Kontrole wyrywkowe
Na liniach produkcyjnych są wykonywane kontrole jakości dwóch typów: 100% inspekcji i kontrola wyrywkowa. Kontrola każdego elementu wytwarzanego w dużych ilościach niskim kosztem, jak nakrętki i śruby, żarówki i elementy elektroniczne, może kosztować tyle pracy i pieniędzy, że nie byłoby to racjonalne ekonomicznie ani organizacyjnie. 100% inspekcji nie jest także wykonalne w sytuacjach, w których kontrola może wiązać się ze zniszczeniem produktu. Dlatego podejście 100% inspekcji przyjmuje się raczej do produktów służących do podtrzymania życia, drogich towarów i produktów, które nie są zużywane ani niszczone w trakcie kontroli. Oznacza to, że wiele produktów jest poddawanych kontrolom wyrywkowym w różnych procesach.
- Charakterystyka kontroli wyrywkowej
- Kontrola wyrywkowa i procesy produkcji
- Schematy kontroli wyrywkowej
- Określanie wielkości próbki do kontroli wyrywkowej z korektą
- Zapobieganie wypuszczeniu wadliwych produktów przy użyciu kontroli wyrywkowej
Charakterystyka kontroli wyrywkowej
W kontroli wyrywkowej próbki są brane z partii docelowej (partii kontroli) do zbadania w celu ustalenia akceptowalności partii zależnie od jej standardów jakości. Dzięki niewielkiej liczbie elementów do skontrolowania w porównaniu ze 100% inspekcji, producenci mogą zaoszczędzić czas i pieniądze. Kontrola wyrywkowa umożliwia ponadto zbadanie pewnej liczby elementów testowych, które nie mogłyby zostać skontrolowane w trakcie 100% inspekcji.
Kontrole wyrywkowe nie gwarantują jednak jakości wszystkich wyprodukowanych produktów. Dlatego do kontroli wyrywkowych potrzebny jest system, który tnie koszty kontroli, biorąc pod uwagę korzyści dla producenta i konsumentów, a zarazem obniża ryzyko wad w celu utrzymania wysokiej jakości przez dłuższy czas. Oznacza to, że ważny jest schemat kontroli i to, jak ustalana jest wielkość próbki dla procesu produkcyjnego.
Kontrola wyrywkowa i procesy produkcji
Na następującym schemacie jest pokazana relacja między prosami produkcji i kontroli w przypadku podzespołów elektronicznych. Jak widać, proces produkcji i proces kontroli są misternie skoordynowane od akceptacji po produkcję i wysyłkę. W poszczególnych podprocesach przeprowadzane są kontrole wyrywkowe i 100% inspekcji.
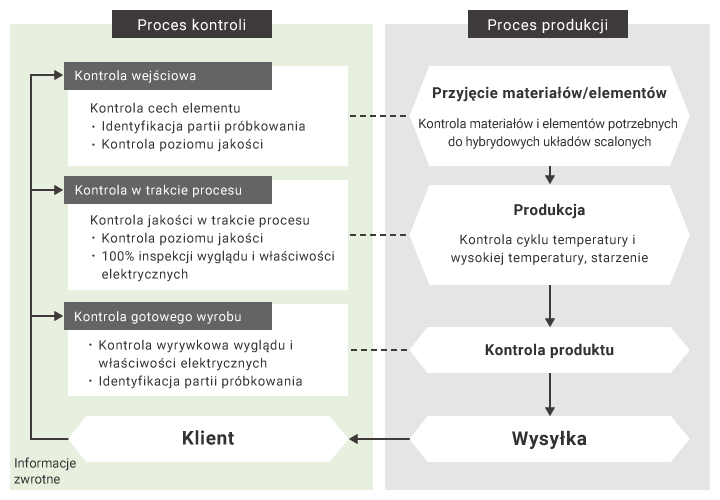
Schematy kontroli wyrywkowej
Kontrole wyrywkowe można podzielić na kilka grup zależnie od lokalizacji wykonywania kontroli, celu kontroli, charakterystyki i metody. Oprócz podziału zależnie od lokalizacji i celu, w tym kontrola przyjęcia, kontrola wysyłki i kontrola dostawy, kontrole wyrywkowe można również rozróżnić zależnie od produktów, których dotyczą, jak kontrola gotowego produktu, kontrola półwyrobu, kontrola elementów i kontrola materiałów. W tej sekcji przedstawione są najbardziej typowe klasyfikacje kontroli i schematy kontroli.
Klasyfikacja według schematów kontroli
- Kontrola wyrywkowa partiami
- Nadzorowana kontrola wyrywkowa
W kontroli wyrywkowej partiami określona ilość próbek jest brana do kontroli z partii produktów wyprodukowanej przy użyciu tych samych materiałów i sprzętu. Wynik kontroli jakości próbek decyduje o tym, czy jakość partii jest akceptowalna. Generalnie kontrola wyrywkowa oznacza domyślnie kontrolę partiami tego rodzaju.
W nadzorowanej kontroli wyrywkowej niewielka ilość produktów jest próbkowana do kontroli z różnych części procesu produkcyjnego w celu zarządzania warunkami procesu. Kontrola ta służy badaniu warunków procesu i jest także nazywana kontrolą procesu lub kontrolą punktową. Jest przeprowadzana na konkretne potrzeby zarządzania, jak utworzenie schematu zarządzania do użytku w kontroli jakości lub pozyskanie danych do badania czasu cyklu. O ile przedmiotem innych kontroli wyrywkowych są produkty, to nadzorowana kontrola wyrywkowa służy badaniu maszyn, systemów, operatorów lub metod pracy. Ułatwia to wczesne wykrywanie i naprawianie ewentualnych problemów w działaniach, sprzęcie lub systemach. Nadzorowana kontrola wyrywkowa zazwyczaj nie wymaga zatem tylu próbek co inne kontrole wyrywkowe.
Klasyfikacja na podstawie określenia poziomu akceptacji
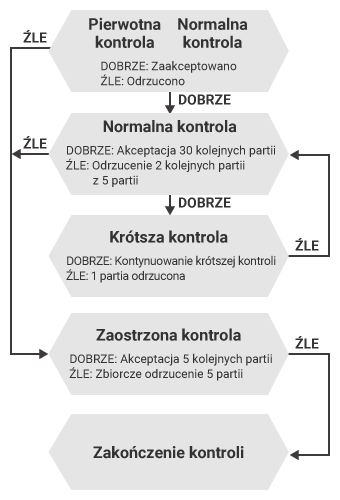
- Kontrola wyrywkowa na podstawie charakterystyki operacyjnej
- Kontrola wyrywkowa z korektą
- Kontrola naprawcza
- Kontrola wyrywkowa do produkcji w trybie ciągłym
Kontrola wyrywkowa oparta na charakterystyce operacyjnej to plan kontroli, który zapewnia ochronę producenta i gwarancję dla nabywców, a zarazem spełnia wymagania zarówno producentów, jak i nabywców. Ten schemat próbkowania chroni producenta, wyznaczając pewną niewielką wartość procentową partii dobrej jakości, które zostały błędnie odrzucone (ryzyko producenta). Z drugiej strony ten schemat próbkowania zabezpiecza nabywców, wyznaczając pewną niewielką wartość procentową partii złej jakości, które zostały błędnie zaakceptowane (ryzyko nabywcy). Generalnie przyjmuje się, że ryzyko producenta wynosi 5%, a ryzyko konsumenta 10%, co można zaobserwować na krzywej OC.
Kontrola wyrywkowa z korektą koryguje gwarancję jakości dla nabywców, poluzowując lub zacieśniając kontrolę wyrywkową zależnie od statystyk jakości z poprzednich kontroli. Kontrola wyrywkowa z korektą może być indeksowana na podstawie AQL lub LQ lub być przeprowadzana jako plan kontroli z pomijaniem partii. Procedura próbkowania kontroli z korektą jest zdefiniowana w ISO 2859-1, ISO 2859-2 i ISO 2859-3.
W kontroli naprawczej partia odrzucona w kontroli wyrywkowej jest poddawana 100% inspekcji. Tego schematu nie można zatem zastosować do produktów nienadających się do 100% inspekcji.
Kontrola wyrywkowa w produkcji w trybie ciągłym to schemat kontroli polegający na sekwencyjnej kontroli produktów wytwarzanych w trybie ciągłym, a nie w partiach. Plan kontroli może zaczynać się od 100% inspekcji, a następnie przechodzić do kontroli wyrywkowej po wykryciu pewnej liczby niewadliwych produktów. W przypadku wykrycia wady ponownie wykonuje się kontrolę w trybie 100% inspekcji.
Klasyfikacja według planów próbkowania
- Jednokrotna kontrola wyrywkowa
- Dwukrotna kontrola wyrywkowa
- Wielokrotna kontrola wyrywkowa
- Sekwencyjna kontrola wyrywkowa
W jednokrotnej kontroli wyrywkowej akceptowalność partii jest określana na podstawie wyniku jednej kontroli wyrywkowej.
W dwukrotnej kontroli wyrywkowej akceptowalność partii jest określana na podstawie wyniku drugiej kontroli wyrywkowej, jeśli wynik pierwszej kontroli nie wskazuje jednoznacznie, czy partię należy zaakceptować czy odrzucić.
W wielokrotnej kontroli wyrywkowej badana jest większa liczba próbek niż w schemacie dwukrotnej kontroli wyrywkowej. Pewna liczba elementów jest próbkowana za każdym razem i wynik jest porównywany z przyjętym standardem. W tym trybie kontroli akceptacja lub odrzucenie zależy od określonej liczby kontroli, przy czym wyniki są dzielone na akceptowalne, nieakceptowalne i niepewne.
W sekwencyjnej kontroli wyrywkowej akceptowalność jest określana z większą dokładnością niż w schemacie wielokrotnej kontroli wyrywkowej. Sekwencyjna kontrola wyrywkowa może być przeprowadzana na dwa sposoby: indywidualna kontrola sekwencyjna, w trakcie której jest próbkowany jeden element, i zgrupowana kontrola sekwencyjna, która polega na próbkowaniu pewnej stałej liczby elementów jednocześnie.
Określanie wielkości próbki do kontroli wyrywkowej z korektą
W przypadku kontroli wyrywkowej z korektą wielkość próbki może być określana na trzy sposoby:
- Indeksowanie AQL
- Indeksowanie LQ (jakości granicznej)
- Pomijanie partii
- Indeksowanie AQL
- AQL to skrót od Acceptance Quality Limit (limit akceptowalnej jakości). Jest to górny limit, do którego produkty w kontroli wyrywkowej są akceptowane, i standard kontroli powszechnie stosowany w kontrolach wyrywkowych. Jeśli w kontroli wyrywkowej indeksowanej na podstawie AQL jakość produktów z procesu, z którego pobierane są próbki, nie spada poniżej AQL, zakłada się, że te produkty są akceptowalne.
- Indeksowanie LQ i pomijanie partii
- Indeksowanie LQ i pomijanie partii różnią się od indeksowania AQL indeksem używanym do określania poziomu jakości i sposobem próbkowania. Przykładowo w kontroli wyrywkowej indeksowanej na podstawie LQ jako indeks służy jakość graniczna (LQ). Kontrola wyrywkowa, w której pomijane są partie, przyjmuje bez kontroli, że pewne sekwencja partii jest akceptowalna, pod warunkiem, że pewna liczba partii jest zgodna ze standardem.
W tej sekcji są objaśnione podstawy planów próbkowania indeksowanych na podstawie AQL, ponieważ jest to najpowszechniej stosowany schemat kontroli wyrywkowych. Ten tryb kontroli oparty jest na schemacie próbkowania zdefiniowanym w ISO 2859-1, w ramach którego najpierw jest odczytywana litera próbki, a następnie jest wyznaczana wielkość próbki. Czytając tę procedurę, można się dowiedzieć, jak jest wybierany standard i rygorystyczność kontroli, jak określana jest wielkość próbki i jak weryfikowana jest liczba akceptacji i odrzutów.
Odczytywanie litery próbki
Liczba próbek, które należy pobrać z partii, jest wskazywana kodem alfabetycznym nazywanym literą próbki, ustalanym w sposób opisany w poniższej tabeli na podstawie wielkości partii i poziomu kontroli (ISO 2859-1).
Wielkość partii | Specjalne poziomy kontroli | Ogólne poziomy kontroli | |||||
---|---|---|---|---|---|---|---|
S-1 | S-2 | S-3 | S-4 | I | II | III | |
Od 2 do 8 | A | A | A | A | A | A | B |
Od 9 do 15 | A | A | A | A | A | B | C |
Od 16 do 25 | A | A | B | B | B | C | D |
Od 26 do 50 | A | B | B | C | C | D | E |
Od 51 do 90 | B | B | C | C | C | E | F |
Od 91 do 150 | B | B | C | D | D | F | G |
Od 151 do 280 | B | C | D | E | E | G | H |
Od 281 do 500 | B | C | D | E | F | H | J |
Od 501 do 1200 | C | C | E | F | G | J | K |
Od 1201 do 3200 | C | D | E | G | H | K | L |
Od 3201 do 10000 | C | D | F | G | J | L | M |
Od 10001 do 35000 | C | D | F | H | K | M | N |
Od 35001 do 150000 | D | E | G | J | L | N | P |
Od 150001 do 500000 | D | E | G | J | M | P | Q |
500001 i więcej | D | E | H | K | N | Q | R |
Litera próbki to kod wskazujący jej wielkość, ułatwiający korzystanie ze schematu kontroli wyrywkowej. Na podstawie tej litery jest określana wielkość próbki.
W odniesieniu do poziomu kontroli wybiera się „Ogólny poziom kontroli II”, o ile nie ma problemów z procesem. W odniesieniu do wielkości partii należy wybrać wielkość partii kontrolowanych próbek. Litera próbki jest określana na podstawie poziomu kontroli i wielkości partii.
Jeśli na przykład wielkość partii wynosi 2000, to przy ogólnym poziomie kontroli II literą próbki będzie K.
Określanie wielkości próbki
Do określania wielkość próbki służy litera próbki. Wielkość próbki determinuje rygorystyczność kontroli. Rygorystyczność kontroli dzieli się na następujące poziomy:
- Normalna kontrola
- Krótsza kontrola
- Zaostrzona kontrola
Najpierw, na podstawie warunków bieżącego procesu, należy wybrać jeden z trzech powyższych poziomów rygorystyczności kontroli. Następnie należy przejrzeć plany próbkowania (tabela główna) na wybranym poziomie.
Ta tabela jest określona dla poszczególnych kombinacji rygorystyczności kontroli i planu próbkowania. Zazwyczaj wykonywana jest normalna kontrola, o ile w procesie nie występują żadne problemy. Jeśli schematem kontroli jest na przykład plan jednokrotnego próbkowania z normalną kontrolą, należy posłużyć się następującą tabelą określoną w ISO:
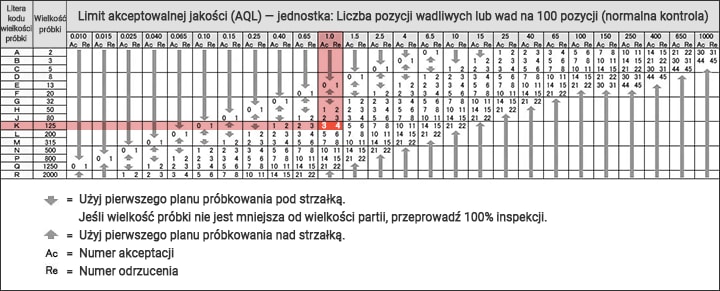
W przykładzie podanym w punkcie „Odczytywanie litery próbki” literą próbki jest K, a wielkość próbki wynosi 125 jednostek. Jeśli udział procentowy wad wynosi 1,0%, próg akceptacji (As) wynosi 3, a próg odrzutu (Rs) wynosi 4. Oznacza to, że partia jest akceptowana, jeśli zostaną wykryte nie więcej niż 3 wadliwe elementy. Ta sama partia nie zostanie zaakceptowana, jeśli w kontroli zostaną wykryte 4 wadliwe elementy lub więcej.
Zastrzeżenia dotyczące określania wielkości partii
W kontroli wyrywkowej próbki wybierane z wyprodukowanych produktów są poddawane kontroli. Produkty są kontrolowane według partii, a wyniki kontroli z poszczególnych partii stanowią cenne informacje pokazujące tendencje zmian w procesie produkcji w trybie ciągłym. Dlatego należy wykonywać kontrole jak najszybciej i przekazywać wyniki w formie informacji zwrotnych do hali produkcyjnej.
Sposób definiowania partii zależy od firmy. Definicja partii wpływa na liczbę próbek. Jeśli partia jest mała, elementy są często próbkowane, przez co kontrole mogą stać się uciążliwe. Jeśli partia jest duża, w razie problemu z jakością więcej produktów może zostać wstrzymanych przed wysyłką. Dlatego wybierając wielkość partii należy wyznaczyć górne i dolne limity. Ponadto partia musi składać się z produktów produkowanych w tych samych warunków, co wymaga dobrej znajomości statusu działania procesu produkcyjnego.
Zapobieganie wypuszczeniu wadliwych produktów przy użyciu kontroli wyrywkowej
Zapobieganie przepuszczaniu wadliwych produktów przez kontrolę wymaga zrozumienia wskaźników akceptacji i odrzucenia bieżącego schematu kontroli. Krzywa operacyjno-charakterystyczna (OC) to wykres wizualizujący te wskaźniki. Ta krzywa, nazywana także krzywą charakterystyki inspekcji, różni się zależnie od schematu i poziomu kontroli oraz służy do określania wielkości partii i wielkości próbki podczas kontroli wyrywkowej.
W krzywej OC wskaźnik akceptacji partii znajduje się na osi pionowej, a wskaźnik odrzucenia produktu na osi pionowej. W efekcie kontroli wyrywkowej im mniej jest wad, tym wskaźnik akceptacji jest wyższy, a im więcej wad, tym wskaźnik akceptacji niższy. Wykres przebiega łagodną krzywą od lewego górnego do prawego dolnego rogu.
W tej sekcji są wytłumaczone podstawowe zasady interpretacji krzywej OC i jest omówione, w jaki sposób może ona zapobiec wypuszczaniu wad na rynek.
Co może pokazać krzywa OC?
Posłużymy się przykładową krzywą OC kontroli wyrywkowej przeprowadzanej na 10 próbkach pobranych z 1000 produktów, której wynik zostanie uznany za pozytywny, jeśli będzie zawierała nie więcej niż jeden wadliwy produkt (wskaźnik odrzucenia 1%).
Wynik kontroli może przedstawiać różne wzorce, od samych wadliwych do samych dobrych próbek. Poniższy wykres pokazuje krzywą OC reprezentującą tę relację.
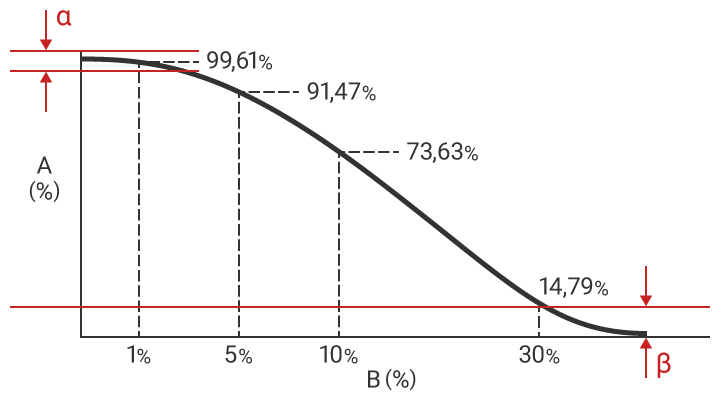
- A
- Wskaźnik akceptacji
- B
- Wskaźnik odrzucenia partii
- α
- Ryzyko producenta
- β
- Ryzyko konsumenta
Z tej krzywej OC można wyczytać następującą charakterystykę schematu kontroli:
- Prawdopodobieństwo przejścia tej kontroli przez partię przy wskaźniku odrzucenia 1% wynosi 99,61%.
- Prawdopodobieństwo przejścia tej kontroli przez partię przy wskaźniku odrzucenia 5% wynosi 91,47%.
- Prawdopodobieństwo przejścia tej kontroli przez partię przy wskaźniku odrzucenia 10% wynosi 73,63%.
- Prawdopodobieństwo przejścia tej kontroli przez partię przy wskaźniku odrzucenia 30% wynosi 14,79%.
Warte podkreślenia jest to, że 14,79% partii przy wskaźniku odrzucenia 30% przejdzie kontrolę. Z drugiej strony, istnieje także prawdopodobieństwo odrzucenia partii, które właściwie powinny przejść kontroli. W ISO odpowiedzią na ten problem jest przyjęcie ryzyka producenta na poziomie 5% (α: prawdopodobieństwo odrzucenia partii o udziale wadliwych elementów poniżej akceptowalnego poziomu jakości) i ryzyka konsumenta na poziomie 10% (β: prawdopodobieństwo akceptowania partii o udziale wadliwych elementów powyżej akceptowalnego poziomu jakości).
Określanie optymalnej wielkości próbki na podstawie krzywej OC
Dopóki kontroli są poddawane tylko próbkowane produkty, zawsze może się zdarzyć wysyłka wadliwych partii. Prawdopodobieństwo wysyłki wadliwych partii można jednak zredukować.
Zwiększenie wielkości próbki przy jednoczesnym utrzymaniu takich samych poziomów akceptacji i odrzucenia może zmniejszyć ryzyko wysyłki wadliwych partii. Jeśli na przykład kontrola jakości zostanie zwiększona do 20, to prawdopodobieństwo przejścia przez tę partię kontroli przy wskaźniku odrzucenia 30% będzie wynosiło już tylko 3,41%. Krzywa OC w przypadku zwiększenia ilości kontroli do 20 jest następująca.
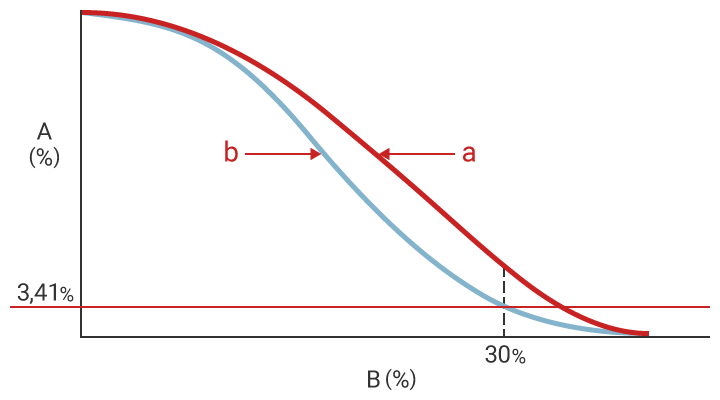
- A
- Wskaźnik akceptacji
- B
- Wskaźnik odrzucenia partii
- a
- Kontrola na 10 próbkach
- b
- Kontrola na 20 próbkach
Jak widać, zwiększenie liczby próbek może przełożyć się na poprawę jakości partii wysyłki. Jednak im większa próbka, tym więcej czasu zajmuje kontrola. Zwiększenie próbki jest szczególnie trudne w sytuacjach, gdy produkty mogą ulec zniszczeniu w trakcie kontroli.
Chociaż optymalna wielkość próbki wyznaczana jest na podstawie kosztu robocizny związanej z kontrolą oraz wymaganej jakości, to krzywa OC jest narzędziem pokazującym zależność między tymi dwoma kryteriami.
Matematyka krzywych OC
Dlaczego krzywa OC przybiera taką formę?
Jeśli wskaźnik odrzucenia wynosi 0 i partia może przejść kontrolę, jeśli jej wskaźnik akceptacji jest niższy od wskaźnika odrzucenia (i nie przechodzi, jeśli wskaźnik akceptacji jest większy), nie ma możliwości, aby wadliwe produkty trafiły na rynek. Jednak jedynym sposobem, aby to osiągnąć, jest wdrożenie 100% inspekcji.
Kontrola wyrywkowa to po prostu sposób zapobiegania wysyłce wadliwych produktów na zasadzie prawdopodobieństwa. Umożliwia nam ona przyjęcie pewnego sposobu zminimalizowania wadliwych produktów na rynku.
Prawdopodobieństwo P(r), że n próbek będzie zawierało r wadliwych produktów, można obliczyć z następującego wzoru:

Zgodnie z rozkładem dwumianowym prawdopodobieństwo P(≦r), że liczba wadliwych produktów będzie wynosiła r lub mniej, wynosi:

Jeśli zatem wartości n i r są stałe, P(≦r) jest funkcją p (wskaźnika akceptacji), czyli mamy P(p) zamiast P(≦r), a wykres tej funkcji jest krzywą OC.