Rozwiązanie problemów z pomiarem zużycia matrycy
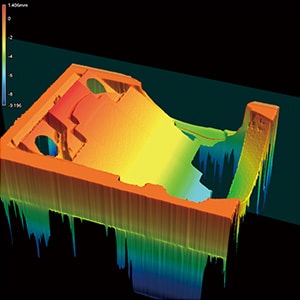
Matryce są niezbędne do formowania takich produktów jak części samochodowe, materiały budowlane, produkty detaliczne i komponenty elektroniczne. Z uwagi na to, że zmniejszenie kosztów produkcji matryc i wydłużenie ich żywotności są bezpośrednio powiązane z kosztami i jakością produktu, ulepszenia w dziedzinie inżynierii matryc są niezwykle ważne dla poprawy naszego codziennego życia.
Ponieważ matryce są niezbędne do formowania szerokiej gamy materiałów, na tej stronie rozważymy zużycie występujące podczas używania matryc i wyjaśnimy środki zaradcze mające na celu wydłużenie żywotności matryc w oparciu o obecnie dostępną wiedzę. Przedstawimy również metody pomiaru zużycia matryc, problemy z konwencjonalnymi metodami pomiarowymi oraz rozwiązanie tych problemów.
- Zużycie matrycy
- Środki zaradcze w przypadku niestandardowego zużycia
- Problemy dotyczące konwencjonalnego pomiaru zużycia matrycy
- Rozwiązanie problemów z pomiarem zużycia matrycy
- Podsumowanie: znaczna poprawa i wyższa wydajność w trudnych przypadkach pomiaru zużycia matryc
Zużycie matrycy
Zużycie matrycy to zjawisko, w którym powierzchnia matrycy ulega zużyciu w wyniku tarcia między częściami, gdy matryca jest stale używana. Zużycie matrycy można podzielić na „niestandardowe zużycie” i „standardowe zużycie”. Niestandardowe zużycie jest spowodowane niewłaściwym materiałem lub kształtem, zmęczeniem metalu i korozją. Standardowe zużycie jest spowodowane kontaktem części lub tarciem, które stopniowo zmniejsza powierzchnię matrycy.
Niestandardowe zużycie
Niestandardowe zużycie może prowadzić do poważnych uszkodzeń, takich jak wada lub uszkodzenie wnęki matrycy albo rdzenia. Typowe rodzaje niestandardowego zużycia obejmują pięć następujących rodzajów. Wśród tych rodzajów niestandardowego zużycia zużycie ścierne i zużycie adhezyjne występują najczęściej w przypadku matryc, a te dwa rodzaje zużycia są nazywane zatarciem.
- Zużycie ścierne:
- Zużycie ścierne dzieli się na zużycie w obecności dwóch i trzech ciał. Zużycie w obecności dwóch ciał występuje, gdy twardszy materiał wbija się w bardziej miękki materiał. Zużycie w obecności trzech ciał występuje, gdy powierzchnia matrycy jest mechanicznie szlifowana przez twardy proszek ścierny (twarde cząstki). Ten rodzaj zużycia jest określany jako płużenie.
-
Zużycie w obecności dwóch ciał - A
- Twardszy materiał
- B
- Bardziej miękki materiał
Zużycie w obecności trzech ciał - A
- Twardszy materiał
- B
- Bardziej miękki materiał
- C
- Twarde cząstki
- Zużycie adhezyjne:
- Zużycie adhezyjne to zjawisko zużycia, w którym stykające się wystające części przylegają do siebie, a następnie oddzielają się od powierzchni. Zjawisko to jest również nazywane zatarciem.
-
- A
- Stykające się części
- B
- Przyleganie i oddzielenie
- Zużycie zmęczeniowe:
- Ten rodzaj zużycia występuje z powodu zmęczenia metalu wynikającego z powtarzających się uruchomień i zatrzymań. Powtarzające się naprężenie powoduje utwardzanie powierzchni, co z czasem prowadzi do powstawania drobnych pęknięć. Te małe pęknięcia ostatecznie przekształcają się w większe pęknięcia, powodując oddzielenie powierzchni. Naprężenie ścinające, które powoduje drobne spękania, jest najwyższe w punkcie nieco poniżej powierzchni. Większe pęknięcia zaczynają powstawać od tego punktu. Może dojść do oddzielenia się kształtów rybiej łuski (płatkowania) lub dużych arkuszy (złuszczania).
- Zużycie cierne:
- Zużycie to tworzy drobne wżery na powierzchni w wyniku powtarzających się niewielkich ruchów, które wytwarzają siłę tarcia na powierzchniach części dopasowanych do siebie. Drobne spękania pojawiają się na powierzchni, gdzie występuje zużycie cierne. Ponieważ obciążenie zewnętrzne i siła tarcia ciernego są przykładane łącznie w tych miejscach, wytrzymałość zmęczeniowa jest zmniejszona do połowy lub mniej pierwotnego poziomu i może skutkować pęknięciem zmęczeniowym.
- Zużycie korozyjne:
- Zużycie to występuje, gdy materiał powierzchniowy jest usuwany z części ślizgowej z powodu różnicy potencjałów elektrycznych między metalami, która jest generowana w korozyjnym środowisku. Tarcie dodatkowo przyspiesza zużycie. Zjawisko to jest również określane jako zużycie chemiczne. Występuje ono w wyniku mechanicznego działania tarcia i reakcji chemicznej z gazem lub cieczą. Gdy ten rodzaj zużycia występuje w ciekłym środowisku, jest również określany jako korozja kawitacyjna.
Standardowe zużycie
Zużycie to występuje podczas normalnego użytkowania w przypadkach, gdy nie występuje zużycie ścierne ani zużycie adhezyjne. Standardowe zużycie dzieli się na zużycie początkowe i zużycie w stanie ustalonym. Zużycie początkowe jest również nazywane zużyciem montażowym i występuje, gdy drobne nierówności powierzchni są usuwane z materiałów po rozpoczęciu pracy. Zużycie w stanie ustalonym to normalne zużycie występujące podczas ciągłego użytkowania. Dzięki wymianie części na nową, gdy osiągnie ona ustalony wymiar używany do normalnego zarządzania zużyciem, możliwe jest zapobieganie awariom i wadom matryc.
Środki zaradcze w przypadku niestandardowego zużycia
W tej sekcji objaśniono środki zaradcze dotyczące zużycia ściernego i zużycia adhezyjnego, które są typowymi rodzajami niestandardowego zużycia matrycy.
Środki zaradcze w przypadku zużycia ściernego
Środki przeciwdziałania zużyciu ściernemu różnią się w przypadku zużycia w obecności dwóch i trzech ciał.
- Zużycie w obecności dwóch ciał:
- Możliwe środki zaradcze w przypadku zużycia w obecności dwóch ciał obejmują zwiększenie twardości materiału i zastosowanie stali zawierającej duże ilości węglików. Ponieważ odporność na ścieranie jest ogólnie wyższa, gdy powierzchnia jest twardsza, skuteczne jest również hartowanie, azotowanie lub podobna metoda obróbki matrycy.
- Zużycie w obecności trzech ciał:
- Aby zapobiec zużyciu w obecności trzech ciał, należy całkowicie uszczelnić powierzchnie ślizgowe maszyny, aby zapobiec przedostawaniu się piasku lub innych cząstek powodujących ścieranie. Jednym ze skutecznych środków zaradczych jest zainstalowanie filtra w układzie smarowania, aby takie cząstki mogły zostać szybko usunięte, jeśli dostaną się do układu.
Środki zaradcze w przypadku zużycia adhezyjnego
Możliwe środki zaradcze w zakresie zużycia adhezyjnego obejmują użycie materiału matrycy o wymaganej twardości i wytrzymałości. Jednak w rzeczywistości istnieją ograniczenia dotyczące środków zaradczych, które można zastosować tylko poprzez ulepszenie materiału matrycy. Z tego powodu konieczne jest wdrożenie środków zaradczych, które zapobiegają przywieraniu poprzez zmniejszenie współczynnika tarcia między powierzchnią matrycy a obrabianym przedmiotem. Optymalizacja smarowania jest szczególnie ważna i konieczne jest równomierne nakładanie smaru, projektowanie odpowiedniego kształtu matryc, aby zapobiec wyciekaniu smaru, oraz optymalizacja warunków obróbki. Skuteczna jest również obróbka twardej powierzchni w celu zmniejszenia współczynnika tarcia.
Problemy dotyczące konwencjonalnego pomiaru zużycia matrycy
Niezwykle ważne jest sprawdzenie, czy zużycie matrycy mieści się w granicach tolerancji. W szczególności w przypadku matryc, które są używane do formowania pod wysokim ciśnieniem, potrzebny jest dokładny i ilościowy pomiar kształtu 3D.
Konwencjonalne pomiary zużycia matryc opierają się na zastosowaniu systemów pomiaru profilu lub współrzędnościowych maszyn pomiarowych. Niemniej jednak mogą wystąpić różne problemy z pomiarem za pomocą konwencjonalnej współrzędnościowej maszyny pomiarowej lub systemu pomiaru profilu. Obejmuje to uzyskiwanie dokładnych pomiarów z wysokim poziomem trudności, co skutkuje zmiennością mierzonych wartości. Kwantyfikacja zmierzonych danych również jest trudna, a analiza trendów i inne analizy związane ze starzeniem się matrycy są problematyczne.
Problemy z pomiarem zużycia matrycy za pomocą systemu pomiaru profilu
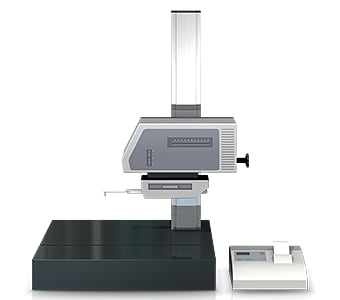
System pomiaru profilu mierzy i rejestruje profil obiektu przez śledzenie jego powierzchni za pomocą rysika. W ostatnich latach opracowano systemy pomiaru profilu wykorzystujące laser zamiast rysika, które umożliwiają pomiar złożonych kształtów przez bezkontaktowe śledzenie profilu. Niektóre modele są nawet w stanie wykonywać pomiar zarówno górnych, jak i dolnych powierzchni.
System pomiaru profilu musi wyznaczać dokładną linię pomiarową dla punktów pomiarowych.
Wiąże się to z poniższymi problemami.
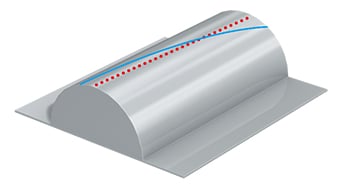
- Prace pomiarowe wymagają dużo czasu, w tym na przymocowanie matrycy do jigu i wypoziomowanie. Wiedza i umiejętności związane z użytkowaniem systemów pomiaru profilu wymagane są również do dokładnego wypoziomowania obiektu.
- Rysik systemu pomiaru profilu porusza się w górę i w dół po łuku wyśrodkowanym na punkcie podparcia ramienia, a jego końcówka porusza się również po osi X. Powoduje to błąd w danych osi X.
- Śledzenie oczekiwanej linii za pomocą rysika jest niezwykle trudnym zadaniem, a nawet niewielkie przesunięcie rysika powoduje błąd w mierzonych wartościach.
- Można zmierzyć tylko część obiektu, a ocena całej powierzchni jest niemożliwa.
Problemy z pomiarem zużycia matrycy za pomocą współrzędnościowej maszyny pomiarowej
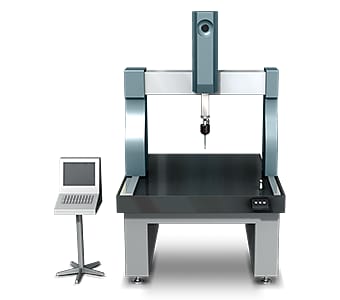
Typowe współrzędnościowe maszyny pomiarowe mierzą kształty przez „skanowanie” z użyciem sondy kontaktowej przykładanej po powierzchni w celu śledzenia i pomiaru kształtu. Ten rodzaj skanowania mierzy dużą liczbę punktów na określonej wysokości.
Ta metoda pomiaru wiąże się jednak z poniższymi problemami.
- Niezwykle trudne jest upewnienie się, że sonda porusza się zgodnie z przeznaczeniem od prostych linii wzdłuż środka walca lub zakrzywionej powierzchni do linii przechodzących przez środek okręgu. W przypadku zaokrąglonego narożnika o małym kącie środkowym, ponieważ cały okrąg jest obliczany na podstawie krótkiego łuku, nawet niewielki błąd pomiaru ulegnie znacznemu zwiększeniu. Takie odchylenia w punktach pomiarowych mogą powodować nieznaczne różnice w mierzonych wartościach.
- Podczas pomiaru kształtu 3D o małym rozmiarze sonda może nie być w stanie zetknąć się z pozycjami pomiarowymi. W związku z tym, że dokładność pomiaru jest proporcjonalna do liczby mierzonych punktów lub linii, konieczne jest zmierzenie dużej ich liczby.
Tak więc pomiar za pomocą współrzędnościowej maszyny pomiarowej wiąże się z istotnymi problemami, w tym z faktem, że nie wszyscy operatorzy w miejscu pracy mogą dokładnie mierzyć kształty, istnieniem części, których w ogóle nie można zmierzyć, a także z ograniczonymi miejscami, w których można zainstalować maszynę.
Rozwiązanie problemów z pomiarem zużycia matrycy
Przyrządy pomiarowe, które są zwykle używane, wiążą się z takimi problemami jak długi czas wymagany do pozycjonowania obiektu oraz fakt, że pomiar trójwymiarowych obiektów i obszarów odbywa się za pomocą styku punktowego lub liniowego. Aby rozwiązać te problemy pomiarowe, firma KEYENCE opracowała optyczny profilograf 3D ze sterowaniem jednym przyciskiem serii VR.
Urządzenie serii VR dokładnie rejestruje kształt 3D całej powierzchni docelowej bez kontaktu z obiektem. Mierzy również trójwymiarowy kształt obiektu umieszczonego na stoliku urządzenia przez skanowanie 3D wykonywane z wysoką dokładnością w ciągu zaledwie sekundy. Umożliwia natychmiastowy i ilościowy pomiar bez błędów w wynikach pomiaru. W tej sekcji przedstawiono kilka konkretnych zalet serii VR.
Korzyść nr 1: pomiar dużej liczby punktów w zaledwie sekundę.
Urządzenie serii VR pozyskuje dane powierzchniowe (800 000 punktów) trójwymiarowego kształtu obiektu w ciągu zaledwie sekundy, znacznie skracając czas wymagany do pomiaru dużej liczby punktów. Urządzenie dokładnie i natychmiastowo mierzy maksymalne i minimalne nierówności na całej powierzchni docelowej, umożliwiając szybką ocenę wszystkich miejsc na obiekcie z uwzględnieniem ustawionych tolerancji. Umożliwia to zarządzanie trudnymi do określenia stanami, takimi jak stopień zużycia lub wyszczerbienia.
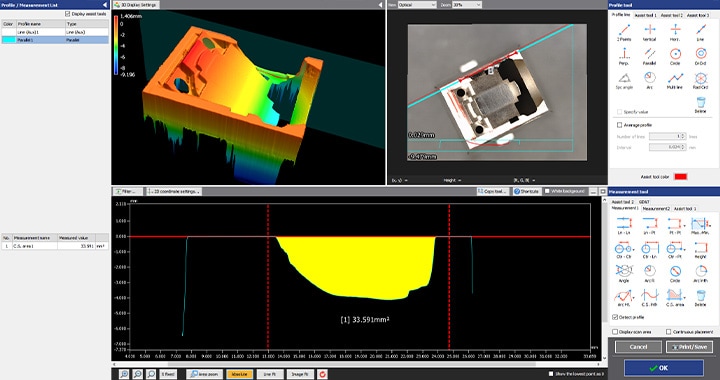
Po zeskanowaniu obrabianego przedmiotu jego profil (przekrój poprzeczny) może być również mierzony w miejscach innych niż użyte w poprzednim pomiarze. Eliminuje to konieczność ponownego ustawiania i mierzenia tego samego obiektu.
Korzyść nr 2: porównywanie pomiarów między częściami lub z danymi CAD
Możliwości urządzenia serii VR wykraczają poza skuteczne gromadzenie danych. Dane pomiarowe mogą zostać wyświetlone na liście, a taką samą analizę zawartości można przeprowadzić dla wszystkich danych jednocześnie.
Na przykład możliwe jest zmierzenie kształtów produktów wytworzonych przy użyciu zarówno nowej, jak i starej matrycy oraz zidentyfikowanie różnic w kształcie wynikającym z zastosowania matryc. Ponadto możliwe jest załadowanie danych CAD w celu szybkiego określenia, jak bardzo wadliwy produkt różni się od dobrego produktu. Umożliwia to łatwą analizę ilościową i ocenę zużycia matrycy.
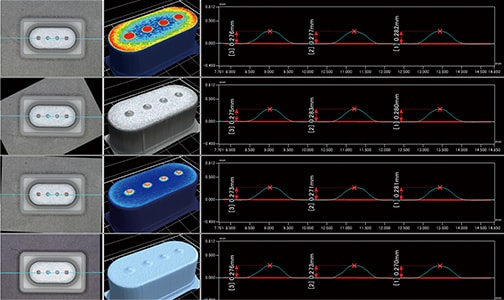
Urządzenie serii VR może szybko mierzyć obiekty o złożonych kształtach, co wcześniej wymagało dużego nakładu pracy i czasu. Wszystkie wyniki pomiarów są zapisywane w postaci cyfrowej, co znacznie zmniejsza nakład pracy wymagany do późniejszego porównania i analizy danych.
Podsumowanie: znaczna poprawa i wyższa wydajność w trudnych przypadkach pomiaru zużycia matryc
Profilograf serii VR jest w stanie szybko zmierzyć i określić ilościowo stopień zużycia matrycy, co wcześniej wymagało dużego doświadczenia, było czasochłonne lub niemożliwe do wykonania w przypadku złożonych matryc. W rezultacie może ocenić jakość produktu z wyższą dokładnością i skutecznością.
- Ponieważ mierzona jest cała powierzchnia, dane dla dużej liczby punktów są rejestrowane jednocześnie. Może to znacznie skrócić czas wymagany do pomiaru złożonych kształtów.
- Dzięki profilografom serii VR wiele zestawów danych pomiarowych może być wyświetlanych na liście w celu porównania, umożliwiając identyfikację i analizę szeregu różnic w odkształceniach spowodowanych zużyciem.
- Skanując produkt powstały w wyniku tłoczenia i porównując zmierzone dane z danymi CAD, można dokładnie określić warunki zużycia matrycy.
- Eliminuje to zmienność wynikającą z czynnika ludzkiego, umożliwiając prawdziwy pomiar ilościowy.
- Aby wykonać pomiar, wystarczy umieścić obiekt na stoliku i nacisnąć przycisk. Nie jest potrzebne pozycjonowanie ani inne przygotowania. Eliminuje to konieczność przydzielania wyspecjalizowanego operatora do prac pomiarowych.
- Kształty 3D mogą być łatwo mierzone przy dużych prędkościach z wysoką dokładnością. Umożliwia to pomiar dużej liczby obiektów w krótkim czasie, pomagając poprawić jakość.
System umożliwia również porównywanie z wcześniejszymi danymi kształtu 3D, a także zapewnia łatwą analizę danych, takich jak rozkład chropowatości. Może on być skutecznie wykorzystywany do różnych celów, w tym do analizy trendów zużycia matrycy w czasie i sprawdzania warunków strat materiału.