A Method for Measurement of Strain Shapes
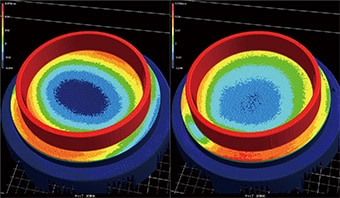
Tension, compression, torsion, and other forces acting on an object are expressed using various terms. The ratio of the deformation generated by the application of these forces is referred to as “strain.” There are three types of strain, classified according to the direction and position of the applied force (load). The resulting deformation includes warpage, waviness, elongation, compression, expansion, and twisting.
Here we will introduce the principles of three types of strain, as well as methods for measuring the deformation caused by strain. We will also introduce the problems in conventional measurement methods, and a solution to these problems.
- Strain
- Strain Measurement Using a Strain Gauge
- Problems in Conventional Strain Shape Measurement
- Solution to Problems in Strain Shape Measurement
- Summary: Dramatic Improvement and Higher Efficiency in Difficult Strain Measurements
Strain
When an object is pulled, pressed, or subjected to other force, the object deforms. For example, when an object is pulled, it elongates in the direction it is pulled in. When the object is pressed, it compresses in the pressing direction. The ratio of the deformed shape to the original shape is referred to as “strain.” Strain includes longitudinal strain, lateral strain, and shearing strain, each with a different load direction.
Longitudinal strain and lateral strain
Longitudinal strain is deformation in the load (compression) direction occurring when the object is pressed. Lateral strain is deformation (expansion) in the direction perpendicular to the load on the object.
Strain also occurs when the object is pulled. In this case, longitudinal deformation is deformation (elongation) in the direction that the load is applied (tension). Lateral strain is deformation (shrinkage) in the direction perpendicular to the load on the object. The ratio between longitudinal and lateral strain is called “Poisson’s ratio.”
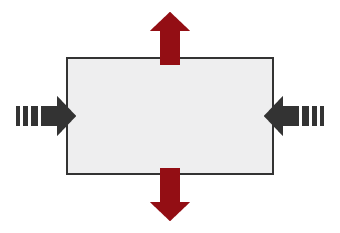
- Compression
- Expansion
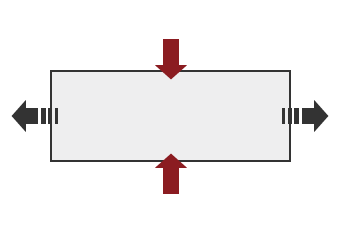
- Tension
- Shrinkage
Shearing strain
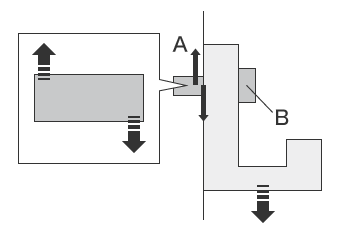
- A
- Shear force
- B
- Hook
This is the strain that occurs when an object is subjected to shear force. This can be understood easily by picturing the force of scissors cutting paper, or a hook used to hang a painting on the wall.
Torsion
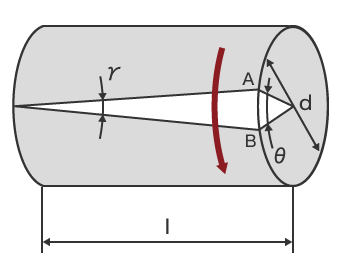
- θ
- Torsion angle:
- γ
- Shearing strain
- l
- Axis length
- d
- Diameter
- AB
- Maximum torsion force
Shear force is generated when the axis is twisted. At the same time a tensile force and compressive force equal to the shear force are generated in two directions inclined by 45° from the axis. As a result, strain caused by torsion is not a single strain, but rather is a combined strain consisting of shearing strain, longitudinal strain, and lateral strain.
Strain Measurement Using a Strain Gauge
A strain gauge measures the amount of strain by utilising the change in resistance that results from gauge expansion and contraction. By attaching the gauge to the location where strain occurs and measuring the resistance values before strain and while strain is occurring, it is possible to identify the strain process. The following expression shows the relationship between the original resistance value, amount of resistance change, and the amount of strain.
⊿R / R = K × ε
- ⊿R
- Amount of resistance change (Ω)
- R
- Original resistance value (Ω)
- K
- Constant of proportionality*
- ε
- Amount of strain
* K is called the “gauge factor,” and is the constant of proportionality which is determined based on the metal material used in the strain gauge.
A strain gauge is designed to measure the amount of strain in an object, and it cannot measure the shape. The strain shape is measured using instruments such as a profile measurement system, height gauge, or coordinate measuring machine.
Problems in Conventional Strain Shape Measurement
Strain occurs as a result of complex deformation regardless of the loading direction. An object under strain has a three-dimensional shape which is conventionally measured using a profile measurement system or height gauge. However, measurement using a profile measurement system or height gauge involves the following problems.
Problems in strain shape measurement using a profile measurement system
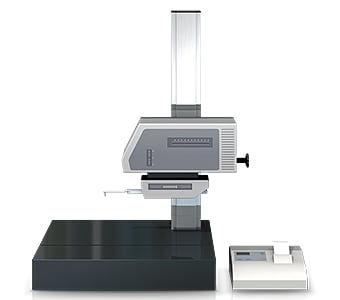
A profile measurement system measures and records the profile of a target by tracing its surface with a stylus. In recent years, profile measurement systems have been developed that use a laser instead of a stylus to measure complex shapes by tracing the profile in a non-contact manner. Some models are even able to perform measurement of both the top and bottom surfaces.
When a profile measurement system measures a three-dimensional target, the target must be positioned so it is level.
This measurement method can experience the following problems:
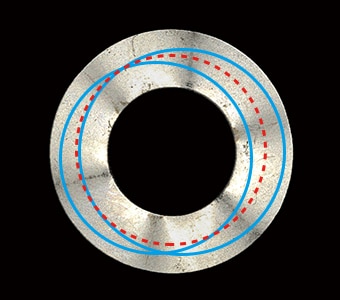
- Measurement and fixturing is time consuming. Knowledge and skills related to using profile measurement systems are also required in order to level a target accurately.
- The stylus of a profile measurement system moves up and down in an arc centred on the fulcrum of the stylus arm, and the tip of the stylus also moves in the X-axis direction. This produces error in the X-axis data.
- Tracing the desired line with the stylus is extremely difficult work, and even slight displacement of the stylus produces error in the measured values.
- As only lines can be evaluated, strain over the entire surface cannot be visualised.
Problems in strain shape measurement using a height gauge
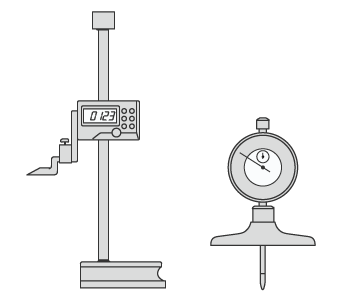
- Left
- Height gauge
- Right
- Depth gauge
A height gauge can be used in combination with a dial gauge to measure height.
- Because only individual points can be checked, it is necessary to perform measurements in many different areas to improve accuracy. However even when much time is invested and many points are measured, it is still impossible to identify the conditions of the entire surface.
- When the part is small or has a complex shape, it may be difficult to perform contact measurement at extremely small parts of a narrow section. Variation in measurement results between different operators and error in the measuring instrument also make stable measurement impossible.
Solution to Problems in Strain Shape Measurement
The measuring instruments that are ordinarily used involve problems such as the long time required to position the target, and the fact that measurement of three-dimensional targets and areas is performed by means of point or line contact. To resolve these measurement problems, KEYENCE has developed the 3D Optical Profilometer VR Series.
The VR Series accurately captures the 3D shape of the entire target surface without contacting the target. It also measures the 3D shape by 3D-scanning the target on the stage in as little as one second with high accuracy. It is capable of instantaneous and quantitative measurement with no errors in the measurement results. This section introduces some specific advantages of the VR Series.
Advantage 1: Capture the entire surface shape. Instantaneously visualise strain in detailed parts.
KEYENCE has fully reviewed the measurement algorithms and hardware, achieving measurement over a wide area of up to 200 mm x 100 mm in as little as one second. This makes it possible to freely measure the target point, including localised shape and strain, and to measure waviness and roughness at the same time as strain. In addition, measurement results do not vary from one person to the next.
With impressive measurement speeds as fast as one second, the VR Series makes it possible to substantially increase the number of samples that are measured, and to shorten the work time. This leads to improved measurement quality, allows inspection operators to be reassigned as production operators, and helps boost production quantities. The VR Series also improves the speed of all measurement tasks such as prototype evaluations and shipping inspections.
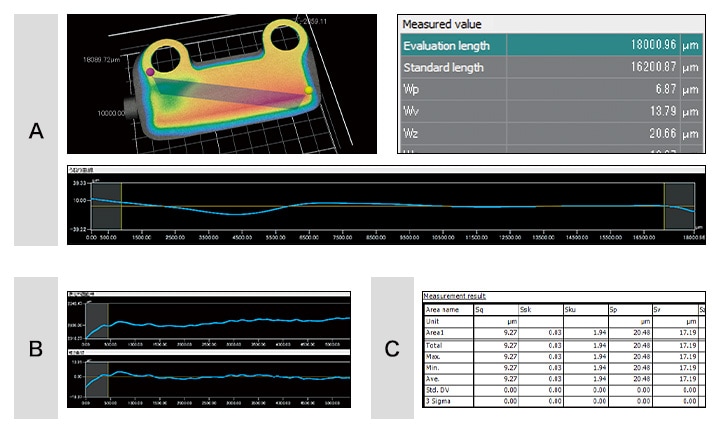
- A
- Waviness and strain measurement
- B
- Roughness profile measurement
- C
- Surface roughness measurement
Unlike profile measurement systems or height gauges, the VR Series extracts the features of the target placed on the stage and automatically corrects its position. The strict positioning which previously required much time and effort is no longer necessary. This makes it possible for even an operator who is unfamiliar with measurement to easily and instantaneously perform measurement. This eliminates the need to assign a specialised operator to measurement work.
With the VR Series, even the parallelism of targets with complex shapes can be accurately measured simply by placing the target on the stage and pressing a button.
Advantage 2: Visually identify changes in strain.
Unexpected deformation of parts can occur due to mechanical stress, including cases of torsion strain where shape changes are complex and measurement is difficult. When such targets are measured by means of lines or points, not only is it impossible to acquire accurate shape data, but identification of the shape itself is difficult.
With the VR Series, you only need to place the target on the stage and scan it. The 3D shape of the target can be captured and no positioning is required.
As the target height can be displayed in colours and profile measurement is possible at any part of the target, it is possible to visualise and identify the locations and precise numerical values of shape defects. This makes it possible to smoothly identify and correct the causes of defects caused by the moulds, dies, and forming conditions.
Because the shape data is measured quantitatively, it is possible to easily manage strain based on numerical tolerances or to use the measurements for trend analysis.
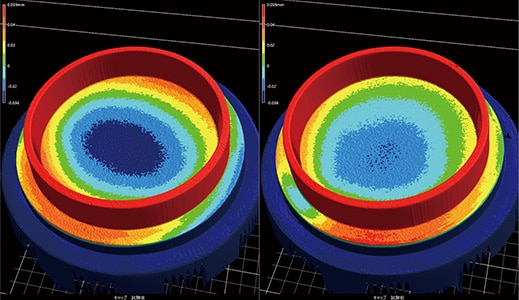
Summary: Dramatic Improvement and Higher Efficiency in Difficult Strain Measurements
The VR Series can measure strain and other 3D target shapes accurately and instantaneously by high-speed 3D scanning without contacting the target.
- Because the entire surface is measured, it is possible to identify all locations of strain on the target, and to perform profile measurement at any desired part.
- No positioning is required. Simply place the target on the stage and press a button to complete measurement.
- 3D shapes can be measured easily at high speeds with high accuracy. This makes it possible to measure a large number of targets in a short time.
- Multiple sets of measurement data can be easily and quantitatively compared and analysed.
In addition, by setting a tolerance for flatness, it is possible to easily judge OK/NG products, and to analyse NG products based on the data. This allows strain measurement and visualisation of minute parts and parts with complex shapes that cannot be measured with conventional methods. The VR Series delivers fast and accurate measurement and seamless data analysis with a dramatic improvement in work efficiency.