Pomiar kąta natarcia
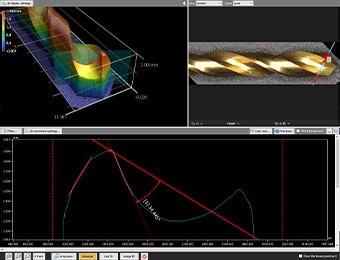
Kąt między bitem narzędzia tnącego a wiórami ze skrawania jest nazywany kątem natarcia. Ma on duży wpływ na opór cięcia, generowanie wiórów ze skrawania, ciepło cięcia i okres eksploatacji. Sprawdzenie i kontrolowanie kąta natarcia narzędzia tnącego ma kluczowe znaczenie dla zapewnienia prawidłowego wykonania obróbki skrawaniem. Z tego względu kąt natarcia może być trudny do zmierzenia narzędziami konwencjonalnymi. W tym artykule objaśniono podstawowe informacje na temat kąta natarcia i przedstawiono najnowszą technologię stosowaną do jego dokładnych pomiarów.
- Kąt natarcia
- Dodatni i ujemny kąt natarcia we frezowaniu walcowo-czołowym
- Zależność między kątem narzędzia tnącego, kątem natarcia i kątem przyłożenia narzędzia
- Problemy z konwencjonalnym pomiarem kąta natarcia
- Rozwiązanie problemów z pomiarem kąta natarcia
- Podsumowanie
Kąt natarcia
Końcówka zamontowana na końcu bitu narzędzia tnącego ma kąt natarcia zaprojektowany w sposób umożliwiający wydostawanie się wiórów ze skrawania w trakcie cięcia obrabianego przedmiotu. Kąt natarcia jest kątem utworzonym między powierzchnią cięcia docelowego przedmiotu obrabianego (powierzchnia odniesienia) a powierzchnią (powierzchnia natarcia), na której wióry ze skrawania wydostają się, gdy narzędzie tnące ściera docelowy przedmiot obrabiany.
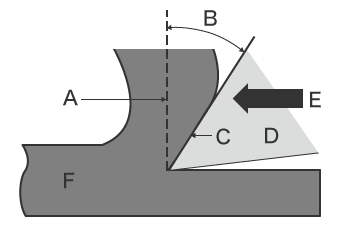
- A
- Powierzchnia odniesienia (wióry ze skrawania)
- B
- Kąt natarcia
- C
- Powierzchnia natarcia
- D
- Końcówka (bit narzędzia tnącego)
- E
- Kierunek cięcia
- F
- Przedmiot obrabiany
Dla odniesienia kąt krawędzi ostrza narzędzia nazywany jest kątem narzędzia tnącego. Powierzchnia po przeciwnej stronie (dolna strona na rysunku) powierzchni natarcia końcówki (narzędzia tnącego) jest nazywana powierzchnią przyłożenia. Kąt, jaki tworzy z obrabianym przedmiotem, jest nazywany kątem przyłożenia. Jest to kąt wymagany do zapobiegania wzajemnym zakłóceniom między narzędziem a obrabianym przedmiotem.
Dodatni i ujemny kąt natarcia we frezowaniu walcowo-czołowym
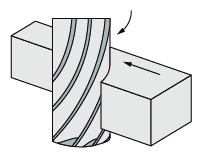
Frezy walcowo-czołowe są stosowane do tworzenia kształtów i otworów w trakcie frezowania i mogą ciąć różne materiały w kilku kierunkach. Frez walcowo-czołowy ogólnie opisuje się jako kształt dodatni lub kształt ujemny zgodnie z kątem natarcia bitu narzędzia.
W większości przypadków wybierany jest kształt dodatni z mniejszym oporem cięcia dla bitu narzędzia. Mając to na uwadze, frez walcowo-czołowy z kątem ujemnym może być stosowany do cięcia twardych przedmiotów obrabianych, jak stal o wysokiej twardości, gdzie wymagana jest wytrzymałość bitu narzędzia. Patrz różnice między kształtem dodatnim a ujemnym poniżej.
Kształt dodatni
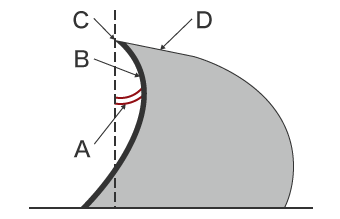
- A
- Kąt natarcia = dodatni
- B
- Powierzchnia natarcia (tylna strona bitu narzędzia)
- C
- Krawędź bitu narzędzia
- D
- Powierzchnia przyłożenia
- Charakterystyka dodatniego kąta natarcia
-
- Ostrze tnące jest ostre, a opór cięcia jest niewielki.
- Można uzyskać doskonałą chropowatość powierzchni cięcia nawet podczas obróbki skrawaniem z niewielką prędkością.
- Nadaje się do materiałów miękkich lub przedmiotów łatwych w obróbce (miedź, aluminium, stal nierdzewna, tworzywo sztuczne, materiał nieobrobiony, stal poddana obróbce cieplnej).
Kształt ujemny
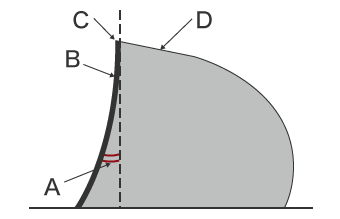
- A
- Kat natarcia = ujemny
- B
- Powierzchnia natarcia (tylna strona bitu narzędzia)
- C
- Krawędź bitu narzędzia
- D
- Powierzchnia przyłożenia
- Charakterystyka ujemnego kąta natarcia
-
- Podczas obróbki skrawaniem z niewielką prędkością opór cięcia jest duży, ale zmniejszona jest chropowatość powierzchni cięcia.
- Podczas obróbki skrawaniem z dużą prędkością uzyskuje się doskonałą chropowatość powierzchni cięcia.
- Nadaje się do twardych materiałów, gdzie występuje prawdopodobieństwo wyszczerbienia (stal o dużej twardości lub żeliwo).
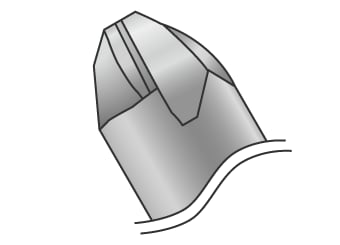
W przypadku kulistego frezu walcowo-czołowego, który ma końcówkę półkulistą, rdzeń bitu narzędzia może zostać pogrubiony przez użycie kształtu ujemnego dla kąta spirali bitu narzędzia. Dzięki temu możliwe jest zapewnienie wysokiej sztywności.
Zależność między kątem narzędzia tnącego, kątem natarcia i kątem przyłożenia narzędzia
Podczas procesu cięcia narzędzie tnące (z reguły narzędzie z twardego metalu) wbija się w obrabiany przedmiot i tnie, kształtuje oraz usuwa materiały.
Nie tylko trzeba uwzględnić kąt narzędzia tnącego, ale również zapewnić prawidłowe ustawienie kąta natarcia, aby wióry ze skrawania wydostawały się we właściwym kierunku. Jednocześnie kąt natarcia musi być prawidłowo ustawiony, aby nie dopuszczać do kontaktu narzędzia z wykończoną powierzchnią po cięciu. Główną zależność między każdym kątem podsumowano poniżej.
Kąt narzędzia tnącego
Podczas cięcia materiałów o dużej twardości ważne jest zwiększenie kąta narzędzia tnącego. Z tego względu, jeśli kąt narzędzia tnącego jest za mały, może dojść do wyszczerbienia lub spękań. Podczas cięcia materiałów miękkich lub materiałów o wysokich właściwościach spawalniczych zasadne jest zmniejszenie kąta narzędzia tnącego, aby poprawić wydajność cięcia.
Kąt natarcia
Kąt natarcia określa grubość i kierunek przepływu wiórów.
Im większy kąt natarcia, tym mniejszy kąt ścinania wiórów. Wraz ze zmniejszaniem kąta ścinania zwiększa się grubość wiórów. Redukuje to siłę i temperaturę cięcia, co ostatecznie prowadzi do zmniejszenia zużycia narzędzia. Z tego względu, jeśli kąt natarcia jest za duży, może powodować zmniejszenie wytrzymałości krawędzi narzędzia i pęknięcie podczas obróbki skrawaniem twardych materiałów.
Podczas cięcia twardych materiałów zasadne jest stosowanie narzędzia o ujemnym kącie natarcia, jak wyjaśniono w powyższym przykładzie. Ujemny kąt natarcia może powodować rozrzucanie wiórów na powierzchnię obrabianego przedmiotu i skutkować cięciem materiału w miejscach, gdzie nie jest to potrzebne. Te wióry na powierzchni natarcia są nazywane metalem martwym. Należy zachować ostrożność podczas korzystania z tego typu narzędzia, ponieważ może to wpłynąć na warunki tworzenia się wiórów, okres eksploatacji narzędzia i chropowatość wykończonej powierzchni.
Kąt przyłożenia
Kąt przyłożenia jest wymagany do zapobiegania wzajemnym zakłóceniom między narzędziem a obrabianym przedmiotem. Zbyt duży kąt przyłożenia zmniejsza wytrzymałość krawędzi narzędzia tnącego, w związku z czym jest ona bardziej podatna na wstrząs mechaniczny. Z tego względu duży kąt przyłożenia nie tworzy większej szerokości zużycia na powierzchni natarcia nawet wtedy, gdy zużycie postępuje. Zaletą jest zmniejszenie prawdopodobieństwa wibracji towarzyszących. Podczas cięcia materiałów ciągliwych (jak stopy aluminiowe) zwiększający się kąt przyłożenia zmniejszy prawdopodobieństwo przywierania wiórów do powierzchni przyłożenia.
Kąt w każdej części narzędzia jest blisko powiązany z wydajnością obróbki skrawaniem przedmiotu, dokładnością, jakością wykończenia oraz okresem eksploatacji narzędzia. Ponieważ ze względu na zużycie narzędzia może dojść do zmian tych kątów, pomiar kształtu narzędzia jest niezwykle ważny dla zachowania i poprawienia jakości oraz wydajności obróbki skrawaniem.
Problemy z konwencjonalnym pomiarem kąta natarcia
Dokładny pomiar kąta natarcia jest bardzo ważny, ponieważ niewłaściwy kąt natarcia może spowodować zużycie narzędzia, przywieranie martwego metalu, wadę chropowatości wykończonej powierzchni oraz skrócenie okresu eksploatacji narzędzia.
Do konwencjonalnego pomiaru kąta natarcia stosuje się system pomiaru profilu lub mikroskop. Metody te wiążą się jednak z następującymi problemami.
Problemy z pomiarem kąta natarcia za pomocą systemu pomiaru profilu
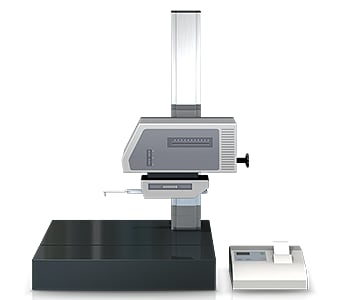
System pomiaru profilu mierzy i rejestruje profil obiektu przez śledzenie jego powierzchni za pomocą rysika.
W ostatnich latach opracowano systemy pomiaru profilu wykorzystujące laser zamiast rysika, które umożliwiają pomiar skomplikowanych kształtów przez bezkontaktowe śledzenie profilu. Niektóre modele są nawet w stanie wykonywać pomiar zarówno górnych, jak i dolnych powierzchni.
Pomiar kąta natarcia narzędzia za pomocą systemu pomiaru profilu wiąże się z poniższymi problemami.
- Ponieważ kąt jest za mały, rysik może odłączyć się od obiektu, co uniemożliwi zmierzenie prawidłowej wartości.
- Podczas ponownego polerowania powierzchni natarcia trudno jest ocenić, czy regulacje były skuteczne, jeśli oceny pomiaru są wykonywane na linii.
Rozwiązanie problemów z pomiarem kąta natarcia
W przypadku zwykłych maszyn pomiarowych może być wymagane dużo czasu w celu zamocowania obiektu za pomocą jigu. Ponadto ze względu na wykonywanie pomiaru przez kontakt punktowy lub liniowy na trójwymiarowym obiekcie lub obszarze występuje problem wyboru obiektu lub punktów pomiaru.
Aby rozwiązać te problemy pomiarowe, firma KEYENCE opracowała optyczny profilograf 3D ze sterowaniem jednym przyciskiem serii VR.
To narzędzie dokładnie rejestruje kształt 3D całej powierzchni docelowej bez kontaktu z obiektem. Mierzy również trójwymiarowy kształt obiektu umieszczonego na stoliku urządzenia przez skanowanie 3D wykonywane z wysoką dokładnością w ciągu zaledwie sekundy. Umożliwia natychmiastowy i ilościowy pomiar bez błędów w wynikach pomiaru. W tej sekcji przedstawiono kilka konkretnych zalet serii VR.
Korzyść nr 1: możliwość bezkontaktowego pomiaru kształtów 3D z doskonałą charakterystyką kątową.
Konwencjonalne przyrządy pomiarowe mogą jedynie rejestrować punkty lub linie za pomocą rysika. Utrudnia to pomiar obiektów, które mają kąty ostre, są małe lub mają złożone kształty.
Urządzenie serii VR umożliwia natychmiastowe skanowanie pełnej powierzchni części, pozwalając na bezkontaktowy pomiar kształtu 3D. Pozwala to na doskonałe renderowanie charakterystyki kątowej obiektu dzięki możliwości natychmiastowego rejestrowania dokładnych danych profilu dla całego kształtu 3D. Ponadto urządzenie VR zapewnia wiele korzyści dotyczących pomiarów narzędzi, np. frezów walcowo-czołowych, gdzie kształty i charakterystyka kątowa są złożone i precyzyjne.
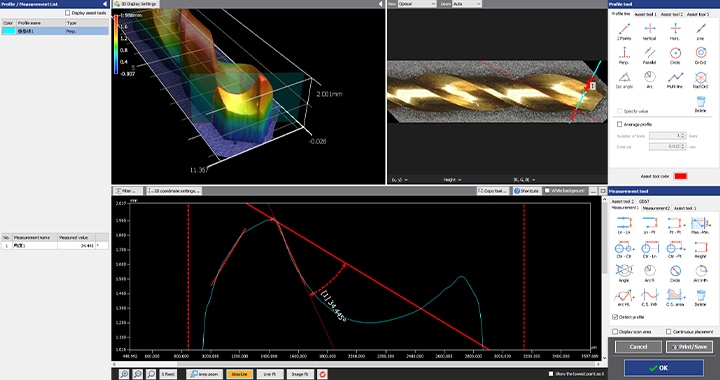
Korzyść nr 2: pomiary są identyfikowalne zgodnie z normami krajowymi.
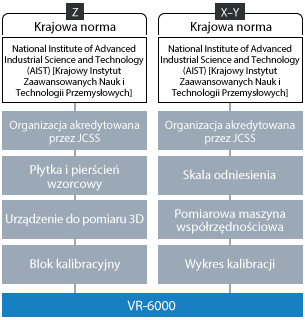
Urządzenie serii VR natychmiast i dokładnie skanuje kształt obiektu, aby go zmierzyć.
Wyniki pomiarów opierają się na systemie identyfikowalności powiązanym z normami krajowymi.
Sprawdzian zgodny z identyfikowalnością XYZ jest powiązany ze standardową skalą laboratorium z certyfikatem JCSS, co pozwala na wykonanie dokładnej kalibracji na miejscu w każdej chwili. Zapewnia to pomiar o wysokiej niezawodności i zgodny z normą.
Podsumowanie
Urządzenie serii VR umożliwia natychmiastowy pomiar kształtu 3D obiektu przez skanowanie bezkontaktowe. Kąt natarcia narzędzia wymagany do prawidłowej obróbki skrawaniem można łatwo i dokładnie zmierzyć, po prostu umieszczając narzędzie na stoliku pomiarowym i klikając jeden przycisk. Poniżej wymieniono korzyści wynikające z korzystania z urządzenia serii VR.
- W przeciwieństwie do konwencjonalnych kontaktowych systemów pomiarowych urządzenia serii VR mogą przeprowadzić dokładny pomiar bez względu na kształt lub rozmiar obiektu bądź charakterystykę kątową mierzonej lokalizacji.
- Wyniki pomiaru są identyfikowalne zgodnie z krajowymi normami, co zapewnia niezawodność pomiarów kształtów. Takie rezultat uznaje się za niemożliwy do uzyskania za pomocą mikroskopu cyfrowego. Jednocześnie system można łatwo skalibrować w dowolnym momencie.
Ogólnie urządzenie serii VR może natychmiast i dokładnie zmierzyć kształt narzędzia, w tym kąt natarcia, poprawiając jakość obróbki skrawaniem, wydajność oraz okres eksploatacji narzędzia.
Oprócz narzędzi może również mierzyć dokładny kształt 3D obrabianych przedmiotów. Urządzenie serii VR można opisać jako narzędzie znacznie zwiększające wydajność wszystkich powiązanych procesów roboczych na stanowisku obróbki skrawaniem, a także poprawiające jakość i produktywność.