Řešení problémů při měření deformace po tepelném zpracování
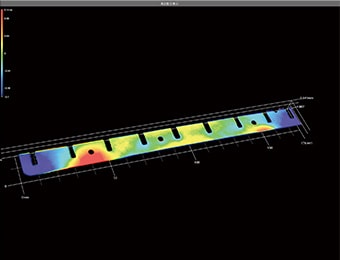
Obecně lze říci, že tepelné zpracování je proces, při kterém se na materiály nebo produkty působí teplem. Tepelné zpracování zahrnuje zpracování kovových materiálů zahříváním a tepelnou sterilizaci potravin a jiných produktů. Tato část se zabývá deformací kovu v důsledku tepelného zpracování. Zatímco deformace v důsledku tepelného zpracování může být jednoduchá, například stlačení nebo deformace v případě čtvercových nosníků a tyčí, u produktů složitých tvarů může dojít k trojrozměrné deformaci. To vyžaduje pokročilé technologie pro měření těchto tvarů.
Tato stránka vysvětluje základní poznatky o deformacích způsobených tepelným zpracováním, které se používají u materiálů ze železa nebo oceli pro kontrolu jejich struktury a zlepšení jejich vlastností. Zabývá se také problémy s měřením deformace a některými možnými řešeními.
- Tepelné zpracování kovů
- Příklady deformace způsobené tepelným zpracováním (změna objemu v důsledku fázové přeměny)
- Opatření k prevenci deformačních problémů způsobených tepelným zpracováním
- Problémy při konvenčním měření deformace po tepelném zpracování
- Řešení problémů při měření deformace po tepelném zpracování
- Shrnutí: Dramatické zlepšení měření deformace po tepelném zpracování
Tepelné zpracování kovů
Tepelné zpracování kovů je technika zpracování, při níž se kov zahřívá a ochlazuje, aby se změnily jeho vlastnosti, aniž by se změnil jeho tvar. Mezi vlastnosti, které je třeba upravit, patří pevnost, tvrdost, houževnatost, odolnost proti nárazu, odolnost proti opotřebení, odolnost proti korozi, obráběcí vlastnosti a zpracovatelnost za studena.
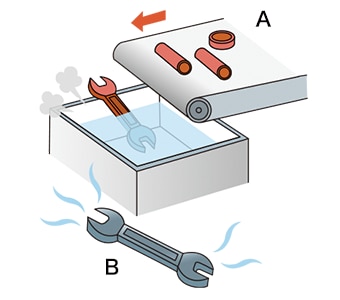
- A
- Zahřívání (dokud kov nezčervená)
- B
- Chlazení (dokud zahřátý kov nezčerná)
Příklady deformace způsobené tepelným zpracováním (změna objemu v důsledku fázové přeměny)
Existuje více metod tepelného zpracování, včetně kalení, temperování, žíhání a normalizace. Během těchto procesů dochází k jevu známému jako fázová přeměna.
Fázová přeměna je proces, ke kterému dochází při tepelném zpracování, kdy se kov mění z pevné látky na kapalinu a poté se opět mění z kapaliny na pevnou látku. K tomu dochází proto, že se mění aktuální forma (struktura) kovu, když se mění jeho krystalová mřížka v důsledku teploty. Když se během fázové přeměny mění struktura, mění se i objem, což způsobuje deformaci.
Například když se eutektoidní ocel, což je ocel obsahující přibližně 0,8 % uhlíku, zahřeje z pokojové teploty, aby se vytvořila austenitová struktura, a poté se ochladí, deformuje se v důsledku změny struktury. Struktura po fázové přeměně se liší v závislosti na způsobu chlazení, a proto způsob chlazení ovlivňuje také velikost deformace.
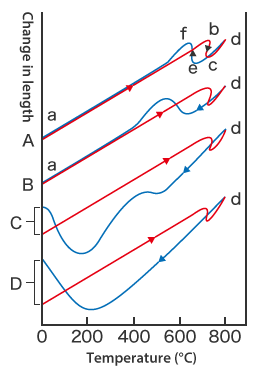
Tento graf ukazuje rozdíly v deformaci způsobené různými způsoby chlazení.
V případě A se kov v důsledku zahřívání rozpíná (a → b) a změny jeho rozměrů v důsledku fázové přeměny lze pozorovat při teplotě přibližně 750 °C během zahřívání (b → c) a při teplotě přibližně 730 °C během ochlazování (e → f).
V případě C (chlazení olejem) a D (chlazení vodou) je zřejmá změna délky po ochlazení.
- A: Chlazení v peci (pomalé chlazení)
- Kov se po zahřátí uchovává v peci a uvnitř pece se ochlazuje. Tato metoda ochlazuje kov rychlostí přibližně 30 °C za hodinu. Struktura po fázové přeměně je perlitová.
- B: Chlazení vzduchem
- Po zahřátí se kov vyjme z pece a ochladí se na pokojovou teplotu. Struktura po fázové přeměně je sorbit.
- C: Chlazení olejem
- Zahřátý kov se ochladí v oleji. Obvykle se kov chladí v oleji při teplotě přibližně 60 až 80 °C. Ve struktuře po fázové přeměně se část austenitové struktury přemění na troostit.
- D: Chlazení vodou
- Kov se ochladí ve vodě o teplotě přibližně 40 °C. Struktura po fázové přeměně je martenzit.
Opatření k prevenci deformačních problémů způsobených tepelným zpracováním
Kromě fázové přeměny popsané v předchozí části patří mezi další příčiny deformačních problémů způsobených tepelným zpracováním nesprávný nebo nerovnoměrný tvar povrchu nebo ohřev/chlazení. V této části jsou vysvětleny tyto deformační problémy, jejich příčiny a opatření, která jim mají zabránit.
Trhliny při kalení
Jedná se o problém, při kterém dochází k praskání materiálu. Může se objevit následující den po kalení nebo později po ochlazení materiálu na teplotu přibližně 200 °C nebo nižší.
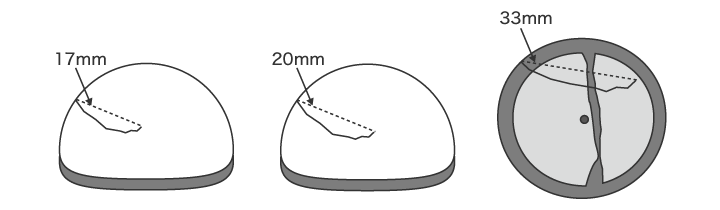
- Příčiny:
- Mezi možné příčiny patří tvarové vady způsobené objemovou roztažností v důsledku nerovnoměrného ohřevu nebo chlazení, nevhodné temperování bezprostředně po kalení a příliš vysoká teplota kalení.
- Protiopatření:
-
- Zkontrolujte tvar produktu a stav povrchu.
- Kalené materiály nechlaďte na teplotu přibližně 200 °C nebo nižší.
- Temperování materiálů provádějte ihned po kalení.
- Snižte teplotu kalení.
Trhliny při broušení
Jedná se o problém, při kterém dochází k praskání ocelového materiálu při jeho broušení po tepelném zpracování. Existují dva typy trhlin při broušení: trhliny při broušení typu 1, které vznikají, když povrch opracovaný řezáním, leštěním nebo jiným způsobem dosáhne teploty přibližně 100 °C, a trhliny při broušení typu 2, které vznikají, když povrch opracovaný řezáním, leštěním nebo jiným způsobem dosáhne teploty přibližně 300 °C.
-
Trhlina při broušení typu 1
-
Trhlina při broušení typu 2
- Příčiny:
- Zbytkový austenit se při přeměně na martenzit rozpíná. Napětí způsobené tímto rozpínáním způsobuje praskání materiálu. K této deformaci může dojít také tehdy, když povrch opracovaný řezáním, leštěním nebo jiným způsobem dosáhne teploty přibližně 650 až 850 °C.
- Protiopatření:
-
- Proveďte vhodné temperování.
- Snižte teplo vznikající třením při broušení.
Deformace při kalení
Existují dva typy deformace oceli způsobené tepelným zpracováním: tepelná deformace způsobená tepelnou roztažností nebo smršťováním při kalení nebo temperování a změna objemu způsobená fázovou transformací.
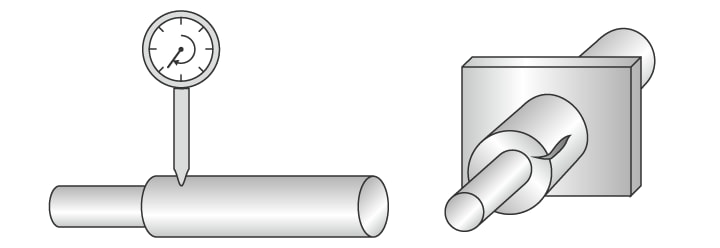
- Příčiny:
- K této deformaci dochází v důsledku nerovnoměrného zahřívání nebo ochlazování, rychlého zahřívání nebo ochlazování nebo dílů s nestejnou tloušťkou. Pokud má materiál složitý tvar, může tuto deformaci způsobit i nerovnoměrné rozložení teploty v materiálu.
- Protiopatření:
-
- Zkontrolujte tvar, aby se produkt mohl rovnoměrně zahřívat a chladit.
- Snižte rychlost ohřívání a chlazení.
Problémy při konvenčním měření deformace po tepelném zpracování
Je nesmírně důležité ověřit, zda rozměry a tvary po tepelném zpracování odpovídají tolerancím. Zejména produkty složitých tvarů vyžadují vysoce přesné a kvantitativní 3D měření tvaru.
Při konvenčním měření deformace po tepelném zpracování se používají systémy pro měření profilů nebo souřadnicové měřicí stroje. Při měření pomocí konvenčního souřadnicového měřicího stroje nebo systému pro měření profilů však existují různé problémy. Patří mezi ně vysoká náročnost potřebná k získání přesných měření a kolísání naměřených hodnot.
Problémy při měření deformace pomocí systému pro měření profilů
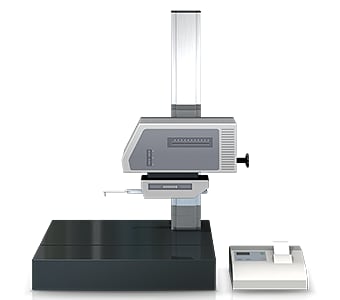
Systém pro měření profilů měří a zaznamenává profil cíle sledováním jeho povrchu pomocí stylusu. V posledních letech byly vyvinuty systémy pro měření profilů, které používají k měření složitých tvarů bezkontaktním trasováním profilu laser místo stylusu. Některé modely jsou dokonce schopny měřit horní i spodní povrch.
U systému pro měření profilů je však nutné získat přesné měřicí linie pro měřicí body.
To zahrnuje následující problémy.
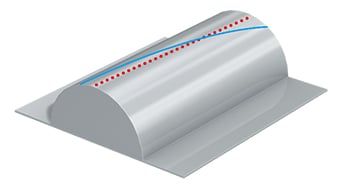
- Měření vyžaduje mnoho času, včetně času na upevnění vzorku na přípravek a jeho vyrovnání. K přesnému vyrovnání cíle jsou rovněž zapotřebí znalosti a dovednosti související s používáním systémů pro měření profilů.
- Stylus systému pro měření profilů se pohybuje nahoru a dolů v oblouku se středem v opěrném bodě ramene stylusu a hrot stylusu se pohybuje také ve směru osy X. To vede k chybám v údajích o ose X.
- Obkreslení požadované čáry pomocí stylusu je nesmírně obtížná práce a i malé posunutí stylusu způsobuje chyby v naměřených hodnotách.
- Zvýšení počtu cílů je složité i z důvodu nutnosti přesně určit konkrétní místa měření.
- Měřit lze pouze část cíle a vyhodnocení celého povrchu není možné.
Problémy při měření deformací pomocí souřadnicového měřicího stroje
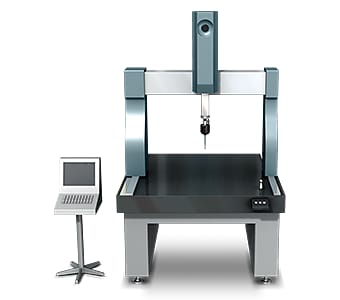
Typické souřadnicové měřicí stroje používají sondu ke skenování nebo sledování povrchu a shromažďování dat z několika bodů s určitou roztečí.
Tato metoda měření zahrnuje následující problémy.
- Zajištění, aby se sonda pohybovala tak, jak má, je nesmírně obtížný úkol, zejména v případě přímek podél středu válce nebo zakřiveného povrchu nebo přímek procházejících středem kružnice. Pokud má kružnice nebo kruh široký středový úhel, pak se i malá chyba v měření značně zvětší, protože celá kružnice se počítá na základě krátkého oblouku. Takové odchylky v měřicích bodech mohou mít za následek mírné odchylky v naměřených hodnotách.
- Při měření malého 3D tvaru se může stát, že se sonda nebude moci dotknout měřených míst. Protože přesnost měření je úměrná počtu měřených bodů nebo čar, je nutné měřit velký počet bodů nebo čar.
Měření pomocí souřadnicového měřicího stroje tak s sebou nese značné problémy, mezi něž patří skutečnost, že ne všichni operátoři na pracovišti mohou přesně měřit tvary, existence dílů, které nelze měřit vůbec, a omezená místa, kde lze stroj nainstalovat.
Řešení problémů při měření deformace po tepelném zpracování
Tyto měřicí přístroje mohou mít problémy s umístěním objektu nebo hrotu sondy a mohou mít potíže s poskytováním celkových dat o měření 3D povrchu, protože měří pouze pomocí bodů nebo čar. Pro řešení těchto problémů vyvinula společnost KEYENCE optický 3D profilometr řady VR.
Řada VR přesně zachycuje 3D tvar celého povrchu cíle již za jednu sekundu a bez kontaktu s cílem. Dokáže okamžitě a přesně kvantifikovat celý 3D povrch bez chyb měření. V této části jsou představeny některé konkrétní výhody řady VR.
Výhoda 1: Měření velkého počtu bodů již za jednu sekundu
Řada VR získává povrchová data (800 000 bodů) pro 3D tvar cíle již za jednu sekundu, což výrazně zkracuje dobu potřebnou pro měření velkého počtu bodů. Přesně a okamžitě měří maximální a minimální nerovnosti na celém povrchu cíle a umožňuje rychlé vyhodnocení všech míst na cíli na základě nastavených tolerancí.
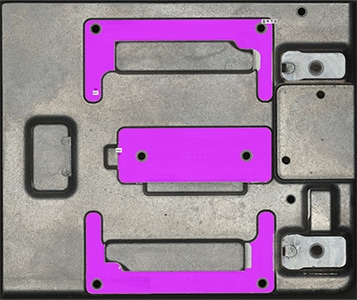
Po naskenování obrobku lze jeho profil (průřez) měřit i na jiných místech, než která byla použita při minulém měření. Díky tomu není nutné znovu nastavovat a měřit stejný cíl.
Výhoda 2: Naměřené údaje lze porovnat s referenčními údaji
Řada VR dokáže více než jen efektivně shromažďovat data. Naměřená data lze zobrazit v seznamu a na všechna data lze současně použít stejný obsah analýzy.
Je možné rychle zkontrolovat rozdíly v datech získaných měřením více tvarů cíle před a po tepelném zpracování a velikost rozdílu u špatných produktů ve srovnání s referenčním produktem. To umožňuje snadnou kvantitativní analýzu a vyhodnocení deformace způsobené tepelným zpracováním.
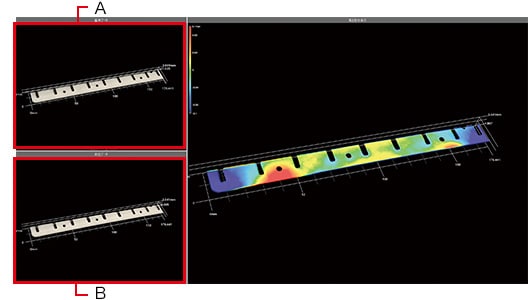
- A
- Referenční údaje
- B
- Údaje o měření
Řada VR dokáže rychle měřit cíle složitých tvarů, což by dříve vyžadovalo mnoho času a práce. Nejenže jsou data rychle zachycena, ale všechny výsledky měření jsou digitalizovány, což výrazně snižuje práci potřebnou k porovnávání a analýze dat.
Shrnutí: Dramatické zlepšení měření deformace po tepelném zpracování
Dříve bylo měření deformace způsobené tepelným zpracováním časově náročné, což omezovalo počet měřených vzorků. V některých případech nebylo měření vůbec možné kvůli složitému tvaru dílu. Řada VR je však schopna rychle měřit a kvantifikovat deformace těchto tvarů. Díky tomu může řada VR vyhodnocovat kvalitu produktů s vyšší úrovní přesnosti a efektivity.
- Výrazné zkrácení času stráveného měřením složitých tvarů díky současnému snímání dat o celém povrchu.
- Různé rozdíly v deformaci lze snadno identifikovat a analyzovat zachycením a porovnáním více sad naměřených dat.
- Je možné provádět skutečná kvantitativní měření, čímž se eliminují odchylky výsledků způsobené lidskou chybou.
- Stačí umístit cíl na podložku a kliknutím na tlačítko zachytit přesná data, čímž odpadá potřeba specializovaného operátora, protože není potřeba žádné polohování ani jiná příprava.
- Přesné měření mnoha cílů v krátkém čase díky vysokorychlostnímu skenování.
Řada VR je také schopna porovnávat data s předchozími skeny a modely CAD a analyzovat drsnost.