem Grundmetall zu verschmelzen.
- Ursache:
- Die Überlappung wird durch eine niedrige Schweißgeschwindigkeit und eine übermäßige Zufuhr von Schweißgut verursacht. Die Überlappung bei einer Kehlnaht wird durch das Abtropfen von überschüssigem geschmolzenem Metall aufgrund der Schwerkraft verursacht.
-
Unterfüllung
- Erscheinungsbild:
- Unterfüllung liegt vor, wenn nicht genügend Zusatzwerkstoff in der Schweißnaht vorhanden ist, sodass die Gesamtdicke der Schweißnaht geringer ist als die Dicke des Grundwerkstoffs.
- Ursache:
- Unterfüllung wird durch falsche Schweißbedingungen (Schweißstrom oder -geschwindigkeit) verursacht.
-
Hinterschneidung
- Erscheinungsbild:
- Eine Hinterschneidung ist eine Rille, die sich am Schweißnahtgrund bildet, wenn auf Grundwerkstoff oder eine vorherige Schweißnaht geschweißt wird.
- Ursache:
- Eine Hinterschneidung wird in der Regel durch zu hohe Schweißströme oder -geschwindigkeiten verursacht.
-
Vertiefungen
- Erscheinungsbild:
- Vertiefungen sind Oberflächenmängel, die entstehen, wenn sich im Schweißgut Gashohlräume bilden, sich verfestigen und beim Entweichen des Gases ein Loch in der Oberfläche der Schweißraupe erzeugen. Gashohlräume, die sich innerhalb der Schweißraupe verfestigen, sind interne Mängel, die als Lunker bezeichnet werden.
- Ursache:
- Zu den Ursachen für Vertiefungen gehören Herausforderungen mit dem Schutzgas, unzureichendes Desoxidationsmittel, Öl, Rost, Beschichtungen oder andere Stoffe, die an der Oberfläche des Grundwerkstoffs haften, sowie Feuchtigkeit im Material.
-
- A
- Vertiefung
- B
- Lunker
Rissbildung
- Arten und Erscheinungsbilder:
- Unter Rissbildung versteht man Risse, die sich in einer heißen Schweißnaht unmittelbar nach dem Schweißen bilden. Die Risse werden grob in Erstarrungsrisse und Verflüssigungsrisse unterteilt. Erstarrungsrisse treten auf, wenn die Schweißnaht erstarrt. Verflüssigungsrisse treten beim Mehrlagenschweißen auf, wenn die vorherige Schweißschicht durch anschließendes Schweißen aufgeschmolzen wird. Je nach Lage und Form werden die Risse als Längsrisse, Grundrisse, Querrisse oder Kraterrisse klassifiziert.
-
- A
- Längsriss
- B
- Grundriss
- C
- Querriss
- D
- Kraterriss
Neben den Mängeln, die an der Form und dem Erscheinungsbild zu erkennen sind, gibt es weitere Mängel, die die Festigkeit der Schweißverbindung beeinträchtigen.
- Unvollständiges Einbrennen – wenn die Einbrandtiefe aufgrund unzureichender Erhitzung nicht die erforderliche Tiefe erreicht
- Unvollständiges Verschmelzen – wenn das geschmolzene Metall an einer bestimmten Stelle nicht mit dem Grundwerkstoff verschmilzt.
Da es sich hierbei um interne Mängel handelt, ist eine Prüfung anhand von Querschnittsproben erforderlich.
Lösungen für die Messung von Schweißraupenformen
Prüfungen sind unerlässlich, um die Qualität der Schweißraupen zu gewährleisten. Visuelle Vergleiche mit guten Produktmustern und Messsystemen erfordern ein hohes Maß an Geschick und Zeit, und die Beurteilung kann je nach Anwender variieren. Aufgrund des Systems und der Präzision sind Systeme zur automatisierten Inline-Prüfung in vielen Fällen nicht für Zwecke wie den Einsatz während der Forschungs- und Entwicklungsphase, Tests zur Festlegung der Schweißbedingungen, Stichprobenprüfungen oder die 100%-Inspektion von mehreren Produkten, die in kleinen Chargen hergestellt werden, geeignet.
Um diese Herausforderungen bei der Messung von Schweißraupen zu lösen, hat KEYENCE das 3D-Profilometer der Modellreihe VR entwickelt.
Die Modellreihe VR erfasst präzise die 3D-Form der gesamten Oberfläche, ohne das Messobjekt zu berühren. Die 3D-Form kann zudem durch einen 3D-Scan des Messobjekts auf dem Objekttisch in nur einer Sekunde mit hoher Präzision gemessen werden. Das System ist in der Lage, sofortige und quantitative Messungen durchzuführen. In diesem Abschnitt werden einige Vorteile der Modellreihe VR vorgestellt.
Vorteil 1: Die 3D-Form der gesamten Messobjektoberfläche kann mit einer einzigen Messung präzise und vollständig in wenigen Sekunden erfasst werden
Die Modellreihe VR erfasst Oberflächendaten in nur einer Sekunde. Dies ermöglicht eine hochpräzise und sofortige Messung und quantitative Beurteilung der 3D-Formen von komplexen Schweißraupen.
Die maximalen und minimalen Unregelmäßigkeiten der Oberfläche können in einer leicht verständlichen Farbkarte angezeigt werden, womit die Stellen, an denen Defekte aufgetreten sind, leicht identifiziert werden können. Es ist zudem möglich, detaillierte Profildaten zu erfassen, indem eine beliebige Stelle auf dem Messobjekt angegeben wird, z. B. die Position von Mängeln.
Selbst nach der Messung können Profildaten für andere Bereiche aus früheren 3D-Scandaten gewonnen werden, sodass das Messobjekt nicht mehr erneut gescannt werden muss. Darüber hinaus können Messdaten von mehreren Messobjekten nebeneinander verglichen werden und die gewünschten Bedingungen können auf mehrere Datensätze gleichzeitig angewendet werden. Dies führt zu einer erheblichen Reduzierung des Zeitaufwands und einer verbesserten Arbeitseffizienz.
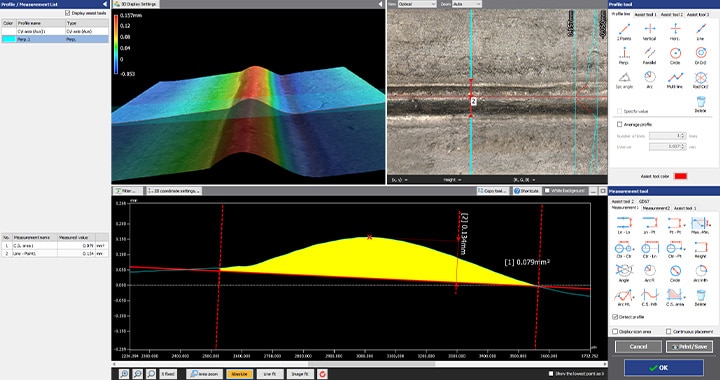
Vorteil 2: Die Bedienung ist anwenderfreundlich und die Messung kann auch von ungeübten Anwendern durchgeführt werden, ohne dass es zu anwenderspezifischen Abweichungen kommt
Die Messung von 3D-Formen kann ganz einfach durchgeführt werden, indem Sie das Messobjekt auf den Objekttisch legen und die Aufnahme starten. Diese Modellreihe umfasst die neue „Smart Measurement“-Funktion, die den Messbereich automatisch konfiguriert und den Objekttisch entsprechend der Größe des Messobjekts bewegt. Damit entfällt die Arbeit, die bislang für die Einstellung der Messlänge und des Z-Bereichs erforderlich war.
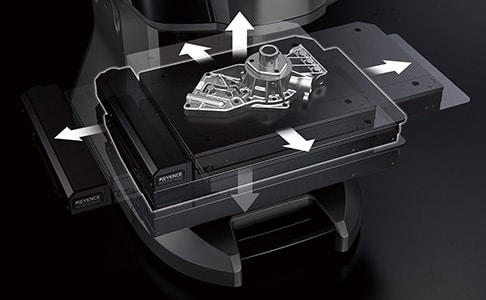
Die große Auswahl an Hilfswerkzeugen ermöglicht eine einfache und intuitive Konfiguration der gewünschten Messungen.
Zusätzlich zur einfachen Konfiguration ermöglichen die Hilfswerkzeuge eine einfache Bedienung des Systems, sodass selbst ungeübte Anwender, die mit Messungen nicht vertraut sind, Formen in nur einer Sekunde präzise messen können. Dadurch kann die Anzahl der Proben nicht nur in der Forschungs- und Entwicklungsphase und für Tests zum Festlegen der Bedingungen, sondern auch für die Messung und Prüfung von Produkten bei der Serienfertigung problemlos erhöht werden.
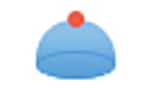
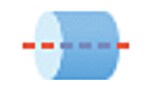
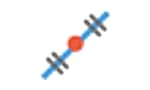
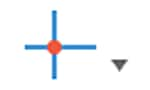
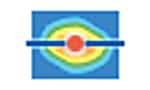
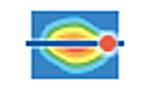
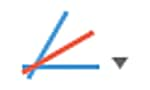
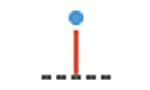
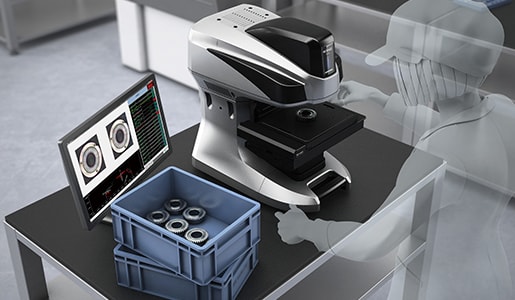
Zusammenfassung: Die Modellreihe VR bietet erhebliche Verbesserungen bei der Messung von Schweißraupenformen, die zuvor nur schwer zu messen waren
Die Modellreihe VR kann 3D-Messobjekte präzise und sofort mit hoher Geschwindigkeit messen, ohne das Messobjekt zu berühren. Schwierige Messungen wie die Identifizierung komplexer Unregelmäßigkeiten in 3D-Schweißraupenformen und die Erkennung von Mängeln können in nur einer Sekunde durchgeführt werden. Die Modellreihe VR löst viele Herausforderungen, die bei gängigen Messsystemen auftreten können.
- Abnormale Stellen auf einer Schweißraupe können in einer Farbkarte visualisiert werden.
- Sobald ein Scan abgeschlossen ist, kann jederzeit eine Profilmessung an einer beliebigen Stelle und ein Vergleich mehrerer Datensätze durchgeführt werden.
- Es sind weder Positionierung noch andere Vorbereitungen erforderlich. Anwender können einfach das Messobjekt auf den Objekttisch platzieren und die Aufnahme per Klick starten. Damit muss für die Messung kein Fachpersonal mehr herangezogen werden.
- Da 3D-Formen mit hoher Geschwindigkeit und Präzision gemessen werden können, ist die Messung einer großen Anzahl von Proben in kurzer Zeit möglich. Dies ist nützlich für Qualitätsverbesserungen.
- Dies verhindert durch menschliche Faktoren bedingte Abweichungen und ermöglicht so eine zuverlässige quantitative Messung.
Dieses System ermöglicht Vergleiche mit CAD-Daten und eine einfache Datenanalyse, wie z. B. die Verteilung innerhalb der Toleranzen. Es kann effektiv für eine Vielzahl von Zwecken eingesetzt werden, einschließlich Forschung und Entwicklung, Bestimmung von Schweißbedingungen, Stichprobenprüfungen, 100%-Inspektion von Kleinserienprodukten und Trendanalysen in der Produktion.