Nyírási lelógás pontos mérése vágott felületeken
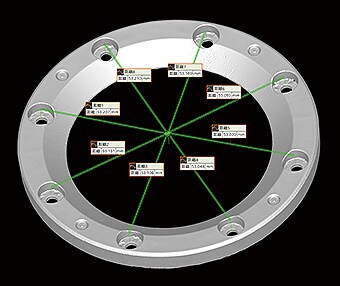
Sokféle présmegmunkálás létezik, ideértve a nyírást, hajlítást és húzást. Ezen típusok közül a nyírás magában foglalja a lyukasztást és a bevágásos megmunkálást is. A nyírással előállított felület a vágási felület, és a vágott felület alakjának vizsgálatával olyan jellemzőket lehet beazonosítani, mint a stancoló és a szerszám közötti hézag.
Ez a rész a nyírással kapcsolatos alapvető ismereteket és a lelógás elvét magyarázza el. Emellett a lelógás és más nyírási keresztmetszetek mérési problémáit is bemutatja, valamint megoldást ad ezekre a problémákra.
- Nyírási lelógás
- Nyírásból származó vágott felület
- Hézag
- Nyírási folyamat
- A lelógás mérésének nehézségei
- Megoldások a lelógás mérésére
- Összegzés: Drasztikus javulás és nagyobb hatékonyság a lelógások mérése során
Nyírási lelógás
A nyírási lelógás olyan jelenség, amely egy nyírással megmunkált termék felületén jelentkezik. Amikor a megmunkált anyagot stancolóval és szerszámmal vágják, akkor az anyagot a vágott felületen keletkező húzóerő húzza, így sima felület jön létre. Ezt a sima felületet nevezik lelógásnak. A méret és az alakzat a stancoló és a szerszám közötti hézagtól függően változik. A stancoló és a szerszám közötti hézag nagy mértékben befolyásolja a termék minőségét, valamint a présgép élettartamát.
Nyírásból származó vágott felület
A nyírásból származó vágási felület négy rétegből áll: lelógás, nyírási felület, törésfelület és sorja. Még ha maga a munkadarab sík lemez is, a felület nem sima.
Mint fentebb kifejtettük, a lelógás egy sima felület, amely a megmunkált anyag felületén kialakuló feszültség következtében jön létre. A nyírási felület egy fényes felület, amelyet a megmunkált anyagba behatoló stancoló hoz létre. A nyírási felületen finom függőleges csíkok láthatók, amelyek a stancolón lévő karcolások, fémlerakódások vagy más anyag miatt keletkeznek. A törésfelület durvább, mint a nyírási felület, úgy néz ki, mintha a megmunkált anyagot letépték volna. A sorja kemény, éles formájú és egyenetlen szélű.
A vágási felület jellemzői a megmunkált anyagtól, a stancoló süllyesztési sebességétől, valamint a stancoló és a szerszám közötti hézag nagyságától függően változnak.
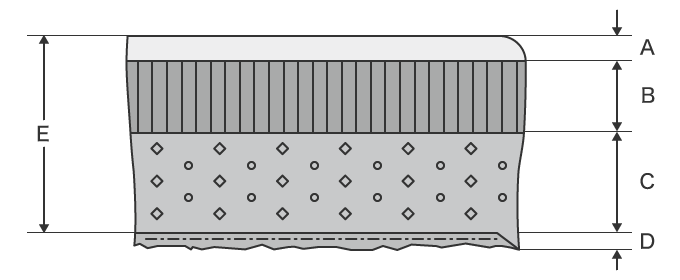
- A
- Lelógás
- B
- Nyírási felület
- C
- Törési felület
- D
- Sorják
- E
- Lapvastagság
Hézag
A hézag a stancoló és a szerszám közötti résre utal. A vágási felület jellemzői a hézag nagyságától függően változnak. Ha a hézag helyesen van beállítva, azt optimális hézagnak nevezzük.
A hézag mérete nagyon fontos, mert befolyásolja a nyírás minőségét (például a méretpontosságot és a lelógás/sorja megelőzését), valamint a szerszám élettartamát. Ha az optimális hézag be van állítva, a stancoló oldalától és a szerszám oldalától kiinduló repedések középen találkoznak. Ideális nyírással teljes nyírási felületet kapunk, lelógás vagy sorja nélkül. Ezt azonban még optimális hézag mellett is nehéz elérni.
A beállított hézag és a vágási felület közötti összefüggés az alábbiakban látható.
Optimális hézag
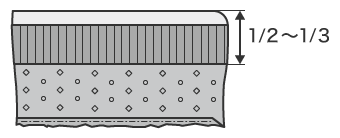
Ha az optimális hézag be van állítva, a nyírási felület egyenletes, és a lemezvastagság 1/2–1/3 részét fedi. Ha a hézag nem állandó, a nyírási felület aránya a különböző részeken eltérő lesz.
Túl nagy hézag
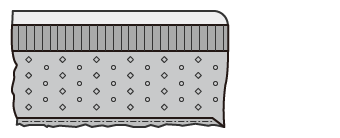
Ha a hézag túl nagy, akkor a lelógás és a sorja nagyobb lesz, és a termék pontossága ingadozóvá válik. A kitolási nyomás okozta vetemedés (kivágási vetemedés) is nagyobb lesz.
Túl kicsi hézag
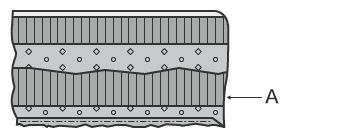
- A
- Másodlagos nyírás
Túl kicsi hézag esetén a stancoló és a szerszám vágóéleiből kiinduló törések nem illeszkednek (találkoznak), és a másodlagos nyírófelület hatására rostos sorja keletkezik. A stancoló és a szerszám terhelése szintén nagy lesz, ami szerszám okozhat, ezt dörzsölődésnek neveznek.
Az optimális hézagérték a megmunkált anyagtól és a lemezvastagságtól függően eltérő. Egy általános használatú érték a következő képlettel számítható ki.
Egyoldali hézag = % x megmunkált lemezvastagság
* [%] a hézag és a lemezvastagság arányát jelzi. Mivel ez az anyagtól vagy a kitolási pontosságtól függően eltérő lehet, ezért a tényleges vizsgálati érték alapján számítható ki.
Nyírási folyamat
A nyírással történő vágás folyamata az alábbi ábrán látható.
(1) A stancoló megnyomja a megmunkált anyag tetejét.
- A lemez meggörbül, és a megmunkált anyagban lelógás alakul ki.
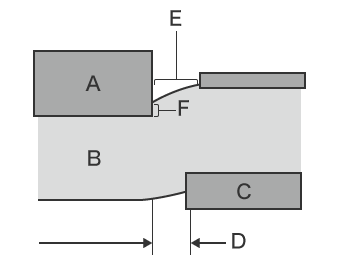
- A
- Stancoló
- B
- Fémlemez
- C
- Szerszám
- D
- Hézag
- E
- Lelógás
- F
- Nyírási felület
(2) Ha az anyagot nem lehet tovább hajlítani, a stancoló belesüllyed az anyagba.
- A stancoló és a szerszám által keltett nyíróerő hatására repedés alakul ki.
- Ha a megmunkált anyag nem képes ellenállni a húzóerőnek, a megmunkált anyag megreped.
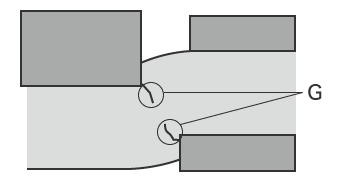
- G
- Repedések
(3) A stancoló és a szerszám sarkai húzóerőt fejtenek ki a megmunkált anyagra.
- Amikor a stancoló és a szerszám pengéjének repedései addig nőnek, amíg át nem érnek, sorja keletkezik.
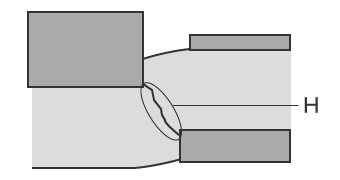
- H
- Átmenő repedés
A nyírás az a folyamat, amely létrehozza a nyírási felület, miközben a megmunkált anyagra a nyíróerő hat.
A lelógás mérésének nehézségei
A legtöbb hagyományos esetben a présesés mérésére optikai komparátort vagy profilmérőt használnak. A lelógás pontos mérése azonban nehéz lehet nagy méretű lemezanyagokban.
Mérési nehézségek - Optikai komparátor
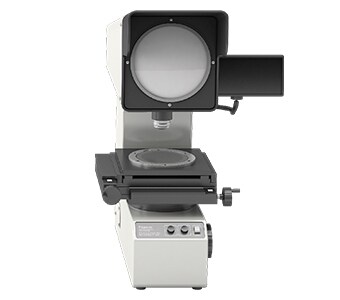
Az optikai komparátor egyfajta optikai mérőműszer, amelynek mérési elve hasonló az optikai mikroszkópéhoz. Ez a mérőműszer a tárgyasztalra helyezett céltárgyat alulról világítja meg, és a célprofilt egy képernyőre vetíti. Egyes nagy optikai komparátorok képernyőátmérője nagyobb, mint 1 m (3,3′). Ha stancolás után nagy felületen mérhetők leesés, az alkatrészt vízszintesen kell elhelyezni.
Ez a mérési módszer a következő problémákat vetheti fel:
- Mivel az optikai komparátor csak a vágási felületre merőleges irányból méri a látható keresztmetszetet, a céltárgyat úgy kell elhelyezni, hogy a lelógás látható legyen, és a méréshez pontosan szintbe kell állítani. A céltárgy elhelyezésének következetlenségei azonban mérési eltéréseket okozhatnak.
- Ha a munkadarab alakja összetett, előfordulhatnak olyan részek, amelyek optikai árnyékban vannak, és merőleges irányból nem mérhetők. Továbbá, a vetített méretek és a rajz közötti eltéréseket nem lehet számszerű formában megállapítani, a profil alakját pedig át kell vinni pauszpapírra, ami megnehezíti az adatok tárolását és összehasonlítását.
Ez számos mérési problémát eredményez, köztük olyan helyeket is, amelyeket nem lehet megmérni, így a céltárgyat el kell vágni.
Mérési nehézségek - Profilmérő
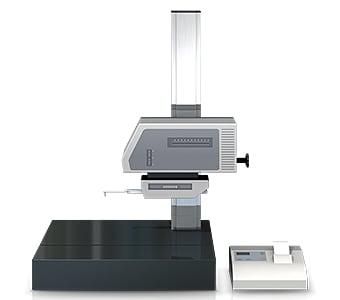
A céltárgy profilját egy profilmérő rendszer méri és rögzíti úgy, hogy a felületét egy érintőceruzával követi végig. Az elmúlt években olyan profilmérő rendszereket fejlesztettek ki, amelyek érintőceruza helyett lézert használnak az összetett alakzatok mérésére a profil érintésmentes követésével. Egyes modellek képesek a felső és az alsó felület mérésére is.
Ha profilmérő rendszert használunk a stancolás utáni lelógás nagy felületen történő mérésére, az alkatrészt szintbe kell helyezni.
Ez a mérési módszer a következő problémákat veti fel:
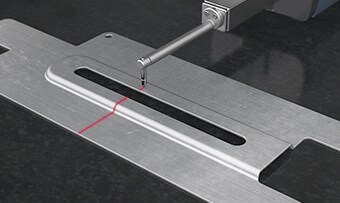
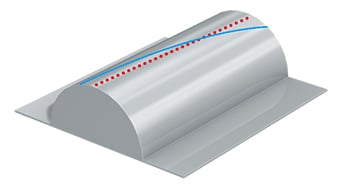
- A céltárgyat mérés előtt rögzíteni kell és szintbe kell állítani.
- A profilmérő-rendszer érintőceruzája felfelé és lefelé egy íven mozog, melynek középpontja az érintőceruza karjának forgástengelye, az érintőceruza hegye pedig az X-tengely irányába mozog. Ez hibát okoz az X-tengely adataiban.
- A kívánt vonal végigkövetése az érintőceruzával rendkívül nehéz munka, és már az érintőceruza enyhe elmozdulása is hibát okoz a mért értékekben.
Megoldások a lelógás mérésére
A szokásosan használt mérőműszerek olyan problémákkal járnak, mint a cél elhelyezéséhez szükséges hosszú idő, valamint az, hogy a háromdimenziós célok és területek mérése pont- vagy vonalérintéssel történik. Ezen mérési problémák megoldására fejlesztette ki a KEYENCE a 3D optikai profilmérő VR sorozatát.
A VR sorozat pontosan rögzíti a teljes célfelület 3D alakját anélkül, hogy érintkezne a tárggyal. A VR sorozat nem igényel különleges rögzítést vagy szubjektív döntéseket, így bármely operátor pontos méréseket végezhet.
1. előny: Nincs szükség rögzítésre.
A VR sorozat a céltárgy beállítása vagy rögzítése nélkül képes a lelógás mérésére.
A VR sorozat a teljes felület érintésmentes mérésével képes a lelógás pontos mérésére. A munkadarab alakzatai rövid idő alatt elemezhetők az elemző sablonok segítségével, amelyek lehetővé teszik a felhasználók számára a mérési tételek előzetes regisztrálását. Ez lehetővé teszi a korábban sok időt igénylő mérések gyors elvégzését.
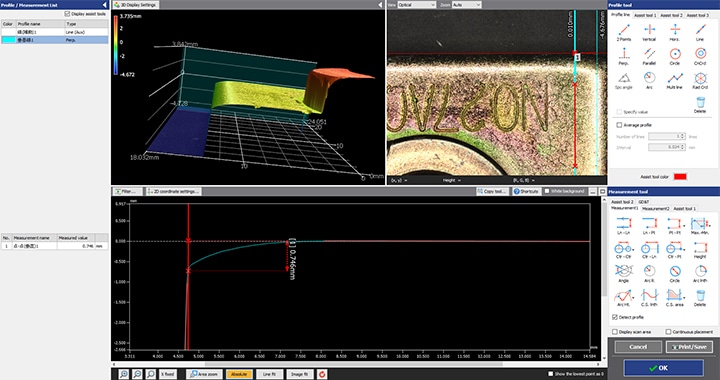
2. előny: Az automatikus pozicionálás funkció kiküszöböli a bonyolult beállításokat.
A VR sorozat automatikusan beállítja a mérési tartományt és a szkennelési beállításokat, így a felhasználónak csak a céltárgyat kell a tárgyasztalra helyeznie. Nincs szükség időigényes beállításokra, így bármely felhasználó másodperceken alatt pontos adatokat rögzíthet.
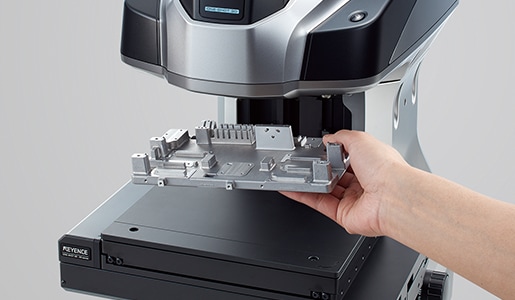
3. előny: Olvassa be a teljes felület alakját akár egy másodperc alatt.
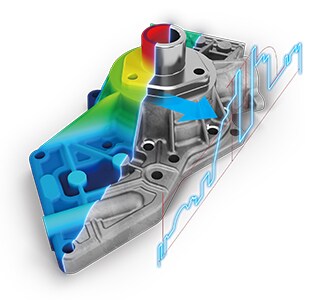
A KEYENCE teljes mértékben felülvizsgálta a mérési algoritmusokat és a hardvert, lehetővé téve a teljes felület beolvasását egy másodperc alatt. A mérés automatikusan elvégezhető a kívánt célpontokon, a felhasználók közötti mérési eltérések nélkül.
Ez a mérési minőség javulásához vezet, lehetővé teszi az ellenőrző operátorok termelési operátorokká történő áthelyezését, és elősegíti a gyártási mennyiség növelését. Ez az összes mérési feladat, például a prototípus-értékelések és a szállítási ellenőrzések sebességét is növeli.
Összegzés: Drasztikus javulás és nagyobb hatékonyság a lelógások mérése során
A VR sorozat pontos és azonnali 3D céltárgy mérést tesz lehetővé, nagysebességű 3D szkenneléssel anélkül, hogy érintkezne a céltárggyal. Megoldja a hagyományos mérőműszerekkel kapcsolatos összes problémát, beleértve a lelógás, a nyírási felület, a törésfelület és a sorja közötti határok mérését.
- Nincs vágás vagy roncsolásos vizsgálat.
- Nincs mérési eltérés a különböző operátorok között.
- A mérés egyszerűen elvégezhető a céltárgy tárgyasztalra helyezésével és egyetlen gomb megnyomásával, pozicionálás vagy egyéb előkészítés nélkül. Így nincs szükség speciális operátor kijelölésére a mérési munkákhoz.
- A 3D alakzatok könnyen, nagy sebességgel, nagy pontossággal mérhetők. Ez lehetővé teszi nagyszámú céltárgy rövid idő alatt történő mérését, elősegítve a minőség javítását.
Ez a rendszer lehetővé teszi a korábbi 3D alakzatadatokkal és CAD-adatokkal való összehasonlítást, valamint az egyszerű adatelemzést, például a tűréshatárokon belüli eloszlást. Hatékonyan használható számos célra, beleértve a termékfejlesztést, a gyártási trendelemzést és a mintavételi ellenőrzéseket.