Łatwy i dokładny pomiar elementów chipu
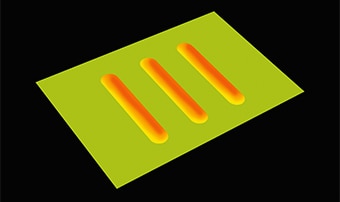
Najnowsze technologie montażu elementów na płytkach drukowanych uwzględniają coraz większą ich gęstość i wyższy stopień skomplikowania. Jest tak ze względu na zapotrzebowanie na mniejsze, lżejsze i cieńsze urządzenia, takie jak smartfony i elektronika domowa, a także z uwagi na zmniejszanie rozmiaru podzespołów elektronicznych, takich jak rezystory chipowe i kondensatory ceramiczne. W tej sekcji przedstawiono problemy mogące występować w zamontowanych elementach, a także sposób wykorzystywania systemów pomiarowych 3D do oceny i analizy tych problemów oraz zapobiegania ich występowaniu.
- Metoda montażu elementów chipu
- Co to jest lutowanie rozpływowe?
- Kontrola temperatury pieca rozpływowego
- Problemy z montażem powierzchniowym
- Przykładowy pomiar deformacji płytki drukowanej
- Przykładowy pomiar równoległości styków aluminiowego kondensatora elektrolitycznego
- Przykładowy pomiar grubości pasty lutowniczej
- Przykładowe pomiary grubości powłoki rezystancyjnej
- Przykładowy pomiar głębokości pęknięć w powłokach
- Pomiar szerokości dielektrycznej
Metoda montażu elementów chipu
Lutowanie rozpływowe spopularyzowało się wraz z miniaturyzacją elementów elektronicznych i większą gęstością ich montażu na płytkach drukowanych.
Metoda lutowania | Charakterystyka | |
---|---|---|
Zalety | Wady | |
Lutownica |
Niskie naprężenia termiczne |
Duże wahania temperatury |
Gorące powietrze |
Niskie naprężenia termiczne |
Duże wahania temperatury |
Laser |
|
Nie nadaje się do masowej produkcji (długi czas przetwarzania) |
Ciepło impulsowe |
|
Nie nadaje się do masowej produkcji (długi czas przetwarzania) |
Rozpływ (typ — podczerwień) |
|
|
Rozpływ (typ — gorące powietrze) |
|
|
Lutowanie falowe |
|
|
Co to jest lutowanie rozpływowe?
Pasta lutownicza, która jest jednolitą mieszaniną sproszkowanego lutu i topnika, nakładana jest na metalową płytkę z wyciętymi otworami i rozprowadzana cienką warstwą za pomocą szpatułki w celu wykonania nadruku. Elementy są następnie montowane na płytce drukowanej, podgrzewane i lutowane.
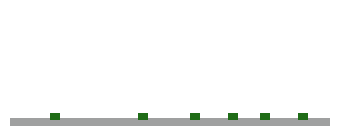
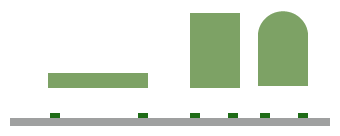
Jeśli liczba elementów jest niewielka, możliwe jest również ręczne ich zamontowanie.
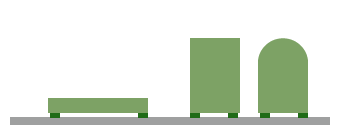
Temperaturę reguluje się w pięciu krokach (patrz sekcja poniżej).
Kontrola temperatury pieca rozpływowego
Zwykle ciepło stosuje się dwuetapowo. W pierwszym etapie nagrzewania płytka drukowana jest doprowadzana i utrzymywana w jednolitej temperaturze. W drugim etapie podgrzewania pasta lutownicza się topi. Temperatura i czas nagrzewania zależą od typu pieca rozpływowego i używanych elementów.
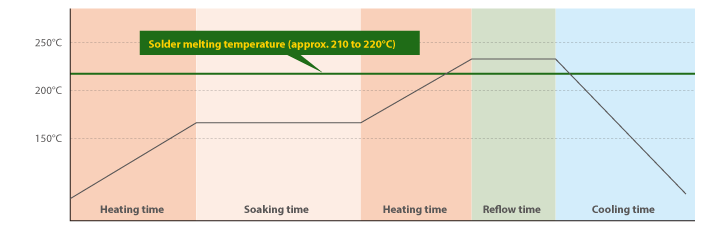
Problemy z montażem powierzchniowym
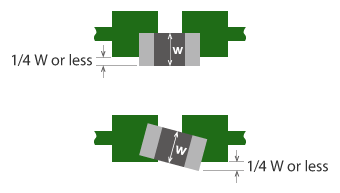
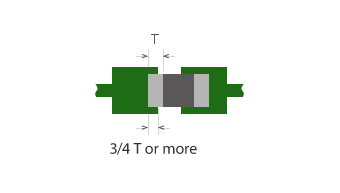
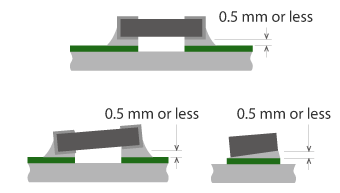
Przykładowy pomiar deformacji płytki drukowanej
Deformacja płytki drukowanej spowodowane jest zmianami temperatury występującymi podczas zasilania lub zmianami środowiskowymi. Analizę przeprowadza się w celu określenia, czy w wyniku tych zmian temperatury wystąpiły defekty. Deformacja wskutek wahań temperatury można mierzyć w zakresie od temperatury pokojowej do 260°C.
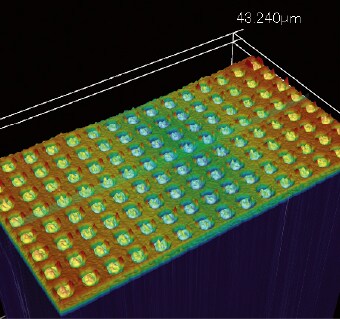
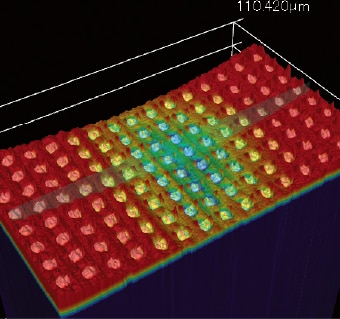
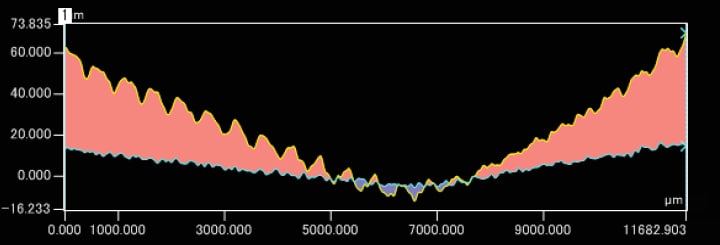
Przykładowy pomiar równoległości styków aluminiowego kondensatora elektrolitycznego
Można zmierzyć płaskość zacisków kondensatora, która może prowadzić do wad montażowych płytki drukowanej i wpływać na jej wytrzymałość montażową.
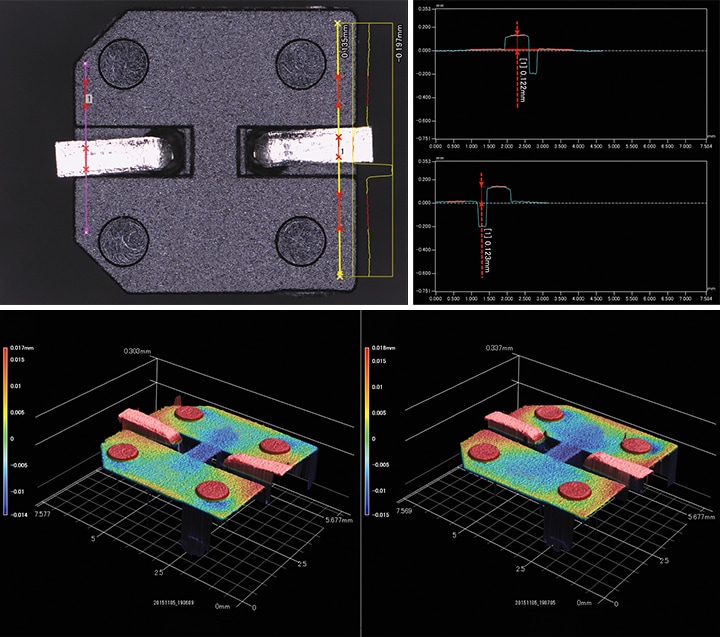
Przykładowy pomiar grubości pasty lutowniczej
Grubość warstwy lutu nałożonej na płytkę drukowaną można zmierzyć.
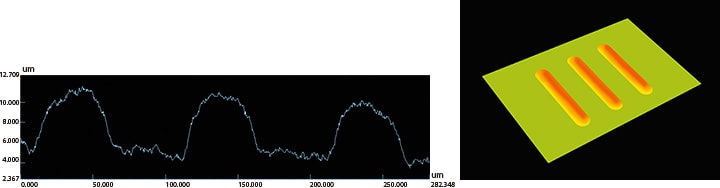
Przykładowe pomiary grubości powłoki rezystancyjnej
Grubość i objętość powłoki rezystancyjnej w stanie mokrym można zmierzyć przed spiekaniem po nadruku powłoki.
Grubość powłoki można zmierzyć, gdy jest mokra, co pozwala skutecznie ustawić warunki procesu spiekania.
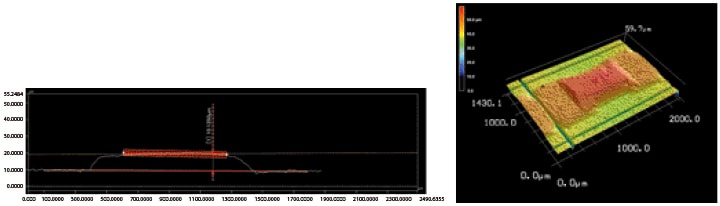
Struktura rezystora chipowego
Rezystory chipowe to małe, kwadratowe stałe oporniki składające się z elementu rezystancyjnego uformowanego na powierzchni podstawy izolacyjnej, np ceramicznej, z elektrodami na obu końcach. Nadają się głównie do montażu powierzchniowego.
Typowa struktura kwadratowego rezystora chipowego
- (1) Brak przewodu na elektrodach styków
- (2) Możliwość lutowania lub klejenia
* Dostępne są również rezystory typu MELF o cylindrycznych kształtach, lecz nie są one powszechnie stosowane.
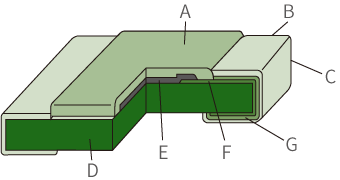
- A
- Powłoka ochronna
- B
- Poszycie zewnętrzne
- C
- Elektroda styku
- D
- Ceramika
- E
- Powłoka rezystancyjna
- F
- Elektroda wewnętrzna
- G
- Poszycie niklowe
- Ceramika (podstawa)
- Podstawa wykonana jest z płyty ceramicznej, aby wytrzymać spiekanie lub przycinanie elementu rezystancyjnego.
- Element rezystancyjny
- Istnieją typy grubo- i cienkowarstwowe.
- Elektroda
- Element rezystancyjny połączony jest z elektrodami stykowymi za pośrednictwem elektrod wewnętrznych. Ma strukturę składającą się co najmniej z trzech warstw.
- Powłoka ochronna
- Powierzchnia elementu rezystancyjnego jest pokryta żywicą lub szkłem, aby zapobiec bezpośredniemu przyleganiu wilgoci lub kurzu.
Przykładowy pomiar głębokości pęknięć w powłokach
Długość i głębokość folii można zmierzyć, aby się upewnić, że rezystory chipowe pozostają zgodne ze specyfikacją.
Można również zmierzyć szerokość i głębokość pęknięć występujących w przyciętych obszarach.
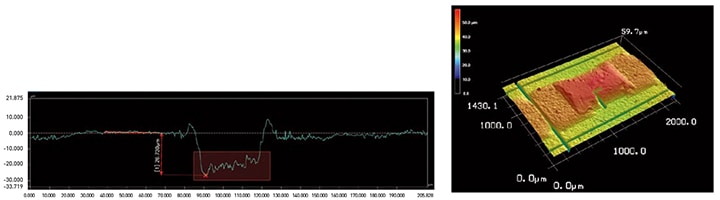
Przycinanie laserowe
Warstwy rezystora chipowego formuje się metodą sitodruku. Ponieważ na ceramicznym podłożu formowanych jest kilkaset elementów rezystancyjnych, nawet niewielkie zmiany w warunkach drukowania powodują bezpośrednie zmiany rezystancji.
Jeśli oporność rezystorów chipowych jest różna, ich charakterystyka elektryczna nie będzie zgodna z danymi znamionowymi. Prowadzi to do konieczności przycinania laserowego w celu dostosowania rezystancji. Przycinanie laserowe polega na mierzeniu elementów rezystancyjnych jeden po drugim i przycinaniu ich w celu zapewnienia określonej rezystancji i zminimalizowania różnic.
- (1) Elementy rezystancyjne są drukowane tak, aby uzyskać nieco niższą rezystancję niż docelowa.
- (2) Przycinanie elementu rezystancyjnego powoduje zwężenie jego ścieżki prądowej, co zwiększa rezystancję.
- (3) Przycinanie zatrzymuje się po osiągnięciu docelowej rezystancji, aby zminimalizować wahania między chipami.

- A
- Przepływ prądu elektrycznego
- B
- Przycinanie laserowe
- C
- Krótka długość przycinania powoduje niewielką zmianę rezystancji.
- D
- Duża długość przycinania powoduje dużą zmianę rezystancji.
* Gdy element jest dalej przycinany, ścieżka prądu w elemencie rezystancyjnym staje się węższa, co zwiększa rezystancję.
Ostateczna długość przycinania i kształt określa się na podstawie zmiany rezystancji podczas przycinania.
Porównując zmiany rezystancji w zależności od długości cięcia — między cięciem prostym a cięciem w kształcie litery L — cięcie L może zapewnić wyższą dokładność końcową i zmniejszyć końcowy wpływ mikropęknięć.
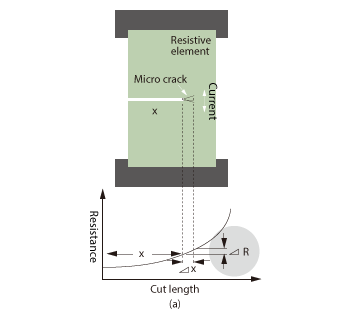
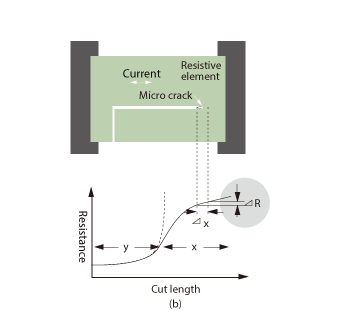
Pomiar szerokości dielektrycznej
Szerokość wzoru i grubość elementu dielektrycznego w stanie mokrym można zmierzyć.
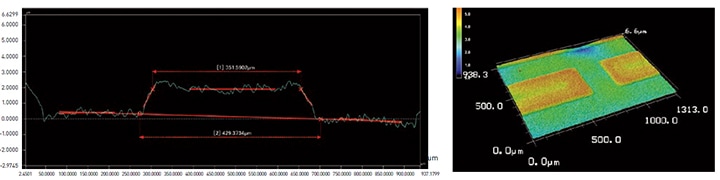
Struktura wielowarstwowego ceramicznego kondensatora chipowego
Podstawowa struktura kondensatora składa się z elementu dielektrycznego umieszczonego między dwiema płytkami elektrod.
- (1) Materiał dielektryczny, taki jak tytanian baru (BaTiO3) — dielektryk ceramiczny, nakładany jest na powłokę nośną.
- (2) Materiał suszy się w celu uzyskania cienkiego arkusza.
- (3) Na arkuszu drukowana jest pasta z materiału elektrodowego zawierającego metale takie jak pallad, srebro lub nikiel.
- (4) Arkusze układane są w stosy od 10 do 1000 warstw, tłoczone i cięte w chipy.
- (5) Ostatnim etapem tworzenia wielowarstwowych kondensatorów ceramicznych jest spiekanie i powlekanie zewnętrznych końcówek srebrem.
Chipy kurczą się około o 10% podczas spiekania ceramiki, co należy uwzględnić przy określaniu ich wymiarów.
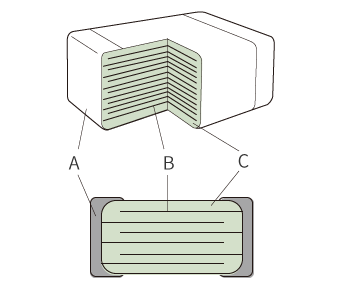
- A
- Elektroda zewnętrzna
- B
- Elektroda wewnętrzna
- C
- Dielektryk ceramiczny
Proporcjonalna zależność między pojemnością elektrostatyczną a powierzchnią płyty elektrody
Równoległe połączenie wielu kondensatorów jest równoznaczne ze zwiększeniem powierzchni elektrody, dzięki czemu można powiększyć pojemność elektrostatyczną przez zwiększenie liczby kondensatorów.
Wykorzystanie wielu kondensatorów wymaga dużo miejsca na płytce drukowanej, więc metoda ta jest nieodpowiednia, gdy wymagana jest jego oszczędność.
Aby tego uniknąć, wielowarstwowe ceramiczne kondensatory chipowe są miniaturyzowane oraz osiągają dużą pojemność dzięki wielowarstwowym strukturom dielektryków ceramicznych i wewnętrznym elektrodom układanym naprzemiennie.