Metoda pro přesné a snadné měření opotřebení
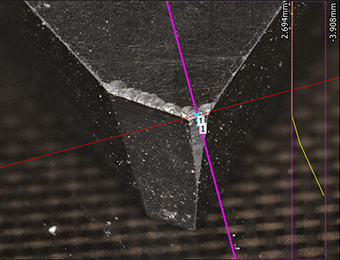
K opotřebení dochází na hranách břitů, kluzných částech mechanických dílů, a má velký vliv na výkon. Účinky opotřebení mohou způsobit poruchu obrábění (v důsledku tepla nebo vibrací), poruchu provozu (způsobenou uvolněním) a v nejhorším případě mohou vést k poruše nebo poškození stroje.
K zabránění opotřebení lze použít olej nebo jiná maziva. Opotřebení je však obtížné zcela zabránit a zůstává potenciálním rizikovým faktorem. Z tohoto důvodu je měření opotřebení nezbytné pro udržení kvality produktů, provádění údržby zařízení a zajištění bezpečnosti.
- Opotřebení
- Typy opotřebení
- Nutnost měření opotřebení
- Problémy při konvenčním měření opotřebení
- Řešení problémů při měření opotřebení
- Shrnutí: Dramatické zlepšení a vyšší efektivita při obtížném měření opotřebení
Opotřebení
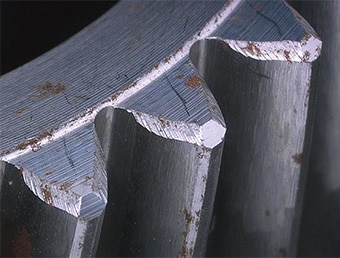
K opotřebení dochází, když se materiál pevného povrchu v důsledku tření postupně odstraňuje. Na tření a opotřebení mají vliv vnější faktory (např. zatížení, rychlost, teplota a atmosféra) i technické faktory (např. geometrický tvar, deformace a stav rozhraní).
Eroze je podobná opotřebení a označuje opotřebení způsobené třením mezi kapalinou a pevným předmětem. Například může docházet k erozi mezi kapalinou v potrubí a stěnami potrubí.
Typy opotřebení
Protože k opotřebení dochází v důsledku mimořádně velkého počtu parametrů, které se vzájemně složitě ovlivňují. To zahrnuje místo tření, fyzikální vlastnosti třecích materiálů, okolní atmosféru, teplo, teplotu a fyzikální a chemické působení. V této části jsou uvedeny některé typické typy opotřebení.
Adhezivní opotřebení
K adhezivnímu opotřebení dochází, když se dva pevné předměty o sebe třou a spojí se (dochází k jejich dotyku), poté se zlomí a oddělí. Adhezivní opotřebení vzniká v důsledku chemických vazeb mezi pevnými předměty. Z tohoto důvodu se častěji vyskytuje mezi následujícími druhy pevných předmětů.
- Materiály stejného typu
- Materiály, které mají stejnou krystalickou strukturu a podobné mřížkové konstanty
Abrazivní opotřebení
K abrazivnímu opotřebení dochází mezi dvěma pevnými předměty, kdy výstupky na tvrdším materiálu mechanicky odřezávají měkčí materiál. K charakteristickým rysům patří poměrně dobré mazací podmínky a nízký stupeň adheze, jakož i větší míra opotřebení ve srovnání s jinými způsoby opotřebení.
Únavové opotřebení
K únavovému opotřebení dochází, když valivé tření převládá nad třením kluzným, například na valivém povrchu ložiska nebo na povrchu zubu ozubeného kola. Proces vedoucí k únavovému tření je znázorněn níže.
- (1) Opakované namáhání působí na povrch v místech, kde se kovové části vzájemně dotýkají.
- (2) Toto opakované namáhání způsobuje postupné ztvrdnutí povrchu.
- (3) Vznikají jemné trhliny, které postupují a vytvářejí větší trhliny.
- (4) Povrchová vrstva se odlupuje.
Střihové napětí, které způsobuje jemné praskání v bodě (3), je největší v bodě mírně uvnitř od povrchu. Stejný proces jako výše má za následek také vznik prohlubně, kdy se vytváří na povrchu ložiska v důsledku únavy odvalováním důlky ve tvaru skvrn, a také odlupování, kdy dochází k odpadávání značně velkých úlomků kovu z povrchu zubu v důsledku únavy materiálu.
Opotřebení otěrem
Opotřebení otěrem je opotřebení, ke kterému dochází na styčné ploše mezi materiály, které byly navrženy na základě předpokladu, že nedojde k prokluzu. Při opakovaném namáhání dílů upevněných šrouby a maticemi (nebo styčných ploch dvou dílů) dochází k mírnému relativnímu prokluzování (otěru), které způsobuje opotřebení. Na povrchu, kde dochází k opotřebení, vznikají jemné trhliny. Protože vnější zatížení a opakované namáhání působí na místo opotřebení vrypy, sníží se únavová pevnost na polovinu nebo méně původní úrovně (únava vrypy), což vede k únavovému lomu.
Nutnost měření opotřebení
Opotřebení obráběcích nástrojů přímo souvisí s kvalitou obrábění a opotřebení součástí přímo souvisí s přesností a bezpečností provozu. Z tohoto důvodu je nesmírně důležité měřit podmínky opotřebení, například míru opotřebení. V této části vysvětlíme význam měření opotřebení na příkladu brzdového obložení a bitu řezného nástroje.
Měření opotřebení brzdových destiček
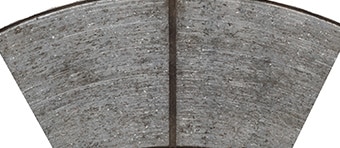
Tloušťka nové brzdové destičky automobilu je přibližně 10 mm. Ačkoli se načasování liší v závislosti na výrobci, obecně se brzdová destička vyměňuje, když je opotřebená na přibližně 1 až 3 mm. Brzdová destička se opotřebovává třením o rotor kotoučové brzdy v případě kotoučové brzdy nebo třením o brzdový buben v případě bubnové brzdy. Opotřebovává se také rotor kotouče a brzdový buben. Protože se stav opotřebení projevuje na opotřebovaném povrchu brzdového obložení, lze životnost brzdového obložení a typ opotřebení, k němuž dochází při brzdění, zjistit měřením nebo pozorováním objemu brzdového obložení a míry opotřebení.
Měření opotřebení bitů nástrojů
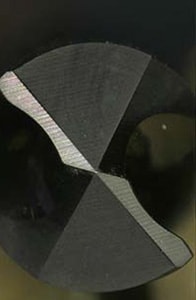
Špička frézy nebo bitu se opotřebovává v důsledku tření o obrobek a řezné třísky. Části, které se opotřebovávají, se liší v závislosti na materiálu; ve většině případů však dochází k opotřebení na hřebenové a odlehčovací ploše. Možnou příčinou je příliš vysoká řezná rychlost nebo nevhodný materiál bitu. Protože při obrábění obtížně řezatelného materiálu dochází k většímu zatížení břitů, je opotřebení větší než při obrábění běžných materiálů. Je třeba dbát zvýšené opatrnosti, protože tření o reliéfní povrch může zvýšit řeznou sílu nebo změnit hloubku řezu.
Z těchto důvodů je měření opotřebení břitů velmi důležité pro vyhodnocení řezné rychlosti a pro výběr materiálu břitů.
Problémy při konvenčním měření opotřebení
Míra opotřebení se obvykle měří pomocí systémů pro měření profilů nebo souřadnicových měřicích strojů. Při měření opotřebení na velké ploše nebo u malých dílů však tyto metody narážejí na následující problémy.
Problémy při měření opotřebení pomocí systému pro měření profilů
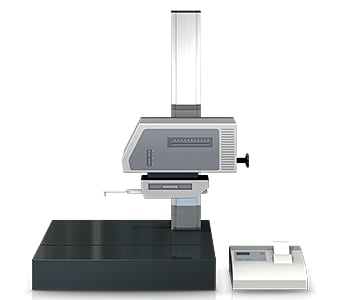
Systém pro měření profilů měří a zaznamenává profil cíle sledováním jeho povrchu pomocí stylusu. V posledních letech byly vyvinuty systémy pro měření profilů, které místo stylusu používají k měření složitých tvarů bezkontaktním trasováním profilu laser. Některé modely jsou dokonce schopny měřit horní i spodní povrch.
Systém měření profilu musí sledovat přesnou měřicí linii pro velikost opotřebení, které je cílem měření.
To zahrnuje následující problémy.
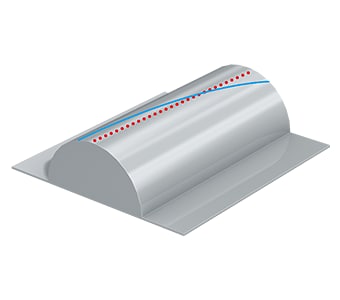
- Měření vyžaduje mnoho času, včetně času na upevnění vzorku na přípravek a jeho vyrovnání. K přesnému vyrovnání cíle jsou rovněž zapotřebí znalosti a dovednosti související s používáním systémů pro měření profilů.
- Stylus systému pro měření profilů se pohybuje nahoru a dolů v oblouku se středem v opěrném bodě ramene stylusu; hrot stylusu se pohybuje také ve směru osy X, což způsobuje chybu v údajích v ose X.
- Obkreslení požadované čáry pomocí stylusu je nesmírně obtížná práce a i malé posunutí stylusu způsobuje chyby v naměřených hodnotách.
- Zvýšení počtu cílů je složité i z důvodu nutnosti přesně určit konkrétní místa měření.
- Měřit lze pouze část cíle a vyhodnocení celého povrchu není možné.
Problémy při měření na souřadnicovém měřicím stroji
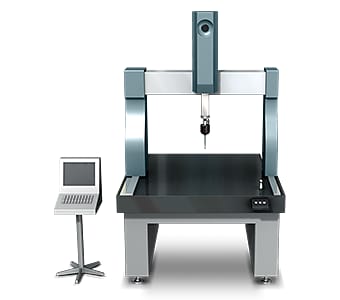
Pokud je plocha opotřebovaného dílu malá, například 1 mm2, je velmi obtížné přesně změřit tvar pomocí přesného zaměření povrchu sondou a vytvoření virtuálního povrchu. Kvůli malému počtu měřicích bodů je při měření malé plochy také obtížné určit přesný 3D tvar. Mnoho práce je navíc spojeno se souvisejícími úkoly, jako je tabulkové zpracování naměřených údajů a porovnání výsledků s výkresy.
Řešení problémů při měření opotřebení
Běžné měřicí přístroje měří trojrozměrný cíl nebo plochu pomocí bodového a liniového kontaktu. To způsobuje problémy, protože uživatelé nemohou identifikovat celý tvar a spolehlivost naměřených hodnot je nízká. Pro řešení těchto problémů s měřením vyvinula společnost KEYENCE optický 3D profilometr řady VR.
Řada VR přesně zachycuje 3D tvar celého povrchu cíle, aniž by došlo ke kontaktu s ním. Měří také 3D tvar pomocí 3D skenování cíle na podložce, a to již za jednu sekundu a s vysokou přesností. Dokáže provádět okamžité a kvantitativní měření bez chyb ve výsledcích měření. V této části jsou představeny některé konkrétní výhody řady VR.
Výhoda 1: Shromáždění dat z 800 000 měřicích bodů za pouhou jednu sekundu.
Řada VR měří celý tvar povrchu a shromažďuje data ze skupiny 800 000 bodů. Protože se měření neprovádí pomocí čar nebo bodů, není nutné opakovat měření, což zkracuje dobu měření. Obtížně definovatelné položky, jako je například míra opotřebení, lze vyhodnotit na základě objemu nebo plochy. Je také možné snadno provádět kvantitativní hodnocení rovinnosti. Řada VR dokáže měřit také profily na konkrétních místech. I po měření lze z dat 3D skenu získat profily různých dílů, aniž by bylo nutné znovu skenovat cíl.
Všechna naměřená data se ukládají a uložená data lze porovnávat s jinými daty nebo s daty 3D návrhu.
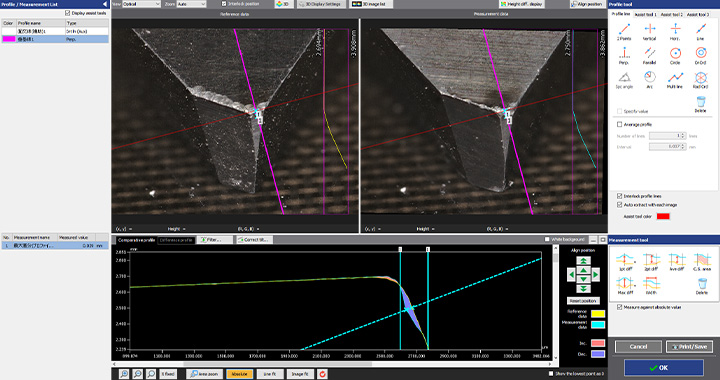
Výhoda 2: Možnost měření plochy široké až 300 mm × 150 mm.
Měření lze provádět jednoduše umístěním cíle na podložku a stisknutím tlačítka. Přesné polohování ani jiná příprava nejsou nutné. To umožňuje provádění vysoce přesných měření i operátorům, kteří nemají znalosti nebo zkušenosti s měřicími přístroji.
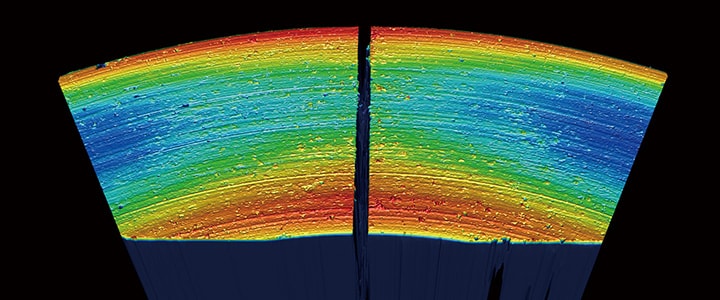
Vzhledem k tomu, že řada VR získává vlastnosti cíle na podložce a automaticky koriguje jeho polohu, není nutné přísné určování polohy, které by vyžadovalo mnoho času a úsilí. Řada VR může také měřit oblast širokou až 300 mm × 150 mm spojením několika měřicích snímků. Díky tomu může měření snadno a okamžitě provádět i nezkušený operátor a není nutné, aby se měřením zabýval specializovaný operátor.
Pomocí řady VR lze přesně změřit velkou plochu, například velkou brzdovou destičku, pouhým umístěním cíle na podložku a stisknutím tlačítka.
Shrnutí: Dramatické zlepšení a vyšší efektivita při obtížném měření opotřebení
Řada VR dokáže přesně a okamžitě měřit 3D tvary cílů pomocí vysokorychlostního 3D skenování bez kontaktu s cílem. Řeší všechny problémy, se kterými se potýkají konvenční měřicí přístroje, protože umožňuje měření nejvyššího a nejnižšího bodu na opotřebovaném povrchu, jakož i měření objemu, plochy průřezu a poměru plochy povrchu k ploše průřezu.
- Dokáže současně přesně měřit nejvyšší bod, nejnižší bod, plochu, objem a povrch.
- Tím se eliminují odchylky způsobené lidským faktorem, což umožňuje skutečné kvantitativní měření.
- Bez nutnosti polohování nebo jiné přípravy lze měření provést pouhým umístěním cíle na podložku a stisknutím tlačítka. Díky tomu není pro měřicí práce nutné přidělovat specializovanou obsluhu.
- 3D tvary lze měřit snadno vysokou rychlostí a s vysokou přesností. To umožňuje měřit velký počet cílů v krátkém čase, což přispívá ke zlepšení kvality.
Tento systém také umožňuje porovnání s minulými daty 3D tvarů, daty CAD a snadnou analýzu dat, například rozložení v rámci tolerancí. Lze jej efektivně využít pro širokou škálu účelů včetně vývoje produktů, analýzy výrobních trendů a kontroly vzorků.