Quantify the 3D Shape of Textured Sheets
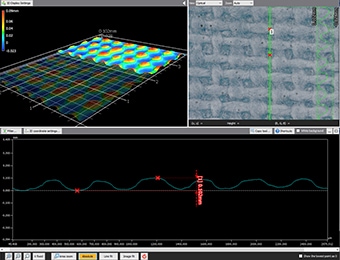
Sheets with a textured surface are used in a wide range of situations. Their purpose and functions are also highly varied and include heat insulation, cushioning, vibration damping, water absorption, slip prevention, bending strength, ease of wiping, pleasing feel, and attractive designs. The types of material and manufacturing methods are equally varied. Methods of creating an uneven surface on the base material include a spinning process which weaves together warp and woof threads, or processing such as embossing or coating of non-woven fabric or flat paper. However, when the unevenness has a height greater or lower than intended, or there is variation in the height or depth, it may be unable to perform its intended function.
This section explains basic knowledge about uneven surface sheets, problems in uneven surface measurement, and a solution using the latest measurement method.
- Textured Surface Sheets
- Types of Textured Sheets
- Processing and Production of Textured Sheets
- Quality Management of Textured Sheets
- Textured Sheets - Measurement Difficulties
- Measurement Solutions
- Summary: Efficient Measurement of Textured Sheets
Textured Surface Sheets
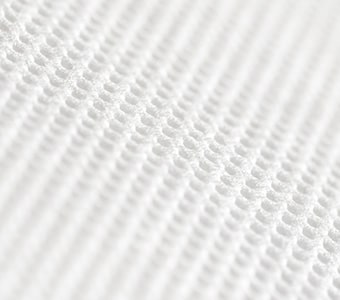
These are sheets which have an uneven rising and falling pattern on the surface that gives the sheet various functions. There are various types classified according to purpose and function, material and size, unevenness shape and pattern, and the processing or manufacturing method. Sheets with a textured surface are widely used in a broad range of applications including the aerospace industry, materials for industrial products such as automobiles and electric appliances, familiar daily commodities, and medical and sanitation products.
Types of Textured Sheets
A textured surface can increase the sheet surface area by giving the surface a three-dimensional shape. The advantages of these shapes are used to create a wide range of types, functions, and applications. Some typical examples are shown below.
- Heat insulation sheet: Capturing warm or cold air in the uneven shape can mitigate temperature differences. Applying such a sheet to a roof or window located between the different temperatures outdoors and indoors reduces the effect on indoor temperature and reduces condensation.
- Heat dissipation sheet: The uneven shape of the sheet functions as a heat sink. Such sheets are used for heat dissipation on components such as CPU and motherboards, power transistors, and power supply parts inside compact electronic devices.
- Cushioning material or vibration damping material: These are sheets of flexible or elastic material such as rubber or urethane with uneven shapes on the surface used to absorb shock or vibration. They are widely used for improving the quietness and interior comfort of automobiles.
- Water absorption sheet: These sheets use the increased surface area provided by the uneven surface to improve the water absorption capability.
Textured surface sheets are also used for a wide range of other products including industrial products, daily commodities, and medical and sanitation products. Uneven shapes may be added for various purposes such as improving the ease of wiping off dirt, preventing slipping, preventing sticking, and attractive designs.
Processing and Production of Textured Sheets
The manufacturing processes and processing technologies used for textured sheets are also highly varied. In case of a textile, it is possible to add the desired function by changing the pitch or the thickness of the warp. In the case of non-woven fabric produced by a spunbond or spunlace method, or a plastic or paper sheet with a smooth surface, various uneven shapes and functions can be added by processes such as embossing or debossing, pattern coating, or etching.
The following section explains the mechanisms of embossing and debossing, which are the most common among these methods.
Embossing and debossing
Embossing and debossing are methods of creating an uneven surface shape by pressing a sheet between two metal or plastic sheets, one of which contains projections and one of which contains indentations, or by pressing a plate with projections onto the sheet from above.
When the shapes created by pressing the sheet between plates (dies) from above and below are higher than the material surface, the process is called embossing. When the shapes are lower than the material surface, it is called debossing. Embossing by applying pressure to the material surface on one side using a single projection plate is also known as “blind stamping.” The mechanism for each process is shown in the schematics below.
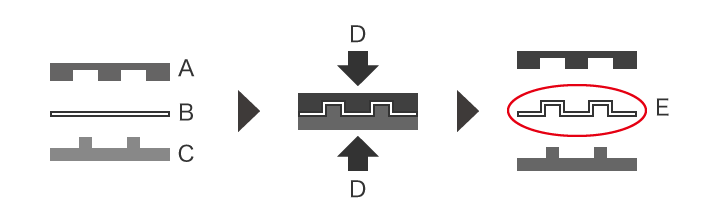
- A
- Indentation plate
- B
- Material (sheet)
- C
- Projection plate
- D
- Applying pressure
- E
- Projecting shape created on the surface
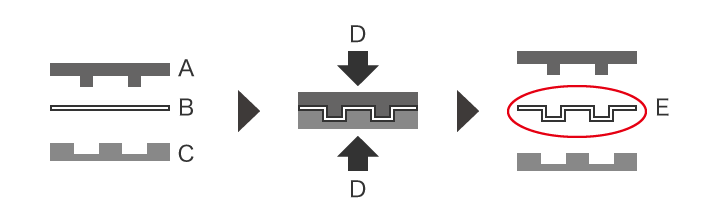
- A
- Projection plate
- B
- Material (sheet)
- C
- Indentation plate
- D
- Applying pressure
- E
- Indentation shape created on surface
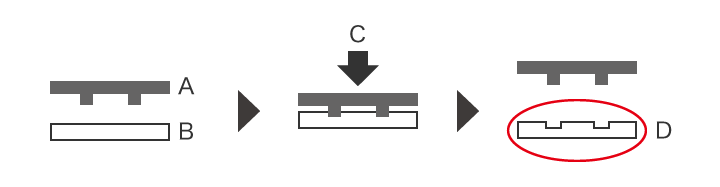
- A
- Projection plate
- B
- Material (sheet)
- C
- Applying pressure
- D
- Indentation shape created without changing the maximum thickness
Quality Management of Textured Sheets
Except for special products, nearly all textured sheets must have a uniform uneven surface pattern. When the height and depth of the uneven shape is not uniform over the entire sheet surface, it will not be possible to produce the desired function or appearance, and the products may be treated as defective.
In case of a fine uneven surface, it is not possible to visually evaluate whether the uneven shape is uniform or not. Even when it is possible at inline inspections to identify the general shape, scratches, bending, wrinkles, and foreign matter on the sheet, it is not possible to precisely measure the height and depth of fine uneven shapes.
With high functionality sheets, because the product cycle is fast, speed is important at every step from R&D through prototyping, evaluation, and commercialisation. Performing efficient and accurate evaluations at each stage will produce a significant difference in the speed.
Textured Sheets - Measurement Difficulties
Regardless of the manufacturing or processing method, it is extremely important to accurately measure the uneven surface shape of sheets when evaluating product performance, quality, and processes. However, measurement using conventional profile measurement systems and other contact measurement systems experiences the following problems.
Measurement difficulties - Profilometer
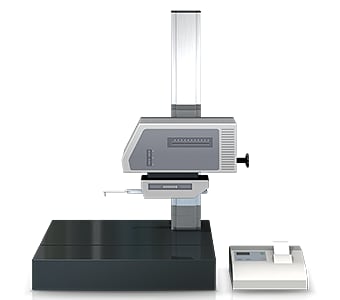
A profile measurement system measures and records the profile of a target by tracing its surface with a stylus.
In recent years, profile measurement systems have been developed that use a laser instead of a stylus to measure complex shapes by tracing the profile in a non-contact manner. Some models are even able to perform measurement of both the top and bottom surfaces.
Measurement and evaluation of textured sheets using a profile measurement system can experience the following problems:
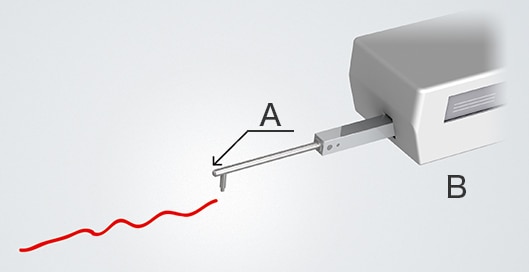
- A
- Stylus
- B
- Detector
- Because the target is measured by tracing along lines, it is difficult to measure and evaluate deformation over a large area.
- It is not possible to identify the uneven shape for the entire target surface.
- When multiple measurement lines are traced in order to measure as large an area as possible, much time is required in order to measure the maximum and minimum heights and depths. In addition, the measured values are unstable due to deviation of the measurement lines.
Measurement Solutions
Conventional contact type measuring instruments only measure shapes using lines or points, and cannot identify the entire shape of a textured sheet. Furthermore, it is difficult to obtain the maximum and minimum values for every surface irregularity on the entire target, or to quickly make quantitative comparisons.
To resolve these measurement problems, KEYENCE has developed the 3D Optical Profilometer VR Series.
The VR Series accurately captures the 3D shape of the entire target surface without contacting the target. It also 3D scans the entire shape in 1 second, enabling instantaneous and quantitative measurement with no errors in the results. This section introduces some specific advantages of the VR Series.
Advantage 1: 3D measurement in 1 second.
The VR Series can acquire surface data from 800,000 points from a thin, flexible, and delicate sheet with a single non-contact measurement in as little as one second. The maximums and minimums of the uneven surface (height, depth) in the acquired 3D shape can be displayed in a colour map to visualise the deformed locations over the entire target.
Multiple profile lines can also be drawn in the desired locations in the scanned data by simple and intuitive operations. Because accurate profile measurement is also possible, detailed data of the deformed parts can be acquired instantly.
Even after measurement, profile measurement of different parts can be performed using past wide area 3D scan data without setting and scanning the target again.
In addition, by using the measurement data of multiple sheets where different processing conditions were applied, it is possible to compare shapes and to apply the desired conditions to multiple sets of data at once.
In addition to accurate measurement and evaluation, this achieves a dramatic reduction of man-hours and improved work efficiency.
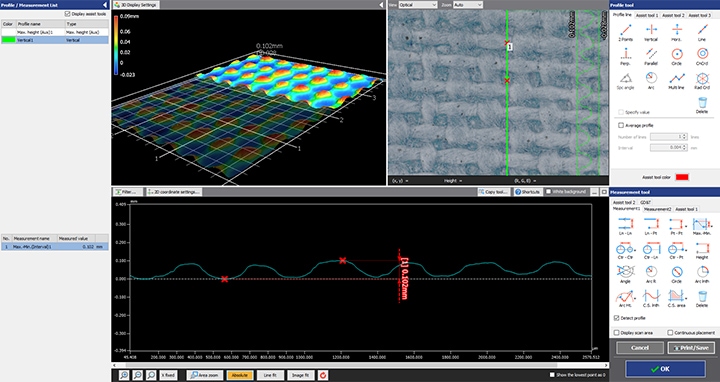
Advantage 2: Operation is easy and measurement can be performed by anyone without variation in the measured values.
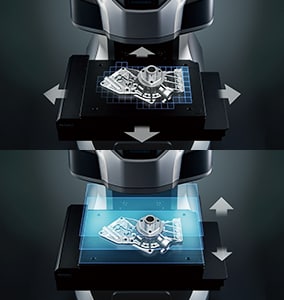
- Top
- Automatic width identification
- Bottom
- Automatic height identification
3D shape measurement can be performed easily just by placing the target on the stage and pressing a button.
By switching between the low magnification and high magnification cameras, accurate measurement of all shape details and surface roughness can be performed using a single system, even for sheets with fine, uneven surfaces.
Because automatic position adjustment is possible based on the target characteristic data, strict levelling or positioning is not required. This series also includes the industry’s first Smart Measurement function that automatically configures the measurement range and moves the stage according to the target size. This eliminates the work that was required to set the measurement length and Z-range.
Assist tools can be used to automatically extract the shape of the surface to ensure measurements are being taken in the same location, regardless of operator. In addition to purposes such as R&D, testing, and evaluation, this makes it possible to easily increase the number of samples or perform trend analysis for measurement and inspection during commercial production as well.
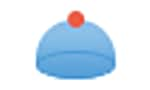
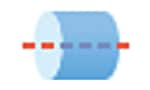
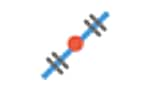
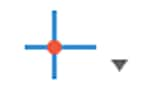
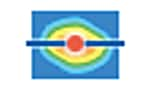
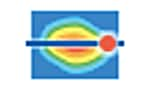
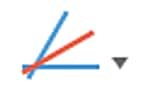
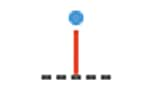
Summary: Efficient Measurement of Textured Sheets
The VR Series can measure 3D target shapes accurately and instantaneously by high-speed 3D scanning without contacting the target. In addition to measuring the 3D dimensions of the sheet, this makes it possible to rapidly complete work that was previously difficult, such as measurement of minute height and uneven shapes, and comparison of multiple data sets.
Using the VR Series offers the following advantages:
- Non-contact, instantaneous scanning.
- Height differences across the entire target can be visualised in a colour map.
- Multiple sets of measurement data can be measured at once.
- Once a scan is completed, profile measurement of any part and comparison of multiple data sets can be performed from past data at any time.
- Without the need for positioning or other preparation, measurement can be done simply by placing the target on the stage and pressing a button. This eliminates the need to assign a specialised operator for measurement work.
- Because 3D shapes can be measured easily at high speeds with high accuracy, a large number of samples can be measured in a short time. This is useful for quality improvements.
- Simple operation and automated control eliminate variation resulting from human factors, making true quantitative measurement possible.
This system allows comparisons with CAD data, and easy data analysis such as distribution within tolerances. In addition to R&D, design, and testing, it can be used effectively in a wide range of situations when manufacturing sheets, including sampling inspection after the start of commercial production and root cause analysis when errors occur.