Présformázott termékek párhuzamosságának mérése
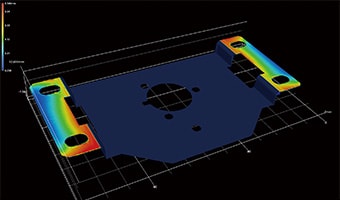
A préselés a műanyag-megmunkálás egyik fajtája; egyes műanyag préselési esetekben előfordulhat, hogy az alakzat nem olyan lesz, amilyennek tervezték. Ez általában akkor következik be, amikor a préselés után az anyag belsejében feszültség marad olyan tényezők miatt, mint például a visszarugózás. Óvatosan kell eljárni, amikor a lemezanyagot hajlítással forgattyús-vagy U-alakúvá alakítják, mert előfordulhat, hogy a sarokrészek nem az előírt szögeket alkotják, és a párhuzamosság eltérhet a megadott tűrésektől. Az autóvázgyártásban az acéllemezek szakítószilárdságára vonatkozó szabvány az elmúlt években szigorúbb lett, és ez megnehezíti a nagy pontosságú préselést.
Ez a szakasz a préselés során felmerülő, párhuzamossággal kapcsolatos problémákat magyarázza el, a párhuzamosság mérésével kapcsolatos ismeretekkel, a párhuzamosságmérés problémáival, valamint ezen problémák megoldásaival együtt.
- A párhuzamossági hiba oka: Visszarugózás
- A hagyományos párhuzamosságmérés során felmerülő problémák
- Megoldás a párhuzamosságmérés során felmerülő problémákra
- Összegzés: Átfogó fejlesztés és nagyobb hatékonyság a présformázott termékek párhuzamos mérésének problémái esetében
A párhuzamossági hiba oka: Visszarugózás
A préselésnél kiemelten fontos a présgép támasztékának és csúszófelületének párhuzamossága, valamint a megmunkált termék párhuzamossága. Ha a támaszték és a csúszófelületének párhuzamossága nem megfelelő, akkor az abban az esetben is érinteni fogja a hajlítási szöget és a mélyhúzó nyersanyagtartóját, ha a csúszka függőlegesen mozog. Ez csökkenti a szerszám élettartamát. A megformázott termékek préselés utáni párhuzamossági hibái elsősorban a megformázott termék belsejében lévő maradék feszültség (belső feszültség) miatt fordulnak elő. Ezt az alakváltozást visszarugózásnak nevezik, és ez az oka annak, hogy a préselés során nehéz a kívánt méretpontosság megtartása.
A visszarugózás típusai
A visszarugózás okai a prés alsó holtponti helyzetében, a megformázott termék belsejében fellépő belső feszültségek vizsgálatával azonosíthatók be. Hajlítás közben az alsó holtponton a húzófeszültség a hajlítás külső oldalán, a nyomófeszültség pedig a hajlítás belső oldalán lép fel. A szerszámleválás akkor következik be, amikor a lemezvastagság irányában feszültségkülönbségek vannak, ami végső soron megváltoztatja a szöget. A visszarugózás jellegzetes típusai közé tartozik a szögváltás vagy a függőleges fal vetemedése a szerszám vállának lekerekített részén, a csavarodás és a gerincvonal meghajlása. Az alábbiakban ismertetjük a visszarugózást okozó feszültséget, és példákat adunk a visszarugózási hibákra.
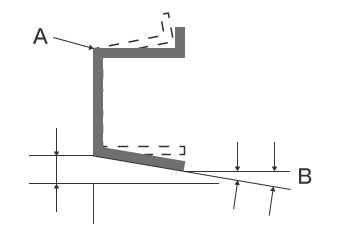
- A
- Hajlítás gerincvonala
- B
- Szögváltás
- Szögváltás:
- Ez egy olyan hiba, amely során a hajlítási szög a lemezvastagság irányában jelentkező feszültségkülönbségek miatt megváltozik.
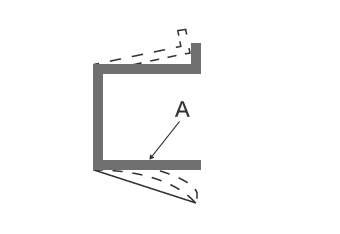
- A
- Falvetemedés
- Falvetemedés:
- Ez egy olyan hiba, amely esetében a fal meggörbül a hosszirányú feszültségkülönbségek miatt.
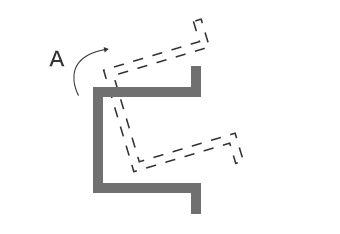
- A
- Csavarodás
- Csavarodás:
- Ez egy olyan hiba, amely során a lemezvastagság irányában jelentkező feszültségkülönbségek és a felület belseje felé ható feszültség hatására a teljes termék megcsavarodik.
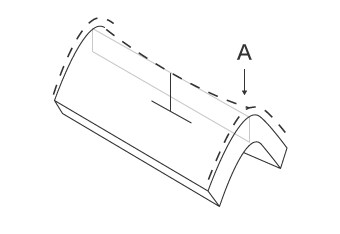
- A
- A gerincvonal vetemedése
- A gerincvonal vetemedése:
- Ez egy olyan hiba, amely esetében a hajlítás gerincvonala meghajlik a lemezvastagság irányában jelentkező feszültségkülönbségek miatt.
Ellenintézkedések a párhuzamosság visszarugózásának javítására
A visszarugózással kapcsolatos ellenintézkedések között általában megtalálható a szerszám kialakításának vagy alakjának megváltoztatása a visszarugózással ellentétes irányban. A présszerszámban történő visszarugózás mértékének és irányának beállításával elérhető a mérettűrés.
Korábban a visszarugózással kapcsolatos ellenintézkedések nagymértékben függtek a tervező intuíciójától és tapasztalatától, és a szerszám módosítására a tesztelés után került sor. Mivel azonban a visszarugózás hajlamos az acéllemez szakítószilárdságával arányosan növekedni, nagyszámú szerszámmódosítás válhat szükségessé olyan esetekben, amikor a visszarugózás nagy mértékű. A probléma megoldására a közelmúltban a FEM-et (végeselem-módszert) használó szimulációkat kezdtek alkalmazni a szerszámtervezésben.
Vannak más ellenintézkedések is, mint például a „kétlépcsős hajlítás”, amely kétszer hajtja végre a hajlítást a gép egyetlen mozdulatával. Ezen túlmenően, a „kiütés” a stancoló vágóélének mindkét sarkánál kiemelkedéseket hoz létre, a „horonymegmunkálás” pedig előre V-alakú bemélyedést (V-bevágást) hoz létre a megmunkált anyag azon részén, amely meghajlik.
Ezeket az ellenintézkedéseket olyan esetekben lehet alkalmazni, amikor a visszarugózás oka ismert. Mivel a tényleges présformázott termékek alakzatai bonyolultak, igen nehéz lehet beazonosítani a visszarugózás okát. Emiatt hatékonyabb módszerre van szükség a visszarugózás kiszámítására.
A visszarugózás mértékének kiszámítása
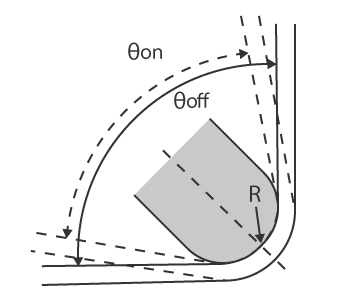
Ha csak hozzávetőlegesen is számítható ki a visszarugózás mértéke, a megmunkálás előtt akkor is lehetséges lesz ellenintézkedések végrehajtása. A visszarugózás mértékének előrejelzésére szolgáló számítási képlet azonban bonyolult, és általában a szerszámtervezéskor használják. Referenciaként a képlet lentebb látható.

- Δθ
- Szögváltozás a visszarugózás eredményeként
- θon
- Hajlítási szög (°) a nyomás alkalmazásakor
- θoff
- Hajlítási szög (°) a visszarugózás után
- σB
- Acéllemez-szilárdság (N/mm2)
- R
- Stancoló görbületi sugár (mm)
- E
- Acéllemez Young-modulus (= 206 000 N/mm2)
- t
- Acéllemez -vastagság (mm)
* A σB (acéllemez szilárdság) és E (acéllemez Young-modulus) az anyag jellemző értéke.
A hajlítás vágóéle a becsült visszarugózás alapján jön létre. Nehéz tovább kiszámítani a visszarugózásból eredő hibát. Más szóval, könnyebb beállítani a belső sugarat, mint kiszámítani a visszarugózás mértékét. Ezenkívül nagy a hiba a számított érték és a tényleges érték között olyan tényezők hatásai miatt, mint például a lemezvastagság változása és a gép specifikációinak különbségei. Ezért a formázás után a mérettűrést méréssel kell ellenőrizni.
A hagyományos párhuzamosságmérés során felmerülő problémák
A párhuzamosság egy olyan érték, amely azt jelzi, hogy egy megformált termék egyes síkjai vagy vonalai mennyire párhuzamosak a referenciaként szolgáló tökéletes virtuális síkkal vagy egyenessel. Mérése virtuális sík vagy vonal beállításával történik, és nem mérhető kézi eszközzel, például tolómérővel vagy mikrométerrel. Emiatt a préselt termék párhuzamosságát koordináta mérőgéppel vagy CNC képmérő műszerrel mérik. Az ezekkel a műszerekkel végzett párhuzamosságmérés azonban precíz és haladó műszaki készségeket és tapasztalatot igényel, és a következő mérési problémákat veti fel.
A koordináta mérőgéppel történő párhuzamosságmérés során felmerülő problémák
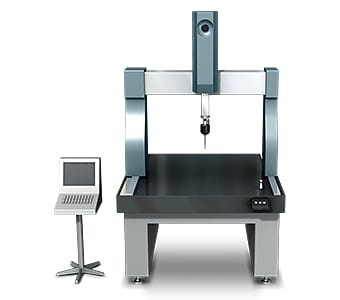
A vetemedés koordináta mérőgéppel történő mérésekor általában az szükséges, hogy a szonda a céltárgy mért felületének négy vagy több sarkával érintkezzen.
Például egy lemez mérésekor általában hat-nyolc pontot mérnek. Ha a mérési terület nagy, a mérési pontosság a mért pontok számának növelésével javítható, hogy több mérési adatot gyűjtsön.
Azonban a következő problémák lépnek fel, ha a párhuzamosság mérésére koordináta mérőgépet használnak.
- Mivel az egyes pontok érintésével kell mérni, alapvetően nehéz a teljes alakzat azonosítása.
- Mivel több pont mérése a több mérési adat megszerzéséhez sok időt vesz igénybe, nem lehet azonosítani a teljes céltárgy részletes alakját.
A CNC képmérő műszerrel történő párhuzamosságmérés során felmerülő problémák
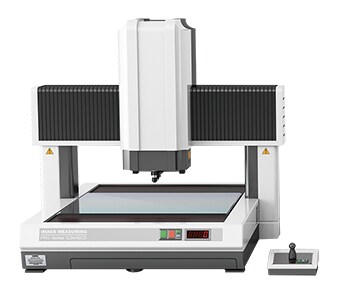
Általában egy képmérő műszer rögzíti a célpontot a tárgyasztalon CCD kamerával, és 3D mérést végez. Lehetséges a színes képekkel történő megfigyelés, de a párhuzamosság mérésénél a következő problémák merülnek fel.
- Hamis észlelés történhet, ha a céltárgyon kiemelkedések vannak. Ezen túlmenően, ha a mérési pontok vagy más beállítások eltérőek, a mérési pontosság is változhat.
- Ha az X, Y, Z vagy más mérőelemek száma nő, a program bonyolulttá válik, amely fejlett szakértői tudást és munkaórákat igényel a konfiguráláshoz. A szükséges mérési munkaórák a mérendő céltárgyak számával arányosan nőnek. Komoly problémák merülnek fel, többek között a mérőkamra és annak referencia-hőmérsékleten tartásának szükségessége, valamint az a tény, hogy a pontos mérést nem minden munkahelyi operátor tudja elvégezni.
Megoldás a párhuzamosságmérés során felmerülő problémákra
Az általában használt koordináta mérőgépeknek sok időre van szüksége a mérés elvégzéséhez, mivel háromdimenziós célpontokat és mérési helyeket mérnek több pont érintéses mérésével. Ezen túlmenően, az ilyen típusú eszközök esetében olyan problémák is megfigyelhetők, hogy az emberi tényezők okozta eltérések miatt alacsony a mérési érték megbízhatósága, valamint a számokból, elemzési függvényekből és más utófeldolgozási technikákból nehezen hozható létre használható adatok.
E mérési problémák megoldására a KEYENCE kifejlesztette a 3D optikai profilmérő VR sorozatát és a 3D CMM szkenner VL-sorozatát.
Ezek a termékek pontosan rögzítik a teljes célfelület 3D alakját anélkül, hogy érintkeznének a céltárggyal. Ezek a 3D alakzatot is mérik úgy, hogy a céltárgyat mindössze egy másodperc alatt, nagy pontossággal 3D-ben beolvassák a tárgyasztalon. Ez a szakasz ezeknek a rendszereknek néhány speciális előnyét mutatja be.
A VR-sorozat 1. előnye: Egyetlen beolvasással akár 800 000 pont is mérhető, így nincs szükség a mérés megismétlésére.
A VR-6000 akár 800 000 adatpontot is képes rögzíteni egy teljes felületen (30 × 15 cm) mindössze egy másodperc alatt. Mivel a mérés nem vonalak vagy pontok használatával történik, nincs szükség ismételt mérésre, ami csökkenti a mérésre fordított teljes időt. Az olyan mérések is egyszerűen elvégezhetőek, amelyek nullapontot igényelnek, mint például a párhuzamosság vagy a merőlegesség. A mérési adatok automatikusan tárolásra kerülnek, és a tárolt adatok összehasonlíthatók más adatokkal vagy 3D tervezési adatokkal.
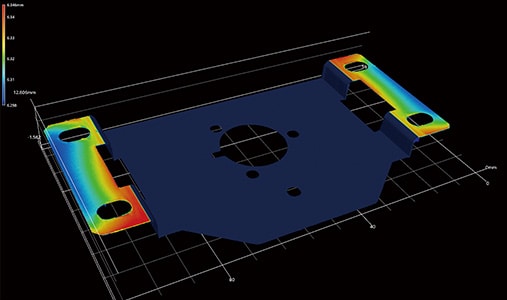
A koordináta mérőgépekkel vagy CNC képmérő műszerekkel ellentétben a VR-sorozat kivonja a tárgyasztalra helyezett céltárgy tulajdonságait, és automatikusan helyzetkorrekciót hajt végre. A korábban sok időt és erőfeszítést igénylő szigorú pozicionálás már nem szükséges. Ez bármilyen típusú operátor számára lehetővé teszi, hogy tapasztalati szinttől függetlenül könnyen és azonnal végezzen méréseket.
A VR-sorozattal az összetett formájú céltárgyak párhuzamossága is pontosan mérhető mindössze a céltárgy tárgyasztalra helyezésével és egy gomb megnyomásával.
VR-sorozat 2. előnye: Lehetséges több mérési adathalmaz mennyiségi összehasonlítása és elemzése.
A VR sorozat akár egy másodperc alatt is képes megmérni a teljes céltárgy 3D alakját a célfelület 3D szkennelésével. Ez lehetővé teszi nagyszámú céltárgy mérését minta-előkészítés nélkül. A mérési helyeket vagy a mérési pontok számát nem kell beállítani, mivel a rendszer automatikusan beállítja a mérési feltételeket.
Több mérési adathalmaz is megjeleníthető egy listában, és ugyanaz az elemzési az összes adatsoron egyszerre végezhető el.
A több céltárgy alakzatadatai közötti különbségek egy szempillantás alatt megerősíthetők. Ez lehetővé teszi a párhuzamosság kötegelt elemzését több adathalmazban, és egyszerűen kvantitatív értékelés készíthető arról, hogy egy nem-megfelelő alkatrész mennyire torzult el egy megfelelő alkatrészhez képest.
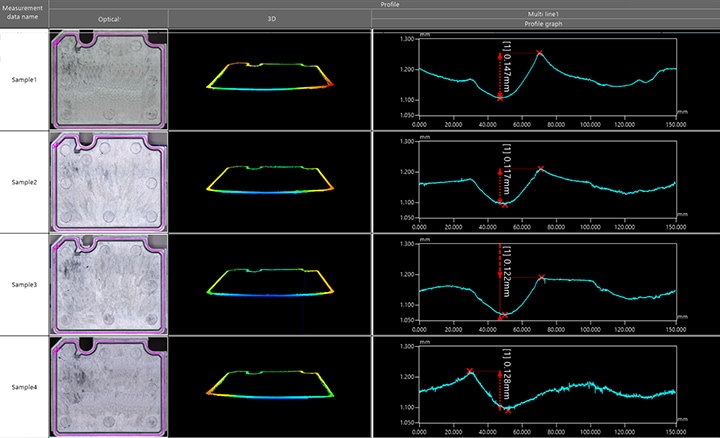
A segédeszközök széles választéka lehetővé teszi a kívánt mérési tartalom egyszerű beállítását.
Az egyszerű konfiguráláson túl a segédeszközök lehetővé teszik, hogy még a kezdő felhasználók is gyors és pontos alakméréseket végezzenek. Ennek eredményeként a minták száma egyszerűen növelhető nem csupán a prototípusok és tesztek, hanem a termékek mérése és ellenőrzése céljából is.
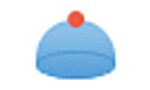
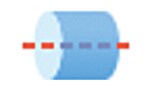
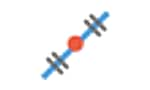
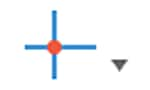
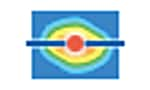
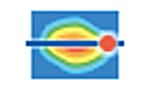
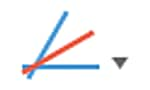
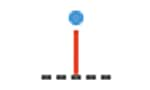
Összegzés: Átfogó fejlesztés és nagyobb hatékonyság a présformázott termékek párhuzamos mérésének problémái esetében
A VR sorozat anélkül tud 3D célalakzatokat pontosan és azonnal mérni nagy sebességű 3D szkenneléssel, hogy hozzáérne a céltárgyhoz. A párhuzamosság mérése azonnal elvégezhető kis, nagy és összetett alakzatú alkatrészek esetében. Ezek a termékek képesek megoldani a hagyományos mérőműszerekkel kapcsolatos összes problémát.
- Mivel a teljes felület adatai rögzíthetők érintésmentes eszközökkel, lehetőség van olyan keresztmetszetek mérésére, amelyeket érintőceruzával nem lehet elérni. A párhuzamosság kis alkatrészeknél is könnyen és pontosan mérhető.
- A segédeszközök széles választéka megoldást ad az emberi tényezők okozta mérési értékek eltérésének problémájára. Ez lehetővé teszi valódi mennyiségi mérések elvégzését.
- A mérés egyszerűen elvégezhető a céltárgy tárgyasztalra helyezésével és egyetlen gomb megnyomásával, pozicionálás vagy egyéb előkészítés nélkül. Így nincs szükség speciális operátor kijelölésére a mérési munkákhoz.
- A 3D alakzatok könnyen, nagy sebességgel, nagy pontossággal mérhetők. Ez lehetővé teszi nagyszámú céltárgy rövid idő alatt történő mérését, elősegítve a minőség javítását.
Ez a rendszer lehetővé teszi a korábbi 3D alakzatadatokkal és CAD-adatokkal való összehasonlítást, valamint az egyszerű adatelemzést, például a tűréshatárokon belüli eloszlást. Hatékonyan használható számos célra, beleértve a termékfejlesztést, a gyártási trendelemzést és a mintavételi ellenőrzéseket.
- A 3D optikai profilmérő VR sorozata a nagyobb felbontású és nagyobb pontosságú mérésekhez
-