Optimising the Observation of Screw Defects (Dents, Scratches, Cracks, and Curvature)
Screws are used to mechanically join together parts in nearly all industrial products. High screw quality and reliability are required not only in the automotive and aerospace industries—where safety is affected by screw accuracy and durability—but also in many products from construction to electronic components.
This section introduces basic screw knowledge and also introduces examples of our 4K digital microscope improving the sophistication and efficiency of screw defect observation and measurement, improvements that are desirable in areas such as research and development and quality assurance.
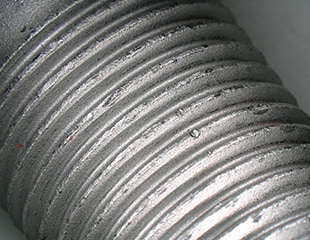
- Screw Basics (Names and Dimensions of Parts, Standards, and Materials)
- Examples of Improving the Sophistication and Efficiency of Screw Defect Observation and Measurement
- A 4K Microscope That Improves the Sophistication of Screw Observation and Analysis
Screw Basics (Names and Dimensions of Parts, Standards, and Materials)
A screw is a securing part with a spiral groove along the side of its cylindrical shaft. Generally, the term screw refers to small screws used alone and the term bolt refers to screws used in combination with nuts. Wood screws have pointed tips and are used in woodworking. This is one example of how screws come in various shapes, conform to various standards, and are made of various materials depending on the materials to join and the application. Basic information for handling screws, such as the names and dimensions of the parts of and the standards for general screws, is described below.
Names and dimensions of screw parts
The names of the typical parts of a (male) screw are shown in the following figure.
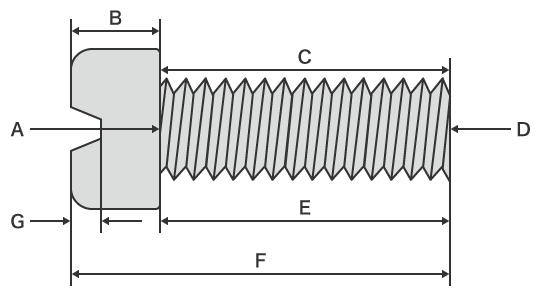
Generally, the length of a male screw is called its nominal length and refers to the length under head (E in the figure). However, this definition varies depending on the screw type and the shape of the head. For example, the total length (F in the figure) is the nominal length in the case of countersunk screws, whose heads are flush with the material when fully screwed in.
If there is a non-threaded part adjacent to the head, this part is referred to as the shank. The shank includes the part of the thread having incomplete peaks and valleys that forms during processing.
Next, typical thread dimensions (for male and female screws) are shown in the following figures and are explained.
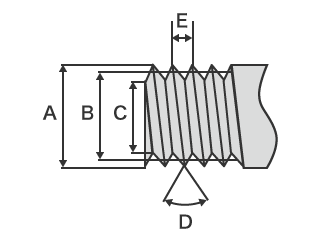
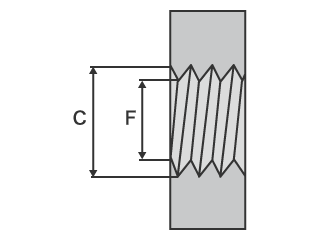
- A
- Crest diameter: Diameter between threads of a male screw. This is the nominal diameter that indicates the thickness of the screw.
- B
- Effective diameter: Diameter of the circle that makes the thread width and the groove width the same.
- C
- Root diameter: Diameter from the base of one valley to the base of the next valley for a male/female screw.
- D
- Thread angle: Angle that opens from the peak of the thread to its surrounding valleys.
- E
- Pitch: Distance between neighbouring thread peaks.
- F
- Crest diameter: Diameter between threads of a female screw.
Screw standards
There are many standards used with screws, leading to differences in dimensions, definitions, and terminology. This section introduces information such as typical standards, definitions, and notations.
- Metric threads
- Refers to screws having a thread angle of 60° and whose nominal dimensions and thread pitch are expressed in millimetres. These screws are classified into coarse pitch threads and fine pitch threads according to the different thread pitches.
They are expressed as “the screw’s nominal diameter × its pitch.” The maximum thread diameter (in millimetres) is listed behind the letter M. For example, M10 indicates the screw has a nominal diameter of 10 mm. Coarse pitch threads are standard. If a screw has fine pitch threads, with small spacing between threads, it is expressed as “MXX × the pitch.” - Unified threads
- Refers to screws having a thread angle of 60°, the same as metric threads, but whose nominal dimensions are expressed in inches. The thread pitch indicates the number of threads within one inch. The unified threads standard is sometimes referred to as inch threads or American threads and is used in, for example, the aerospace industry. Unified threads are available with coarse pitch (UNC), which is the normal size, and with fine pitch (UNF).
“Screw crest diameter (screw number) - (hyphen) number of threads per inch, screw type (UNC or UNF)” is the notation used. For example, “1/4-20UNC” indicates a unified thread screw with coarse pitch having a crest diameter of 1/4 inch and 20 threads per inch.
Screw materials and characteristics
Just as there are diverse shapes and standards for heads and threads depending on the screw application, the materials used also vary. The types and characteristics of typical screw materials are explained below.
- Steel
- The main steel materials used in screws are listed below.
- Carbon steel: This is the most common iron/steel material used in screws. S45C (which has a carbon content of approximately 0.45%) is a hard and strong carbon iron/steel material for mechanical structures and is often used in screws.
- Alloy steel: Formed by adding molybdenum (Mo) or chromium (Cr), this material is used in bolts and other products where strength is required.
- Stainless steel: Generally having excellent corrosion resistance and mechanical properties, this material is classified according to its structures that change under heat treatment such as Cr (Cr martensitic/18Cr ferritic) and Cr-Ni (18-8 austenitic). Austenitic stainless steel is commonly used in screws.
- Copper/copper alloy
- Although this material has lower mechanical strength than other metal materials, it is easy to mould and has excellent electrical and thermal conductivity, ductility, and corrosion resistance. It is commonly used for the securing screws of terminals. Pure copper is classified according to how much oxygen it contains (according to the purity of the copper) into tough pitch copper (with a purity of 99.5%), deoxidised copper (tough pitch copper that has undergone hydrogen embrittlement), and oxygen-free copper (with a high purity of 99.995%). From the point of view of cost, tough pitch copper is most often used as the material for screws.
- Aluminium/aluminium alloy
- Aluminium screws can be made to be approximately 1/3 lighter than steel ones. Aluminium also has excellent corrosion resistance and thermal conductivity and is relatively easy to recycle, which gives it the advantage of being environmentally friendly. On the other hand, the problem with aluminium is that it is relatively weak compared to steel. Aluminium screws can be subjected to heat treatment to strengthen their surfaces and to improve the strength of this material, which makes it possible to obtain the characteristic advantages of aluminium while overcoming its disadvantages.
- Titanium/titanium alloy
- Titanium screws are approximately 60% lighter than steel ones while having excellent resistance against corrosion and heat and approximately the same strength as carbon steel. On the other hand, titanium is difficult to process and is very expensive. Titanium (pure titanium) and titanium alloy have different properties. Their main applications are listed below.
- Titanium: Has high corrosion resistance and is not toxic to the human body. Its excellent biocompatibility leads it to be used in medical bolts and similar applications.
- Titanium alloy: Having a high strength to weight ratio, this material is used in the aerospace industry. Because it is difficult to process, the unit price of titanium alloy screws is high.
- Magnesium/magnesium alloy
- The weight of magnesium is approximately 1/4 that of steel and approximately 2/3 that of aluminium, which makes it extremely lightweight as a metal material used in screws. In addition to being lightweight, magnesium alloy has a high specific strength; excellent electromagnetic shielding, heat dissipation, and vibration absorption; and provides the additional advantage of electrolytic corrosion not occurring when fastened to a case made of the same material. Consequently, it is used in a wide range of fields including automobiles, aircraft, and electrical products. On the other hand, some of its poor properties include low corrosion resistance and the fact that it is difficult to process, so consideration must be given to the usage environment and to surface processing that can compensate for this material’s disadvantages.
- Plastic
- Although it has low strength, plastic is lightweight and easy to mould. Different types of plastic also provide various properties such as corrosion resistance and chemical resistance. Screws can be made out of diverse types of plastic to match the application. For example, PP (polypropylene) has low specific gravity and is resistant to hydrolytic degradation and POM (polyacetal) has well-balanced mechanical properties and excellent chemical resistance.
Examples of Improving the Sophistication and Efficiency of Screw Defect Observation and Measurement
With few exceptions, screws, bolts, nuts, and washers are three-dimensional metal objects. Therefore, in most cases, the problems of only a part of the image coming into focus and it being difficult to determine lighting conditions due to the glossiness of the target or the low contrast with the background could not be avoided when observing dents, scratches, cracks, and other appearance defects that negatively impact quality and when observing three-dimensional shape defects. Also, with contact measurement systems and optical microscopes, it is very difficult to measure three-dimensional shapes with high accuracy, and a major problem was variations in values between operators.
KEYENCE’s VHX Series 4K digital microscope provides an observation system using electronic control and advanced technology such as a high-resolution HR lens and a 4K CMOS image sensor, enabling observation as well as 2D and 3D measurement with simple operations and clear, 4K high-resolution images. At the same time, it solves various problems, improves the sophistication of observations, quantifies measurements, and makes operations more efficient to reduce how long they take.
Tilted observation of threads
The free-angle observation system of the VHX Series 4K digital microscope can be used to clearly observe microscopic dents and scratches at low and high magnifications and from any angle without changing the position of the screw.
The large depth of field allows for quick defect observation with images that are focused throughout the field of view, eliminating the hassle of focus adjustment even for three-dimensional targets.
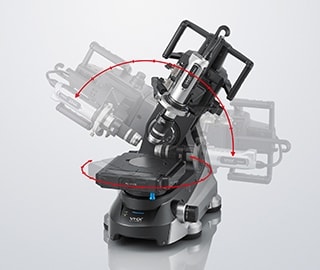
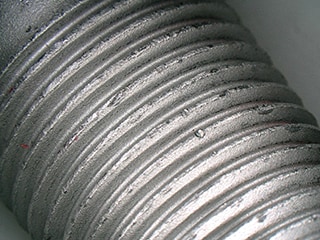
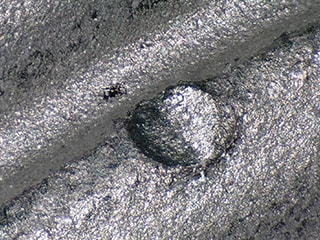
Observation of nut curvature
The VHX Series 4K digital microscope is equipped with Optical Shadow Effect Mode, which easily acquires at the touch of a button high-contrast information while eliminating the hassle of requiring a vacuum. It is possible to observe subtle surface irregularities on metal, which are difficult to observe due to their low contrast.
The target’s colour information can be overlaid on the Optical Shadow Effect Mode image, enabling simultaneous representation of the uneven surface and colour information. As shown in the following figure, the colour map image can be used to assign colours to microscopic uneven surface information, such as that of the curvature of a small nut, visualising it in an easy-to-understand manner.
With the VHX Series, 2D and 3D measurements can be made directly from high-resolution 4K images. The profile information of the desired location can also be acquired during 3D measurement. The automatic creation of reports containing observation images and measured values can be supported with just one device.
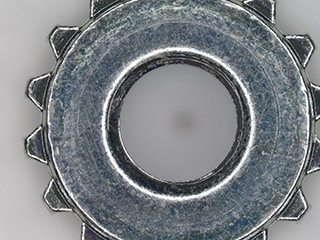
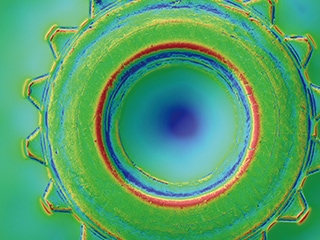
Optical Shadow Effect Mode colour map image (20x)
A 4K Microscope That Improves the Sophistication of Screw Observation and Analysis
The VHX Series 4K digital microscope not only increases the sophistication of observations with clear 4K images, but also greatly improves the level of observation and analysis with diverse observation systems and functions.
The free-angle observation system allows for easy field-of-view alignment, rotation, and oblique axis motion. Eucentric design ensures that the target stays centred in the field of view, even if the lens is tilted or rotated. Smooth tilted observation of three-dimensional and microscopic targets such as screw defects is now possible.
Difficult tasks, such as the observation and visualisation of subtle scratches or microscopic surface irregularities like curvature, can now be performed with simple operations by using Optical Shadow Effect Mode to acquire high-contrast information.
The VHX Series not only increases the sophistication of and quantifies observation and analysis in research and development as well as in quality assurance but also speeds up work, eliminates overspecialisation by making operations easier, and provides numerous other advantages. For additional product info or inquiries, click the buttons below.