Fémtörési felületek törési mintázatai és megoldások a metallurgiai hibaelemzéssel kapcsolatos problémákra
A különböző termékekben használt fémek a használat vagy a környezeti hatások következtében idővel törvényszerűen el fognak törni. A törések okának azonosításához először meg kell vizsgálni a fémeket, és pontos elemzésnek kell alávetni a törött felületeket (fraktográfia).
A gépjárműiparban, a repülőgépiparban és minden más iparágban, ahol a biztonság kiemelt fontosságú, a termékek minőségének javításakor az anyagminőség a legalapvetőbb tényező.
Ebben a részben a metallurgiai hibaelemzéshez használatos módszereket, valamint a törési mintázatok és törött felületek jellemzőit ismertetjük. Emellett konkrét példákat is bemutatunk arra, hogy a 4K-s digitális mikroszkópok hogyan használhatók a metallurgiai hibaelemzéssel kapcsolatos problémák megoldására.
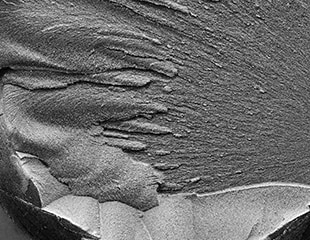
- A törés okának meghatározása a fém törési felülete alapján
- A fraktográfia típusai
- Fémek törési mintázatai
- A metallurgiai hibaelemzéssel kapcsolatos problémák és azok megoldásai
- Fejlettebb és hatékonyabb metallurgiai hibaelemzés
A törés okának meghatározása a fém törési felülete alapján
Különböző fémeket, például acélt, rezet és alumíniumötvözetet számos különféle termékben használnak a háztartási készülékektől és játékoktól kezdve egészen az ipari létesítményekig és berendezésekig.
Mostanában aktívan tanulmányoznak néhány új, nagy teljesítményű anyagot, különösen a gépjármű- és a repülőgépipar területén. Ezek a vizsgálatok az anyagok méretének és súlyának csökkentésére és a merevség javítására vonatkozó követelmények miatt, valamint energiamegtakarítási és költségcsökkentési célokból (a gyártási és feldolgozási költségeket is beleértve) váltak szükségessé. A gépjárművek, repülőgépek, hajók, vasúti kocsik és űrhajók terén a fémek törése emberéleteket veszélyeztethet, ezért ezeken a területeken nagy figyelmet kell szentelni a megfelelő anyagok kiválasztására és a szilárdsági számításokon alapuló biztonsági tervezésre.
A fémek kiválasztásakor számos anyagvizsgálatot kell végezni az ilyen anyagok ellenálló képessége tekintetében.
A leggyakoribb tesztelési módszerek a következők.
- Mechanikus tesztek:
- Szakítóvizsgálat, hajlítási vizsgálat, nyomóvizsgálat, nyírási vizsgálat, kúszásvizsgálat, kopásvizsgálat stb.
- Keménységi tesztek:
- Bemélyedési keménységvizsgálat, dinamikus keménységvizsgálat
- Kémiai tesztek:
- Korrózióvizsgálat
Az anyagok értékeléséhez, kiválasztásához vagy javításához ezeken az anyagvizsgálatokon vagy a kész termékként leszállított és a használat nyomán megtört fémanyag felületén végzett szerkezeti elemzésen (fraktográfia) keresztül meg kell vizsgálni a törés okát és az anyagok alapvető tulajdonságait.
A fraktográfia típusai
A fraktográfia szerkezeti vizsgálaton keresztül elemzi a fémek törésének módját (a törési felület mintázatát vagy a törés alakját) annak érdekében, hogy különböző tényezőket, például az anyagokat, a gyártási módszereket, az alakzatokat és a használati feltételeket figyelembe véve megállapítsa a törések elsődleges okait. A törött felületek szerkezeti megfigyelésére szolgáló módszerek közül a fémek terén az alábbiak a leggyakoribb fraktográfiás módszerek.
Makroszkopikus megfigyelés
A makroszkopikus megfigyelés egy elemzési módszer, amely többek között szabad szemmel, kis nagyítású nagyítóval és sztereoszkopikus mikroszkópok használatával történhet. Ez a megfigyelési módszer egyszerűen, a törés helyén is elvégezhető, és a célja, hogy töréstípus, a kagylószerű mintázat jelenléte stb. alapján nagyjából elkülönítse a lehetséges okokat. Azonban a makroszkopikus megfigyelés önmagában nem elegendő a törés okainak részletes vizsgálatához.
Mikroszkopikus megfigyelés
A mikroszkopikus megfigyelés a mikroszkopikus jellemzőket vizsgálja a törésfelszín szerkezetének optikai mikroszkópokkal és pásztázó elektronmikroszkópokkal történő megfigyelésével. Ez a megfigyelési módszer a törésfelszín különböző jellemzőinek (pl. domborulatok és csíkos mintázatok) elemzése révén a törési alakzatok részletes vizsgálatát teszi lehetővé.

Fémek törési mintázatai
A törési mintázatokat (törési alakzatokat) a következő kategóriákba sorolhatjuk: képlékenységi (plaszticitási) törés, ridegtörés, kifáradási törés és környezeti okokból eredő törés. Valamennyi mintázat esetén a törésfelszín makroszkopikus és mikroszkopikus megfigyelésén keresztül határozható meg a törés oka. Az alábbiakban összefoglaltuk az egyes törési mintázatok és azok törésfelszíneinek jellemzőit.
Képlékenységi (plaszticitási) törés
A képlékenységi (plaszticitási) törési mintázatot, amely bármilyen fémnél jelentkezhet, jelentős mértékű deformálódás, például megnyúlás és a törés helyén jelentkező elvékonyodás jellemzi. A szerkezeti megfigyelés során ennél a típusú törésnél az alábbi jellemzők és részletes törésminták láthatók.
- A törésfelszín jellemzői
-
- Makroszkopikus megfigyelés:
- Nyírási perem (nyírási törés, a törés végpontja), tompa szürkésfehér
- Mikroszkopikus megfigyelés:
- Izometrikus bemélyedések (húzó terheléstől bekövetkező törés), elnyújtott bemélyedés (nyírási törés), hajlított vonalas mintázat (csúszósíkos törés)
Ridegtörés:
A ridegtörés olyan törési mintázat, amelyben a repedés csak kevés plasztikus deformációt mutat, ugyanakkor gyorsan terjed. A repedés növekedésével nem jön létre plasztikus deformáció a törésfelszín körül. Ridegtörés általában normál használat mellett fordul elő sok acélanyag esetén. A törésfelszín sok esetben kvázi-hasadásos törésfelszínekből áll, amelyek rendkívül hideg környezetekben, nagy méretű, hőkezelt acélelemeken és általános szerkezeti acélon figyelhetők meg.
- A törésfelszín jellemzői
-
- Makroszkopikus megfigyelés:
- Ezüstös-fehér, fényes reflexió, halszálkaminta (gyors transzgranuláris törés), sugarakban terjedő repedések
- Mikroszkopikus megfigyelés:
- Kvázi-hasadásos törésfelszín, folyómintázat, granuláris törés, összetett törés
Kifáradási törés
A kifáradási olyan törési mintázat, amelyben a repedés ismételt terhelés hatására fokozatosan alakul ki. Úgy tartják, hogy a mechanikai szerkezeteken előforduló törésmintázatok több mint 70%-a ebbe a kategóriába esik.
A törött anyag felületén nem látható megnyúlás vagy elvékonyodás, ami hasonló a ridegtöréshez, azonban mikroszkopikus megfigyeléssel jelentős plasztikus deformáció figyelhető meg.
A törésfelület általában a többi törési mintázattal összehasonlítva sokkal simább, és mikroszkopikus vizsgálattal kagylószerű (konchoidális) mintázat figyelhető meg. Az ilyen kagylószerű mintázatból megállapítható, hogy hol kezdődött a törés, és milyen irányba folytatódott a repedés.
Erre a törésre jellemző még, hogy mikroszkopikus megfigyeléssel barázdáltságnak nevezett csíkozódás is látható. A csíkozódás merőleges a repedés irányára, és jellemzően alumínium- és rézötvözetek esetén fordul elő gyakran, míg vasötvözetek esetén nem alakul ki könnyen ilyen típusú törés.
- A törésfelszín jellemzői
-
- Makroszkopikus megfigyelés:
- Kagylószerű (konchoidális) mintázat, racsnis mintázat (több feszültségcsúcspont), halszem (a törés kezdőpontja), sugarasan terjedő repedések
- Mikroszkopikus megfigyelés:
- Barázdáltság (a terhelési ciklusnak megfelelően), barázdaszerű mintázat (nem a terhelési ciklusnak megfelelően), másodlagos repedések, súrlódási nyomok vagy semmilyen jellegzetes mintázatot nem viselő törések
Környezeti okokból eredő törés
Környezeti hatások nyomán kialakuló törésről akkor beszélünk, amikor a repedés korrozív környezet hatására alakul ki. Éppen ezért az a típusú törés még rendkívül kis mértékű belső feszültség esetén is előfordulhat.
A környezeti okokból törések leggyakoribb típusai a hidrogénnel való érintkezés hatására kialakuló töredezés és a feszültségkorróziós repedés.
- Hidrogénnel való érintkezés hatására kialakuló töredezés
- A hidrogénnel való érintkezés hatására kialakuló töredezést késleltetett törésnek is nevezzük, és leggyakrabban acél esetén figyelhető meg. A jelenséget (töredezést) az anyagba kerülő hidrogén okozza. A hidrogén jellemzően valamilyen gyártási folyamat, például hegesztés és galvanizálás során, valamint a használati környezetben végbemenő korróziós reakciók hatására kerül az anyagba.
- Feszültségkorróziós repedés
- Ez a fajta repedés gyakran fordul elő olyan baleseteknél, ahol ausztenites rozsdamentes acél a használt anyag. C1-ionokat tartalmazó használati környezetekben különösen gyakran fordulnak elő transzgranuláris törések. A rozsdamentes acéltól eltérő anyagok, például tiszta réz, sárgaréz és alumíniumötvözetek esetén ugyanakkor szemcsehatár-törések jellemzők.
- A törésfelszín jellemzői
-
- Hidrogénnel való érintkezés hatására kialakuló töredezés
-
- Makroszkopikus elemzés
- Ezüstös-fehér, fényes reflexió
- Mikroszkopikus elemzés
- Granuláris törés, hajszálvonalak
- Feszültségkorróziós repedés
-
- Makroszkopikus elemzés
- Részleges reflexió, rozsdásodás/elszíneződés
- Mikroszkopikus elemzés
- Granuláris törés, tollpiheszerű mintázat
- Magas hőmérsékleten bekövetkező törés
-
- Makroszkopikus elemzés
- —
- Mikroszkopikus elemzés
- Granuláris törés, bemélyedések, behúzódás
A metallurgiai hibaelemzéssel kapcsolatos problémák és azok megoldásai
Ahogy azt a fentiekben említettük, a törésfelszínek makroszkopikus és mikroszkopikus megfigyeléssel történő vizsgálatával részletesebben elemezheti a törési mintázatokat, és hatékonyabban azonosíthatja a törések okait és feltételeit.
A modern optikai technológiára, képérzékelőre (CMOS) és képfeldolgozási technológiára épülő 4K-s digitális mikroszkópunk segítségével számos különböző törési mintázatot vizsgálhat nagy felbontásban a megbízhatóbb fraktográfiás elemzések érdekében.
Ebben a részben arra mutatunk be példákat, hogy hogyan használható a KEYENCE VHX sorozatú ultranagy felbontású 4K-s digitális mikroszkópja metallurgiai hibaelemzéshez.
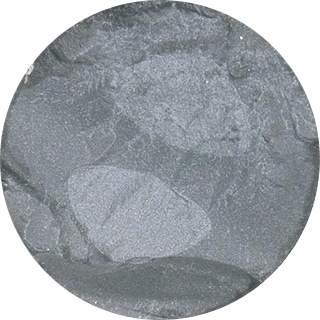
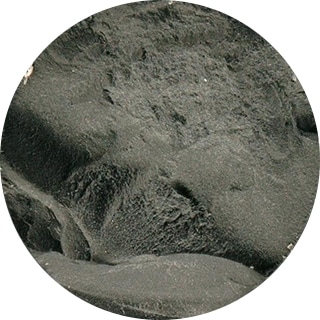
Fémtörési felület becsillanásának megszüntetése
A VHX sorozatú 4K-s digitális mikroszkóppal
A csillanás-eltávolítás funkció elnyomja a zavaró becsillanásokat, így a törési felületek legapróbb repedéseit is kristálytiszta képen vizsgálhatja.
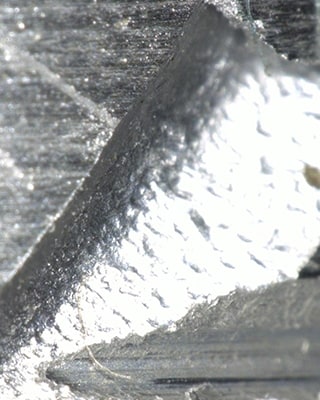
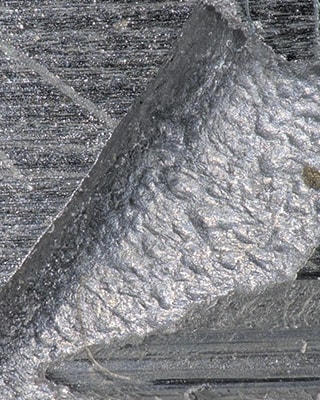
Teljesen éles kép a teljes célterületen még egyenetlen törési felületek esetén is
A VHX sorozatú 4K-s digitális mikroszkóppal
Az élő mélységélesség-kiterjesztés funkció segítségével a törési felület teljes területe élesen jeleníthető meg. Ez a funkció amellett, hogy csökkenti a fókusz ismételt beállításához szükséges időt, egyszerűbbé teszi a törési felületen lévő különböző, összetett törési jellemzők megfigyelését és értékelését.
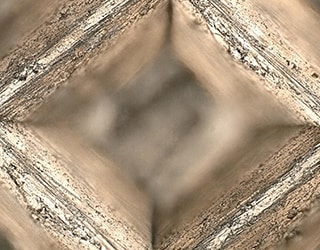
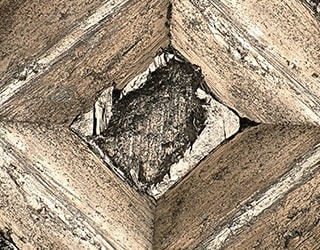
A részletek elemzése a szögtől és az árnyékoktól függetlenül
A VHX sorozatú 4K-s digitális mikroszkóppal
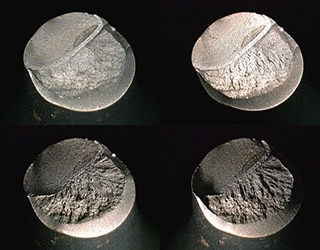
A többszörös megvilágítás funkció használatával a több irányból érkező megvilágítási adatok automatikusan, egyetlen gombnyomással rögzíthetők, így szabadon kiválaszthatja a szerkezeti megfigyeléshez legalkalmasabb képet.
A különböző világítási feltételekkel készült képeket a készülék a számítógépre menti, így azok még a rögzített képek kiválasztása vagy exportálása után is elérhetők maradnak. Így bármikor egyszerűen, az egér használatával betöltheti a más megvilágítási feltételekkel rögzített képeket.
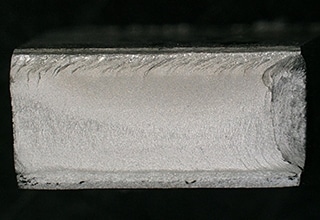
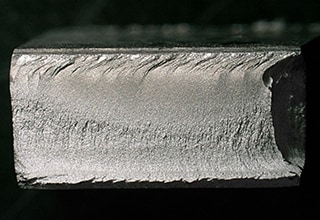
Kristálytiszta megfigyelés még finom mintázatok és apró alakzatok esetén is
A VHX sorozatú 4K-s digitális mikroszkóppal
Az optikai árnyékhatás üzemmód egy új megfigyelési módszer, amely egy speciális kialakítású, nagy felbontású objektív, egy 4K-S CMOS-képérzékelő és világítás kombinálásával elemezni a változó megvilágítás mellett rögzített képek kontrasztját.
Ezzel a módszerrel a fémek törési felületén lévő finom és apró szabálytalanságok is pontosan megfigyelhetők. Az optikai árnyékhatás üzemmód képét színadatokkal létrehozva a szabálytalanságokkal kapcsolatos információk különböző színekkel jeleníthetők meg.
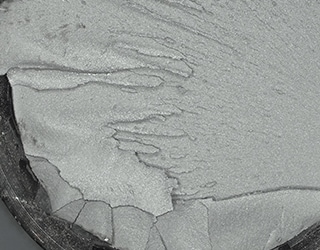
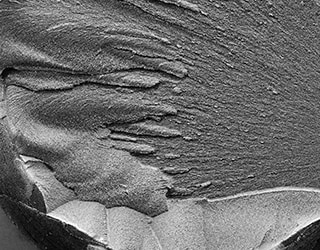
Fejlettebb és hatékonyabb metallurgiai hibaelemzés
Ahogy azt a fentiekben elmagyaráztuk, a VHX sorozatú 4K-s digitális mikroszkóp segítségével egyszerűen vizsgálhatók a fémek törési felületei.
Mivel a VHX sorozattal gyorsabban végezhet metallurgiai hibaelemzést, a minőségjavítási ciklust és a kutatási-fejlesztési folyamatokat is felgyorsíthatja. Emellett a VHX sorozat lehetővé teszi a törési felületek jellemzőit tartalmazó képadatok megőrzését, így a korábbi trendek és összehasonlítások alapján egyszerűbben választhatja ki és javíthatja a használt anyagokat.
A számos egyéb fejlett funkcióval ellátott VHX sorozat megbízható társ a hatékony fraktográfiás elemzésekhez és szerkezeti megfigyelésekhez, amelyekre feltétlenül szükség van ahhoz, hogy vezető szerepet tölthessen be a kutatás és fejlesztés területén. A részletekért kattintson az alábbi gombra, és töltse le a katalógust. Kérdés esetén kattintson az alább látható másik gombra, és vegye fel a kapcsolatot a KEYENCE-szel.