Metoda dokładnego i łatwego pomiaru zużycia
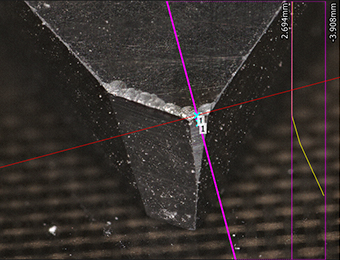
Zużycie występuje na krawędziach końcówek narzędziowych oraz częściach ślizgowych części mechanicznych i ma duży wpływ na wydajność. Skutki zużycia mogą powodować wadę obróbki (z uwagi na ciepło lub wibracje), awarię działania (spowodowaną luzem), a w najgorszym przypadku mogą prowadzić do nieprawidłowego działania lub uszkodzenia maszyny.
W celu zapobiegania zużyciu można stosować olej lub inne środki smarne. Zużyciu trudno jest jednak całkowicie zapobiec i pozostaje ono potencjalnym czynnikiem ryzyka. Z tego względu pomiar zużycia jest niezbędny do utrzymania jakości produktu, przeprowadzenia konserwacji sprzętu i zapewnienia bezpieczeństwa.
- Zużycie
- Rodzaje zużycia
- Konieczność pomiaru zużycia
- Problemy z konwencjonalnym pomiarem zużycia
- Rozwiązanie problemów z pomiarem zużycia
- Podsumowanie: znaczna poprawa i wyższa wydajność pomiarów w trudniejszych przypadkach zużycia
Zużycie
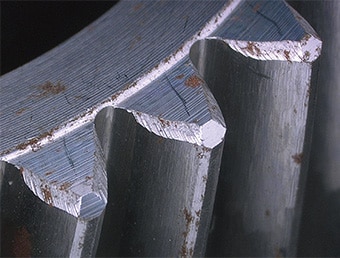
Zużycie występuje, gdy materiał stałej powierzchni jest stopniowo usuwany w wyniku tarcia. Na tarcie i zużycie mają wpływ czynniki zewnętrzne (takie jak obciążenie, prędkość, temperatura i atmosfera), a także czynniki techniczne (takie jak kształt geometryczny, odkształcenie i stan powierzchni styku).
Erozja jest podobna do zużycia i odnosi się do zużycia spowodowanego tarciem między płynem a ciałem stałym. Erozja może na przykład wystąpić między płynem w rurze a ściankami tej rury.
Rodzaje zużycia
Zużycie wynika z bardzo dużej liczby parametrów oddziałujących na siebie w złożony sposób. Obejmuje to miejsce tarcia, właściwości fizyczne materiałów ciernych, atmosferę otoczenia, ciepło, temperaturę oraz oddziaływania fizyczne i chemiczne. W tej sekcji przedstawiono niektóre typowe rodzaje zużycia.
Zużycie adhezyjne
Zużycie adhezyjne występuje, gdy dwa ciała stałe ocierają się o siebie i łączą się ze sobą (przylegają), a następnie pękają i rozdzielają się. Zużycie adhezyjne powstaje w wyniku wiązań chemicznych między ciałami stałymi. Z tego powodu jest bardziej prawdopodobne, że wystąpi między poniższymi rodzajami ciał stałych.
- Materiały tego samego typu
- Materiały o tej samej strukturze krystalicznej i podobnych stałych sieciowych
Zużycie ścierne
Zużycie ścierne występuje między dwoma ciałami stałymi, gdy występy na twardszym materiale mechanicznie przecinają bardziej miękki materiał. Cechy charakterystyczne obejmują stosunkowo dobre warunki smarowania i niski stopień przyczepności, a także większy stopień zużycia w porównaniu z innymi rodzajami zużycia.
Zużycie zmęczeniowe
Zużycie zmęczeniowe występuje, gdy tarcie toczne dominuje nad tarciem ślizgowym, na przykład na powierzchni tocznej łożyska lub na powierzchni zęba koła zębatego. Proces prowadzący do tarcia zmęczeniowego przedstawiono poniżej.
- (1) Powtarzające się naciski działają na powierzchnię, na której metalowe części stykają się ze sobą.
- (2) Powtarzające się naciski powodują stopniowe twardnienie powierzchni.
- (3) Pojawiają się drobne spękania, które z czasem tworzą większe pęknięcia.
- (4) Warstwa powierzchniowa ulega złuszczeniu.
Naprężenie ścinające, które generuje drobne pęknięcia w (3), jest największe w punkcie nieco wewnątrz w stosunku do powierzchni. Taki sam proces jak opisany powyżej skutkuje również wżerami, które w wyniku zmęczenia tocznego tworzą na powierzchni łożyska wgłębienia przypominające łaty, a także odpryskami, które w wyniku zmęczenia materiału powodują odpadanie dużych fragmentów metalu z powierzchni zęba.
Zużycie cierne
Zużycie cierne to zużycie występujące na powierzchni styku materiałów, które zostały zaprojektowane przy założeniu, że nie wystąpi poślizg. Gdy powtarzające się naprężenie jest przykładane do części mocowanych za pomocą śrub i nakrętek (lub do powierzchni styku dwóch części), występuje niewielki względny poślizg (zużycie cierne), który skutkuje zużyciem. Na powierzchni, na której generowane jest zużycie cierne, pojawiają się drobne spękania. Ponieważ obciążenie zewnętrzne i powtarzające się naprężenie działają na miejsce zużycia ciernego, wytrzymałość zmęczeniowa zmniejsza się do połowy lub mniej pierwotnego poziomu (zmęczenie cierne), co prowadzi do pęknięcia zmęczeniowego.
Konieczność pomiaru zużycia
Zużycie narzędzi do obróbki jest bezpośrednio związane z jakością obróbki, natomiast zużycie części jest bezpośrednio związane z dokładnością i bezpieczeństwem pracy. Z tego powodu niezwykle ważne jest mierzenie stanów zużycia, takich jak stopień zużycia. W tej sekcji wyjaśnimy znaczenie pomiaru zużycia na przykładzie klocka hamulcowego i końcówki narzędzia tnącego.
Pomiar zużycia klocków hamulcowych
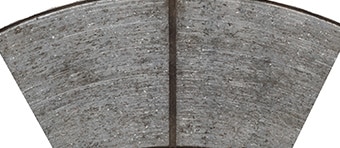
Nowy samochodowy klocek hamulcowy ma około 10 mm grubości. Chociaż żywotność różni się w zależności od producenta, zazwyczaj klocek hamulcowy jest wymieniany, gdy jego zużycie wynosi w przybliżeniu od 1 do 3 mm. Klocek hamulcowy zużywa się w wyniku tarcia o tarczę hamulcową w przypadku hamulca tarczowego lub w wyniku tarcia o bęben hamulcowy w przypadku hamulca bębnowego. Tarcza i bęben hamulcowy również ulegają zużyciu. Ponieważ na zużytej powierzchni klocka hamulcowego widoczne są stany zużycia, trwałość klocka hamulcowego i rodzaj zużycia występującego podczas hamowania można określić przez pomiar lub obserwację objętości klocka hamulcowego i stopnia jego zużycia.
Pomiar zużycia końcówki narzędziowej
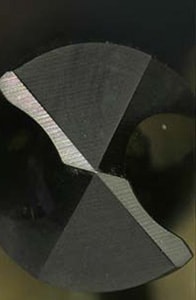
Końcówka frezu walcowo-czołowego lub końcówka narzędziowa zużywają się w wyniku tarcia o obrabiany przedmiot i wióry ze skrawania. Części, które ulegają zużyciu, różnią się w zależności od materiału, jednak w większości przypadków zużycie występuje na powierzchni natarcia i powierzchni odciążającej. Możliwe przyczyny to zbyt duża prędkość skrawania lub nieodpowiedni materiał końcówki narzędziowej. Ponieważ obciążenie końcówki narzędziowej zwiększa się podczas obróbki materiału trudnego do cięcia, zużycie jest większe niż podczas obróbki zwykłych materiałów. Należy zachować ostrożność, ponieważ tarcie na powierzchni odciążającej może zwiększyć siłę cięcia lub zmienić jego głębokość.
Z tych powodów niezwykle ważny jest pomiar zużycia końcówki narzędziowej w celu oceny prędkości skrawania i doboru materiału końcówki narzędziowej.
Problemy z konwencjonalnym pomiarem zużycia
Zazwyczaj stopień zużycia mierzy się za pomocą systemów pomiaru profilu lub współrzędnościowych maszyn pomiarowych. W przypadku pomiaru zużycia na dużym obszarze lub na małych częściach metody te wiążą się jednak z następującymi problemami pomiarowymi:
Problemy z pomiarem zużycia za pomocą systemu pomiaru profilu
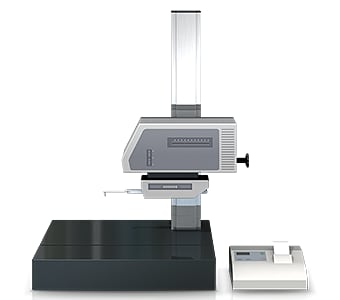
System pomiaru profilu mierzy i rejestruje profil obiektu przez śledzenie jego powierzchni za pomocą rysika. W ostatnich latach opracowano systemy pomiaru profilu wykorzystujące laser zamiast rysika, które umożliwiają pomiar skomplikowanych kształtów przez bezkontaktowe śledzenie profilu. Niektóre modele są nawet w stanie wykonywać pomiar zarówno górnych, jak i dolnych powierzchni.
System pomiaru profilu musi śledzić dokładną linię pomiarową stopnia zużycia, która jest obiektem pomiaru.
Wiąże się to z poniższymi problemami.
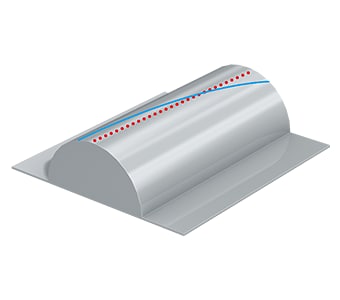
- Prace pomiarowe wymagają dużo czasu, w tym na przymocowanie próbki do jigu i wypoziomowanie. Wiedza i umiejętności związane z użytkowaniem systemów pomiaru profilu wymagane są również do dokładnego wypoziomowania obiektu.
- Rysik systemu pomiaru profilu porusza się w górę i w dół po łuku wyśrodkowanym w punkcie podparcia ramienia rysika. Końcówka rysika porusza się również w kierunku osi X, powodując błąd w danych osi X.
- Śledzenie oczekiwanej linii za pomocą rysika jest niezwykle trudnym zadaniem, a nawet niewielkie przesunięcie rysika powoduje błąd w mierzonych wartościach.
- Trudno jest również zwiększyć liczbę obiektów docelowych ze względu na potrzebę wskazania konkretnych miejsc do pomiaru.
- Można zmierzyć tylko część obiektu, a ocena całej powierzchni jest niemożliwa.
Problemy z pomiarem za pomocą współrzędnościowej maszyny pomiarowej
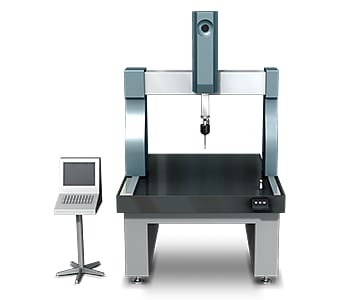
Gdy powierzchnia zużytej części jest niewielka, na przykład 1 mm2, niezwykle trudno jest dokładnie zmierzyć jej kształt przez precyzyjne użycie sondy i utworzenie wirtualnej powierzchni. Trudno jest również zidentyfikować dokładny kształt 3D podczas pomiaru małego obszaru ze względu na niewielką liczbę punktów pomiarowych. Pracochłonne są również powiązane zadania, takie jak tabelaryzacja danych pomiarowych i porównywanie wyników z rysunkami.
Rozwiązanie problemów z pomiarem zużycia
Konwencjonalne przyrządy pomiarowe mierzą trójwymiarowy obiekt lub obszar za pomocą styku punktowego i liniowego. Powoduje to problemy, ponieważ użytkownicy nie mogą zidentyfikować całego kształtu, a wiarygodność zmierzonych wartości jest niska. Aby rozwiązać te problemy pomiarowe, firma KEYENCE opracowała optyczny profilograf 3D ze sterowaniem jednym przyciskiem serii VR.
Urządzenie serii VR dokładnie rejestruje kształt 3D całej powierzchni docelowej bez kontaktu z obiektem. Mierzy również trójwymiarowy kształt obiektu umieszczonego na stoliku urządzenia przez skanowanie 3D wykonywane z wysoką dokładnością w ciągu zaledwie sekundy. Umożliwia natychmiastowy i ilościowy pomiar bez błędów w wynikach pomiaru. W tej sekcji przedstawiono kilka konkretnych zalet serii VR.
Korzyść nr 1: zebranie danych z 800 000 punktów pomiarowych w ciągu zaledwie sekundy.
Profilograf serii VR mierzy kształt całej powierzchni i zbiera dane z grupy 800 000 punktów. Ponieważ pomiar nie jest wykonywany przy użyciu linii lub punktów, powtarzanie pomiaru nie jest wymagane, co skraca czas pomiaru. Elementy trudne do zdefiniowania, takie jak stopień zużycia, mogą być oceniane na podstawie objętości lub powierzchni. Możliwe jest również łatwe przeprowadzenie ilościowej oceny płaskości. Seria VR może również mierzyć profile w określonych miejscach. Nawet po zakończeniu pomiaru można pozyskać profile różnych części z danych skanowania 3D bez konieczności ponownego skanowania obiektu.
Wszystkie dane pomiarowe są zapisywane i mogą być porównywane z innymi danymi lub z danymi projektu 3D.
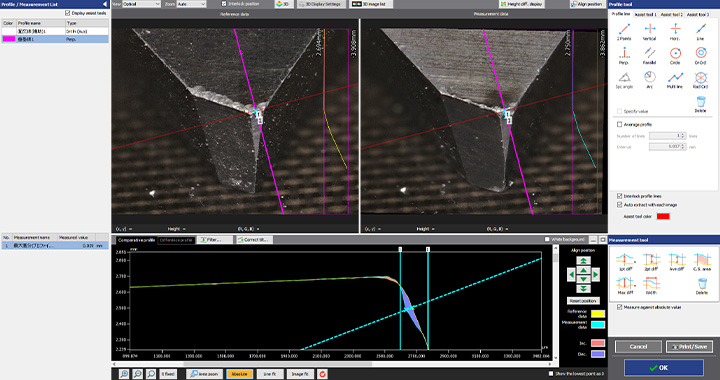
Korzyść nr 2: możliwość pomiaru szerokiego obszaru o wymiarach do 300 mm × 150 mm.
Pomiar można wykonać, po prostu umieszczając obiekt na stoliku urządzenia i naciskając przycisk. Nie jest konieczne ścisłe pozycjonowanie ani inne przygotowania. Umożliwia to wykonywanie bardzo dokładnych pomiarów przez operatorów, którzy nie mają wiedzy ani doświadczenia związanego z przyrządami pomiarowymi.
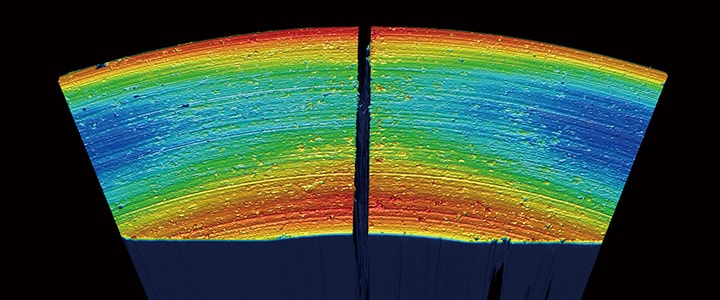
Ponieważ profilograf serii VR wyodrębnia cechy obiektu na stoliku i automatycznie koryguje jego pozycję, nie jest konieczne ścisłe pozycjonowanie wymagające dużych nakładów czasu i wysiłku. Profilograf serii VR może również mierzyć szeroki obszar o wymiarach do 300 mm × 150 mm przez połączenie wielu obrazów pomiarowych. Umożliwia to nawet niedoświadczonemu użytkownikowi łatwe i natychmiastowe wykonanie pomiaru oraz eliminuje potrzebę przydzielania wyspecjalizowanego operatora do prac pomiarowych.
Dzięki profilografom serii VR można dokładnie zmierzyć dużą powierzchnię, na przykład dużego klocka hamulcowego, po prostu przez umieszczenie go na stoliku urządzenia i naciśnięcie przycisku.
Podsumowanie: znaczna poprawa i wyższa wydajność pomiarów w trudniejszych przypadkach zużycia
Urządzenie serii VR umożliwia dokładny i natychmiastowy pomiar trójwymiarowych kształtów obiektu przez szybkie bezkontaktowe skanowanie 3D. Rozwiązuje on wszystkie problemy, z jakimi borykają się konwencjonalne przyrządy pomiarowe, umożliwiając pomiar najwyższych i najniższych punktów na powierzchni zużycia, a także pomiar objętości, pola przekroju poprzecznego i stosunku pola powierzchni do pola przekroju poprzecznego.
- Jest on w stanie jednocześnie dokładnie mierzyć najwyższy i najniższy punkt, obszar, objętość i pole powierzchni.
- Eliminuje to zmienność wynikającą z czynnika ludzkiego, umożliwiając prawdziwy pomiar ilościowy.
- Aby wykonać pomiar, wystarczy umieścić obiekt na stoliku i nacisnąć przycisk. Nie jest potrzebne pozycjonowanie ani inne przygotowania. Eliminuje to konieczność przydzielania wyspecjalizowanego operatora do prac pomiarowych.
- Kształty 3D mogą być łatwo mierzone przy dużych prędkościach z wysoką dokładnością. Umożliwia to pomiar dużej liczby obiektów w krótkim czasie, pomagając poprawić jakość.
System ten umożliwia również porównywanie z wcześniejszymi danymi kształtu 3D i danymi CAD, a także zapewnia łatwą analizę danych, takich jak rozkład w granicach tolerancji. Może być skutecznie wykorzystywany do szerokiego zakresu celów, w tym rozwoju produktu, analizy trendów produkcyjnych i kontroli pobierania próbek.