Pomiar równoległości produktów formowanych przez tłoczenie
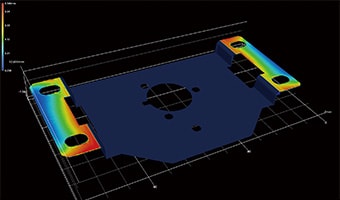
Tłoczenie to rodzaj obróbki plastycznej. W niektórych przypadkach tłoczenia tworzywa sztuczne mogą nie być formowane zgodnie z projektem. Zwykle dzieje się tak, gdy wewnątrz materiału po tłoczeniu pozostają naprężenia wynikające z czynników takich jak sprężynowanie. Podczas tłoczenia blach w kształt korby lub litery U przez zginanie należy zachować ostrożność, ponieważ części narożne mogą zostać uformowane pod kątami odbiegającymi od zalecanych, a równoległość może wykraczać poza wyznaczone tolerancje. W produkcji ram dla przemysłu motoryzacyjnego w ostatnich latach podniesiono standard związany z wytrzymałością na rozciąganie blach stalowych, co utrudnia ich precyzyjne tłoczenie.
W tej sekcji omówiono problemy z równoległością w procesie tłoczenia oraz przedstawiono podstawowe informacje dotyczące pomiaru równoległości, problemy z pomiarem równoległości oraz rozwiązania tych problemów.
- Przyczyna błędu związanego z równoległością: sprężynowanie
- Problemy z konwencjonalnym pomiarem równoległości
- Rozwiązanie problemów z pomiarem równoległości
- Podsumowanie: kompleksowa poprawa i wyższa skuteczność pomiaru jako rozwiązanie problemów z pomiarem równoległości produktów formowanych przez tłoczenie
Przyczyna błędu związanego z równoległością: sprężynowanie
Równoległość płyty stołu prasy i powierzchni ślizgowej oraz równoległość produktu formowanego są w tłoczeniu niezwykle istotne. Nieprawidłowa równoległość płyty stołu i powierzchni ślizgowej będzie mieć niekorzystny wpływ na kąt zgięcia i dociskacz do ciągnienia, nawet jeśli suwak będzie poruszać się pionowo. Powoduje to skrócenie okresu eksploatacji tłocznika. Wady równoległości produktu formowanego po tłoczeniu wynikają przede wszystkim z naprężeń resztkowych (wewnętrznych), które występują wewnątrz produktu formowanego. To odkształcenie, nazywane sprężynowaniem, utrudnia zachowanie wymaganej dokładności wymiarowej.
Rodzaje sprężynowania
Przyczyny sprężynowania można określić, badając warunki naprężeń wewnętrznych w formowanym produkcie w dolnym martwym punkcie prasy. Podczas zginania w dolnym martwym punkcie naprężenia rozciągające oddziałują na powierzchnię zewnętrzną zgięcia, natomiast naprężenia ściskające oddziałują na jego powierzchnię wewnętrzną. Oddzielenie tłocznika występuje przy różnicach naprężeń zgodnych z kierunkiem grubości blachy, które ostatecznie powodują zmianę kąta zgięcia. Typowymi rodzajami sprężynowania są zmiana kąta czy wypaczenie ścianki pionowej przy zaokrąglonej części występu tłocznika, skręcenie oraz wypaczenie grzbietu. Poniżej omówiono naprężenia powodujące sprężynowanie i przykładowe wady wynikające ze sprężynowania.
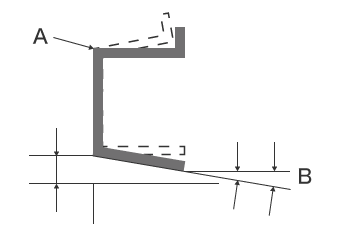
- A
- Zgięcie grzbietu
- B
- Zmiana kąta
- Zmiana kąta:
- Jest to wada polegająca na zmianie kąta zgięcia wskutek różnic naprężeń zgodnych z kierunkiem grubości blachy.
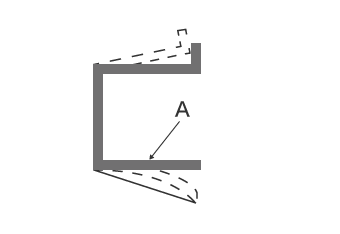
- A
- Wypaczenie ścianki
- Wypaczenie ścianki:
- Jest to wada polegająca na wypaczeniu ścianki wskutek różnic naprężeń wzdłużnych.
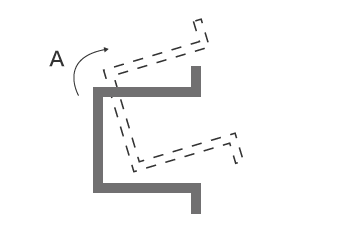
- A
- Skręcenie
- Skręcenie:
- Jest to wada polegająca na skręceniu całego elementu wskutek różnic naprężeń zgodnych z kierunkiem grubości blachy oraz wskutek naprężeń oddziałujących do wnętrza powierzchni.
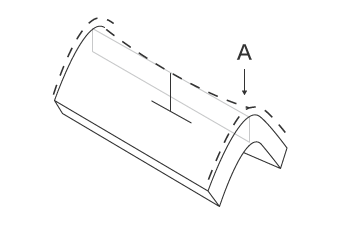
- A
- Wypaczenie grzbietu
- Wypaczenie grzbietu:
- Jest to wada polegająca na wypaczeniu zginanego grzbietu wskutek różnic naprężeń zgodnych z kierunkiem grubości blachy.
Rozwiązania zapobiegające sprężynowaniu w odniesieniu do równoległości
Rozwiązania zapobiegające sprężynowaniu obejmują zasadniczo zmianę projektu lub kształtu tłocznika w kierunku przeciwnym do kierunku, w którym występuje sprężynowanie. Korygując wielkość i kierunek sprężynowania na tłoczniku prasy, można spełnić tolerancje wymiarowe.
W przeszłości rozwiązania zapobiegające sprężynowaniu wprowadzano przede wszystkim w oparciu o intuicję i doświadczenie projektanta, a tłocznik modyfikowano po zakończeniu prób. Ponieważ wielkość sprężynowania zazwyczaj wzrasta proporcjonalnie do wytrzymałości blachy stalowej na rozciąganie, w przypadku znacznego sprężynowania może jednak zaistnieć konieczność wprowadzenia istotnych zmian w tłoczniku. W celu rozwiązania tego problemu do projektowania tłoczników od pewnego czasu wykorzystuje się symulacje z zastosowaniem metody elementów skończonych (FEM).
Istnieją również inne rozwiązania zapobiegawcze, takie jak „zginanie dwustopniowe”, które polega na dwukrotnym zginaniu przy jednym skoku maszyny. Dodatkowo w wyniku „uderzania” na obu narożach krawędzi skrawającej stempla powstają występy, a w wyniku „obróbki pod rowki” na części obrabianego mechanicznie materiału, który jest zginany, z wyprzedzeniem wykonuje się wgniecenia w kształcie litery V (karby trójkątne).
Te rozwiązania zapobiegawcze można wdrażać w przypadkach, gdy przyczyna sprężynowania jest znana. Ponieważ kształty rzeczywistych produktów formowanych przez tłoczenie są złożone, ustalenie przyczyny sprężynowania może być bardzo trudne. Z tego względu trzeba stosować skuteczniejszą metodę wykonywania obliczeń związanych ze sprężynowaniem.
Obliczanie wielkości sprężynowania
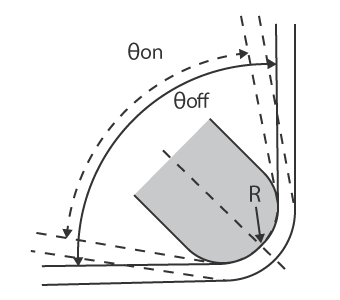
Jeżeli można przynajmniej orientacyjnie obliczyć wielkość sprężynowania, można wdrożyć rozwiązania zapobiegawcze przed przystąpieniem do obróbki mechanicznej. Wzór na obliczanie przewidywanej wielkości sprężynowania jest jednak skomplikowany i zasadniczo używa się go na etapie projektowania tłocznika. Przedstawiono go poniżej.

- Δθ
- Zmiana kąta wskutek sprężynowania
- θon
- Kąt zgięcia (°) po przyłożeniu nacisku
- θoff
- Kąt zgięcia (°) po wystąpieniu sprężynowania
- σB
- Wytrzymałość blachy stalowej (N/mm2)
- R
- Promień krzywizny stempla (mm)
- E
- Moduł Younga blachy stalowej (= 206 000 N/mm2)
- t
- Grubość blachy stalowej (mm)
* σB (wytrzymałość blachy stalowej) oraz E (moduł Younga blachy stalowej) są wartościami właściwymi dla danego materiału.
Krawędź skrawającą do zginania tworzy się na podstawie szacunkowej wielkości sprężynowania. Dalsze obliczanie błędu wynikającego ze sprężynowania sprawia trudności. Innymi słowy, łatwiej jest skorygować promień wewnętrzny, niż obliczyć wielkość sprężynowania. Dodatkowo między wartością obliczoną a wartością rzeczywistą występuje duży błąd spowodowany takimi czynnikami jak zmienność grubości blachy czy różnice w danych technicznych maszyny. Dlatego tolerancję wymiarową należy potwierdzić, wykonując pomiar po formowaniu.
Problemy z konwencjonalnym pomiarem równoległości
Równoległość to wartość, która wskazuje, jak równoległa jest każda płaszczyzna lub linia formowanego produktu w odniesieniu do idealnej płaszczyzny lub linii wirtualnej, będącej płaszczyzną lub linią odniesienia. Mierzy się ją, ustawiając płaszczyznę lub linię wirtualną. Nie można jej mierzyć narzędziem ręcznym, takim jak suwmiarka czy mikrometr. Z tego względu równoległość tłoczonego produktu mierzy się, używając współrzędnościowej maszyny pomiarowej lub przyrządu do pomiaru obrazu CNC. Do wykonania pomiaru równoległości z wykorzystaniem tych przyrządów wymagane są jednak precyzyjne i zaawansowane umiejętności techniczne i bogate doświadczenie. Z pomiarem tym wiążą się również poniższe problemy.
Problemy z pomiarem równoległości za pomocą współrzędnościowej maszyny pomiarowej
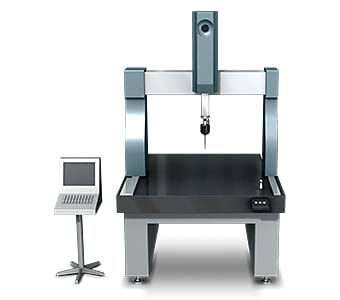
Ogólnie rzecz biorąc, podczas pomiaru wypaczenia za pomocą współrzędnościowej maszyny pomiarowej koniec sondy musi się stykać z co najmniej czterema narożnikami na mierzonej powierzchni obiektu.
Na przykład na płytce mierzy się zazwyczaj od sześciu do ośmiu punktów. Gdy obszar pomiarowy jest duży, dokładność pomiaru można ulepszyć przez zwiększenie liczby punktów pomiarowych w celu zebrania większej ilości danych pomiarowych.
Korzystanie ze współrzędnościowej maszyny pomiarowej do pomiaru równoległości wiąże się jednak z poniższymi problemami.
- Ponieważ konieczny jest pomiar przez kontakt z poszczególnymi punktami, przede wszystkim trudno jest zidentyfikować kształt całego obiektu.
- Ponieważ pomiar większej liczby punktów w celu uzyskania większej ilości danych pomiarowych wymaga dużo czasu, nie da się zidentyfikować szczegółowego kształtu całego obiektu.
Problemy z pomiarem równoległości za pomocą przyrządu do pomiaru obrazu CNC
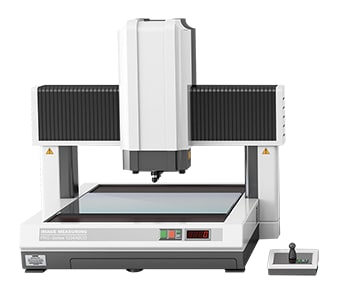
Zasadniczo wizyjny system pomiarowy rejestruje obiekt na stoliku za pomocą kamery CCD i wykonuje pomiar 3D. Można przeprowadzać obserwacje z wykorzystaniem obrazów kolorowych, lecz jeśli wykorzystuje się je na potrzeby pomiaru równoległości, występują poniższe problemy.
- Jeżeli obiekt ma występy, może dojść do fałszywej detekcji. Ponadto jeśli punkty pomiarowe lub inne ustawienia będą różne, wystąpią różnice w dokładności pomiaru.
- Gdy liczba X, Y, Z lub innych elementów pomiarowych wzrasta, program staje się złożony, wymagając zarówno zaawansowanej wiedzy specjalistycznej, jak i większej liczby roboczogodzin na konfigurację. Wymagana liczba roboczogodzin na pomiary wzrasta proporcjonalnie do liczby obiektów poddawanych pomiarom. W tym zakresie występują poważne problemy, takie jak konieczność dysponowania komorą pomiarową, konieczność utrzymywania temperatury odniesienia w komorze pomiarowej, czy fakt, że nie każdy operator potrafi przeprowadzać dokładne pomiary.
Rozwiązanie problemów z pomiarem równoległości
Współrzędnościowe maszyny pomiarowe, które są zwykle używane, wymagają dużo czasu na wykonanie pomiaru, ponieważ mierzą trójwymiarowe obiekty i miejsca pomiaru z zastosowaniem metody kontaktowej w wielu punktach. Dodatkowo przy korzystaniu z tego typu narzędzia mogą występować inne problemy, takie jak niska wiarygodność wartości zmierzonych ze względu na zmiany wynikające z czynników ludzkich czy trudność w tworzeniu użytecznych danych na podstawie wartości liczbowych, funkcji analitycznych i innych technik przetwarzania końcowego.
Aby rozwiązać te problemy pomiarowe, firma KEYENCE opracowała optyczny profilograf 3D ze sterowaniem jednym przyciskiem serii VR oraz współrzędnościową maszynę pomiarową ze skanerem 3D serii VL.
Te produkty dokładnie rejestrują kształt 3D całej powierzchni docelowej bez kontaktu z obiektem. Mierzą również trójwymiarowy kształt obiektu umieszczonego na stoliku urządzenia poprzez skanowanie 3D wykonywane z wysoką dokładnością w ciągu zaledwie sekundy. W tej sekcji przedstawiono kilka konkretnych zalet tych układów.
Korzyść nr 1 zapewniana przez profilograf serii VR: możliwość pomiaru do 800 000 punktów w trakcie jednego skanowania, co eliminuje konieczność powtarzania pomiaru.
Profilograf VR-6000 może uzyskać do 800 000 punktów danych z całej powierzchni w ciągu zaledwie sekundy. Ponieważ pomiar nie jest wykonywany przy użyciu linii lub punktów, powtarzanie pomiaru nie jest wymagane, co skraca całkowity czas pomiaru. Przeprowadzanie pomiarów wymagających punktów wyjściowych, takich jak pomiary równoległości lub prostopadłości, również jest proste. Dane pomiarowe są zapisywane automatycznie i mogą być porównywane z innymi danymi lub z danymi trójwymiarowego projektu.
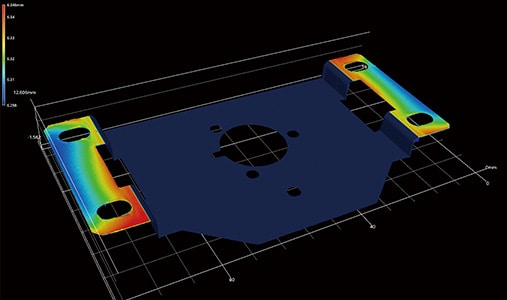
W przeciwieństwie do współrzędnościowej maszyny pomiarowej lub przyrządu do pomiaru obrazu CNC profilograf serii VR odzwierciedla cechy obiektu znajdującego się na stoliku oraz automatycznie dokonuje korekty położenia. Nie jest już konieczne ścisłe pozycjonowanie, co wcześniej było czasochłonne i wymagało wiele wysiłku. Dzięki temu każdy operator, niezależnie od posiadanego doświadczenia, może wykonać pomiar bez problemu i w mgnieniu oka.
Korzystając z profilografów serii VR, można dokładnie zmierzyć nawet równoległość obiektów o złożonym kształcie — wystarczy umieścić obiekt na stoliku urządzenia i nacisnąć przycisk.
Korzyść nr 2 zapewniana przez profilograf serii VR: możliwość ilościowego porównywania i analizowania wielu zbiorów danych pomiarowych.
Profilograf serii VR może zmierzyć kształt 3D całego obiektu przez trójwymiarowe zeskanowanie jego powierzchni w ciągu zaledwie sekundy. Dzięki temu można przeprowadzać pomiar wielu obiektów bez uprzedniego przygotowania próbki. Nie trzeba konfigurować miejsc pomiaru ani liczby punktów pomiarowych, ponieważ system automatycznie ustawi warunki pomiaru.
Wiele zbiorów danych pomiarowych może zostać wyświetlonych na liście, a taką samą analizę zawartości można jednocześnie przeprowadzić dla wszystkich zbiorów danych.
Różnice w danych kształtów wielu obiektów można potwierdzać w ułamku sekundy. Umożliwia to przeprowadzanie zbiorczej analizy równoległości z wykorzystaniem wielu zbiorów danych oraz bezproblemowe dokonywanie oceny ilościowej na potrzeby porównania wypaczenia części nieprawidłowej z częścią prawidłową.
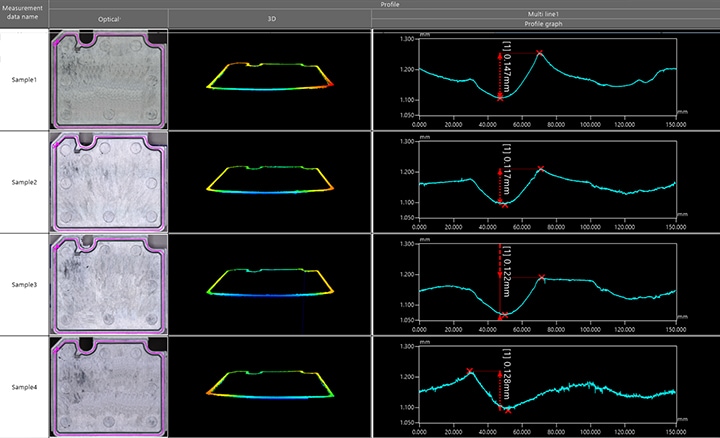
Szeroka gama narzędzi pomocniczych umożliwia prostą konfigurację żądanej zawartości pomiarowej.
Oprócz prostej konfiguracji narzędzia pomocnicze oferują szybkie i dokładne wykonywanie pomiarów kształtów i mogą je obsługiwać nawet początkujący użytkownicy. W rezultacie liczbę próbek można łatwo zwiększyć nie tylko w przypadku prototypów i prób, ale także przy pomiarach i kontroli produktów.
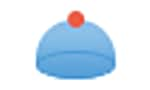
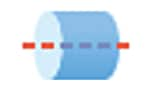
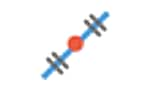
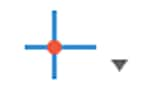
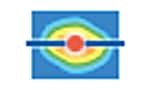
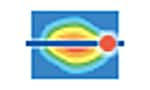
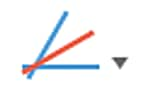
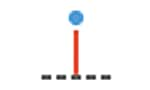
Podsumowanie: kompleksowa poprawa i wyższa skuteczność pomiaru jako rozwiązanie problemów z pomiarem równoległości produktów formowanych przez tłoczenie
Profilograf serii VR umożliwia dokładny i natychmiastowy pomiar trójwymiarowych kształtów obiektu przez szybkie bezkontaktowe skanowanie 3D. Pomiar równoległości małych i dużych elementów oraz elementów o skomplikowanych kształtach można ukończyć w mgnieniu oka. Te produkty mogą rozwiązać wszystkie problemy z konwencjonalnymi przyrządami pomiarowymi.
- Ponieważ dane całej powierzchni mogą być rejestrowane w sposób bezkontaktowy, można mierzyć przekroje, do których rysik nie jest w stanie dotrzeć. Równoległość można mierzyć łatwo i dokładnie nawet w przypadku małych elementów.
- Szeroka gama narzędzi pomocniczych rozwiązuje problem ze zmiennością wartości pomiarowych spowodowanej czynnikami ludzkimi. Dzięki temu można wykonywać wiarygodne pomiary ilościowe.
- Pomiar można wykonać, po prostu umieszczając obiekt na stoliku urządzenia i naciskając przycisk. Nie ma potrzeby pozycjonowania ani wykonywania innych przygotowań. Eliminuje to konieczność przydzielania wyspecjalizowanego operatora do prac pomiarowych.
- Kształty 3D mogą być łatwo mierzone przy dużych prędkościach z wysoką dokładnością. Umożliwia to pomiar dużej liczby obiektów w krótkim czasie, pomagając poprawić jakość.
System ten umożliwia również porównywanie z wcześniejszymi danymi kształtu 3D i danymi CAD, a także zapewnia łatwą analizę danych, takich jak rozkład w granicach tolerancji. Może być skutecznie wykorzystywany do szerokiego zakresu celów, w tym rozwoju produktu, analizy trendów produkcyjnych i kontroli pobierania próbek.
- Seria VR optycznych profilografów 3D ze sterowaniem jednym przyciskiem służących do pomiarów o wyższej rozdzielczości i dokładności
-