Kivezetések emelkedésének gyors és pontos mérése félvezető burkolatokban
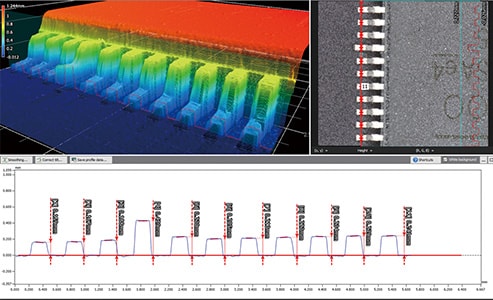
Az autókommunikáció és az elektronikus vezérlés térnyerésével, valamint a kisebb és vékonyabb méretű eszközök, például okostelefonok, táblagépek és hordható eszközök iránti kereslet növekedésével folyamatosan nő az igény a kiemelkedő szerelési minőség és megbízhatóság iránt. Különös figyelmet kell fordítani a félvezető-tokozások (kivezetőkeret-tokozások) tűire, mivel a tűk felemelése csatlakozási hibához és a csatlakozási szilárdság csökkenéséhez vezethet.
Ez a rész ismerteti a kivezetőkeretekkel és a kivezetőemeléssel kapcsolatos alapvető ismereteket, a kivezetőemelés hagyományos mérésének problémáit, valamint azt a legújabb mérési módszert, amely nemcsak ezeket a problémákat oldja meg, hanem jelentősen javítja a munka hatékonyságát és pontosságát is.
- Kivezetőkeretek (kivezetők)
- Kivezetőkeretek anyagai, feldolgozása és alkalmazásai
- Kivezetésemelés, csatlakozási hibák és egyéb felületi szerelési problémák
- Problémák a kivezetésemelés hagyományos mérésében
- Megoldás a kivezetőemelés mérésével kapcsolatos problémákra
- Összegzés
Kivezetőkeretek (kivezetők)
A kivezetőkeret egy olyan alkatrész, amely támogatja és rögzíti a félvezető chipet (félvezető elemet) egy félvezető tokozásban, például integrált áramkörben (IC) vagy nagy integráltságú (LSI) áramkörben. Külső kivezetőkön keresztül csatlakozik a külső vezetékekhez, amelyek a tokozásból a százlábú lábaihoz hasonló módon kiálló, több külső csatlakozókapcsok.
Az ilyen típusú kész félvezető tokozatot kivezetőkeret-tokozatnak, a gyantából kiálló külső kivezetőket pedig egyszerűen kivezetésnek nevezzük. A következő ábrákon a kivezetőkeret egyes részeinek elnevezése és a félvezetőtok belső felépítése látható.
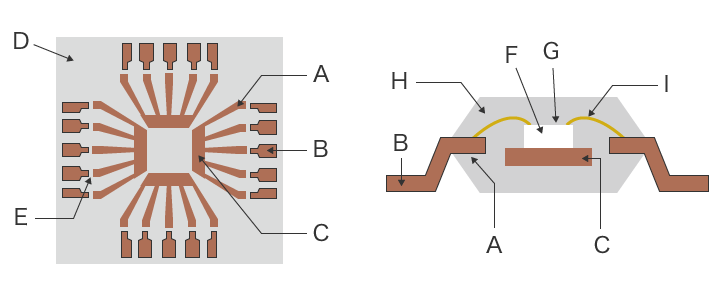
- A
- Belső vezeték
- B
- Külső vezeték
- C
- Szerszámlap
- D
- Keret
- E
- Elzáró rúd
- F
- Félvezető chip (félvezető elem)
- G
- Elektródalap
- H
- Gyantatokozat
- I
- Kötőhuzal
Kivezetőkeretek anyagai, feldolgozása és alkalmazásai
A kivezetőkeretek általában vékony réz (Cu) ötvözetből, vas (Fe) ötvözetből vagy hasonló anyagokból készülő lapok, amelyek kiváló tulajdonságokkal rendelkeznek, beleértve az elektromos vezetőképességet, a mechanikai szilárdságot, a hővezető képességet és a korrózióállóságot.
A progresszív precíziós préselés (lyukasztás, húzás és hajlítás) ennek a vékony lemeznek egy hosszú csíkjával történik. Egy sor folyamat eredményeként létrejönnek a szerszámlapok, amelyek támogatják és rögzítik a félvezető chipeket (félvezető elemeket), a belső vezetékeket (amelyek a félvezető elemekhez csatlakoznak), a külső vezetékeket (amelyek a külső vezetékekhez csatlakoznak) és egyéb szükséges alkatrészeket. A kivezetőkeret gyártási folyamata a megmunkálási folyamatokon kívül maratást, bevonást és egyéb felületkezelési eljárásokat is magában foglal.
A kiemelőkereteket nem csak az IC és LSI áramkörök tokozásaiban használják, hanem diszkrét félvezetőkhöz, fotocsatolókhoz, LED-ekhez és egyéb alkatrészekhez is. Az összes fenti komponensben huzalkötést használnak a félvezető elemek elektródáinak és a belső vezetékek összekapcsolására.
Kivezetésemelés, csatlakozási hibák és egyéb felületi szerelési problémák
Az utóbbi években az egyre kisebb méretű, szerelt elektronikus eszközök és az elektronikus áramkörök egyre nagyobb sűrűsége miatt a kivezetőkeretek és csatlakozásaik esetében még nagyobb pontosságra van szükség. A felületi szerelés során a külső vezetékek méret- és alakhibái, ill. egysíkúsági hibái a szerelés során problémákat okozhatnak. A felületre szerelt eszközök (SMD-k) kivezetőemelése számos tényező eredményeként fordulhat elő, beleértve a forrasztópaszta nem megfelelő terülését (alacsony nedvesíthetőségét), amit a kivezető felületének nem megfelelő kezelése vagy az elégtelen újraömlesztési melegítés, a nem megfelelő újraömlesztési körülmények miatti elégtelen forrasztóanyag-olvadás és a NYÁK vetemedése okoz. Ez az emelkedés csatlakozási hibákat és a csatlakozási szilárdság csökkenését eredményezheti.
Az alábbiakban ismertetjük a kivezetőemelés és egyéb tipikus szerelési hibák lehetséges okait, valamint példákat mutatunk be az ezekhez kapcsolódó ellenintézkedésekre.
Kivezetőemelés (alkatrész nem megfelelő illeszkedése)
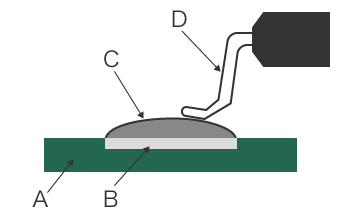
- A
- NYÁK
- B
- Szerelőlap
- C
- Forrasztóanyag
- D
- Kivezető (rész) emelése
- Probléma: A külső vezetékek és az egyéb elektronikus alkatrészek kivezetései forrasztatlanok maradnak, és felemelkednek.
- Okok: A forrasztópaszta nyomatának vagy részeinek hibás elhelyezkedése, egyenetlen mennyiségű nyomtatott forrasztópaszta, egyenetlen olvadási idő, kivezetések vagy egyéb érintkezők deformálódása és elégtelen szerelési nyomás
- Ellenintézkedések: Javítsa ki a pozíciókat, csökkentse a folyatószer mennyiségét, ellenőrizze és igazítsa be a kivezetők és egyéb csatlakozók alakját, valamint ellenőrizze a nyomtatási és újraömlesztési körülményeket.
A forraszanyag elégtelen olvadása
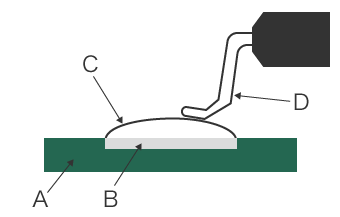
- A
- NYÁK
- B
- Szerelőlap
- C
- Maradék forrasztópor
- D
- Kivezetések emelkedése
- Probléma: A forrasztóanyag nem olvad meg teljesen, és forrasztópor marad vissza. Ez olyan problémákat eredményez, mint a szerelt alkatrészek csökkent csatlakozási szilárdsága és a kivezetések felemelkedése.
- Okok: Nem megfelelő újraömlesztési körülmények, megromlott forrasztópaszta
- Ellenintézkedések: Ellenőrizze az újraömlesztési körülményeket, és ellenőrizze vagy módosítsa a forrasztópaszta tárolási módját.
Nincs forrasztás
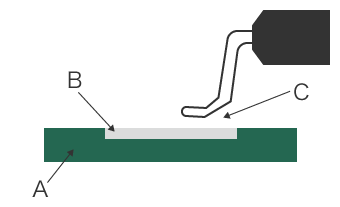
- A
- NYÁK
- B
- Szerelőlap
- C
- Nem elegendő vagy hiányzó forrasztás (vezetékcsatlakozási hiba)
- Probléma: A rögzítőlapon nincs forrasztóanyag, vagy a forrasztóanyag mennyisége rendkívül kevés.
- Okok: Nem elegendő mennyiségű nyomtatott forrasztópaszta, nem megfelelő nedvesíthetőség a rögzítőlapok és -vezetékek felületi körülményei vagy a megromlott forrasztópaszta miatt, valamint az elégtelen újraömlesztési hevítés
- Ellenintézkedések: Ellenőrizze a szerelőlap és a kivezetés felületeinek, a nyomtatómaszkok és a forrasztópaszta állapotát. Ellenőrizze az újraömlesztési körülményeket.
A forrasztópaszta elégtelen terülése
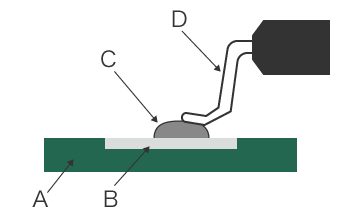
- A
- NYÁK
- B
- Szerelőlap
- C
- Forrasztóanyag (elégtelen terülés)
- D
- Kivezető
- Probléma: A forrasztóanyag nem terül el kellőképpen a szerelőlapokon és a kivezetéseken, ami csökkenti a csatlakozási szilárdságot és a kivezető felemelkedését.
- Okok: Nem elegendő mennyiségű a nyomtatott forrasztópaszta, elromlott szerelőlapok, kivezetők vagy forrasztópaszta, vagy nem elegendő újraömlesztési hevítés
- Ellenintézkedések: Ellenőrizze a szerelőlap és a kivezetés felületeinek, a nyomtatómaszkok és a forrasztópaszta állapotát. Ellenőrizze az újraömlesztési körülményeket.
Egyenetlen mennyiségű forrasztóanyag
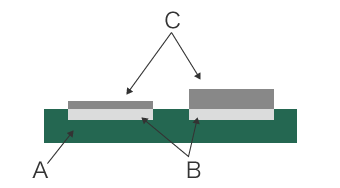
- A
- NYÁK
- B
- Szerelőlap
- C
- Forrasztóanyag (egyenetlen mennyiség vagy magasság)
- Probléma: A forrasztóanyag mennyisége a forrasztott részeknél nem állandó. Ez a kivezető emelkedéséhez és csatlakozási hibákhoz vezet.
- Okok: Forrasztópaszta alacsony nyomtathatósága (szitanyomásra alkalmas) vagy nem megfelelő nyomtatási körülmények
- Ellenintézkedés: Ellenőrizze a forrasztópasztát és a nyomtatási körülményeket.
Problémák a kivezetésemelés hagyományos mérésében
Nem könnyű ellenőrizni a csatlakozási körülményeket az egyes szerelt félvezető-tokozáson található számos kivezetés esetében. A körülmények ellenőrzésére szolgáló mérés még nehezebb a kisebb elektronikus alkatrészek és komponensek, valamint a sűrűn szerelt NYÁK lapok esetében.
A hagyományos magasságmérővel vagy koordinált mérőgéppel (CMM) végzett mérés a következő problémákkal jár.
Problémák a kivezetésemelés magasságmérővel történő mérésénél
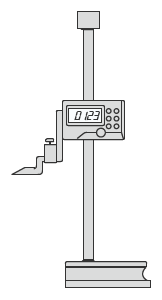
A magasságmérő mérőórával kombinálva használható a magasság mérésére.
Mivel csak pontokat lehet mérni, a pontosság növelése érdekében sok időt kell ráfordítani és sok ponton kell mérést végezni. De még ha rá is szánjuk a sok időt, és sok ponton végzünk is mérést, akkor sem lehet meghatározni a teljes felület állapotát.
A NYÁK-ra sűrűn szerelt félvezető eszközök kivezetéseinél néha nehézkes az érintkezés mérése rendkívül kis részeken és keskeny szakaszokon. A mérési eredmények különböző kezelők közötti eltérése és a mérőműszer hibája szintén lehetetlenné teszi a stabil mérést.
Problémák a kivezetésemelés koordinátamérő géppel történő mérésénél
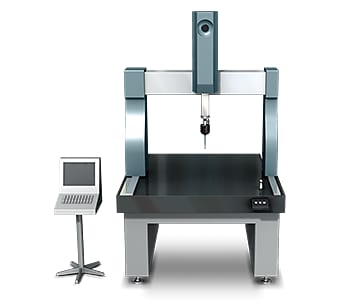
Koordinált mérőgéppel történő méréskor a szonda hegyét a mérési célfelület több pontjához hozzá kell érinteni.
Azonban a NYÁK vagy az alkatrészek a szonda mérési nyomása által okozott enyhe meghajlása is eltérést okozhat a mért értékekben.
Ezen túlmenően, mivel egy félvezető tokozásban a kivezetések helye kicsi, ezért előzetesen precíziós programot kell készíteni a mérőgép számára. Egyes kivezetések a csatlakozás mérete vagy helyzete miatt nem is mérhetők.
Megoldás a kivezetőemelés mérésével kapcsolatos problémákra
A szokásosan használt, érintkezős típusú mérőműszerekkel sok ideig tart a mérés, mivel pontérintkező segítségével háromdimenziós célokat és területeket mérnek. De akkor ott van még az emberi tényező okozta eltérések miatti alacsony mérési érték megbízhatóságának problémája, valamint a számokból és egyéb utófeldolgozásokból származó, használható adatok létrehozásának nehézsége is.
Ezen mérési problémák megoldására fejlesztette ki a KEYENCE a 3D optikai profilmérő VR sorozatát.
A VR sorozat pontosan rögzíti a teljes célfelület 3D alakját anélkül, hogy érintkezne a céltárggyal. A tárgyasztalon lévő céltárgy 3D szkennelése akár egy másodperc alatt is elvégezhető a 3D alakzat nagy pontosságú mérése érdekében. Képes azonnali és mennyiségi mérés elvégzésére, hiba nélkül a mérési eredményekben. Ez a szakasz a VR sorozat néhány specifikus előnyét mutatja be.
1. előny: A mérés akár egy másodperc alatt is elvégezhető. A teljes célfelület 3D alakja egyetlen méréssel pontosan rögzíthető.
A VR sorozat mindössze egy másodperc alatt feltárja a területadatokat (800.000 pontról egy szkennelés alatt), ami drámaian csökkenti a nagyszámú pont méréséhez szükséges időt. A 3D-s alakzat pontos mérését és gyors értékelését teszi lehetővé a teljes célponton.
A több kivezetőmagasság különbségei megjeleníthetők egy színes térképen, amellyel egy szempillantás alatt azonosítani lehet, hogy mely kivezetők emelkedtek fel, és mekkora felemelkedésre került sor. A szkennelés befejezése után bármely alkatrész profilmérése egy későbbi időpontban is elvégezhető, és ezáltal azonosíthatók a részletes körülmények.
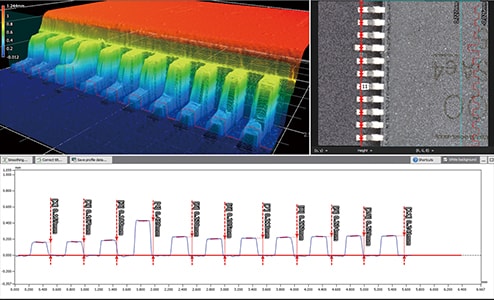
2. előny: Képes kis célpontok kvantitatív mérésére egyszerűen.
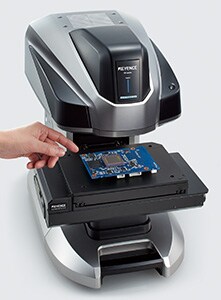
Az alacsony nagyítású és a nagy nagyítású kamerák közötti váltással a teljes forma vagy a részletek pontos 3D-s pásztázása még olyan kis célpontok esetében is elvégezhető, mint például a félvezető eszközök vezetékei.
A 3D alakmérés egyszerűen elvégezhető a céltárgy tárgyasztalra helyezésével és egy gomb megnyomásával. Mivel a céljellemzők adatai alapján lehetséges az automatikus helyzetbeállítás, nincs szükség szigorú pozicionálásra. Ez lehetővé teszi az emberi tényezők okozta eltérések nélküli kvantitatív mérést, függetlenül a kezelő tapasztalatainak és ismereteinek szintjétől; ezáltal nőhet az adott időn belül mérhető minták száma.
A beállításhoz ez a sorozat az iparág első intelligens mérési funkcióját használja, amely automatikusan konfigurálja a mérési tartományt és mozgatja a tárgyasztalt. Ez kiküszöböli a mérési hossz, a Z-tartomány és egyéb funkciók beállításához szükséges munkát.
Összegzés
A VR sorozat nagy sebességű, érintésmentes 3D-s szkennelés segítségével pontosan és azonnal meg tudja mérni a teljes felület 3D-s alakját, hogy azonosítsa a kivezető-emelkedést, az egyes alkatrészek szerelési körülményeit és egyéb szükséges elemeket.
- A mérés akár egy másodperc alatt is elvégezhető. Több kivezető emelkedése (magassága) rögzíthető, mivel az adott felület azonosítható a színes térképen. Részletes adatok a kívánt keresztmetszet profilmérésével nyerhetők.
- A nagyítás váltásával lehetőség nyílik a kis és kényes szerelésű alkatrészek teljes alakjának vagy részletes részeinek nagy pontosságú és érintésmentes mérésére.
- Nincs szükség pozícionálásra. Nincs szükség tapasztalatra vagy ismeretekre. Csak helyezze a céltárgyat a tárgyasztalra, és a mérés elvégzéséhez nyomja meg a gombot.
- A 3D alakzat színes térképen jeleníthető meg. A vizuálisan könnyen érthető adatok megosztása lehetővé teszi a zökkenőmentes koordinálást és az ellenintézkedések megtételét.
- Több mérési adathalmaz könnyen és mennyiségileg összehasonlítható és elemezhető.
Ezáltal több mérési adathalmaz egymás mellett összehasonlítható. A beállításokat az összes adathalmazra egyszerre alkalmazva az elemzés elvégezhető. A VR sorozat segítségével rögzített 3D-s alakadatok megosztásával jelentősen csökkenthető a szükséges idő, és javítható a teljes folyamat hatékonysága, beleértve a mérést, a hibaelemzést és a hibaelhárítási intézkedéseket is.