Dokładny pomiar promienia gięcia w obróbce blach
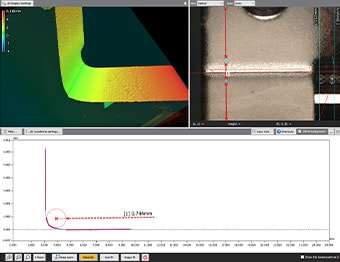
Gięcie materiałów metalowych wykorzystuje plastyczność, która jest unikalną cechą metali i stanowi metodę obróbki powszechnie stosowaną przy pracy z blachą i w innych zadaniach.
Gięcie jest ściśle związane z wytrzymałością materiału, przez co zginanie do niewłaściwego promienia może spowodować deformację, zmniejszenie wytrzymałości i uszkodzenie. Dlatego pomiar promienia gięcia może mieć duży wpływ na jakość.
Na tej stronie wykorzystano obróbkę blachy jako przykład obróbki metalu w celu przedstawienia podstawowych informacji na temat promienia gięcia, sposobu jego obliczania, środków zaradczych w przypadku wad i problemów z konwencjonalnym pomiarem promienia gięcia oraz przedstawiono najnowszą metodę pomiaru, która znacznie poprawia wydajność i dokładność pracy.
- Promień gięcia
- Gięcie w obróbce blachy
- Naprężenia występujące podczas gięcia blach i związane z nimi środki ostrożności
- Obliczanie osiągniętej długości gięcia przy użyciu promienia gięcia
- Środki zaradcze zapobiegające przeciwdziałania pękaniu i minimalny promień gięcia
- Problemy z konwencjonalnym pomiarem promienia gięcia
- Rozwiązanie problemów z pomiarem promienia gięcia
- Podsumowanie
Promień gięcia
Promień gięcia to promień od punktu początkowego gięcia do środka gięcia podczas obróbki plastycznej metalu, blachy, rur lub prętów przez tłoczenie lub walcowanie.
Każdy materiał ma limit zginania bez złamania, który zależy od jego grubości lub średnicy. Nazywa się to minimalnym promieniem gięcia. Promień gięcia musi być ustawiony odpowiednio do miejsca gięcia i zastosowania. Na końcowy promień gięcia może również wpływać odporność na naprężenia spowodowane zginaniem.
Gięcie w obróbce blachy
Jednym z typowych procesów, w których promień gięcia jest istotny, jest obróbka blachy. Powszechna metoda gięcia arkuszy opiera się na wykorzystaniu „prasy krawędziowej”, która dociska arkusz między górną matrycą zwaną stemplem a dolną matrycą. Oprócz matryc V pokazanych na poniższych ilustracjach stosowane są różne inne rodzaje matryc w zależności od kształtu gięcia i materiału. Należą do nich matryce promieniowe, które wyginają arkusz po łagodnym łuku, oraz matryce w kształcie litery U, które wyginają arkusz w dwóch punktach jednocześnie w jednym ruchu.
- A
- Stempel (górna matryca)
- B
- Blacha
- C
- Matryca (dolna)
- D
- Tłoczenie
Podczas gięcia grubych arkuszy niektóre prasy krawędziowe mogą używać stempla promieniowego lub głębokiej matrycy V (dolnej) nawet do zwykłego gięcia V. W przypadku gięcia z dużym promieniem arkusz może ulec niewielkiemu przesunięciu podczas tego procesu. Do pomiaru promienia można użyć stempla zwanego „liniałem promienia”.
Naprężenia występujące podczas gięcia blach i związane z nimi środki ostrożności
W wygiętym arkuszu generowane są poniższe naprężenia. W zależności od grubości i twardości obrabianego materiału mogą one mieć duży wpływ na promień gięcia.
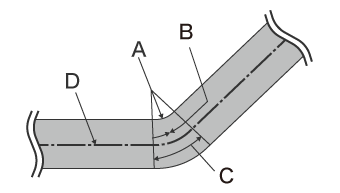
- A
- Promień gięcia
- B
- Naprężenie ściskające
- C
- Naprężenie rozciągające
- D
- Oś neutralna
- • Naprężenie ściskające
- Wewnętrzna strona neutralnej osi grubości arkusza jest ściskana, generując siłę w materiale, która opiera się ściskaniu.
- • Naprężenie rozciągające
- Zewnętrzna strona jest ciągnięta w kierunku rozciągania, generując siłę w materiale, która przeciwstawia się rozciąganiu.
- * W przekroju poprzecznym w kierunku grubości linia biegnąca przez środek arkusza, gdzie nie działa żadna z tych sił, nazywana jest osią neutralną.
Gdy prasowany materiał jest usuwany z matryc, może on sprężynować z powodu resztkowego naprężenia ściskającego i naprężenia rozciągającego, zwiększając kąt zgięcia części. Nazywa się to sprężynowaniem i jest bardziej prawdopodobne, że efekt ten wystąpi w twardych materiałach, ponieważ mają one tendencję do generowania większych naprężeń ściskających i rozciągających. Materiały takie należy zginać pod kątem węższym niż zamierzony kąt końcowy.
Wielkość sprężynowania zależy od materiału i grubości arkusza, a grube blachy mają tendencję do przesuwania osi neutralnej do wewnątrz. Dlatego ważne jest, aby określić wartość sprężynowania i ustawić odpowiednie warunki obróbki.
Obliczanie osiągniętej długości gięcia przy użyciu promienia gięcia
Aby umożliwić stabilne gięcie, wymagana jest osiągnięta długość gięcia. Można ją oszacować, uzyskując odległość od powierzchni promienia gięcia do osi neutralnej. Ponieważ proste części A i B nie są zmieniane przez zginanie, należy użyć wartości rzeczywistych.
Współczynnik przesunięcia osi neutralnej (λ: lambda) w punkcie gięcia różni się w zależności od grubości materiału, twardości, kąta gięcia i wewnętrznego promienia gięcia. Uważa się, że oś neutralna przebiega w miejscu, które znajduje się około od 20% do 45% grubości od powierzchni wewnętrznej. W miejscu pracy stosuje się wartości oparte na doświadczeniu. Poniżej przedstawiono wzór do obliczania osiągniętej długości gięcia.
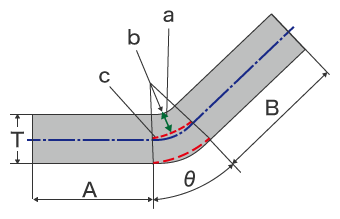
- a
- Odległość od powierzchni promienia gięcia do osi neutralnej
- b
- Promień gięcia
- c
- Oś neutralna na giętej części
L = A + B + (R + T x λ) x 2n x θ / 360
L = osiągnięta długość
A, B = długość części niepoddanych naprężeniom zginającym
R = wewnętrzny promień gięcia
T = grubość
θ = kąt gięcia
λ = współczynnik przesunięcia osi neutralnej (%) * wartość oparta na doświadczeniu
Środki zaradcze zapobiegające przeciwdziałania pękaniu i minimalny promień gięcia
Problemy występujące podczas gięcia obejmują defekty, takie jak pękanie i rozrywanie giętych części. Należy zwrócić uwagę na kierunek obrabiania materiału, ponieważ wady te są ściśle związane z kierunkiem walcowania. Prawdopodobieństwo występowania pęknięć i innych defektów jest większe, gdy materiał zginany jest równolegle do kierunku walcowania. Wady te są szczególnie prawdopodobne w przypadku materiałów ze stali nierdzewnej i aluminium.
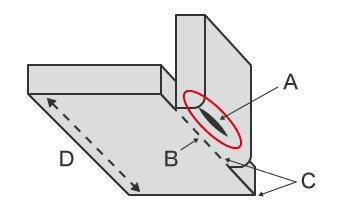
- A
- Prawdopodobne miejsce wystąpienia pęknięcia
- B
- Linia gięcia
- C
- Linia konturu wyrównana z linią gięcia
- D
- Kierunek walcowania równoległy do linii gięcia
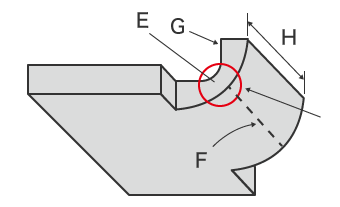
- E
- Zmniejszona grubość blachy na wygiętej części
- F
- Linia gięcia
- G
- Przekrój złamania
- H
- Szerokość gięcia mniejsza niż ośmiokrotność grubości blachy
Aby zapobiec tym wadom, konieczne jest przestrzeganie minimalnego promienia gięcia. Różni się on jednak w zależności od materiału, grubości blachy, matrycy i innych czynników, co utrudnia obliczenie jego prawidłowej wartości za pomocą wzoru matematycznego. W związku z tym należy ustalić ten promień na podstawie doświadczenia lub testów oraz zastosować środki zaradcze zapobiegające pękaniu podczas projektowania i obróbki metalu.
- Linię gięcia należy ustawić prostopadle do kierunku walcowania.
- Wybrany materiał powinien mieć wysoką plastyczność.
- Należy wybrać materiał o małych ziarnach krystalicznych lub zmniejszyć rozmiar ziaren krystalicznych przez ogrzewanie.
- Odsunięcie linii gięcia od linii konturu blachy zmniejsza prawdopodobieństwo wystąpienia pęknięć spowodowanych jej niewystarczającym wydłużeniem podczas gięcia.
- Gdy wykrojony arkusz jest zginany, ścięta powierzchnia łatwiej się wydłuża bez pękania niż powierzchnia z pęknięciami. Blachę należy zgiąć stroną ugięcia przy ścinaniu na zewnątrz.
- Powinno się użyć szerokości gięcia co najmniej osiem razy większej niż grubość arkusza.
Chociaż należy zwrócić uwagę na projekt i materiały, aby zapobiec pękaniu i innym wadom, kluczowe znaczenie ma także upewnienie się, że materiał jest wygięty do odpowiedniego kształtu w ramach tolerancji. W następnej sekcji wyjaśniono metody pomiaru promienia gięcia, a także związane z nimi problemy oraz ich rozwiązanie.
Problemy z konwencjonalnym pomiarem promienia gięcia
Gdy wymagana jest wyższa dokładność gięcia, trudniej jest całkowicie zapobiec wadom nawet w przypadku prawidłowego doboru materiału, konstrukcji i matryc. Pęknięcia, wykruszenie i wadliwe kształty (takie jak szerszy promień gięcia spowodowany sprężynowaniem) mogą prowadzić do problemów, w tym niższych wskaźników wydajności, a także niskiej jakości i łamliwości produktów.
Dlatego bardzo ważne jest, aby dokładnie zmierzyć i skontrolować kształty jak największej liczby giętych produktów podczas prób matryc oraz w przypadku zmiany materiału lub warunków gięcia. Podczas pomiaru promienia gięcia oprócz narzędzi ręcznych, takich jak mierniki promienia, używa się współrzędnościowych maszyn pomiarowych (CMM), projektorów analogowych i inne przyrządów pomiarowych. Istnieją jednak różne problemy z pomiarem promienia gięcia za pomocą tych konwencjonalnych narzędzi.
Problemy z pomiarem promienia gięcia za pomocą współrzędnościowej maszyny pomiarowej
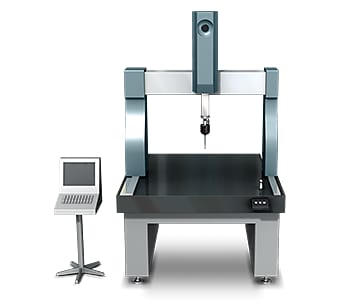
W przypadku zwykłego pomiaru giętej części za pomocą współrzędnościowej maszyny pomiarowej konieczne jest zetknięcie końcówki sondy z wieloma punktami na powierzchni docelowej.
Gdy obszar pomiarowy jest duży, dokładność pomiaru można ulepszyć przez zwiększenie liczby punktów pomiarowych w celu zebrania większej ilości danych.
Wiąże się to jednak z poniższymi problemami.
- Pomiar jest czasochłonny. Pomiar wymaga dużo czasu i wysiłku, szczególnie w przypadku dokładnych pomiarów na dużym obszarze, ze względu na dużą liczbę punktów wymagających zmierzenia.
- Gdy mały obrabiany przedmiot ma zagłębione części, złożony kształt lub mały promień gięcia, sonda może mieć trudności ze stykiem.
- Pomiar wymaga umiejętności i doświadczenia. Tylko ograniczona liczba operatorów jest w stanie dokonywać pomiarów, co skutkuje nieefektywną pracą pomiarową.
- Tabelaryzacja danych i obliczanie wartości również wymaga specjalistycznej wiedzy, umiejętności i wielu roboczogodzin.
Problemy z pomiarem promienia gięcia za pomocą projektora analogowego
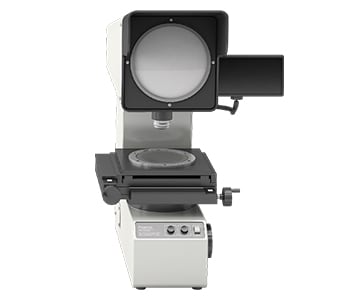
Projektor analogowy jest rodzajem optycznego przyrządu pomiarowego o zasadach pomiaru podobnych do mikroskopu optycznego. Przyrząd ten emituje światło pod obiektem, wyświetlając profil na ekranie.
Niektóre duże projektory analogowe mają ekran o średnicy ponad jednego metra. Urządzenia te mogą nakładać rzutowany profil 2D na powiększony rysunek, aby wizualnie zidentyfikować różnice między nimi. Wymaga to jednak wiele pracy i umiejętności.
Pomiar za pomocą projektora analogowego wiąże się z poniższymi problemami.
- Podczas montażu obiektu wymagane jest jego poziomowanie. Niektórych kształtów próbek nie można zmierzyć.
- Ponieważ wygięte obiekty mają trójwymiarowe kształty, niemożliwe jest określenie warunków całej wygiętej powierzchni za pomocą profilu 2D rzutowanego z boku obiektu.
- Metoda pomiaru różni się nieznacznie u różnych operatorów i możliwe są różnice w zmierzonych wartościach. Różnic między rzutowanymi wymiarami a rysunkiem nie można uzyskiwać w formie liczbowej, a kształt profilu trzeba przenieść z użyciem kalki, co utrudnia przechowywanie i porównywanie danych.
Podsumowując, metoda ta wiąże się z wieloma problemami. Nie wszyscy operatorzy mogą dokładnie mierzyć profile i nie wszystkie części mogą być mierzone. Ponadto niektóre próbki będą musiały zostać przycięte ze względu na kształt obiektu.
Rozwiązanie problemów z pomiarem promienia gięcia
Konwencjonalne przyrządy pomiarowe mogą jedynie rejestrować punkty lub linie albo mogą tylko porównywać profile 2D. Daje to niską wiarygodność pomiaru i utrudnia uzyskanie wartości liczbowych.
Aby rozwiązać te problemy pomiarowe, firma KEYENCE opracowała optyczny profilograf 3D ze sterowaniem jednym przyciskiem serii VR.
Urządzenie serii VR dokładnie rejestruje kształt 3D całej powierzchni docelowej bez kontaktu z obiektem. Narzędzie to pozwala użytkownikowi na wykonywanie dokładnych i powtarzalnych pomiarów w zaledwie sekundę. Wystarczy po prostu umieścić próbkę na stoliku pomiarowym i kliknąć jeden przycisk. System automatycznie ustawia zakres i warunki pomiaru, zapewniając dokładne pomiary ilościowe bez różnic między użytkownikami. W tej sekcji przedstawiono kilka konkretnych zalet serii VR.
Korzyść nr 1: możliwość uchwycenia kształtu 3D całej powierzchni w zaledwie sekundę.
Urządzenie serii VR natychmiastowo rejestruje dane powierzchni (800 000 punktów danych w jednym skanowaniu) w ciągu zaledwie sekundy. Umożliwia to dokładny pomiar i ocenę maksymalnych i minimalnych nierówności powierzchni na całej giętej części.
Urządzenie serii VR może również mierzyć profile w określonych miejscach. Nawet po zakończeniu pomiaru można pozyskać profile różnych części z danych skanowania 3D bez konieczności ponownego skanowania obiektu.
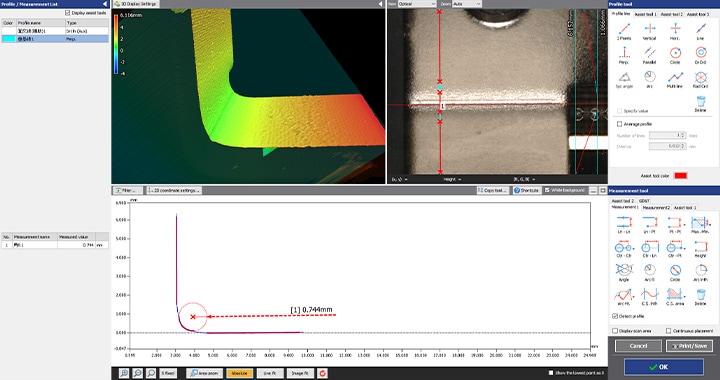
Korzyść 2: łatwa obsługa zapewniająca dokładne i powtarzalne pomiary bez względu na operatora.
Pomiar kształtu 3D można łatwo wykonać, po prostu umieszczając obiekt na stoliku pomiarowym i naciskając przycisk. Ścisłe poziomowanie lub pozycjonowanie nie jest wymagane, ponieważ dostępna jest automatyczna regulacja położenia na podstawie danych cech obiektu. Seria ta zawiera również pierwszą w branży funkcję Smart Measurement, która automatycznie konfiguruje zakres pomiarowy i przesuwa stoli pomiarowy zgodnie z rozmiarem obiektu. Eliminuje to konieczność ustawiania długości pomiaru i zakresu Z.
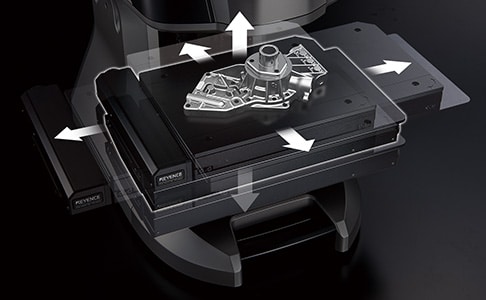
Szeroka gama narzędzi pomocniczych umożliwia prostą konfigurację żądanej zawartości pomiarowej.
Oprócz prostej konfiguracji obsługę systemu ułatwiają też narzędzia pomocnicze, dzięki którym nawet początkujący użytkownik może szybko i dokładnie mierzyć kształty. W rezultacie liczbę próbek można łatwo zwiększyć nie tylko w przypadku prototypów i prób, ale także przy pomiarach i kontroli produktów.
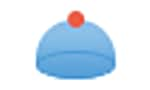
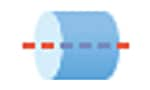
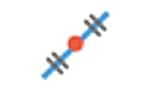
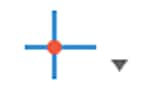
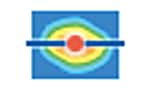
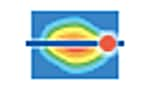

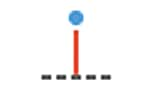
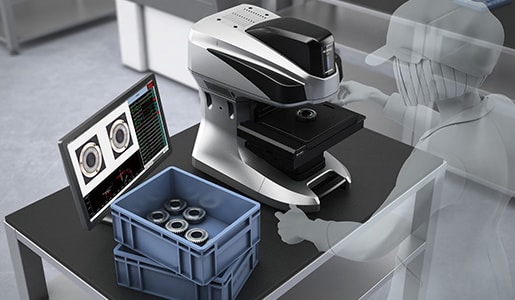
Podsumowanie
Urządzenie serii VR umożliwia dokładny i natychmiastowy pomiar trójwymiarowych kształtów obiektu przez szybkie bezkontaktowe skanowanie 3D. W ciągu zaledwie sekundy można zmierzyć nawet promień wygiętej części, nieregularności powierzchni i parametry innych trudnych do zmierzenia obiektów. Seria VR rozwiązuje wszystkie problemy z konwencjonalnymi przyrządami pomiarowymi.
- Ta seria jest w stanie mierzyć przekroje bez przecinania obiektu.
- Eliminuje to zmienność wynikającą z czynnika ludzkiego, umożliwiając prawdziwy pomiar ilościowy.
- Pomiar można wykonać, po prostu umieszczając obiekt na stoliku urządzenia i naciskając przycisk. Nie ma potrzeby pozycjonowania ani wykonywania innych przygotowań. Eliminuje to konieczność przydzielania wyspecjalizowanego operatora do prac pomiarowych.
- W krótkim czasie można zmierzyć dużą ilość próbek, ponieważ kształty 3D mogą być łatwo mierzone przy dużych prędkościach i z wysoką dokładnością. Jest to przydatne do poprawy jakości.
System ten umożliwia również porównywanie z wcześniejszymi danymi kształtu 3D i danymi CAD, a także zapewnia łatwą analizę danych, takich jak rozkład w granicach tolerancji. Może być skutecznie wykorzystywany do szerokiego zakresu celów, w tym rozwoju produktu, analizy trendów produkcyjnych i kontroli pobierania próbek.