Przyczyny powstawania wad tłoczenia (zadziory, obtłuczenia) oraz obserwacja wad i przekrojów (powierzchnie pękania)
Wytłaczanie jest szeroko stosowaną metodą wytwarzania różnych produktów. Zwłaszcza wraz z postępem elektronicznego sterowania samochodami w ostatnich latach pojawiają się wymagania dotyczące jeszcze większej dokładności, trwałości i niezawodności nie tylko ram pojazdów i części przesuwnych, ale także części elektrycznych, które są miniaturyzowane i montowane z większą gęstością, oraz części metalowych do sprzętu elektronicznego.
W tej części przedstawione są typowe wady tłoczenia, ich przyczyny i środki zaradcze. W tej części przedstawiono przykłady zastosowań naszego mikroskopu cyfrowego 4K, który jeszcze bardziej zwiększa stopień zaawansowania obserwacji wad przekrojów, np. powierzchni pękania. Przykłady te są ważne w testowaniu, projektowaniu i tworzeniu prototypów w badaniach i rozwoju oraz w kontrolach przeprowadzanych w ramach zapewniania jakości.
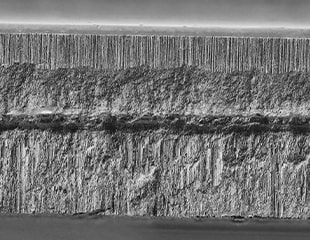
- Przyczyny i środki zaradcze w przypadku wad tłoczenia
- Przykłady obserwacji przekrojów poprzecznych i defektów na tłoczonych wyrobach
- Mikroskop 4K, który optymalizuje badania i rozwój, projektowanie i zapewnianie jakości produktów wytłaczanych
Przyczyny i środki zaradcze w przypadku wad tłoczenia
Rodzaje wytłaczania
W procesie tłoczenia materiał jest kształtowany w pożądany sposób poprzez zastosowanie ciśnienia różnymi metodami, zazwyczaj za pomocą formy zwanej matrycą i stempla. Typowe metody wytłaczania są następujące.
- Ścinanie: materiał jest przetwarzany (cięty) metodą przyłożenia siły przekraczającej jego granicę pęknięcia.
- Zginanie: materiał jest zginany przez przyłożenie siły rozciągającej z jednej strony i ściskającej z drugiej strony.
- Głębokie tłoczenie: materiał jest przetwarzany poprzez zastosowanie naprężeń rozciągających.
- Ściskanie: materiał jest przetwarzany poprzez zastosowanie naprężeń ściskających.
Przyczyny i środki zaradcze w przypadku typowych wad tłoczenia
W tej części przedstawione są typowe wady tłoczenia, ich przyczyny i środki zaradcze. Trudno jest całkowicie i stale wyeliminować wszystkie wady z powodu takich czynników, jak właściwości materiału, konstrukcja i zasady obróbki. Ważne jest jednak, by jak najbardziej poprawić wskaźnik wydajności, zmniejszając częstotliwość występowania defektów różnymi środkami zaradczymi.
- Zadziory
- Przyczyna: ten defekt pojawia się na przykład dlatego, że podczas ścinania szczelina (luz) między stemplem a matrycą jest zbyt duża.
Środek zaradczy: upewnij się, że 1/2 do 1/3 grubości blachy jest powierzchnią ścinaną i że stan ten jest jednolity.
Poniżej przedstawiono strukturalne obrazy przekrojów poprzecznych materiału po ścinaniu przy różnych warunkach luzu wraz z objaśnieniami nazw i cech części.
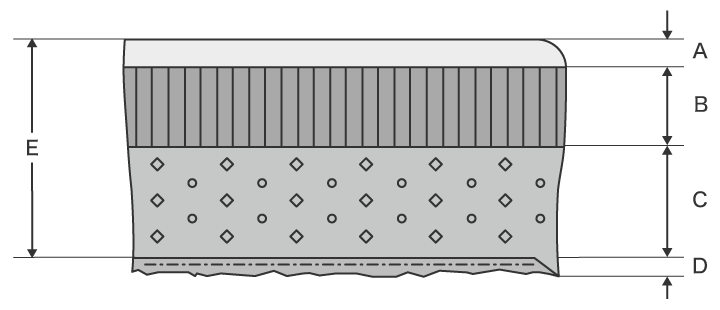
- Ugięcie przy ścinaniu: gładka powierzchnia spowodowana powierzchnią ciągniętego materiału.
- Ścięta powierzchnia: błyszcząca powierzchnia z pionowymi paskami. Widoczne są delikatne rysy spowodowane cięciem stempla podczas ścinania oraz tarciem między osadzającym się metalem a materiałem.
- Spękana powierzchnia: w porównaniu z powierzchnią ściętą jest to bardziej chropowata powierzchnia, która została zdarta, przez co jest bardzo nierówna.
- Zadzior: postrzępiony wypust z materiału. Duże zadziory mogą prowadzić do wad produktów z powodu niedostatecznej dokładności dopasowania części oraz problemów bezpieczeństwa, takich jak urazy spowodowane ostrymi końcówkami zadziorów.
- Grubość płyty
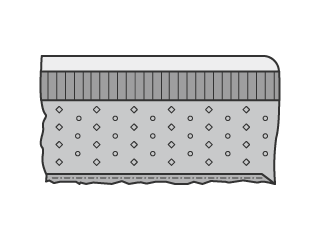
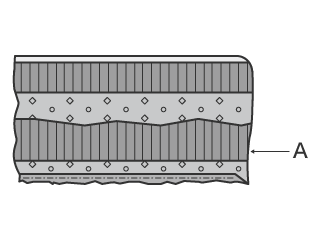
Gdy prześwit przekroczy odpowiednią wartość, im większy prześwit, tym większy zadzior. Ponadto dokładność kształtu i wymiaru zmniejsza się z powodu takich problemów, jak odkształcenia spowodowane ciśnieniem upustu. Z drugiej strony, zbyt mały prześwit powoduje powstanie wtórnej powierzchni ściętej (A na rysunku po prawej) po drugiej stronie powierzchni pęknięcia, co skutkuje powstaniem zadziorów w kształcie wiskerów.
Wielkość zadzioru wyraża się jako grubość jego podstawy (A na rysunku) lub jako jego wysokość (B na rysunku).
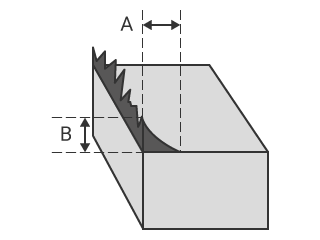
- Sprężynowanie
- Przyczyna: po zgięciu resztkowe naprężenia ściskające i rozciągające w materiale działają przeciwnie do siebie, powodując, że obrobiona część wygina się z powrotem w kierunku swojego pierwotnego kształtu.
Środki zaradcze: wygiąć pod większym kątem niż zamierzony lub dodać do stempla płytkę uderzeniową albo nacięty rowek.
- Zmarszczki
- Przyczyna: powstają, gdy do kołnierza podczas głębokiego tłoczenia jest przyłożona siła ściskająca.
Środek zaradczy: eliminacja zmarszczek za pośrednictwem głębokiego tłoczenia, aby przyłożyć do materiału równomierne obciążenie. Oprócz stałego eliminowania zmarszczek jest też możliwe eliminowanie zmarszczek w ruchu, które wykorzystuje siłę sprężyny lub poduszki matrycy.
- Pęknięcia
- Przyczyny: pęknięcia powstają w materiale, gdy siła rozciągająca przekracza granicę pęknięcia podczas głębokiego tłoczenia.
Podczas gięcia w giętej części mogą pojawić się pęknięcia, rozszczepienia i rozdarcia spowodowane kierunkiem walcowania materiału lub wymiarem szerokości gięcia.
Środki zaradcze: przy głębokim tłoczeniu zmniejszyć ciśnienie tłumiące zmarszczki lub nadać gładkość krzywiźnie matrycy, co zmniejszy odporność na odkształcenia. Podczas gięcia należy się upewnić, że linia gięcia i kierunek walcowania materiału są prostopadłe lub ustawić szerokość gięcia na co najmniej ośmiokrotność grubości blachy.
- Gromadzenie odpadów (powód wgnieceń i zarysowań)
- Przyczyna: jest to zjawisko polegające na tym, że odpady (które powinny zostać usunięte z formy) przyczepiają się do stempla z powodu takich czynników jak ciśnienie próżniowe, warstwy oleju i magnetyzm po obróbce metodą wyciągania. Nagromadzenie odpadów jest przyczyną wad, takich jak wgniecenia i zadrapania na powierzchni materiału, a także może uszkodzić formę.
Środki zaradcze: zamontować na stemplu trzpień wybijający, który stworzy fizyczną szczelinę między odpadami a stemplem. Inne metody obejmują odprowadzanie powietrza z końcówki stempla, wycinanie rowka w stemplu i wprowadzanie tam powietrza oraz odsysanie odpadów od dołu. Można też zmniejszyć stopień przylegania odpadów do stempla przez obniżenie lepkości stosowanego oleju lub przez wycięcie rowka w stemplu w celu zmniejszenia powierzchni kontaktu z olejem.
Przykłady obserwacji przekrojów poprzecznych i defektów na tłoczonych wyrobach
Czasem intensywna praca w zakładzie produkcyjnym to za mało, by uniknąć wad tłoczenia. W początkowych fazach badań i rozwoju, wyboru materiałów oraz projektowania produktów i form należy dążyć do ulepszeń poprzez jak największą liczbę powtarzanych testów i prototypów. W zapewnianiu jakości ważne jest też badanie przyczyn wadliwego działania części metalowych produkowanych metodą tłoczenia i ulepszanie tych części.
Dlatego szczegółowa obserwacja defektów za pomocą mikroskopu optycznego jest niezbędna na wszystkich tych etapach.
Na przykład, mikroskop optyczny może być użyty do szczegółowego sprawdzenia, czy warunki obróbki były odpowiednie w stosunku do odciętej części podczas ścinania i czy zadziory mogą być związane z tymi warunkami. Z drugiej strony, obrobione elementy metalowe są trójwymiarowe, co utrudnia ich obserwację, bo trudno jest uzyskać ostry obraz w całym polu widzenia i ponieważ chropowatość powierzchni i współczynnik odbicia różnią się w tym samym polu widzenia.
W tej części opisano zalety mikroskopu cyfrowego 4K serii VHX, przedstawiając jednocześnie przykłady jego zastosowania do prowadzenia bardzo dokładnych obserwacji mikroskopijnych różnic powierzchniowych, takich jak ugięcie przy ścinaniu, ścięte powierzchnie i spękane powierzchnie w przekroju poprzecznym wyrobu wytłaczanego oraz wyglądu defektów, takich jak zadziory i wgniecenia.
Obserwacja przekrojów poprzecznych wyprasek z dużą precyzją (ugięcie przy ścinaniu, ścięte powierzchnie, spękane powierzchnie)
Przekrój poprzeczny ściętego wyrobu wytłaczanego może być wykorzystany do oceny takich elementów jak odpowiednia wielkość prześwitu między stemplem i matrycą, stosunek powierzchni ściętej do grubości blachy, jakość obróbki i przyczyny powstawania zadziorów. Stan powierzchni — np. wgłębienia i występy, chropowatość i wzór — różni się w przypadku ugięcia przy ścinaniu, ściętych powierzchni i spękanych powierzchni, które pojawiają się w przekroju poprzecznym. Ponadto, mimo że każda część ma ten sam kolor i niski kontrast, współczynnik odbicia światła jest różny, więc trudno jest zaobserwować ogólny stan powierzchni, bo na przykład w niektórych częściach występują odblaski.
Mikroskop cyfrowy 4K serii VHX jest wyposażony w funkcje, które zapewniają zarówno wysoką rozdzielczość, jak i dużą głębię ostrości, takie jak telecentryczny obiektyw HR i matryca 4K CMOS, dzięki czemu mikroskop ma wyjątkową rozdzielczość. Dzięki temu można uzyskać wyraźne obrazy, na których cały przekrój jest ostry, nawet jeśli jeden przekrój zawiera różne powierzchnie.
Specjalnie zaprojektowany układ optyczny, matryca 4K CMOS oraz tryb efektu cienia optycznego — nowa metoda obserwacji, która łączy oświetlenie z analizą przesunięcia (kontrastu) uchwyconego przy oświetleniu z wielu kierunków — pozwalają na wyraźną obserwację mikroskopijnych nierówności powierzchni i innych warunków powierzchniowych z wysokim kontrastem. Obrazy uzyskane w trybie efektu cienia optycznego mogą być łączone z informacjami o kolorze, aby wizualizować informacje o głębokości i wysokości za pomocą różnych kolorów.
Seria VHX pozwala na zastosowanie tej zaawansowanej metody obserwacji za pomocą prostych operacji, co znacznie zwiększa szybkość obserwacji i oceny przekroju poprzecznego, które wymagają dużo czasu na określenie stanu.
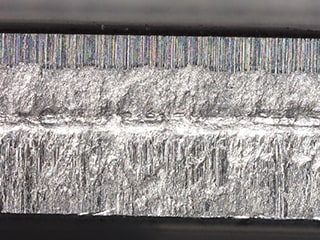
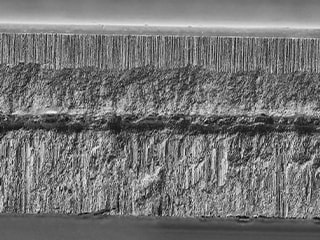
Obserwacja mikroskopijnych zadziorów z pełną ostrością
Nawet jeśli zadziory na tłoczonych produktach są małe, są twarde i ostre, więc mogą sprawić, że produkt będzie mniej bezpieczny. Podczas montażu części mogą pojawić się zadziory, które negatywnie wpływają na wydajność produkcji.
W badaniu przyczyny powstawania zadziorów najważniejsze są informacje o ich podstawie i wierzchołku, ale trudno jest zaobserwować oba te aspekty wyraźnie i jednocześnie w całościowym obrazie za pomocą mikroskopów optycznych, ponieważ zadziory są trójwymiarowe i mikroskopijne, co oznacza, że podczas obserwacji można uzyskać ostry obraz tylko ich części.
Najnowocześniejsza technologia optyczna i system obserwacyjny mikroskopu cyfrowego 4K serii VHX pozwala na obserwację trójwymiarowych obiektów dzięki łatwo rejestrowanym obrazom z pełną ostrością w całym polu widzenia.
Obiektyw, matryca 4K CMOS i oświetlenie pierścieniowe — zapewniające wysoką rozdzielczość i dużą głębię ostrości — pozwalają obserwować nawet zadziory w kształcie wiskerów, dostarczając obrazy 4K o wysokiej dokładności, na których cały zadzior od podstawy aż po czubek jest ostro widoczny.
Dzięki obrazowi o wysokiej dokładności można od razu zobaczyć ogólny widok defektu, co znacznie optymalizuje proces badania przyczyn za pomocą obserwacji.
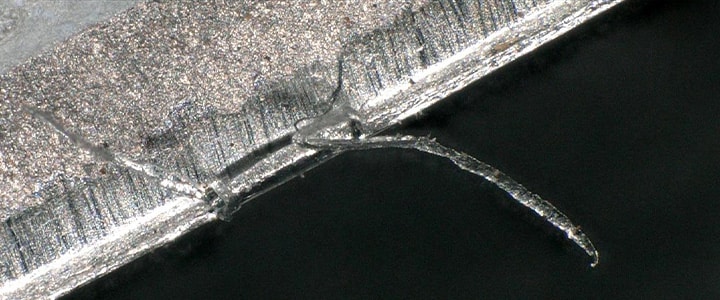
Obserwacja z wysokim kontrastem wgnieceń i innych mikroskopijnych defektów
Drobne wgniecenia i mikroskopijne rysy powstałe w wyniku nagromadzenia odpadów i podobne defekty są minimalnie skontrastowane z tłem, gdy materiałem jest metal. Dlatego czasem trudno było określić warunki i zdarzały się przypadki, niewykrycia wgnieceń i rys, nawet mimo poświęcenia długiego czasu na regulacje.
Dzięki mikroskopowi cyfrowemu 4K serii VHX nie trzeba ręcznie określać warunków. Jednym kliknięciem przycisku operator może wybrać obraz najbardziej odpowiedni do celu obserwacji dzięki funkcji multioświetlenia, która automatycznie pozyskuje dane o oświetleniu wielokierunkowym. Nawet po wybraniu obrazu automatycznie zapisywane są obrazy z innymi warunkami oświetlenia, co pozwala na obserwację w różnych warunkach bez konieczności ponownego umieszczania próbki na stoliku.
Tryb efektu cienia optycznego, nowa metoda obserwacji, która z łatwością rejestruje obrazy o wysokim kontraście, eliminując jednocześnie kłopot związany z koniecznością stosowania próżni, może być wykorzystywany do obserwowania nawet mikroskopijnych wgnieceń na wyraźnych obrazach z wysokim kontrastem.
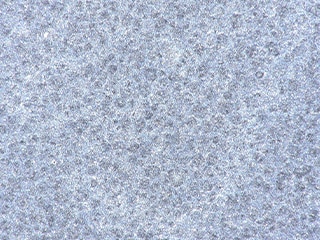
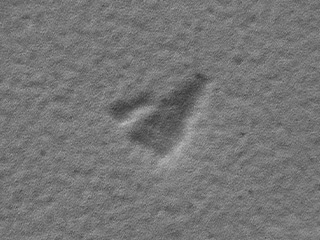
Mikroskop 4K, który optymalizuje badania i rozwój, projektowanie i zapewnianie jakości produktów wytłaczanych
Chociaż obserwacje przekrojów poprzecznych i defektów mikroskopowych produktów tłoczonych są trudne i wymagają długiego czasu na określenie stanu nawet przez doświadczonych operatorów ze względu na takie czynniki jak charakterystyczna połyskliwość materiałów metalowych używanych do produkcji tych produktów, mikroskop cyfrowy 4K serii VHX pozwala na przeprowadzenie tych obserwacji szybko i przy użyciu prostych czynności.
Obrazy 4K o wysokiej dokładności, uzyskiwane za pomocą różnych funkcji, zwiększają zaawansowanie i efektywność obserwacji istotnych dla badań i rozwoju, projektowania i ulepszania produktów i form oraz zapewniania jakości w przypadku wadliwego działania produktów.
Aby uzyskać dodatkowe informacje o serii VHX lub zadać pytanie, kliknij poniższe przyciski.