Dokładny pomiar i analiza kształtu 3D wypaczonych płytek drukowanych
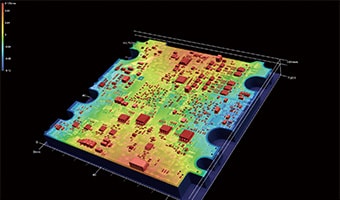
Podczas montażu części i urządzeń elektronicznych płytki drukowane narażone są na naprężenia spowodowane klejeniem i nagrzewaniem w trakcie procesu rozpływowego. Proces ten zapewnia wydajny montaż elementów, lecz naprężenia spowodowane ogrzewaniem mogą powodować deformacje termiczne płytek drukowanych, takie jak wypaczenia, falistość lub odkształcenia liniowe. Gdy płytka drukowana jest zdeformowana, wytrzymałość połączenia części lub dopasowania z obudową może ulec pogorszeniu, powodując znaczny spadek wydajności.
W tej sekcji przedstawiono podstawowe informacje na temat deformacji płytek drukowanych, problemy z pomiarem odkształceń oraz najnowsze metody pomiarowe.
- Odkształcenia płytek drukowanych
- Analiza symulacji i ocena odkształceń płytek drukowanych
- Trudności z pomiarem i oceną odkształceń płytek drukowanych
- Rozwiązania do pomiaru odkształceń płytek drukowanych
- Podsumowanie: znaczna poprawa i wyższa wydajność pomiarów odkształceń płytek drukowanych
Odkształcenia płytek drukowanych
Powierzchnia płytki drukowanej (PCB) powinna być płaska, aby umożliwić prawidłowy montaż elementów. Odkształcenia termiczne, takie jak wypaczenie lub krzywizna, mogą jednak wystąpić z powodu nadmiernego naprężenia spowodowanego ciepłem. Poniżej wyjaśniono powody, dla których deformacje płytek drukowanych stają się coraz większym problemem, a także skutki tych odkształceń.
Odkształcenia termiczne płytek drukowanych
W wyniku stosowania wielowarstwowych i coraz bardziej kompaktowych konstrukcji płytek drukowanych, na których montowane są elementy elektroniczne, a także postępów w montażu o wysokiej gęstości, metoda rozpływowa została przyjęta jako podstawowy sposób mocowania elementów. W procesie rozpływowym pasta lutownicza drukowana jest na wymaganych częściach i nakładane jest spoiwo do mocowania elementów. Następnie monter umieszcza elementy elektroniczne na płytce drukowanej. Płytka drukowana trafia do pieca, gdzie następuje jej podgrzanie w celu utwardzenia lutu lub spoiwa, co usprawnia montaż elementów.
Ze względu na wprowadzenie lutu bezołowiowego z przyczyn związanych z ochroną środowiska, do topienia lutu w procesie rozpływowym wymagane są obecnie wyższe temperatury. Wyższe temperatury wewnątrz pieca rozpływowego zwiększają naprężenia na płytkach drukowanych. Skutkuje to częstszymi problemami, takimi jak wypaczenie lub krzywizna płytki drukowanej, w piecu wysokotemperaturowym.
Skutki odkształceń płytek drukowanych
Odkształcenie płytek drukowanych może powodować problemy, takie jak nieprawidłowe lutowanie z powodu odchyleń elementów lub awarie połączeń z powodu naprężeń w lutowanych częściach. Gdy odkształcenie jest duże, dokładność montażu płytki drukowanej w obudowie może być mniejsza. Wady te mogą w znacznym stopniu obniżyć wydajność.
W przypadku niewielkiego odkształcenia części lub całej płytki drukowanej, która została zainstalowana w obudowie i wysłana bez zauważenia problemu, mogą wystąpić usterki produktu spowodowane awariami połączeń elementów elektronicznych, co może skutkować reklamacjami użytkowników. W szczególności płytki drukowane układów sterowania stosowane w samochodach lub samolotach wymagają najwyższego poziomu kontroli jakości, ponieważ wszelkie usterki mogą być katastrofalne w skutkach. W rezultacie kształt płytki drukowanej jest ważnym elementem kontrolnym tak samo jak uniesienie wyprowadzeń i kształt wypływki lutowniczej.
Analiza symulacji i ocena odkształceń płytek drukowanych
W przypadku ulepszeń mających na celu wyeliminowanie odkształceń płytek drukowanych należy uwzględnić, zweryfikować i ocenić warunki nagrzewania na każdym etapie. Należy to zrobić zarówno podczas projektowania, jak i rzeczywistej oceny ogrzewania.
Analiza symulacji odkształceń przy użyciu oprogramowania
Na etapie projektowania płytek drukowanych można przeprowadzić analizę symulacji z wykorzystaniem danych CAD. Jedną z metod wykorzystywanych do symulacji i oceny zachowania odkształcającego się obiektu jest metoda elementów skończonych (MES).
Metoda elementów skończonych (MES)
Metoda elementów skończonych to metoda analizy symulacji, w której złożony kształt dzieli się na elementy aż do uzyskania zbioru prostych kształtów, a następnie znajduje się naprężenia i odkształcenia dla każdego elementu o prostym kształcie. Układając poszczególne proste kształty w celu odtworzenia w pełni oryginalnej struktury, można przewidzieć naprężenia i odkształcenia dla każdej części całego obiektu. Wykorzystując dane CAD docelowego produktu w oprogramowaniu komputerowym, można przeprowadzić analizę symulacji pod kątem czynników takich jak sztywność, wytrzymałość, odporność na drgania, odkształcenia plastyczne, pękanie i deformacje termiczne.
Elementy klasyfikuje się według kształtu, jak pokazano poniżej.
Element zerowymiarowy (skalarny) |
![]() |
||
---|---|---|---|
Element jednowymiarowy (kolumnowy) |
![]() |
||
Element dwuwymiarowy (powłokowy) |
![]() |
![]() |
|
Element trójwymiarowy (bryła) |
![]() |
![]() |
![]() |
- Element jednowymiarowy (skalarny): punkt bez kształtu
- Element jednowymiarowy (kolumnowy): linia reprezentująca część, taką jak belka, słup lub dźwigar
- Element dwuwymiarowy (powłokowy): płaszczyzna. Służy do reprezentowania cienkich arkuszy i podobnych części.
- Element trójwymiarowy (bryła): istnieją trzy rodzaje brył. W kolejności od lewej są to: czworościan foremny w kształcie piramidy, pięciościan foremny w kształcie trójkątnej belki i sześcian foremny. Użycie większej liczby elementów sześciennych może zwiększyć dokładność analizy grubych obiektów, jednak poziom trudności jest wysoki i wymagany będzie długi czas obliczeń. Z drugiej strony postęp w technologii automatycznego tworzenia siatki elementów 3D przy użyciu elementów czworościennych skrócił czas obliczeń, a metoda ta jest odpowiednia, gdy priorytetem jest skrócenie czasu a nie dokładność.
Główne funkcje i przebieg analizy symulacji
Ponieważ mniejsza liczba wymiarów zmniejsza liczbę wymaganych kształtów, czas przetwarzania analizy jest krótszy. Zwiększenie liczby wymiarów wymaga wprawdzie więcej czasu, lecz pozwala uzyskać dokładniejsze dane. W zwykłym przepływie do symulacji deformacji elementu 3D płytki drukowanej dane projektowe płytki drukowanej najpierw dzieli się na siatkę. Chociaż prawie wszystkie dane projektowe płytek drukowanych są dwuwymiarowe, niektóre programy wymagają konwersji do formatu 3D oprogramowania CAD. Do każdego elementu siatki przykładane jest naprężenie przez wirtualne podniesienie temperatury zgodnie z profilem temperaturowym procesu rozpływowego, a następnie pozyskiwane są symulowane dane.
Wymagania dotyczące testu nagrzewania płytki drukowanej i rzeczywistego pomiaru/oceny
Po przeprowadzeniu symulacji płytkę drukowaną należy umieścić w piecu rozpływowym w celu sprawdzenia, czy zachowuje się tak samo jak w symulacji w proponowanym profilu temperaturowym.
Mimo że zależy to od rozmiaru, gdy płytka drukowana podzielona jest na trójwymiarowe elementy przy użyciu metody elementów skończonych, liczba elementów może osiągnąć około pięćdziesięciu tysięcy. Jeśli cały kształt powierzchni płytki drukowanej nie zostanie zatem dokładnie zmierzony, nie można uzyskać prawidłowych wyników kontroli bez względu na to, jak szczegółowa jest analiza symulacji. Rzeczywisty pomiar jest bardzo ważnym procesem w celu zidentyfikowania wszystkich punktów, które wymagają ulepszenia na etapie projektowania.
Następnie wyjaśnimy problemy z pomiarami za pomocą konwencjonalnych przyrządów pomiarowych oraz przedstawimy najnowszy system pomiarowy, który jest w stanie dokonać oceny przez porównanie z symulacjami komputerowymi o wysokiej dokładności.
Trudności z pomiarem i oceną odkształceń płytek drukowanych
Przy użyciu konwencjonalnych przyrządów pomiarowych trudno jest dokładnie zmierzyć cały kształt płytki drukowanej. W związku z tym niełatwo jest również określić ilościowo kształt próbki i zachodzące w niej zmiany, nawet po przeprowadzeniu zaawansowanych symulacji i eksperymentów. Poniżej przedstawiono niektóre z problemów, które można napotkać podczas korzystania z konwencjonalnych systemów pomiarowych.
Trudności pomiarowe — profilometr
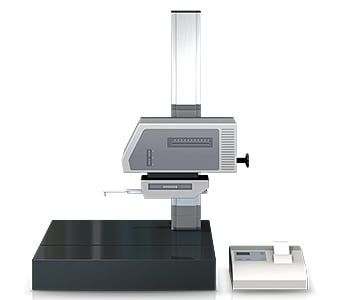
Profilometr mierzy i rejestruje profil obiektu w trakcie śledzenia jego powierzchni rysikiem.
W ostatnich latach opracowano systemy pomiaru profilu wykorzystujące laser zamiast rysika, które umożliwiają pomiar skomplikowanych kształtów przez bezkontaktowe śledzenie profilu. Niektóre modele są nawet w stanie wykonywać pomiar zarówno górnych, jak i dolnych powierzchni.
W przypadku pomiaru odkształceń płytek drukowanych z wykorzystaniem profilometrów pojawiają się następujące trudności:
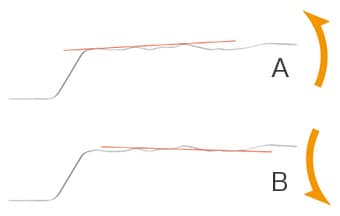
- A
- Nachylenie do góry
- B
- Nachylenie w dół
- Ponieważ obiekt mierzy się przez śledzenie wzdłuż linii, trudno jest zmierzyć i ocenić deformację na dużym obszarze.
- Zidentyfikowanie kształtu całej powierzchni obiektu jest niemożliwe.
- Pomiar wokół elementów zamontowanych na powierzchni jest trudny.
- Ustawienie płaszczyzny odniesienia za pomocą linii sprawia trudności i może skutkować błędem pomiaru (patrz ilustracja).
Trudności pomiarowe — CMM
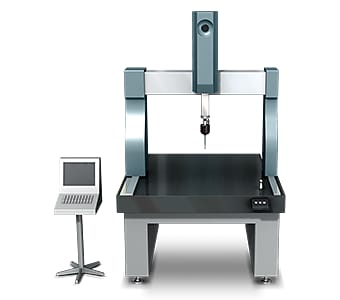
Ogólnie rzecz biorąc, podczas pomiaru odkształcenia płytek drukowanych za pomocą współrzędnościowej maszyny pomiarowej koniec sondy musi się stykać z co najmniej czterema narożnikami na mierzonej powierzchni obiektu.
Na przykład w przypadku płytki mierzy się zazwyczaj od sześciu do ośmiu punktów. Gdy obszar pomiarowy jest duży, dokładność pomiaru można ulepszyć przez zwiększenie liczby punktów pomiarowych w celu zebrania większej ilości danych pomiarowych.
Maszyny CMM stoją przed następującymi wyzwaniami podczas pomiaru deformacji płytek drukowanych:
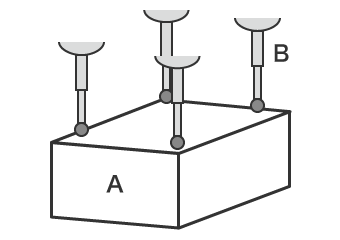
- A
- Obiekt
- B
- Sonda
- Ponieważ konieczny jest pomiar kontaktowy w ograniczonej liczbie punktów, niemożliwe jest zidentyfikowanie całego kształtu obiektu.
- Pomiar większej liczby punktów w celu uzyskania większej ilości danych pomiarowych wymaga dużo czasu i nie jest możliwe zidentyfikowanie szczegółowego kształtu całego obiektu ani lokalizacji nieregularności powierzchni.
Rozwiązania do pomiaru odkształceń płytek drukowanych
Konwencjonalne przyrządy mierzą kształty tylko za pomocą linii lub punktów, a cały kształt zdeformowanej płytki drukowanej nie może zostać zidentyfikowany. Ponadto trudno jest uzyskać maksymalne i minimalne wartości dla każdej nieregularności powierzchni na całym obiekcie lub szybko dokonać porównań ilościowych.
Aby rozwiązać te problemy pomiarowe, firma KEYENCE opracowała optyczny profilograf 3D ze sterowaniem jednym przyciskiem serii VR.
Urządzenie serii VR dokładnie rejestruje kształt 3D całej powierzchni docelowej bez kontaktu z obiektem. Nie wymaga specjalnego mocowania ani podejmowania subiektywnych decyzji, umożliwiając wykonywanie dokładnych pomiarów przez dowolnego operatora.
Korzyść nr 1: rejestrowanie danych na całej powierzchni w ciągu sekundy.
Urządzenie serii VR umożliwia zarejestrowanie 800 000 punktów danych powierzchni podczas pojedynczego bezkontaktowego pomiaru w ciągu zaledwie sekundy. Maksymalne i minimalne nieregularności powierzchni (wysokość, głębokość) w uzyskanym kształcie 3D mogą być wyświetlane na mapie kolorów w celu wizualizacji zdeformowanych charakterystyk na całym detalu.
Ponieważ dane rejestrowane są na całej powierzchni, linie profilu można narysować w dowolnym miejscu w celu wizualizacji i ilościowego określenia zmian wysokości.
Dane pomiarowe mogą być również nakładane i porównywane z danymi CAD lub z danymi skanowania z płytki drukowanej przed podgrzaniem, aby w pełni zrozumieć odkształcenie.
Pozwala to na znaczne zmniejszenie liczby roboczogodzin i poprawę wydajności pracy, a także dokładne pomiary, porównania i oceny.
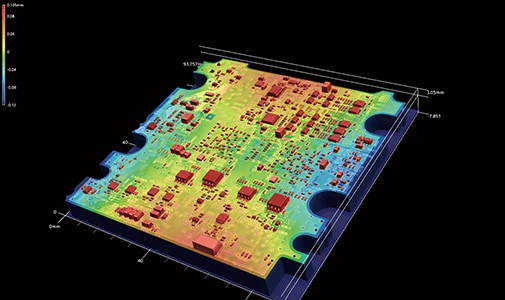
Korzyść nr 2: prosta obsługa pomiarów
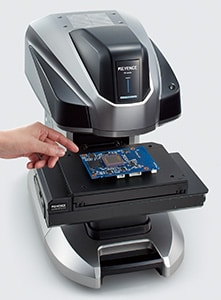
Pomiar kształtu 3D można łatwo wykonać, po prostu umieszczając obiekt na stoliku pomiarowym i naciskając przycisk.
Przełączając się między kamerami o małym i dużym powiększeniu, można wykonać dokładny pomiar całej płytki drukowanej lub szczegółowych części za pomocą jednego systemu, nawet w przypadku małych płytek drukowanych.
Urządzenie serii VR zawiera pierwszą w branży funkcję inteligentnego pomiaru, która wykrywa rozmiar i warunki powierzchniowe płytki drukowanej i automatycznie konfiguruje zakres skanowania i warunki, aby zarejestrować całą powierzchnię płytki drukowanej.
Szeroka gama wbudowanych narzędzi pomocniczych umożliwia wykonywanie dokładnych i powtarzalnych pomiarów nawet przez początkujących użytkowników. Ułatwia to zwiększenie liczby mierzonych próbek i przeprowadzanie analizy trendów nie tylko w celu testowania weryfikacyjnego i oceny projektów i symulacji, ale także w celu pomiaru i kontroli podczas produkcji komercyjnej.
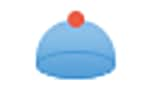
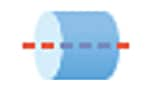
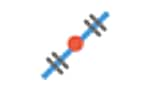
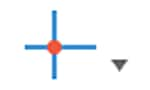
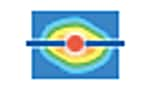
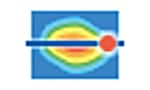
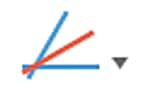
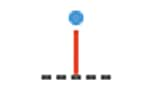
Podsumowanie: znaczna poprawa i wyższa wydajność pomiarów odkształceń płytek drukowanych
Urządzenie serii VR umożliwia dokładny i natychmiastowy pomiar trójwymiarowych kształtów obiektu przez szybkie bezkontaktowe skanowanie 3D. Oprócz pomiaru wymiarów 3D całej płytki drukowanej umożliwia to szybkie wykonanie prac, które wcześniej były trudne, takich jak pomiar kształtów niewielkich wysokości i nieregularności powierzchni oraz porównywanie wielu zestawów danych.
Korzystanie z serii VR rozwiązuje wszystkie problemy pomiarowe związane z konwencjonalnymi pomiarami.
- Różnice wysokości w całym obiekcie można wizualizować na kolorowej mapie.
- Porównywanie wielu zestawów danych pomiarowych jest łatwe, a warunki można stosować do wielu zestawów danych jednocześnie, co znacznie zwiększa wydajność pracy.
- Po zakończeniu skanowania można w dowolnym momencie wykonać pomiar profilu dowolnej części i porównać wiele zestawów danych.
- Pomiar można wykonać, po prostu umieszczając obiekt na stoliku urządzenia i naciskając przycisk. Nie ma potrzeby pozycjonowania ani wykonywania innych przygotowań. Eliminuje to konieczność przydzielania wyspecjalizowanego operatora do prac pomiarowych.
- W krótkim czasie można zmierzyć dużą ilość próbek, ponieważ kształty 3D mogą być łatwo mierzone przy dużych prędkościach i z wysoką dokładnością. Jest to przydatne do poprawy jakości.
Oprócz badań i rozwoju, projektowania i testowania może być skutecznie wykorzystywany w szerokim zakresie sytuacji podczas wytwarzania produktów elektronicznych, w tym do kontroli próbek po rozpoczęciu produkcji komercyjnej i analizy przyczyn w przypadku wystąpienia błędów.