Přesné měření poloměru ohybu při zpracování plechu
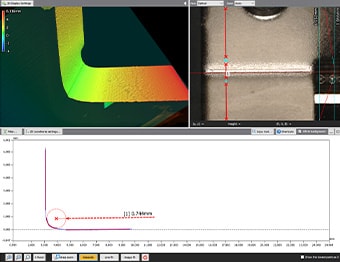
Ohýbání kovových materiálů využívá tvárnosti, která je pro kovy jedinečná, a je metodou obrábění, která se běžně používá při zpracování plechů a jiných kovů.
Ohýbání úzce souvisí s pevností materiálu, a proto může ohýbání na nevhodný poloměr způsobit deformaci, snížení pevnosti a poškození. Proto může mít měření poloměru ohybu velký vliv na kvalitu.
Na této stránce jsou na příkladu zpracování plechů vysvětleny základní poznatky o poloměru ohybu, způsobu jeho výpočtu, opatřeních proti vadám, problémech při konvenčním měření poloměru ohybu a nejnovější metodě měření, která výrazně zvyšuje efektivitu a přesnost práce.
- Poloměr ohybu
- Ohýbání při zpracování plechu
- Napětí vznikající při ohýbání při zpracování plechu a související bezpečnostní opatření
- Výpočet rozvinuté délky ohybu pomocí poloměru ohybu
- Opatření proti praskání a minimální poloměr ohybu
- Problémy při konvenčním měření poloměru ohybu
- Řešení problémů při měření poloměru ohybu
- Souhrn
Poloměr ohybu
Poloměr ohybu je poloměr od počátečního bodu ohybu ke středu ohybu při plastickém zpracování kovu nebo jiného plechu, trubky nebo tyče lisováním nebo válcováním.
Každý materiál má mezní hodnotu pro ohyb bez lomu, která je určena jeho tloušťkou nebo průměrem. Tento poloměr se nazývá minimální poloměr ohybu. Poloměr ohybu musí být nastaven vhodně pro místo ohybu a aplikaci. Odolnost proti napětí způsobenému ohybem může ovlivnit i výsledný poloměr ohybu.
Ohýbání při zpracování plechů
Jedním z typických procesů, kde je důležitý poloměr ohybu, je zpracování plechů. Běžná metoda ohýbání plechů využívá „lisovací brzdu“, která lisuje plech mezi horní raznicí a spodní raznicí. Kromě V-lisů znázorněných na obrázcích níže se používají různé typy lisovacích nástrojů podle tvaru ohybu a materiálu. Patří mezi ně poloměrové šablony, které ohýbají plech do mírného oblouku, a raznice ve tvaru písmene U, které ohýbají plech ve dvou bodech současně jedním tahem.
- A
- Razník (horní raznice)
- B
- Plech
- C
- Matrice (spodní raznice)
- D
- Lisování
Při ohýbání silných plechů mohou některé lisy používat poloměrovou šablonu nebo mohou používat hlubokou raznici ve tvaru písmene V (spodní raznici) i pro běžné ohýbání do tvaru písmene V. Při ohýbání na velký poloměr ohybu může dojít k malému posunu plechu během ohýbání. K měření poloměru lze použít razník známý také jako „pravítko“.
Napětí vznikající při ohýbání při zpracování plechu a související bezpečnostní opatření
V ohnutém plechu vznikají následující napětí. V závislosti na tloušťce a tvrdosti obrobeného materiálu mohou mít tato napětí velký vliv na poloměr ohybu.
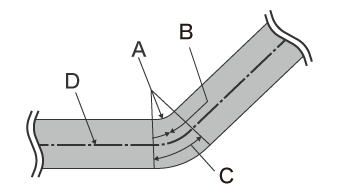
- A
- Poloměr ohybu
- B
- Tlakové napětí
- C
- Napětí v tahu
- D
- Neutrální osa
- • Tlakové napětí
- Vnitřní strana neutrální osy tloušťky plechu je stlačována, čímž v materiálu vzniká síla, která klade odpor stlačení.
- • Napětí v tahu
- Vnější strana je natahována ve směru tahu, čímž v materiálu vzniká síla, která klade odpor tahu.
- * V průřezu ve směru tloušťky se přímka procházející středem plechu, kde nepůsobí žádná z těchto sil, nazývá neutrální osa.
Po vyjmutí lisovaného materiálu z lisovacích forem může materiál v důsledku zbytkového tlakového a tahového napětí pružit a zvětšovat úhel ohybu ohýbaného dílu. Tento jev se nazývá zpětný ráz a je pravděpodobnější u tvrdých materiálů, protože tyto materiály mají tendenci vytvářet vyšší tlakové a tahové napětí. Takové materiály je třeba přehnout do úhlu užšího, než je zamýšlený konečný úhel.
Velikost zpětného rázu se liší v závislosti na materiálu a tloušťce plechu, přičemž silné plechy mají tendenci mít neutrální osu posunutou dovnitř. Proto je důležité zjistit velikost zpětného rázu a nastavit vhodné podmínky pro opracování kovu.
Výpočet rozvinuté délky ohybu pomocí poloměru ohybu
Rozvinutá délka ohybu je nutná pro stabilní ohyb. Lze ji odhadnout pomocí vzdálenosti od povrchu poloměru ohybu k neutrální ose. Protože přímé části A a B se ohýbáním nemění, použijte skutečné hodnoty.
Poměr posunu neutrální osy (λ: lambda) v místě ohybu se liší v závislosti na tloušťce materiálu, tvrdosti, úhlu ohybu a vnitřním poloměru ohybu. Předpokládá se, že neutrální osa se nachází v místě, které je přibližně 20 % až 45 % tloušťky od vnitřního povrchu. Na pracovišti se používají hodnoty vycházející ze zkušeností. Následuje vzorec pro výpočet rozvinuté délky ohybu.
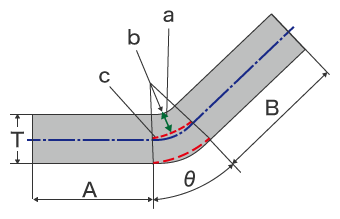
- a
- Vzdálenost povrchu poloměru ohybu od neutrální osy
- b
- Poloměr ohybu
- c
- Neutrální osa v ohýbané části
L = A + B + (R + T x λ) x 2n x θ / 360
L = rozvinutá délka
A, B = délka dílů, které nejsou namáhány ohybem
R = vnitřní poloměr ohybu
T = tloušťka
θ = úhel ohybu
λ = poměr posunu neutrální osy (%) * Hodnota vycházející ze zkušeností
Opatření proti praskání a minimální poloměr ohybu
Problémy vznikající při ohýbání zahrnují vady, jako je praskání a trhání v ohýbaných dílech. Je třeba věnovat pozornost směru, ve kterém je materiál opracováván, protože tyto vady úzce souvisejí se směrem válcování materiálu. Praskliny a jiné vady se častěji vyskytují, je-li materiál ohýbán rovnoběžně se směrem válcování. Tyto vady se vyskytují zejména u materiálů z nerezové oceli a hliníku.
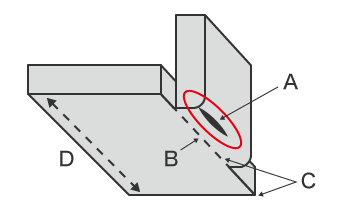
- A
- Místo, kde je pravděpodobné, že dojde k prasknutí
- B
- Linie ohybu
- C
- Obrysová čára zarovnaná s linií ohybu
- D
- Směr válcování rovnoběžný s linií ohybu
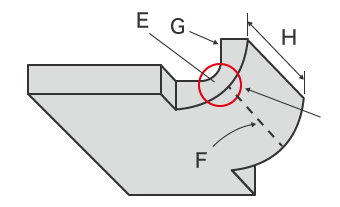
- E
- Snížená tloušťka plechu na ohýbané části
- F
- Linie ohybu
- G
- Průřez zlomu
- H
- Šířka ohybu menší než osminásobek tloušťky plechu
Aby se těmto vadám předešlo, je nutné dodržet minimální poloměr ohybu. Minimální poloměr ohybu se však liší v závislosti na materiálu, tloušťce plechu, raznici a dalších faktorech, takže je obtížné vypočítat správnou hodnotu pomocí matematického vzorce. Proto je nutné stanovit minimální poloměr ohybu na základě zkušeností nebo zkoušek a do konstrukce a zpracování kovů zahrnout protiopatření, která zabrání vzniku trhlin.
- Nastavte linii ohybu kolmo na směr válcování.
- Zvolte materiál s vysokou tažností.
- Vyberte materiál s malými krystalickými zrny nebo zmenšete velikost krystalických zrn zahřátím.
- Posuňte linii ohybu od obrysové čáry plechu, abyste snížili pravděpodobnost vzniku trhlin v důsledku nedostatečného prodloužení při ohýbání plechu.
- Při ohýbání děrovaného plechu se střižený povrch prodlouží snáze, aniž by došlo k prasknutí, než povrch lomený. Ohněte ho stranou, která je na vnější straně střihu.
- Použijte šířku ohybu, která je nejméně osmkrát větší než tloušťka plechu.
I když je důležité věnovat pozornost konstrukci a materiálům, aby se předešlo praskání a dalším vadám, rozhodující je zajistit, aby materiál byl ohýbán do vhodného tvaru v rámci tolerancí. V následující části jsou vysvětleny metody měření poloměru ohybu, problémy s jednotlivými metodami a jejich řešení.
Problémy při konvenčním měření poloměru ohybu
Při požadavku na vyšší přesnost ohýbání je obtížnější zcela zabránit vzniku vad, a to i při správné volbě materiálu, konstrukce a lisovacích nástrojů. Praskliny, třísky a vadné tvary (např. větší poloměr ohybu způsobený pružením) mohou vést k problémům, včetně nižší výtěžnosti a špatné kvality a lámavosti produktů.
Proto je velmi důležité přesně měřit a kontrolovat tvary co největšího počtu ohýbaných produktů během zkoušek lisování a při změně materiálu nebo podmínek ohýbání. Při měření poloměru ohybu se kromě ručních přístrojů, jako jsou měřidla poloměru, používají souřadnicové měřicí stroje (CMM), optické komparátory a další měřicí přístroje. Při měření poloměru ohybu pomocí těchto běžných měřicích přístrojů však dochází k různým problémům.
Problémy při měření poloměru ohybu pomocí souřadnicového měřicího stroje
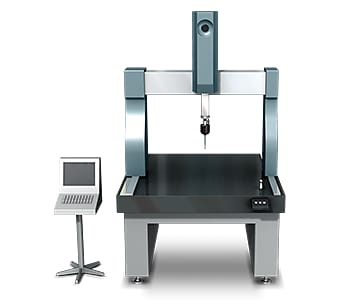
Pro běžné měření ohnutého dílu pomocí souřadnicové měřicí soupravy je nutné, aby se hrot sondy dotýkal více bodů na povrchu cíle.
Pokud je měřená oblast velká, lze přesnost měření zvýšit zvýšením počtu měřených bodů, aby se shromáždilo více dat měření.
S tím však souvisí následující problémy.
- Měření zabere mnoho času. Měření vyžaduje mnoho času a úsilí, zejména pro vysoce přesné měření rozsáhlé oblasti, protože je nutno měřit mnoho bodů.
- Pokud má malý obrobek zapuštěné části, složitý tvar nebo malý poloměr ohybu, může být pro sondu obtížné navázat kontakt.
- Měření vyžaduje dovednosti a zkušenosti. Měření je schopen pouze omezený počet operátorů, což vede k neefektivní práci při měření.
- Tabulkové zpracování naměřených dat a výpočet hodnot rovněž vyžaduje odborné znalosti, dovednosti a mnoho člověkohodin.
Problémy při měření poloměru ohybu pomocí optického komparátoru
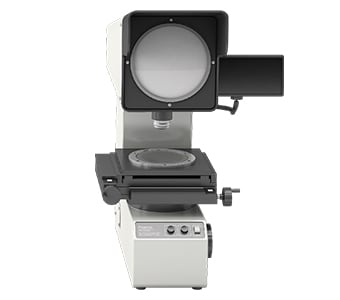
Optický komparátor je typ optického měřicího přístroje, jehož princip měření je podobný principu optického mikroskopu. Tento měřicí přístroj vysílá světlo pod cíl a promítá profil na obrazovku.
Některé velké optické komparátory mají obrazovku o průměru více než 1 m (3,3′). Tyto optické komparátory mohou superponovat promítaný 2D profil na zvětšený výkres, a vizuálně tak identifikovat rozdíly mezi nimi, což však vyžaduje mnoho práce a zručnosti.
Měření pomocí optického komparátoru zahrnuje následující problémy.
- Při instalaci cíle je nutné jeho vyrovnání. Některé tvary vzorků nelze měřit.
- Vzhledem k tomu, že ohýbané cíle mají trojrozměrný tvar, není možné určit podmínky celého ohýbaného povrchu pomocí 2D profilu promítaného ze strany cíle.
- Metoda měření se u různých provozovatelů mírně liší a je pravděpodobné, že i naměřené hodnoty se budou lišit. Rozdíly mezi promítnutými rozměry a výkresem nelze získat v číselné podobě a tvar profilu se musí přenést na křídový papír, což ztěžuje ukládání a porovnávání dat.
Celkově je s touto metodou spojeno mnoho problémů; ne všichni operátoři na pracovišti mohou přesně měřit profily a ne všechny díly lze měřit. Některé vzorky bude nutné kvůli tvaru cíle oříznout.
Řešení problémů při měření poloměru ohybu
Běžné měřicí přístroje jsou omezeny na snímání bodů nebo čar nebo mohou porovnávat pouze 2D profily. To vede k nízké spolehlivosti měření a ztěžuje získání číselných hodnot.
Pro řešení těchto problémů s měřením vyvinula společnost KEYENCE optický 3D profilometr řady VR.
Řada VR přesně zachycuje 3D tvar celého povrchu cíle, aniž by došlo ke kontaktu s ním. Tento nástroj umožňuje uživateli provádět přesná a opakovatelná měření za pouhou 1 sekundu pouhým umístěním vzorku na podložku a kliknutím na jediné tlačítko. Systém automaticky nastavuje rozsah a podmínky měření, čímž zajišťuje přesná kvantitativní měření bez rozdílů mezi jednotlivými uživateli. V této části jsou představeny některé konkrétní výhody řady VR.
Výhoda 1: 3D tvar celého povrchu lze zachytit již za 1 sekundu.
Řada VR okamžitě získává data o povrchu (800 000 datových bodů v jednom skenu) za pouhou jednu sekundu. Umožňuje přesné měření a vyhodnocování maximálních a minimálních nerovností povrchu v celém ohýbaném dílu.
Řada VR může také měřit profily na konkrétních místech. I po měření lze z dat 3D skenu získat profily různých dílů, aniž by bylo nutné znovu skenovat cíl.
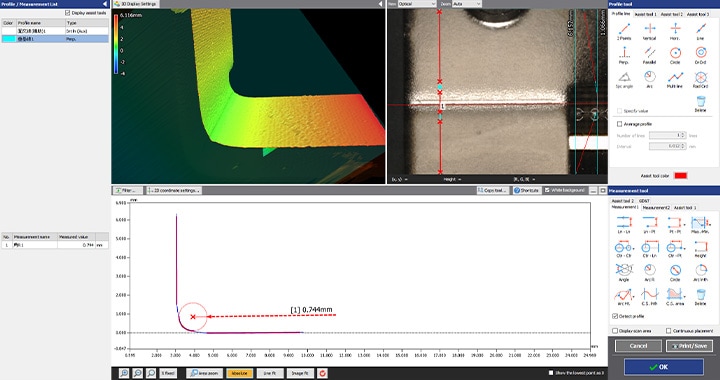
Výhoda 2: Snadné ovládání pro přesné a opakovatelné měření od uživatele k uživateli.
Měření 3D tvaru lze snadno provést pouhým umístěním cíle na podložku a stisknutím tlačítka. Protože je možné automatické nastavení polohy na základě údajů o cílových prvcích, není nutné přísné vyrovnání nebo polohování. Tato řada také obsahuje první funkci Inteligentní měření v odvětví, která automaticky nastavuje rozsah měření a posouvá podložku podle velikosti cíle. Tím odpadá práce s nastavováním délky měření a rozsahu Z.
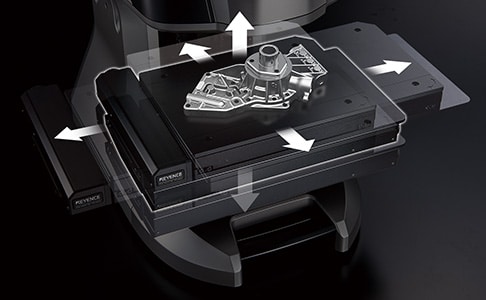
Široká škála pomocných nástrojů umožňuje jednoduché nastavení požadovaného obsahu měření.
Kromě snadné konfigurace umožňují pomocné nástroje obsluhu systému i začínajícím uživatelům, takže každý může měřit tvary rychle a přesně. Díky tomu lze snadno zvýšit počet vzorků nejen pro prototypy a zkoušky, ale také pro měření a kontrolu produktů.
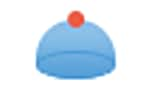
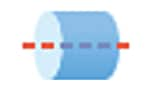
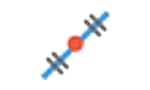
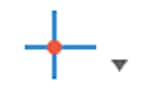
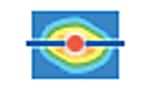
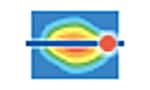
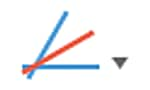
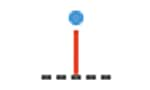
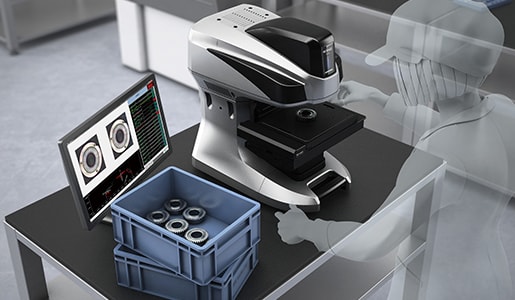
Souhrn
Řada VR dokáže přesně a okamžitě měřit 3D tvary cílů pomocí vysokorychlostního 3D skenování bez kontaktu s cílem. Dokonce i poloměr ohnutého dílu, nerovnosti povrchu a další obtížné cíle lze změřit za pouhou jednu sekundu. Řada VR řeší všechny problémy spojené s konvenčními měřicími přístroji.
- Tato řada je schopna měřit průřezy bez řezání cíle.
- Tím se eliminují odchylky způsobené lidským faktorem, což umožňuje skutečné kvantitativní měření.
- Bez nutnosti polohování nebo jiné přípravy lze měření provést pouhým umístěním cíle na podložku a stisknutím tlačítka. Díky tomu není pro měřicí práce nutné přidělovat specializovanou obsluhu.
- Protože 3D tvary lze snadno měřit vysokou rychlostí a s vysokou přesností, lze v krátkém čase změřit velké množství vzorků. To je užitečné pro zvýšení kvality.
Tento systém také umožňuje porovnání s minulými daty 3D tvarů, daty CAD a snadnou analýzu dat, například rozložení v rámci tolerancí. Lze jej efektivně využít pro širokou škálu účelů včetně vývoje produktů, analýzy výrobních trendů a kontroly vzorků.