Natychmiastowy i dokładny pomiar wysokości zadziorów na produktach formowanych z tworzyw sztucznych
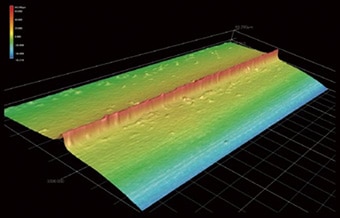
Zadziory to typowe wady kształtu występujące podczas formowania wtryskowego i innych sposobów kształtowania tworzyw sztucznych. Trudno jest zatrzymać maszyny do formowania w ściśle określonych odstępach czasu, więc gdy na dużej liczbie formowanych produktów powstają zadziory, ich usunięcie wiąże się ze znacznymi kosztami. Jeśli formowane produkty z zadziorami odrzucane są jako wadliwe, wydajność znacznie spadnie. Wywiera to dużą presję na marżę zysku. Z tych powodów konieczny jest dokładny pomiar kształtów i wymiarów zadziorów, aby jak najszybciej zidentyfikować przyczyny i zapobiec ich ponownemu wystąpieniu.
Zadziory powstające na formowanych produktach mają trójwymiarowe kształty, co utrudnia ich dokładny pomiar za pomocą konwencjonalnych metod pomiarowych. W tej sekcji przedstawiono podstawowe informacje na temat zadziorów z tworzyw sztucznych oraz najnowszą metodę pomiarową, która rozwiązuje problemy występujące podczas konwencjonalnych pomiarów.
- Zadziory na produktach formowanych z tworzyw sztucznych
- Metody gratowania produktów formowanych z tworzyw sztucznych
- Przyczyny powstawania zadziorów na produktach formowanych z tworzyw sztucznych i środki zaradcze
- Problemy z konwencjonalnym pomiarem wysokości i kształtu zadziorów
- Rozwiązanie problemów z pomiarem wysokości zadziorów
- Podsumowanie
Zadziory na produktach formowanych z tworzyw sztucznych
Zadziory są jednym z typowych rodzajów wad w formowaniu tworzyw sztucznych. Ta wada kształtu powstaje, gdy stopione tworzywo sztuczne wpływa do formy (wypukłej i wklęsłej) i zestala się na linii podziału lub w szczelinach wokół sworzni wypychających.
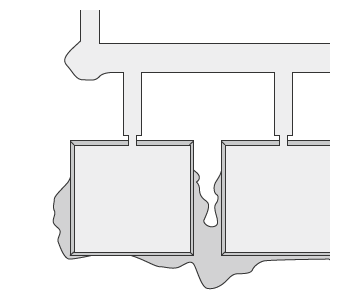
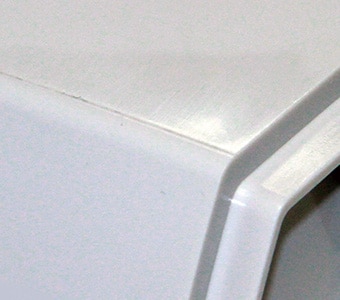
Ponieważ zadziory są niezamierzonymi występami na formowanym produkcie, mogą negatywnie wpływać na jego jakość. Mogą pogorszyć wygląd produktu, a także spowodować obrażenia, jeśli są ostre. Podczas formowania komponentów produktu zadziory na plastikowych częściach formowanych mogą zmniejszyć wydajność procesu montażu. Z tych powodów mogą być usuwane narzędziowo, gdy gratowanie jest możliwe i opłacalne.
Metody gratowania produktów formowanych z tworzyw sztucznych
Gratowanie przeprowadza się, gdy istnieje możliwość usunięcia zadziorów tworzących się na produktach formowanych z tworzyw sztucznych, a liczba poddawanych obróbce produktów jest niezbyt duża. Może być również konieczne, gdy występują na formowanych produktach otrzymanych z zagranicznych fabryk, a produkty te trzeba wykorzystać w celu dotrzymania terminu dostawy.
Gratowanie ręczne
Zadziory usuwa się ręcznie, gdy liczba obrabianych przedmiotów jest niewielka lub gdy zadziory znajdują się w miejscach, w których nie można ich usunąć za pomocą maszyn do automatycznego gratowania.
- Ręczne narzędzia do gratowania obejmują pilniki, frezy, ostrza i ściernice.
- Termoplastyczne zadziory usuwa się przez stopienie za pomocą lutownicy lub innego narzędzia (metodę tę można stosować gdy zadziory są cienkie, a formowany produkt jest gruby).
- Zadziory usuwa się po nadaniu im kruchości przez zamrożenie (metodę tę można stosować, gdy zadziory są cienkie, a formowany produkt jest gruby).
Inne metody, takie jak narzędzia szlifierskie i chemikalia, można stosować z uwzględnieniem formowanego materiału, jego właściwości i zadziorów, urabialności i innych czynników.
Gratowanie maszynowe
Gdy produkty formuje się w złożone kształty, występowanie zadziorów w niektórych miejscach może wymagać pewnego stopnia tolerancji ze względu na strukturę formy. Z drugiej strony, gdy kształty formowanych produktów są proste, usuwanie zadziorów za pomocą maszyny do automatycznego gratowania lub innej może być uwzględnione jako etap procesu formowania tworzyw sztucznych.
- Śrutownica: zadziory usuwa się przez skierowanie materiału do obróbki strumieniowo-ściernej tak, by zetknął się z formowanymi produktami w maszynie. Usunięte zadziory są automatycznie zbierane przez wbudowany odpylacz.
- Myjka wysokociśnieniowa: zadziory usuwa się przez skierowanie strumienia wody pod wysokim ciśnieniem na formowane produkty. Proces ten służy również do czyszczenia formowanych produktów.
- Nóż ultradźwiękowy: ostrze wibrujące z częstotliwością ultradźwiękową dotyka zadziorów i je usuwa. Ponieważ ostrze mikrowibracyjne styka się z termoplastycznym tworzywem sztucznym, które zostało zmiękczone przez ciepło z cząsteczek tworzywa sztucznego, możliwe jest usuwanie zadziorów bez wywierania znacznej siły na formowane produkty.
Istnieją również różne inne rodzaje maszyn do automatycznego gratowania. Typ maszyny wybiera się zgodnie z charakterystyką termoplastycznego tworzywa sztucznego, termoutwardzalnego tworzywa sztucznego lub innego tworzywa sztucznego używanego do formowania produktów, a także czynników takich jak rozmiar, kształt i trwałość formowanych produktów.
Identyfikacja kształtów i wymiarów umożliwia odpowiednie gratowanie
Aby wybrać metodę usuwania zadziorów i zdecydować się na odpowiednią maszynę do gratowania, należy uzyskać jak najwięcej informacji o zadziorach. Zadziory mają trójwymiarowe kształty nawet wtedy, gdy są cienkie. W wielu przypadkach utrudnia to dokładny pomiar ich wysokości i kształtów za pomocą konwencjonalnych przyrządów pomiarowych. Problemy z pomiarem zadziorów i ich rozwiązanie przedstawiono w dalszej części.
Przyczyny powstawania zadziorów na produktach formowanych z tworzyw sztucznych i środki zaradcze
Gdy zwiększa się liczba wadliwych produktów formowanych z tworzyw sztucznych ze względu na występowanie nieoczekiwanych zadziorów, trzeba przeznaczyć wiele roboczogodzin i duże koszty na gratowanie. Dlatego zdecydowanie najlepszym podejściem jest zapobieganie powstawaniu zadziorów i ulepszanie procesów, aby zapobiec ich ponownemu powstawaniu.
W tej sekcji przedstawiono przykłady typowych przyczyn powstawania zadziorów podczas formowania wtryskowego oraz środki zaradcze zapobiegające ich tworzeniu.
Przykładowe przyczyny powstawania zadziorów w procesie formowania wtryskowego
- Niskie ciśnienie zamykania formy w porównaniu z ciśnieniem wtrysku stopionego tworzywa sztucznego.
- Mniejsza dokładność linii podziału między formami (wypukłymi i wklęsłymi).
- Nadmierna płynność stopionego tworzywa sztucznego (potencjalnie spowodowana zbyt wysoką temperaturą formy lub stopionego tworzywa sztucznego).
- Szczeliny między formami spowodowane naprężeniem lub innymi czynnikami.
- Brak równowagi między ilością wtryskiwanego stopionego tworzywa sztucznego, siłą zamykania formy i ciśnieniem wtrysku.
- Brak równowagi między powierzchnią rzutowaną wewnątrz formy a siłą zamykania formy (siłą utrzymującą ciśnienie).
- Naprężona lub przechylona płyta matrycy we wtryskarce.
Zadziory mogą powstawać również z wielu innych przyczyn.
Przykładowe środki zaradcze zapobiegające powstawaniu zadziorów w formowaniu wtryskowym
- Zwiększenie ciśnienia zamknięcia formy lub zmniejszenie ciśnienia wtrysku tworzywa sztucznego.
- Wyregulowanie form w sposób zapewniający dokładne dopasowanie na linii podziału.
- Ulepszenie form za pomocą wkładek, spawania lub innych środków w celu wyeliminowania szczelin między formą wypukłą i wklęsłą.
- Zastosowanie docisku odpowiedniego do powierzchni rzutowanej formy i wyregulowanie go podczas sprawdzania równowagi z siłą zamykania formy.
- Temperatura formy może być wyższa niż ustawiona za pomocą sterownika. W takim przypadku należy dostosować ustawienie temperatury przy jednoczesnym pomiarze rzeczywistej temperatury formy.
- Gdy przepływ tworzywa sztucznego na wlocie formy jest słaby, nadmierne zwiększenie temperatury i płynności tworzywa sztucznego zwiększy prawdopodobieństwo jego wypłynięcia z linii podziału. W związku z tym należy sprawdzić i ulepszyć przewężenie formy z uwzględnieniem odpowiedniej temperatury tworzywa sztucznego.
Ponieważ dokładność formy i maszyny do formowania, ciśnienie zamknięcia formy, temperatura i ciśnienie formy i tworzywa sztucznego oraz inne czynniki są ze sobą powiązane, kluczem do skutecznych środków zaradczych jest kompleksowe sprawdzenie i skorygowanie tych czynników.
Środki zaradcze do rozważenia na podstawie kształtu zadziorów na wadliwych produktach
Zadziory występujące na formowanym produkcie mogą dostarczyć wskazówek dotyczących przyczyny. Oprócz wskazania problematycznych części formy wysokość i grubość zadziorów może wskazywać na rozmiar szczeliny linii podziału i płynność stopionego tworzywa sztucznego, a kąt stożka zadziorów może świadczyć o odkształceniu matrycy lub miejscowym spadku dokładności formy.
Dokładna identyfikacja położenia, kształtów i wymiarów zadziorów na wadliwych produktach pozwala uzyskać ważne informacje do wprowadzenia ulepszeń i zastosowania środków zapobiegających ich ponownemu wystąpieniu.
Problemy z konwencjonalnym pomiarem wysokości i kształtu zadziorów
Jak wspomniano w poprzedniej sekcji, dokładny pomiar kształtów i wymiarów zadziorów na produktach formowanych z tworzyw sztucznych może pomóc w identyfikacji położenia zadziorów i przyczyn ich powstawania, zapobieganiu nawrotom i decydowaniu o warunkach gratowania. Pomiar wysokości trójwymiarowych zadziorów za pomocą konwencjonalnych systemów pomiaru profilu lub mikroskopów wiąże się z poniższymi problemami.
Problemy z pomiarem wysokości i kształtu zadziorów za pomocą systemu pomiaru profilu
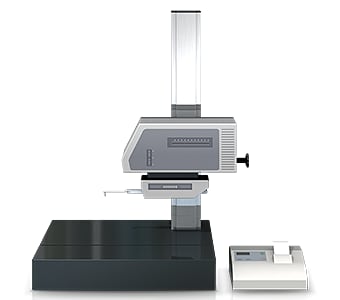
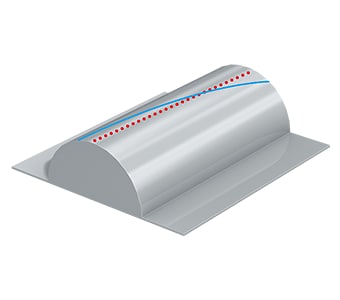
Pomiar wysokości zadziorów za pomocą systemu pomiaru profilu wiąże się z następującymi problemami:
- Prace pomiarowe wymagają dużo czasu, w tym na przymocowanie obiektu do jigu i wypoziomowanie. Wiedza i umiejętności związane z użytkowaniem systemów pomiaru profilu wymagane są również do dokładnego wypoziomowania obiektu.
- Podczas pomiaru zadziorów w zagłębieniach trudno jest namierzyć oczekiwane położenie pomiarowe za pomocą rysika. Nawet niewielkie jego przesunięcie powoduje zmianę mierzonych wartości.
- Trudno narysować linię profilu przechodzącą przez maksymalny punkt na cylindrycznym obiekcie.
- Rysik porusza się w górę i w dół po łuku wyśrodkowanym na punkcie podparcia ramienia, a końcówka porusza się również po osi X. Powoduje to błąd w danych osi X.
Problemy z pomiarem wysokości i kształtu zadziorów za pomocą mikroskopu
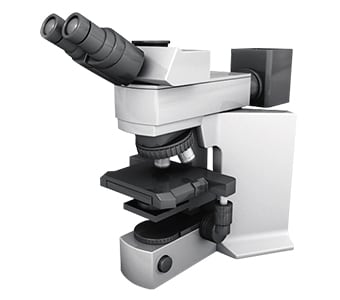
W przeciwieństwie do systemów pomiaru profilu mikroskopy umożliwiają rejestrację informacji o „powierzchni”. Szerokość rowka można zmierzyć przez określenie zakresu ruchu stolika urządzenia, a głębokość — przez określenie zakresu regulacji ostrości. Pomiar mikroskopem wiąże się jednak z poniższymi problemami.
- Gdy zadziory na produktach formowanych z tworzyw sztucznych obserwuje się w dużym powiększeniu, wąskie pole widzenia utrudnia identyfikację całego kształtu zadziorów.
- Pomiar zależy od ludzkich oczu, dlatego wyniki mogą się różnić w zależności od operatora.
- Ponieważ mikroskopy z założenia nie są przyrządami pomiarowymi, mogą nie być w stanie określić ilościowo wyników pomiarów lub zapewnić wiarygodnych wartości pomiarowych.
Rozwiązanie problemów z pomiarem wysokości zadziorów
Produkty formowane z tworzyw sztucznych i tworzące się na nich zadziory mają trójwymiarowe kształty, co utrudnia ich dokładne zmierzenie przy użyciu konwencjonalnych metod pomiarowych. Dużym problemem jest również fakt, że pomiar wymaga umiejętności, a także dużo czasu i pracy.
Aby rozwiązać te problemy z pomiarem wysokości zadziorów, firma KEYENCE opracowała optyczny profilograf 3D ze sterowaniem jednym przyciskiem serii VR.
Urządzenie serii VR dokładnie rejestruje kształt 3D całej powierzchni docelowej bez kontaktu z obiektem. Trójwymiarowe skanowanie obiektu na stoliku pomiarowym można wykonać w ciągu zaledwie sekundy, co zapewnia wysoką dokładność pomiaru kształtu 3D. Umożliwia natychmiastowy i ilościowy pomiar bez błędów w wynikach pomiaru. W tej sekcji przedstawiono kilka konkretnych zalet serii VR.
Korzyść nr 1: kompletny pomiar w zaledwie sekundę. Kształt 3D całej powierzchni docelowej można dokładnie uchwycić w ramach jednego pomiaru.
Urządzenie serii VR natychmiastowo rejestruje 800 000 punktów danych powierzchni podczas pojedynczego skanowania w ciągu zaledwie sekundy. Różne linie profilu, na przykład liniowe, równoległe i prostopadłe, mogą być również rysowane za pomocą prostych i intuicyjnych operacji w żądanych położeniach w precyzyjnych danych. Z uwagi na to, że możliwy jest również dokładny pomiar profilu, pozwala to uzyskać szczegółowe dane niezbędne do identyfikacji przyczyn powstawania zadziorów.
Nawet po zakończeniu pomiaru można wykonać pomiar profilu różnych części przy użyciu wcześniejszych danych skanowania 3D szerokiego obszaru bez konieczności ustawiania i ponownego skanowania obiektu
.Maksymalne i minimalne nierówności powierzchni (wysokość, głębokość) w pozyskanym kształcie 3D mogą być wyświetlane na kolorowej mapie, aby wyraźnie zwizualizować wadliwe obszary na całym obiekcie.
Co więcej, istnieje możliwość porównywania obok siebie danych pomiarowych z wielu obiektów oraz zastosowania oczekiwanych warunków do wielu zestawów danych jednocześnie. Znacznie zmniejsza to liczbę roboczogodzin i zwiększa wydajność pracy.
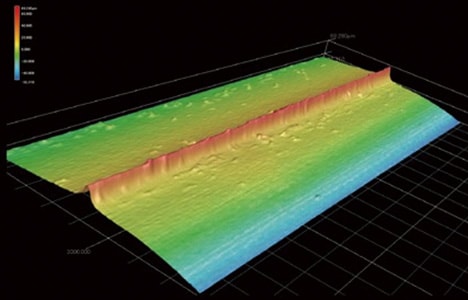
Korzyść nr 2: możliwość kontroli i pomiaru zadziorów na dużym obszarze.
Podczas kontroli zadziorów często trzeba określić ich maksymalną wysokość. Ponieważ położenie największego zadzioru różni się w przypadku poszczególnych obiektów, konieczne jest uzyskanie danych całego obszaru pomiarowego. Urządzenie serii VR umożliwia mierzenie szerokiego obszaru, pozwalając na szybki i dokładny pomiar wierzchołka zadziorów za pomocą prostej operacji.
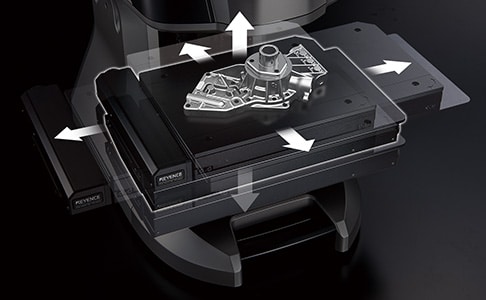
Pomiar kształtu 3D można łatwo wykonać, po prostu umieszczając obiekt na stoliku pomiarowym i naciskając przycisk. Ścisłe poziomowanie lub pozycjonowanie nie jest wymagane, ponieważ dostępna jest automatyczna regulacja położenia na podstawie danych cech obiektu. Seria ta zawiera również pierwszą w branży funkcję Smart Measurement, która automatycznie konfiguruje zakres pomiarowy i przesuwa stoli pomiarowy zgodnie z rozmiarem obiektu. Eliminuje to pracę wymaganą do ustawienia długości pomiaru i zakresu Z.
Szeroka gama narzędzi pomocniczych umożliwia prostą i intuicyjną konfigurację oczekiwanych warunków pomiarowych.
Oprócz łatwej konfiguracji narzędzia wspomagające umożliwiają prostą obsługę systemu nawet przez nowicjuszy, dzięki czemu operatorzy niezaznajomieni z pomiarami mogą uzyskać dokładny wynik w ciągu zaledwie sekundy. Nie licząc celów takich jak badania, rozwój i testy form, umożliwia to łatwe zwiększenie liczby próbek lub przeprowadzenie analizy trendów w celu pomiaru i kontroli podczas produkcji komercyjnej.
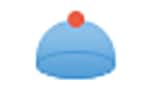
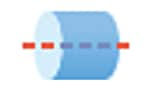
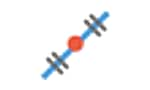
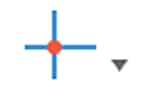
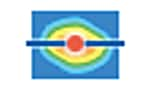
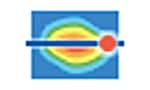
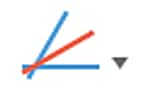
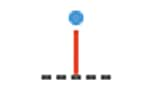
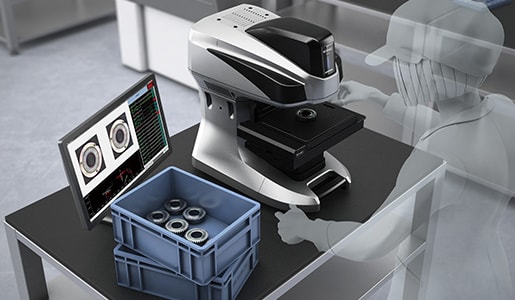
Podsumowanie
Urządzenie serii VR umożliwia dokładny i natychmiastowy pomiar trójwymiarowych kształtów obiektu przez szybkie bezkontaktowe skanowanie 3D. Oprócz pomiarów 3D całego produktu formowanego z tworzywa sztucznego urządzenie serii VR umożliwia wykonywanie w ciągu zaledwie sekundy trudnych pomiarów, takich jak mierzenie wysokości drobnych zadziorów i kształtów nieregularności powierzchni.
Korzystanie z serii VR rozwiązuje wszystkie problemy pomiarowe związane z konwencjonalnym pomiarem.
- Maksymalną wysokość i kształty zadziorów na dużym obszarze można zwizualizować na kolorowej mapie.
- Po zakończeniu skanowania można w dowolnym momencie wykonać pomiar profilu dowolnej części i porównać wiele zestawów danych.
- Aby wykonać pomiar, wystarczy umieścić obiekt na stoliku i nacisnąć przycisk. Nie jest potrzebne pozycjonowanie ani inne przygotowania. Eliminuje to konieczność przydzielania wyspecjalizowanego operatora do prac pomiarowych.
- W krótkim czasie można zmierzyć dużą ilość próbek, ponieważ kształty 3D mogą być łatwo mierzone przy dużych prędkościach i z wysoką dokładnością. Jest to przydatne do poprawy jakości.
- Eliminuje to zmienność wynikającą z czynnika ludzkiego, umożliwiając prawdziwy pomiar ilościowy.
System umożliwia porównywanie z danymi CAD i łatwą analizę danych, takich jak rozkład w granicach tolerancji. Oprócz badań, rozwoju i testów form może być skutecznie wykorzystywany w wielu różnych sytuacjach w miejscach pracy związanych z formowaniem tworzyw sztucznych, w tym podczas kontroli próbek po rozpoczęciu produkcji komercyjnej i analizy przyczyn wystąpienia wad.