Instantaneous and Accurate Measurement of Burr Height on Plastic Moulded Products
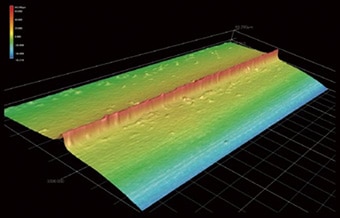
Burrs are typical shape defects that occur in injection moulding and other plastic moulding. Because it is difficult to stop moulding machines at precise intervals, when burrs are formed on large numbers of moulded products, substantial costs are required to remove them. If moulded products with burrs are discarded as defective products, the yield rate will be significantly reduced. This puts a lot of pressure on the profit margin. For these reasons, it is necessary to accurately measure burr shapes and dimension to identify the causes as quickly as possible and work to prevent their recurrence.
Burrs formed on moulded products have three-dimensional shapes, which makes it difficult to accurately measure them using conventional measurement methods. This section explains basic knowledge of plastic burrs and the latest measurement method that solves problems in conventional measurement.
- Burrs on Plastic Moulded Products
- Deburring Methods for Plastic Moulded Products
- Causes of and Countermeasures to Burrs on Plastic Moulded Products
- Problems in Conventional Burr Height and Shape Measurement
- Solution to Problems in Burr Height Measurement
- Summary
Burrs on Plastic Moulded Products
Burrs are one typical type of defect in plastic moulding. This shape defect is formed when molten plastic enters into and solidifies in the mould (male and female mould) parting line or gaps around the ejection pins.
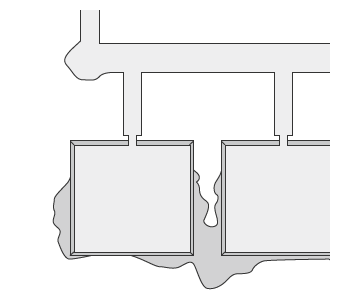
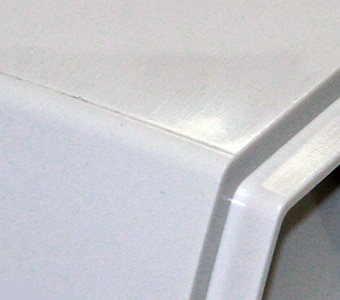
As burrs are unintended projections on the moulded product, they can adversely affect product quality. They may impair product appearance; or, if they are sharp, they may cause injury. When moulding product components, burrs on plastic moulded parts may reduce fitting performance in the assembly process. For these reasons, burrs may be removed using tools when deburring is possible and cost-effective.
Deburring Methods for Plastic Moulded Products
Deburring is performed when the burrs that form on plastic moulded products can be removed and the number of subject products is reasonable. Deburring may also be necessary when there are burrs on moulded products received from overseas factories, and the products must be used in order to meet the delivery deadline.
Manual deburring
Burrs are removed manually when the number of subject workpieces is small or when burrs are located in places where they cannot be removed by automatic deburring machines.
- Handheld deburring tools include deburring files, cutters, blades, and grinding wheels.
- Thermoplastic burrs are removed by melting them off with the heat of a soldering iron or other tool (this method may be used when burrs are thin and the moulded product is thick).
- Burrs are removed after being made brittle by freezing them (this method may be used when burrs are thin and the moulded product is thick).
Other methods such as grinding tools and chemicals may be used with consideration for the moulding material, properties of the moulded product and burrs, workability, and other factors.
Deburring using machines
When products are moulded into complex shapes, the occurrence of burrs in certain locations may need to be tolerated to some degree due to the mould structure. On the other hand, when the shapes of moulded products are simple, deburring using an automatic deburring machine or other machine may be included as a step in the plastic moulding process.
- Blaster: Burrs are removed by directing blast material to contact the moulded products in the machine. The removed burrs are automatically collected by a built-in dust collector.
- Ultra-high pressure waterjet machine: Burrs are removed by directing high-pressure water jets onto the moulded products. This process also serves to clean the moulded products.
- Ultrasonic cutter: A blade vibrating at ultrasonic frequency contacts and removes burrs. Because the micro-vibrating blade contacts thermoplastic plastic which was softened by heat from the plastic molecules, it is possible to remove burrs without applying a significant load to the moulded products.
There are also various other types of automatic deburring machines in addition to the above. The type of machine is selected according to the characteristics of the thermoplastic plastic, thermosetting plastic, or other plastic used for moulded products, as well as factors such as the size, shape, and durability of the moulded products.
Identifying the shapes and dimensions is effective for appropriate deburring
To select the deburring method and decide on an appropriate deburring machine, it is important to acquire as much information as possible about the burrs. Burrs have three-dimensional shapes even when they are thin. In many cases, this makes it difficult to measure their heights and shapes accurately using conventional measuring instruments. These problems in burr measurement and a solution to them will be explained later.
Causes of and Countermeasures to Burrs on Plastic Moulded Products
When larger numbers of defective plastic moulded products caused by unexpected burrs occur, they require large amounts of man-hours and costs for deburring. Therefore, it is definitely best to prevent burrs from occurring in the first place and to improve the processes to prevent burr recurrence.
This section explains examples of typical causes that produce burrs in injection moulding and countermeasures for preventing them.
Examples of causes that result in burrs in injection moulding
- Low mould closing pressure compared to the molten plastic injection pressure
- Decreased accuracy of the parting line between the moulds (male and female moulds)
- Excessively high-flow property of the molten plastic (potentially caused by excessively high temperature of the mould or the molten plastic).
- Gaps between the moulds caused by strain or other factors.
- Imbalance in the amount of injected molten plastic, the mould closing force, and the injection pressure
- Imbalance of the projected area inside the mould and the mould closing force (force that maintains the pressure)
- Strained or tilted die plate in the injection moulding machine
Burrs can be produced as a result of many other causes as well.
Examples of countermeasures to prevent burrs in injection moulding
- Increase the mould closing pressure or reduce the plastic injection pressure.
- Adjust the moulds so that there is a firm fit at the parting line.
- Improve the moulds by using inserts, welding, or other means to eliminate the gaps between the male mould and female mould.
- Apply holding pressure which is appropriate for the projected area of the mould, and adjust it while checking the balance with the mould closing force.
- The mould temperature may be higher than the temperature set with the controller. Adjust the temperature setting while measuring the actual mould temperature.
- When the flow of plastic at the mould gate is poor, excessively increasing the temperature and flow property of the plastic will make it more likely that the plastic will flow out from the parting line. Therefore, review and improve the mould gate based on a suitable plastic temperature.
Because the accuracy of the mould and moulding machine, mould closing pressure, temperature and pressure of the mould and plastic, and other factors are all related to one another, the key to effective countermeasures is checking and correcting these factors from a comprehensive perspective.
Considering countermeasures based on the burr shapes on defective products
The burrs which occur on a moulded product may provide hints regarding the cause. In addition to indicating problematic parts of the mould, burr height and thickness may indicate the size of the parting line gap and the flow property of the molten plastic, while the burr taper angle may indicate die strain or a localised decrease in mould accuracy.
Accurately identifying the locations, shapes, and dimensions of burrs on defective products allows important information to be acquired for carrying out improvements and measures to prevent recurrence.
Problems in Conventional Burr Height and Shape Measurement
As mentioned in the previous section, accurate measurement of the shapes and dimensions of burrs on plastic moulded products can help identify the locations and causes of burrs, prevent their recurrence, and decide the deburring conditions. Height measurement of three-dimensional burrs using conventional profile measurement systems or microscopes involves the following problems.
Problems in burr height and shape measurement using a profile measurement system
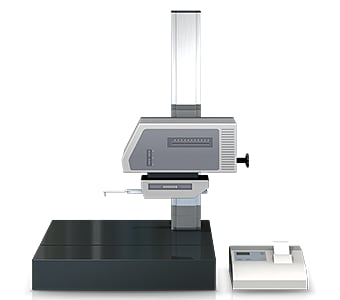
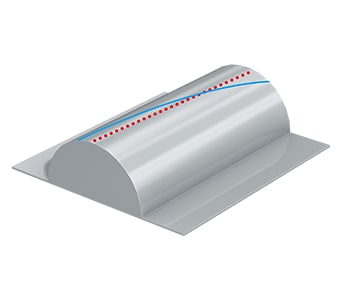
Measurement of burr height using a profile measurement system involves the following problems:
- Measurement work requires much time, including time for fastening the target to a jig and levelling it. Knowledge and skills related to using profile measurement systems are also required in order to level a target accurately.
- When measuring burrs in recessed locations, it is difficult to trace the desired measurement position with the stylus. Even slight displacement of the stylus causes variation in the measured values.
- It is difficult to draw a profile line that passes through the maximum point on a cylindrical target.
- The stylus moves up and down in an arc centred on the fulcrum of the stylus arm, and the tip of the stylus also moves in the X-axis direction. This produces error in the X-axis data.
Problems in burr height and shape measurement using a microscope
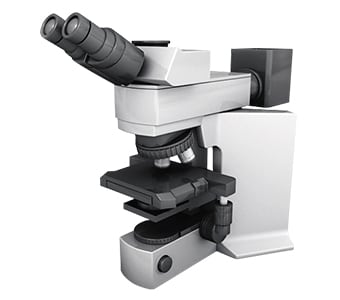
Unlike profile measurement systems, microscopes can capture “surface” information. Groove widths can be measured by determining the amount of stage movement and depth can also be measured by determining the amount of focus adjustment. However, measurement using a microscope involves the following problems.
- When burrs on plastic moulded products are observed at high magnification, the narrow field of view makes it difficult to identify the entire burr shape.
- Because measurement depends on human eyes, there is variation in the measurement results depending on the operator.
- As microscopes are not originally intended to be measuring instruments, they may be unable to quantify the measurement results or provide reliable measurement values.
Solution to Problems in Burr Height Measurement
Plastic moulded products and the burrs which form on these products have three-dimensional shapes; this makes it difficult to accurately measure them using conventional measurement methods. The fact that measurement requires skill as well as much time and labour is also a large problem.
To resolve these problems in burr height measurement, KEYENCE has developed the VR Series 3D Optical Profilometer.
The VR Series accurately captures the 3D shape of the entire target surface without contacting the target. A 3D scan of the target on the stage can be completed in as little as one second for high accuracy measurement of the 3D shape. It is capable of instantaneous and quantitative measurement with no errors in the measurement results. This section introduces some specific advantages of the VR Series.
Advantage 1: Complete measurement in as little as one second. The 3D shape of the entire target surface can be captured accurately with a single measurement.
The VR Series instantaneously acquires 800,000 points of surface data with a single scan in as little as one second. Various profile lines such as linear, parallel, and perpendicular lines can also be drawn by simple and intuitive operations in the desired locations in the precision data. Because accurate profile measurement is also possible, users can instantly acquire detailed data which is indispensable for identifying the causes of burrs.
Even after measurement, profile measurement of different parts can be performed using past wide area 3D scan data without setting and scanning the target again.
The maximum and minimum surface irregularities (height, depth) in the acquired 3D shape can be displayed in a colour map to clearly visualise defective areas over the entire target.
Furthermore, measurement data from multiple targets can be compared side by side, and the desired conditions can be applied to multiple data sets at once. This results in a dramatic reduction in man-hours and improved work efficiency.
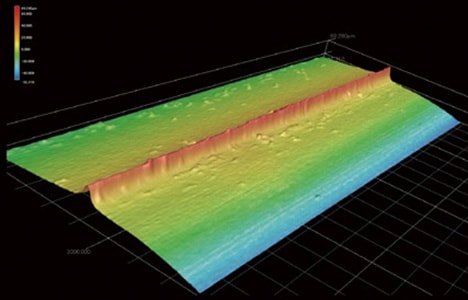
Advantage 2: Capable of burr inspection and measurement over a wide area.
At burr inspections, it is often necessary to identify the maximum burr height. Because the location of the highest burr differs with each individual target, it is necessary to acquire data for the entire measurement area. The VR Series can measure a wide area (up to 11.81 in × 5.91 in), enabling fast and accurate burr peak measurement by a simple operation.
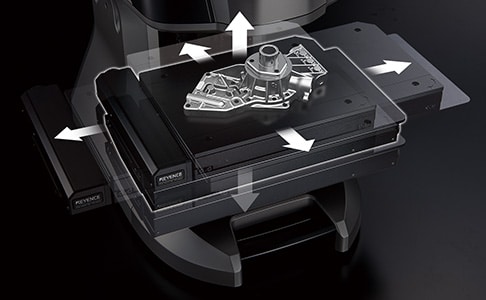
3D shape measurement can be performed easily just by placing the target on the stage and pressing a button. Because automatic position adjustment is possible based on target feature data, strict levelling or positioning is not required. This series also includes the industry’s first Smart Measurement function that automatically configures the measurement range and moves the stage according to the target size. This eliminates the work that was required to set the measurement length and Z-range.
The wide variety of assist tools allows simple and intuitive configuration of the desired measurement conditions.
In addition to easy configuration, the assist tools allow the system to be operated easily even by novices, making it possible even for operators who are unfamiliar with measurement to perform accurate measurement in as little as one second. In addition to purposes such as research, development, and mould trials, this makes it possible to easily increase the number of samples or perform trend analysis for measurement and inspection during commercial production.
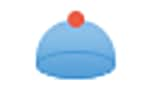
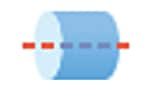
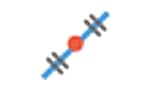
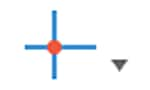
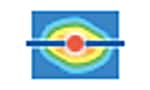
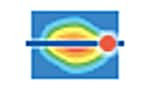

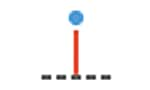
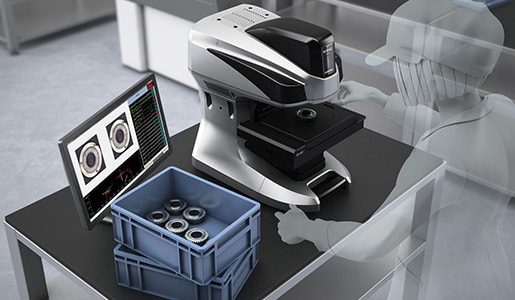
Summary
The VR Series can measure 3D target shapes accurately and instantaneously by high-speed 3D scanning without contacting the target. In addition to 3D measurement of the entire plastic moulded product, the VR Series can complete difficult measurements such as fine burr height and surface irregularity shapes in as little as one second.
Using the VR Series resolves all of the measurement problems involved with conventional measurement.
- The maximum height and shapes of burrs over a wide area (up to 11.81 in × 5.91 in) can be visualised in a colour map.
- Once a scan is completed, profile measurement of any part and comparison of multiple data sets can be performed at any time.
- Without the need for positioning or other preparation, measurement can be performed simply by placing the target on the stage and pressing a button. This eliminates the need to assign a specialised operator for measurement work.
- Because 3D shapes can be measured easily at high speeds with high accuracy, a large number of samples can be measured in a short time. This is useful for quality improvements.
- This eliminates variation resulting from human factors, making true quantitative measurement possible.
This system allows comparisons with CAD data and easy data analysis such as distribution within tolerances. In addition to research, development, and mould trials, it can be used effectively in a wide range of situations in plastic moulding workplaces, including sampling inspections after the start of commercial production and cause analysis when defects occur.